Introduction
Non-Destructive Testing (NDT) is a discipline within materials engineering that consists of different methods and techniques. NDT methods allow the inspection of materials and components without causing any damage, which makes them invaluable in the evaluation of the integrity of structures and materials. These methods make it possible to detect hidden defects, assess the quality of materials, and ensure safety in different applications, especially when applied with a predictive approach.
NDT is significant in ensuring the integrity and safety of equipment and structures within the petroleum industry, ensuring continuity of operations and economic benefit. This article explores the main types of nondestructive testing and their applications in the petroleum industry.
Main types of Non-Destructive Testing
Ultrasound (UT)
Ultrasonic Testing (UT) is one of the main types of non-destructive testing used in the petroleum industry, which employs high frequency sound waves to detect internal defects or to characterize materials. The sound waves are introduced into the material being inspected, and the signals from the flaw reflections, characterized by amplitude and travel time or distance, are captured to create a visual or digital record related to the condition of the internal structure.
It represents the testing method with the greatest technological advances in the last decades with contributions such as: Phase Array Ultrasound (PAUT), Time of Flight of Diffraction (TOFD), and Total Focusing Method (TFM), among others. TFM is the most efficient method to generate high-resolution images of a region of interest (ROI) thanks to dedicated focusing at all angles and at every depth level1.
Applications in the oil industry
- Corrosion assessment: In the oil and gas sector, corrosion represents a significant threat to pipelines, pressure vessels, offshore platforms, and storage tanks. Ultrasonic testing in its different techniques allows for comprehensive inspection of these assets, enabling early detection of damage and maintenance planning. In pipelines, ultrasound is widely used for thickness monitoring at selected control points known as corrosion monitoring locations (CMLs). Corrosion mapping (C-Scan) through PAUT or higher resolution and 3D imaging through TFM offers better insight and visualization of the internal condition of the inspected component. Figure 1 shows equipment with TFM imaging in weld inspection.
- Welding inspection: Welding is an important process in the construction of various components such as: structures, pipelines, pressure vessels, and storage tanks in the oil and gas industry. The UT is used for quality assurance of welds, ensuring that they are free of defects that could cause subsequent failures in service containment, undesired events, and stoppage in the continuity of operations.
- Service crack detection: Several components, such as: pipelines and pressure vessels, can generate cracking processes in welded joints or very close to them, due to the internal service conditions they handle. That is why selected areas known as corrosion monitoring locations are inspected with a certain frequency for the early detection of this type of failures, being ultrasound an ideal test method for these inspections (CMLs).
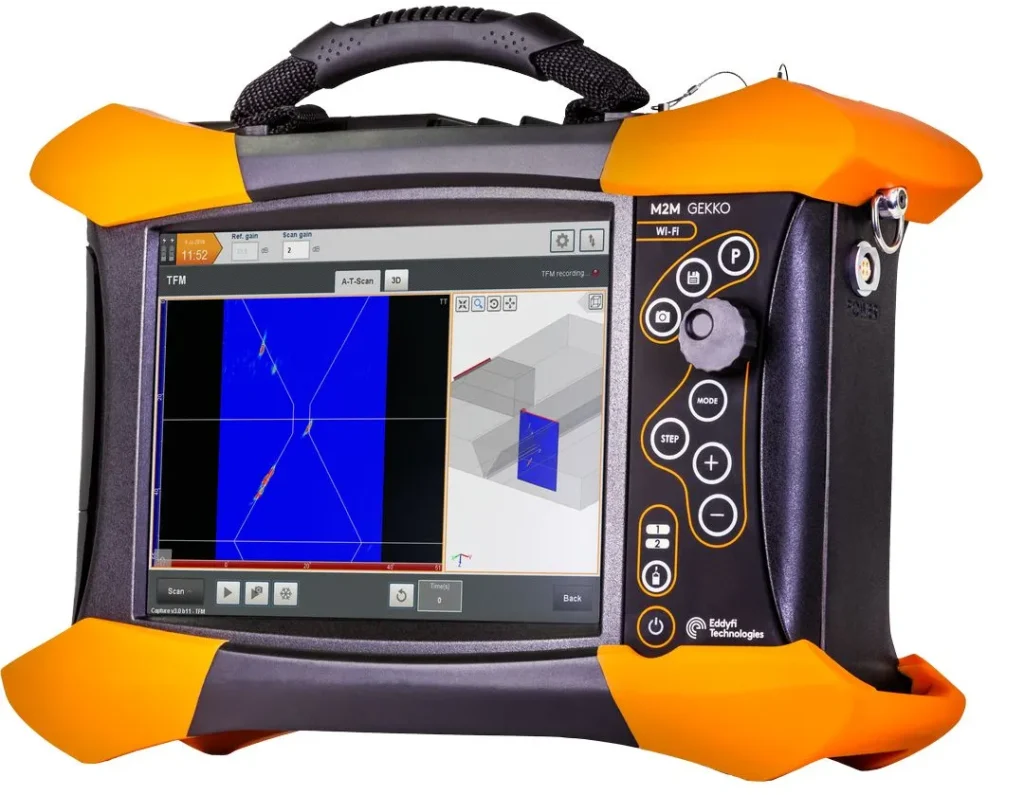
Industrial Radiography (RT)
