Mechanical Vapor Recompression (MVR) is an innovative technology that significantly improves energy efficiency in industrial evaporation processes. By utilizing the latent heat of steam, MVR systems reduce energy consumption by up to 90% compared to traditional evaporation methods.
Mechanical vapor compression (MVC) is an advanced technology for efficient water evaporation that uses mechanical energy to compress the vapor, which offers significant energy savings compared to traditional thermal evaporation methods.
This article focuses on the fundamental functions of MVR, its operating systems and its various applications in different industries, as well as the most recent developments and how these innovations will transform the reuse of steam in thermal recovery systems.
What is Mechanical Vapor Recompression?
This process works as follows:
- Low-pressure steam, usually water vapor, is compressed to add energy.
- The result is a vapor with a smaller volume, but at a higher temperature and pressure.
- The compressed steam is used as a heat source in the heating chamber of the evaporation system.
- The process is repeated during operation.
MVR is a technique used to reduce costs in industrial plant operations by reusing process heat. In addition, it is mainly used in industrial processes such as evaporation and distillation in wastewater treatment. In these processes, Mechanical Vapor Recompression allows the heat from the condenser, which is not lost, to be recovered and used in the evaporation process.
The following video explains how a Mechanical Vapor Recompression (MVR) Turbo Generator works. Courtesy of: TLT-Turbo.
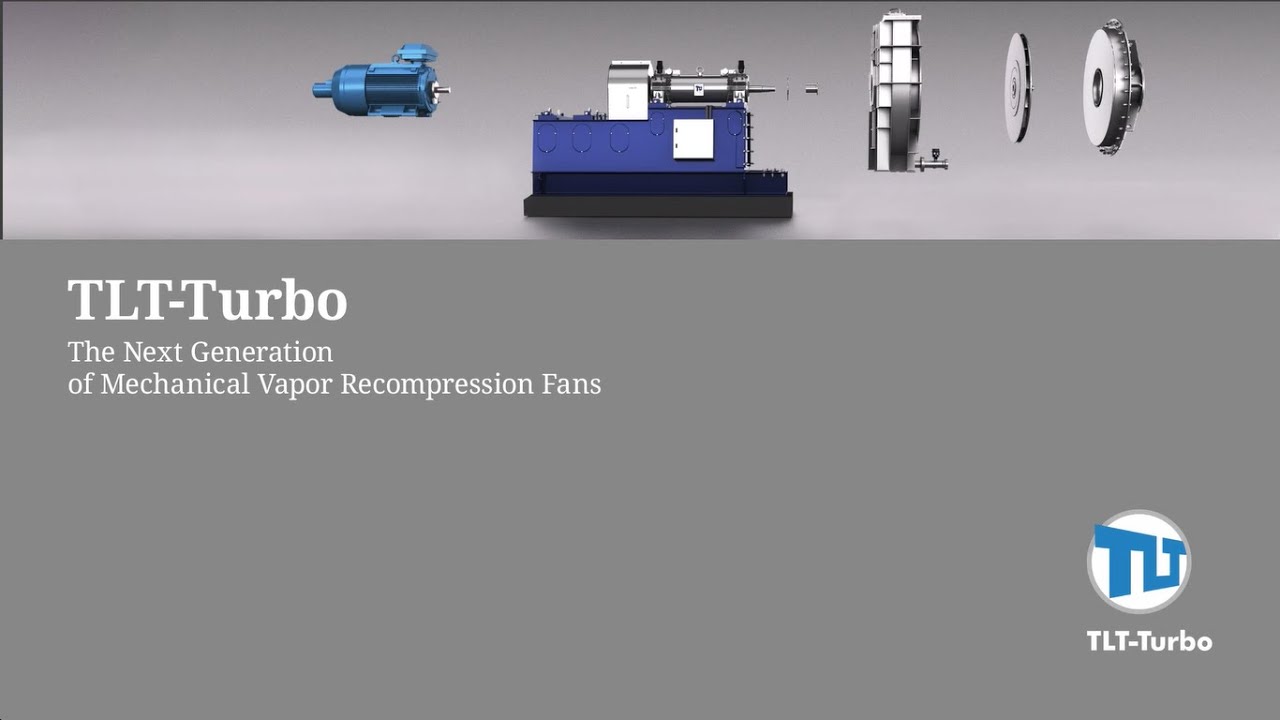
Mechanical Vapor Recompression (MVR).
