Table of Contents
The rapid evolution of technology over the last decade has significantly impacted manufacturing industries around the world. With the advent of Industry 4.0, manufacturers are adopting advanced technologies such as automation, Big Data, and artificial intelligence to optimize processes, reduce costs, and improve product quality.
A key technology in this transition is non-destructive testing (NDT), which has become smarter and more integrated thanks to the modern concept of NDT 4.0, enhancing traditional testing methods with data-driven insights. This article explores how NDT, powered by digital tools and Industry 4.0, is revolutionizing manufacturing processes.
Understanding Non-Destructive Testing (NDT)
Non-Destructive Testing (NDT) refers to a variety of methods and techniques used to evaluate the properties or integrity of materials, components, or assemblies without causing damage to the inspected object. NDT methods, such as ultrasonic, radiography, and magnetic particle testing, have been instrumental for decades in ensuring the quality and safety of products in industries such as aerospace, automotive, oil and gas, and construction.
The main advantage of NDT lies in its ability to detect defects or inconsistencies in materials without affecting their usability. Traditional NDT methods rely heavily on the skill and experience of technicians, as well as manual data analysis. However, with the rise of Industry 4.0, the integration of data analytics, machine learning, and automation is transforming NDT into a more intelligent and efficient system, giving rise to the concept of NDT 4.0.
Industry 4.0 and its influence on manufacturing
Industry 4.0, often referred to as the fourth industrial revolution, is characterized by the digitization of manufacturing processes, driven by the convergence of cyber-physical systems, the Internet of Things (IoT), and artificial intelligence (AI). In essence, Industry 4.0 is about creating smart factories where machines and systems communicate seamlessly, making autonomous decisions based on real-time data to optimize production efficiency.
This revolution enables manufacturers to improve every stage of production, from design and material sourcing to quality control and distribution. The integration of advanced data analytics means that production processes can be monitored, controlled, and optimized with unprecedented accuracy. Sensors and IoT devices enable real-time data collection, while AI-powered systems analyze that data to identify inefficiencies, predict failures, and recommend improvements.
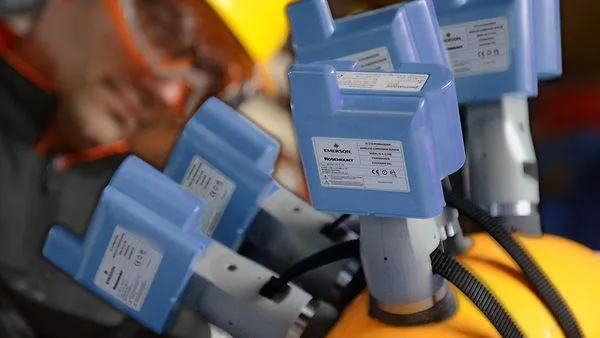
NDT in the context of Industry 4.0: From Traditional to NDT 4.0
While traditional NDT methods are effective in detecting defects in materials, their reliance on manual inspection and analysis can lead to inconsistencies and missed opportunities for optimization. With the advent of NDT 4.0, these tests have been transformed into a sophisticated system that leverages Big Data, AI, and IoT for real-time decision making and predictive maintenance.
Key aspects of NDT 4.0
Data collection and connectivity
In the era of Industry 4.0, the power of data lies in its ability to be continuously captured and analyzed in real time. Sensors installed on manufacturing equipment can now collect large amounts of data or Big Data during production, capturing every detail about the integrity of materials. These sensors are connected through IoT networks, enabling continuous monitoring of components. For example, ultrasonic sensors can detect micro-cracks in materials during the manufacturing process, sending data to cloud-based systems for immediate analysis.
The Internet of Things (IoT) refers to a network of physical devices, vehicles, appliances, and other physical objects that are integrated with sensors, software, and network connectivity, allowing them to collect and share data1.
Big Data in production describes the increasing amounts of data available and analyzed with the help of modern systems2. As companies are able to store the greater amount of data generated during the history of their production, more information will be available for processing and generating more accurate actions for process optimization.
Predictive analytics
Predictive maintenance is one of the most significant advantages of NDT 4.0. By analyzing historical data collected from NDT inspections, AI algorithms can identify patterns that indicate early signs of wear, potential failures, or defects. This predictive capability enables manufacturers to address problems before they escalate, reducing downtime and extending equipment life. Predictive analytics also optimizes maintenance scheduling, ensuring that inspections are performed only when necessary, thereby reducing unnecessary interventions.