Industrial radiography or radiographic testing (RT) uses X-rays or gamma rays to produce images of the internal structure of a component by passing this radiation through the inspected part and onto a recording medium, such as radiographic film, which is then processed to provide an image of the condition of its interior. This method is particularly useful for detecting internal defects, such as voids, cracks, and inclusions, as well as visualizing the elements inside instruments or fixtures.
This method is one of the types of non-destructive testing that has also brought great technological advances in recent decades, such as digital and computerized radiography, which have been increasing their use in the oil and gas sector.
Applications in the oil industry
- Pipe inspection: RT is used to inspect process piping, as well as furnace pipes for foreign objects, loss of thickness in pipes under insulation, sediment formation, clogging, among others, that could compromise process efficiency and structural integrity.
- Valve and pump inspection: Ensuring the reliability of valves and pumps is critical in the oil industry. RT helps to detect loosening or poor positioning of internal elements that could affect their performance, such as dropped valve gates.
- Welding inspection: Welding is a critical process in the construction of various components, such as: structures, pipelines, pressure vessels, and storage tanks in the oil and gas industry. UT is used for quality assurance of welds, ensuring that they are free of defects that generate subsequent failures in service containment, undesired events, and stoppage in the continuity of operations.
- Inspection of castings and forgings: RT is used to inspect castings and forgings for internal defects, ensuring that they meet the required quality standards, such as cast valve bodies.
Magnetic Particle Testing (MT)
Another of the most commonly used type of non-destructive testing is Magnetic Particle Testing (MT), which is used to detect surface and slightly subsurface discontinuities in ferromagnetic materials. The method involves magnetizing the material and applying ferrous particles that are attracted to the magnetic leakage fields generated by the flaws, revealing their presence.
Applications in the oil industry
- Weld inspection: It is commonly used to inspect welds in pipelines, pressure vessels, storage tanks, and other critical structures for cracks and surface defects. It is mainly used in fillet-type welds due to the difficulty of evaluating with volumetric tests such as UT and RT, and in butt groove welds to follow up the different passes and seeking to minimize the rejection of the final inspection with UT or RT and the final hydrostatic test.
- Drill pipe inspection: Drill pipes are subject to high stresses and wear. MT helps detect cracks and other defects that could cause failures during drilling operations.
- Inspection of structural components: Various structural components on oil platforms and refineries can be inspected using MT to ensure their integrity and safety.
- Inspection of rotating parts: Rotating equipment parts made of ferromagnetic material, such as shafts, rotors, and crankshafts, can generate cracks due to the service conditions to which they are exposed. The magnetic particle testing method is ideal for the inspection of these types of components in the search and detection of these types of failures.