Mechanical vapor recompression functions
MVC systems work by compressing steam to increase its temperature and pressure, which makes them suitable for high purity applications in the pharmaceutical and chemical industries. The process is characterized by:
- Energy efficiency
- High quality steam production
- Potential for significant energy savings
The MVR operates on the principle of compressing steam to increase its temperature and pressure, allowing the recovered steam to be reused as a heat source to evaporate liquids. The main functions of the MVR include:
- Energy recovery: MVR systems capture and reuse thermal energy from steam that would otherwise be wasted. This process not only reduces the overall energy requirement, but also minimizes operating costs.
- Liquid concentration: By compressing the vapor, the MVR facilitates the concentration of various liquids, improving product quality and reducing waste volume.
- Waste minimization: MVR technology is an integral part of Zero Liquid Discharge (ZLD) systems, which aim to minimize liquid effluents by concentrating waste streams to near-zero discharge levels.
- Reduced environmental impact: The efficiency of MVR systems leads to lower greenhouse gas emissions and lower water consumption, in line with sustainability objectives in industrial operations.
MVR operating systems
MVR systems consist of several key components that work together to achieve efficient vapor compression and heat recovery:
- Evaporator: The initial stage where the liquid is heated to create vapor. Various designs can be employed, such as falling film or forced circulation evaporators, depending on the process requirements.
- Vapor compressor: This component mechanically compresses the vapor, which increases its pressure and temperature. Common types include centrifugal compressors, positive displacement blowers (Roots type) and axial flow compressors.
- Heat exchanger: After compression, the superheated vapor passes through a heat exchanger where it transfers its latent heat back to the feed liquid, facilitating further evaporation.
- Separators: They are used to separate the condensed liquid from the vapor stream, ensuring that only pure vapor is recycled back into the system.
- Control systems: Automated control systems monitor and regulate operating parameters such as temperature, pressure and flow to optimize performance and ensure safety.
Operating principle and key benefits
The MVC system operates by taking steam generated at low pressure and compressing it to reach higher pressure and temperature levels. This compressed steam is reused as a heat source in the same process, eliminating the need for additional external sources. Notable benefits include:
- Energy efficiency: By recycling steam, primary energy consumption is minimized, which can reduce operating costs by up to 50%.
- High quality steam production: Ideal for processes requiring strict purity standards, such as pharmaceutical distillation.
- Sustainability: Reduction of greenhouse gas emissions and greater alignment with environmental objectives.
Applications of mechanical vapor recompression in industrial processes
MVR technology finds wide application in various industries due to its versatility and efficiency:
- Chemical industry: Used for the evaporation and concentration of chemicals, the MVR improves crystallization processes while minimizing energy costs.
- Food and beverage industry: MVR is used to concentrate juices, dairy products (such as milk) and other food substances, ensuring product quality and reducing waste.
- Pharmaceutical industry: In pharmaceutical manufacturing, MVR is used to concentrate active ingredients and solvents, improving process efficiency while adhering to strict quality standards.
- Wastewater treatment: MVR systems are an integral part of ZLD processes in industrial wastewater treatment, allowing water recovery from effluents while minimizing environmental impact.
- Desalination: In seawater desalination processes, MVR helps recover valuable freshwater from saline sources by efficiently concentrating brine solutions.
- Energy sector: MVR is increasingly used in power plants for vapor recovery applications, converting low-pressure steam into usable energy while reducing natural gas consumption.
Start-up and operational challenges
The commissioning process of an MVC system can be complex and requires careful planning. It is critical to ensure that the system stabilizes gradually to avoid damage to components and to achieve optimum efficiency. Key steps include:
- Initial preparation: This includes verifying the integrity of the thermal insulation systems and ensuring a stable external power supply.
- Initial steam generation: Using external sources until the minimum conditions necessary for the compressor to start operating are reached.