Automation and Artificial Intelligence
One of the limitations of traditional NDT methods is the human factor. NDT 4.0 minimizes this dependency by introducing AI-driven automation. AI can process large amounts of NDT data faster and more accurately than human inspectors, making it possible to detect minute defects that would otherwise go undetected. In addition, AI systems can learn from previous data, continuously improving their detection capabilities. Automated NDT systems can scan components during production without stopping the manufacturing process, ensuring that quality control is an integrated part of production rather than a separate step.
Real-time decision making
NDT 4.0 enables real-time decision making by integrating NDT systems with manufacturing execution systems (MES) and enterprise resource planning (ERP) systems. This integration allows manufacturers to make data-driven adjustments instantly, optimizing production parameters in response to detected anomalies. For example, if an NDT system identifies a potential defect in a batch of products, the MES can automatically adjust machine settings or redirect defective parts for further inspection, minimizing waste and reducing the risk of defective products reaching customers.
The interconnection between machines through the Internet of Things (IoT)3 ensures that solutions can be achieved through systems and independently implement the functions for which they were designed.
How can NDT 4.0 reduce production costs?
NDT 4.0 leverages advanced technologies such as AI, IoT, and Big Data analytics to revolutionize non-destructive testing, making inspections faster, more accurate, and automated. By enabling real-time data monitoring and predictive maintenance, manufacturers can detect potential problems early, reducing the likelihood of defects, minimizing downtime, and preventing costly failures.
This proactive approach enables more efficient resource management, reduces material waste, and improves product quality. As a result, companies can lower production costs, improve operational efficiency, and increase profitability by avoiding expensive repairs, rework, or interruptions in the production process.
Benefits of data-driven NDT in manufacturing
The adoption of NDT 4.0 and data-driven NDT offers manufacturers numerous advantages that align with the overall goals of Industry 4.0:
- Improved quality control: Data-driven NDT systems can monitor and evaluate product quality at every stage of production, ensuring consistent compliance with quality standards. This level of accuracy reduces the likelihood of defects and increases customer satisfaction.
- Reduced costs and downtime: Through predictive maintenance, NDT 4.0 helps manufacturers avoid unplanned downtime and costly repairs. Early detection of problems also minimizes waste of materials and resources, which reduces production costs.
- Improved safety: In industries such as aerospace and oil and gas, material integrity is critical to safety. Data-driven NDT provides a higher level of assurance that components are free of defects, reducing the risk of catastrophic failure and ensuring compliance with safety regulations.
- Increased efficiency and productivity: Automated and AI-based systems optimize the inspection process, reducing the time required for manual inspections and enabling manufacturers to produce more in less time. Real-time data analysis ensures that production processes are continuously optimized for maximum efficiency.
Challenges and the future of NDT 4.0
Despite its advantages, implementing NDT 4.0 is not without its challenges. Integrating NDT systems with Industry 4.0 technologies requires significant investments in infrastructure, data management, and employee training. In addition, concerns about data security and privacy arise when sharing sensitive information across connected networks.
However, as the Industry 4.0 revolution continues to unfold, the future of NDT 4.0 looks promising. Innovations in AI, machine learning, and IoT will continue to enhance NDT capabilities, making them even more integral to modern manufacturing processes. The trend towards “smart factories” means that NDT will evolve from being a separate quality control step to becoming a fully integrated part of the production process.
Conclusion
The optimization of manufacturing processes through non-destructive testing, powered by data-driven insights and Industry 4.0 technologies, marks a new era in quality control and process efficiency. NDT 4.0 has revolutionized traditional NDT methods, turning them into intelligent systems capable of predicting failures, improving product quality, and reducing costs. As manufacturers continue to embrace the principles of Industry 4.0, the role of NDT will become increasingly vital, ensuring that production processes are not only optimized but also safer and more sustainable for the future.
References
- IBM. What is the IoT?; Accessed October 09, 2024. https://www.ibm.com/topics/internet-of-things
- MAXIMILIAN TOP. The NDT 4.0 Guide – Everything you need to know.; Accessed October 10, 2024. https://sentin.ai/en/the-ndt-4-0-guide-everything-you-need-to-know/
- RAHUL ALREJA. NDT and Industry 4.0; Accessed October 11, 2024. https://www.qualitymag.com/articles/95370-ndt-and-industry-40