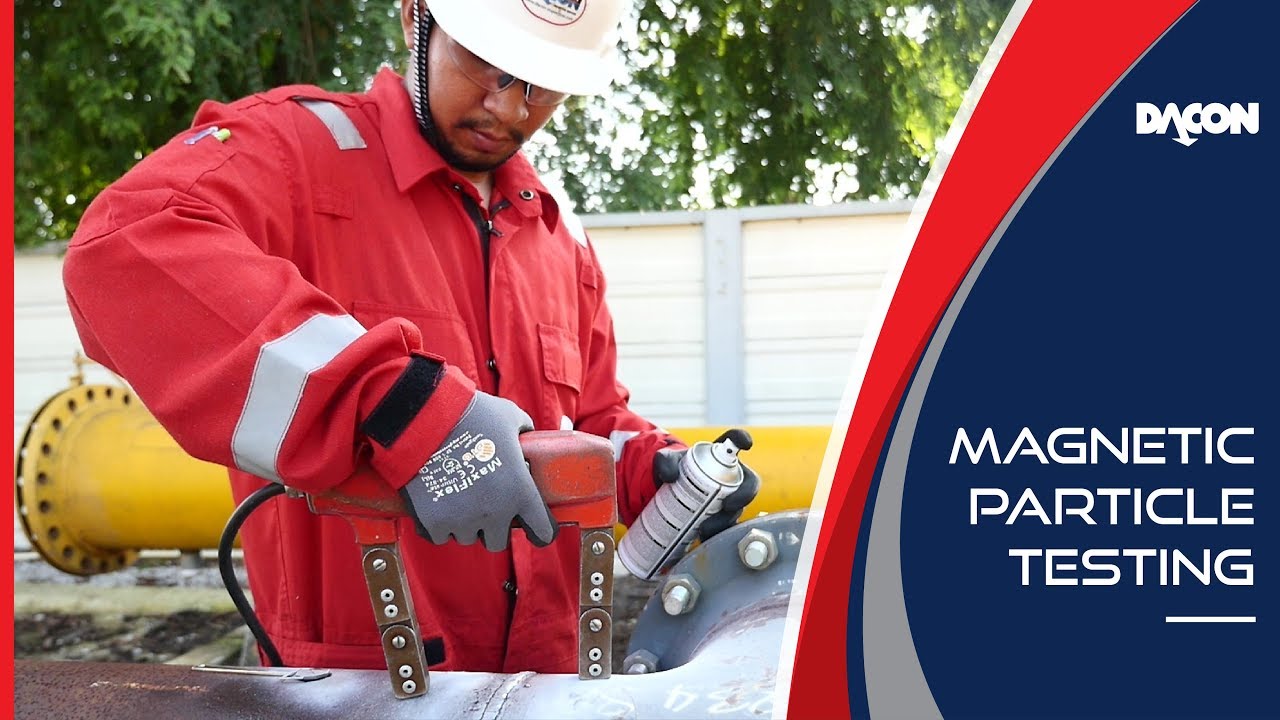
Magnetic Particle Testing (MT): NDT Inspection Technique.
Penetrant Liquid Test (PT)
The Penetrant Testing (PT) method is used to detect surface defects in non-porous materials. The process involves applying a liquid of high capillarity and provided with a contrasting pigment (red for visible penetrants, green for fluorescent penetrants), to the clean surface of the component to be inspected, allowing it to infiltrate into cracks and defects. After a certain time of stay inside the possible flaws and subsequent cleaning of the surface, a white developer is applied by spraying to extract the penetrant from the flaws making contrast with it, and thus making the flaws visible.
Applications in the oil industry
- Weld Inspection: Liquid penetrant testing, like magnetic particle testing, is one of the most commonly used types of non-destructive testing to inspect welds on pipelines, pressure vessels, storage tanks, and other critical structures for cracks and surface defects. It is mainly used in fillet-type welds due to the difficulty of evaluating with volumetric tests such as ultrasonic and radiography, and in butt groove welds for the follow-up of the different passes and in order to minimize the rejection of the final inspection with Ultrasonic or Radiography and the final hydrostatic test. Figure 2 shows an example of the application of the Liquid Penetrant test in weld inspection.
- Inspection of structural components: Various structural components on oil platforms and refineries are inspected using liquid penetrants to ensure their integrity and safety.
- Inspection of rotating parts: Rotating equipment parts of various materials, such as shafts, rotors, and crankshafts, can generate cracks due to the loading conditions to which they are subjected. The Liquid Penetrant test method, as well as magnetic particles, is ideal for the inspection of this type of component in the search and detection of this type of failures.
- Inspection of pipeline components: Various components such as flanges, valves, and fittings can be inspected using a liquid penetrant to detect cracks and surface defects.
- Turbine blades: Turbine blade arrangements can be inspected (even on-site) using liquid penetrant and post-emulsifiable techniques in order to maintain sensitivity to the criticality of the component.