- Compressor start-up: A mixture of air and vapor is introduced, while key parameters such as temperature, pressure and flow rate are monitored.
- Stabilization: Gradually, the system transitions to autonomous operation by closing ventilation valves and disconnecting external sources.
Vacuum operation presents additional challenges, such as the increased volume of expanded vapor, which can increase energy consumption and require a robust compressor design.
Performance analysis
Advanced control systems significantly improve the efficiency of modern vapor compressors through several key mechanisms:
Intelligent control systems: These systems use real-time data analysis to monitor various parameters such as pressure, temperature and flow rate. By continuously adjusting these parameters, the systems ensure optimal compressor performance and energy efficiency.
Advanced control systems incorporate predictive maintenance algorithms that detect potential problems before they cause breakdowns. This minimizes downtime and repair costs, ensuring continuous and efficient operation.
Energy efficiency optimization
Variable speed drives (VSD): VSD technology adjusts motor speed according to demand, reducing energy consumption during periods of low demand. This adaptability ensures that compressors operate at maximum efficiency, minimizing energy waste.
Anti-surge control: High-quality anti-surge control systems regulate compressor parameters to maintain minimum flow and avoid surge conditions.
This ensures stable operation even during process load variations, which improves overall energy efficiency.
Technological innovations in Mechanical Vapor Recompression (MVR)
Some innovations in MVR technology are:
- Ceramic hybrid bearings: In MVR fans, ceramic hybrid bearings with steel rings and ceramic rollers require less maintenance and have better operating performance.
- EVALED RV evaporators: Evaporators for evaporation by mechanical vapor recompression used to treat large quantities of wastewater.
- Vacuum evaporation by mechanical vapor compression: This technology recovers the latent heat of condensation of the distillate to heat the liquid to be evaporated.
Mechanical Vapor Recompression fans (RMV) represent a significant advance in the energy efficiency of industrial processes. The following is the new innovation of these fans. Courtesy of: TLT-Turbo.
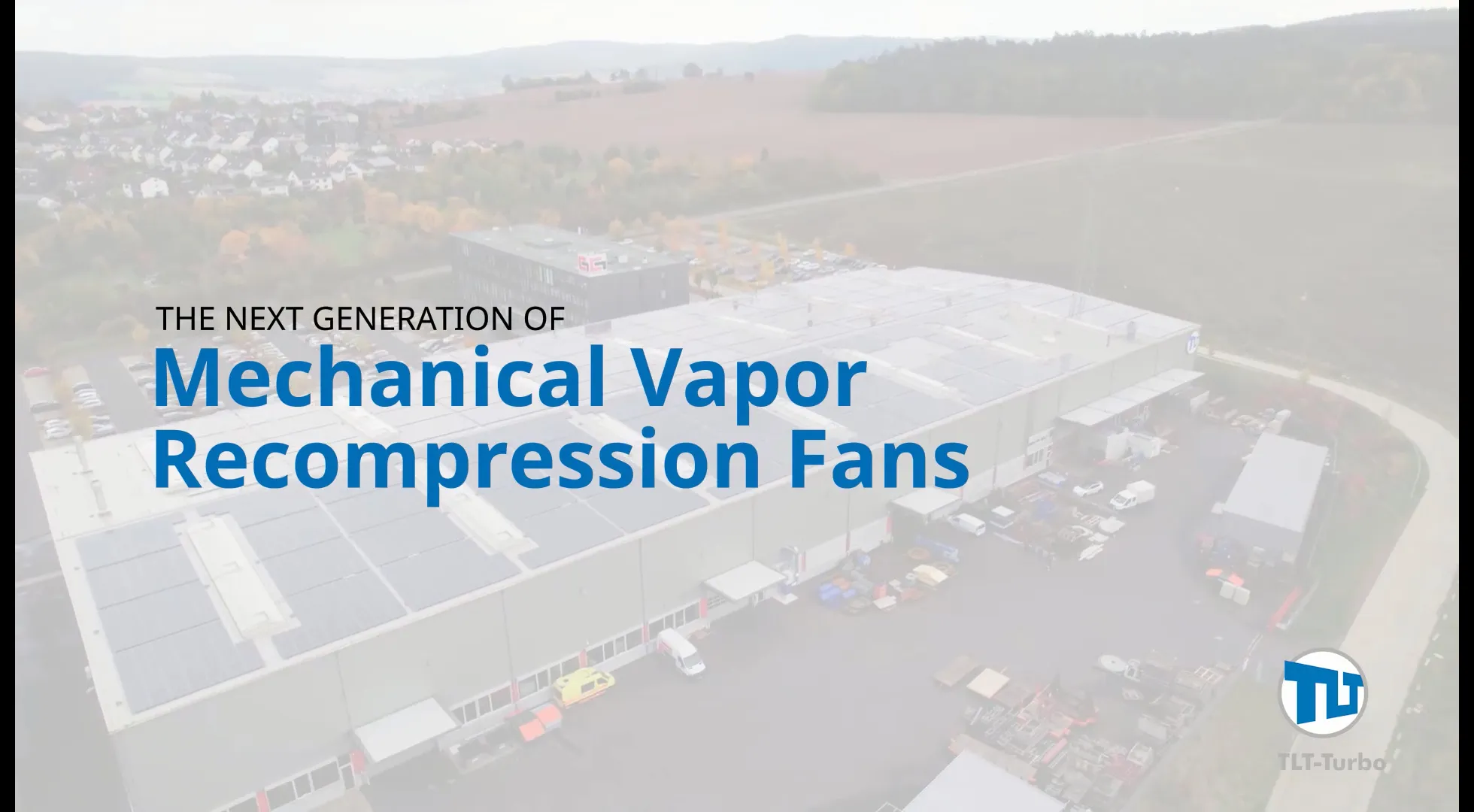
Next generation Mechanical Vapor Recompression (MVR) fans.
Mechanical vapor recompression is a key technology for recovering energy in processes that generate low-pressure steam by increasing its pressure and temperature for reuse. RMV’s new fans promise significant improvements:
- Improved efficiency: Advanced designs optimize energy consumption, reducing operating costs.