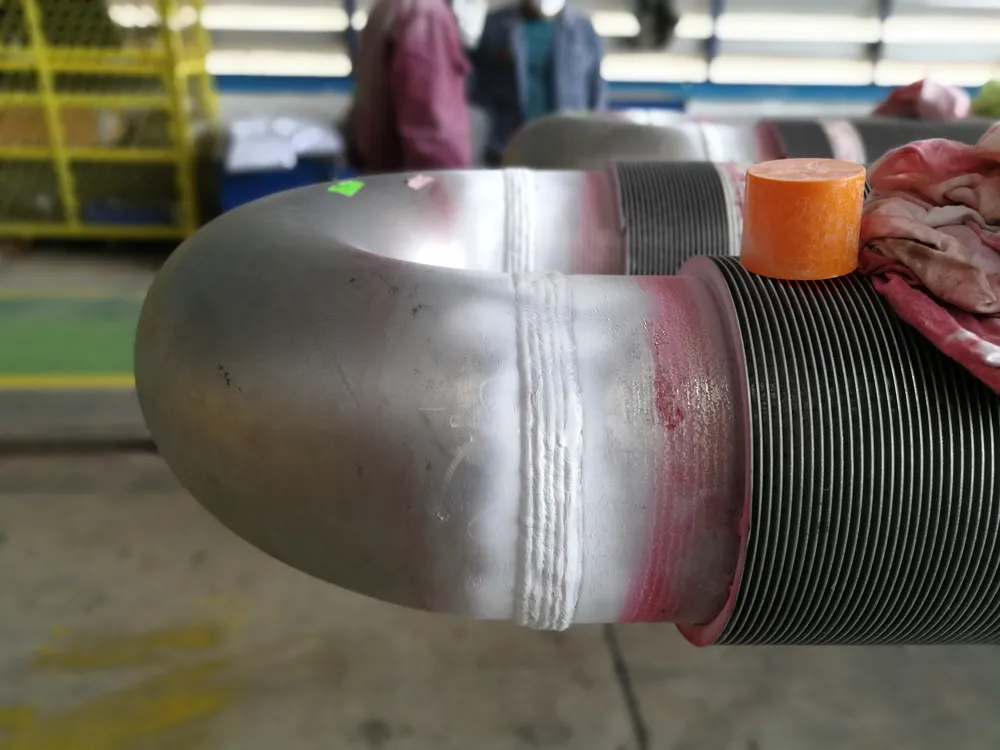
Eddy currents (ECT)
Eddy Current Testing (ECT) is a technique within the Electromagnetic Testing (ET) method. ECT uses the phenomenon of electromagnetic induction to detect defects in conductive materials. Basically, it consists of exposing the surface of a conductive material to an alternating magnetic field provided by an inductor (e.g. a coil) which has an electrical resistance, generating an alternating current at the surface of the component and slightly below it.
These induced currents in turn generate a magnetic field that opposes the inductor magnetic field and thus offering an extra resistance to the inductor which is known as reactance. The vector sum of the resistance and reactance in the inductor is the total impedance and this varies with the presence of defects on the surface of the component on which the variable magnetic field is applied, as well as with the change in the electrical properties of the component.
The test then consists of visualizing the variation of the impedance of the inductor element on the screen of the equipment (impedance plane), which can be associated with the presence of discontinuities in the inspected component or changes in its electrical properties.
This technique is another type of non-destructive testing widely used in the oil and gas sector that has brought great advances in recent decades with technologies such as Eddy Current Array (ECA) for the inspection of heat exchanger tubes in which an image of the surface with the defects (C-Scan view) is displayed and circumferential cracks are easily detected.
Another advance applied to ferromagnetic materials is the Pulsed Eddy Current Array (PECA) technique for the detection and evaluation of Corrosion Under Thermal Insulation (CUI), which is a phenomenon that normally affects carbon steel piping and pressure equipment as a result of water ingress or condensation under the thermal insulation2, and Corrosion Under Fireproofing (CUF), in which a C-Scan view is also shown.
Applications in the oil industry
- Heat exchanger tube inspection: ECT is commonly used to inspect heat exchanger tubes for corrosion, erosion and cracks.
- Weld inspection: ECT is used to detect surface defects and corrosion in welds of pipelines and pressure vessels made of conductive material, ensuring their safety and reliability.