- Advanced materials: Use of materials resistant to corrosion and high temperatures, increasing the useful life of the equipment.
- Digitization and online monitoring: Incorporation of sensors and data analysis to predict failures and improve operation in real time.
- Compactness and modularity: Smaller and modular fans, ideal for adapting to different industrial configurations.
RMV’s upcoming fans mark the future of industrial sustainability, highlighting how technology can maximize energy efficiency and minimize waste.
Load distribution and capacity management
Load sharing algorithms: For compressors operating in parallel or in series, advanced algorithms ensure coordinated load sharing. This approach maximizes efficiency by driving compressors to their optimal operating zones based on current process conditions.
Flow management solutions: Control systems manage gas flows effectively, minimizing disturbances and maintaining satisfactory levels of operation. This capability is crucial for handling transients and ensuring long-term reliability.
In summary, advanced control systems contribute to the efficiency of modern steam compressors by optimizing performance through real-time monitoring, predictive maintenance, energy-efficient technologies such as VSD, integrated automation and effective load management strategies. These innovations not only improve operational efficiency, but also reduce energy consumption and operating costs.
Conclusions
Mechanical vapor recompression represents a significant advance in industrial evaporation technologies. By maximizing energy recovery and minimizing waste, MVR systems not only improve operational efficiency, but also contribute to environmental sustainability.
As industries continue to seek innovative solutions for energy conservation and waste reduction, MVR technology will play a key role in shaping future industrial processes. Its applications in various sectors underscore its versatility and effectiveness in addressing modern industrial challenges.
Vapor compressors, particularly those using MVC technology, offer significant advantages in energy efficiency and high purity steam production. However, their implementation requires careful consideration of start-up procedures, operating conditions and system design. Ongoing research and technological advances continue to improve the performance and applicability of these systems in various industries.
References
- https://inspenet.com/articulo/compresores-de-vapor-eficiencia-industrial/
- https://link.springer.com/article/10.1007/s12206-016-1120-7
- https://www.mdpi.com/1996-1073/16/10/4199
- https://www.atlascopco.com/gas-and-process/en/pressure-points-blog/mechanical-vapor-recompression