- Component inspection: Various conductive material components such as bolts, nuts, and fasteners, can be inspected using ECT for cracks and surface defects.
- Corrosion detection under thermal insulation and fireproofing: Through the advanced variant of PECA it is possible to detect corrosion zones under thermal insulation (CUI) and under fireproofing (CUF) with an approximate measurement of the remaining thickness.
- Inspection under scabs (corrosion): Sometimes scabs or scale, a product of surface corrosion, present a risk in their removal with the component in service due to the uncertainty of the remaining thickness and the possibility of leakage of the highly hazardous fluid. The PECA technique can also be used in the evaluation of these areas not requiring the removal of these incrustations.
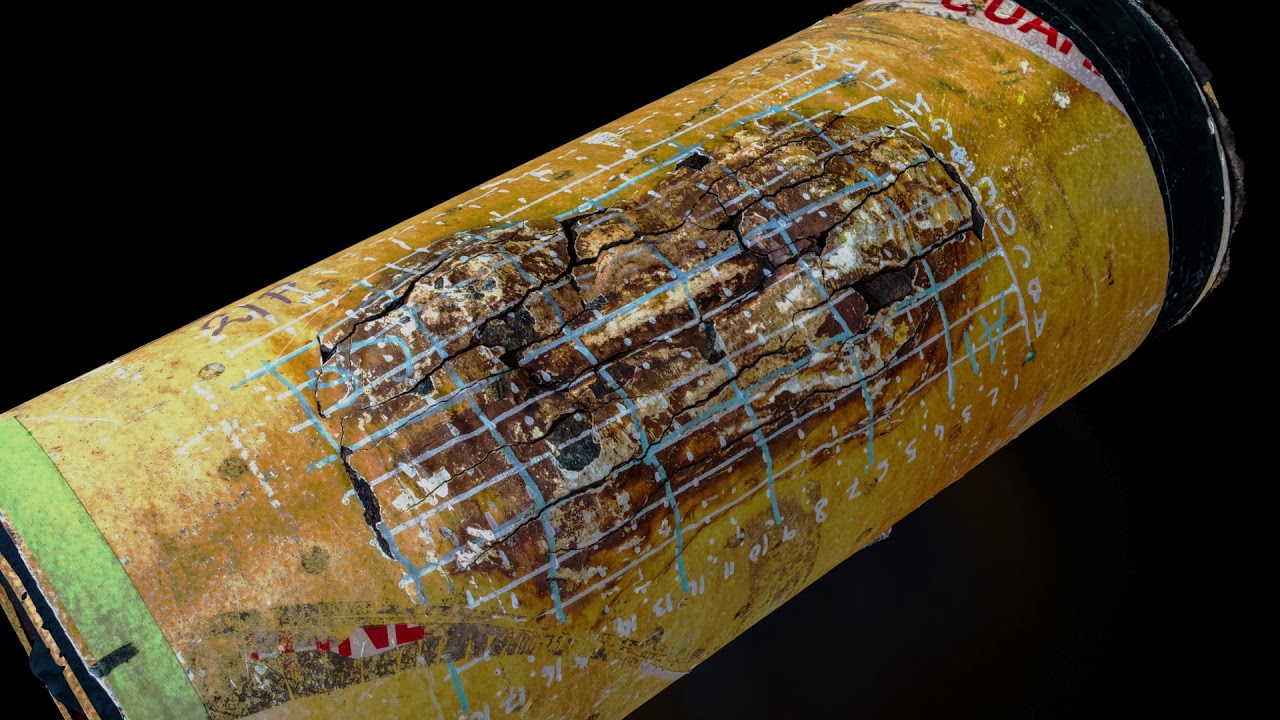
New PECA solution for inspections under scabs.
Visual Inspection (VT)
Visual inspection is one of the oldest and simplest types of nondestructive testing. It involves visual inspection of materials and components, often with the aid of tools such as magnifying glasses, borescopes, and cameras.
Applications in the oil industry
- Routine maintenance inspections: It is commonly used for routine inspections of equipment and structures, allowing early detection of visible defects. Through the use of borescopes and video scopes, inspections can be performed in places inaccessible for direct visual inspection, such as the case of heat exchanger tubes, boilers, turbines, and machinery.
- Weld inspection: Used to inspect welds for surface defects such as cracks, porosity, and surface undercuts.
- Corrosion inspection: Detects surface corrosion and other visible signs of degradation in pipes, tanks, and other structures.
Acoustic Emission (AET)
This technique is used to capture high-frequency sound waves emitted by materials under stress, such as a gas sphere under internal pressure using the same service or other inert gas. This method is effective in detecting areas with active defects internally or externally, and monitoring the integrity of the structures in real-time when it is not required to open the component (pressure vessels, storage tanks, among others).
It is a screening technique, i.e., it is used to detect areas where some material deterioration activity is taking place, but it does not characterize or quantify the failure, for which other NDT methods, such as UT, must be applied later. In spite of being a screening method, this test is of great value, since it allows to define the specific areas to be inspected with other test methods and to decide when the equipment needs to be intervened.
It is one of the types of nondestructive testing that serves as a tool to provide information to methodologies such as Risk Based Inspection (RBI), and thus generate a schedule for the maintenance of equipment (pressure vessel, tank, among others), and thus make better planning of the resources needed for repair activities.
Applications in the oil industry
- Pipeline monitoring: Used to monitor pipelines for signs of cracks, corrosion, and other defects while in operation.
- Inspection of pressure vessels: It is used to detect and locate defects in pressure vessels, ensuring their safe operation.
- Tank inspection: Detects defects in pressure vessels both on the walls and on the floor, ensuring their reliable operation.
- Structural monitoring: Various structures such as oil platforms and storage tanks are monitored using this technique to detect active defects and ensure their integrity.
Infrared Thermography Test (IRT)
The thermographic testing method, also known as infrared thermography, uses infrared cameras to detect thermal anomalies on the surface of materials and components by imaging the distribution of skin or component surface temperatures. These anomalies may indicate underlying defects or areas of concern.
Applications in the oil industry
- Pipeline inspection: Used to detect faults such as insulation problems, and corrosion under insulation in pipelines. It is particularly useful to identify hot spots that indicate problem areas such as plugging or deterioration of internal refractory.
- Electrical systems inspection: Detects hot spots in electrical systems and components, which could indicate faulty connections or over voltage, which could cause failures or fires if not detected in advance.
- Heat exchanger inspection: Locates blockages, fouling, and other problems in heat exchangers by identifying abnormal temperature distributions.
- Tank and vessel inspection: It is widely used to inspect storage tanks and pressure vessels for signs of corrosion, leaks, lack of level, and other defects that could compromise their operational integrity.
- Detection of combustible gas leaks: By using intermediate wavelengths in the infrared spectrum range, it is possible to detect flammable gas leaks, which is of great value in avoiding catastrophic events in the oil and gas industry.
Guided Waves (GWT)
Guided waves are ultrasonic waves propagating along a structure and guided by its geometrical boundaries. It is a technique to find the location of the defect and estimate the size of the defect using the arrival time and the amplitude of the ultrasonic signal, respectively. The operating frequency of GWT is usually low (5 to 250 kHz) compared to ordinary ultrasonic testing. The low-frequency operation helps to generate non-dispersive ultrasonic guided waves and reduces attenuation for long-range pipeline inspection.
This test is used as a screening inspection for areas where corrosion activity is taking place. Although it can give an estimate of the damage, other NDT methods such as UT and RT are required to characterize and quantify the failure in detail. A variant or technique within the test known as Short Range Guided Waves (SRGWT), allows for certain inspections such as inspection under pipe supports. When used with electromagnetic acoustic transducers (EMAT), these inspections show a higher resolution and sensitivity, being able to characterize and quantify the faults in detail.

Guided Wave Ultrasonic Inspections – GUL.
Applications in the oil industry
- Pipeline inspection: It is widely used to inspect long pipeline sections, as well as thermally insulated pipelines for the detection of areas with corrosion activity, in order to subsequently define those areas to be evaluated with other NDT methods.
- Pipeline monitoring: Currently, it is applied for continuous monitoring of long stretches of pipelines in which the sensors and their connections to the instrument are fixed, and the signals are constantly monitored to detect variations in amplitudes and thus anticipate areas with gestation of corrosion activity.
- Corrosion detection under pipe supports: Through the Short Range Guided Wave Technique (SRGWT), areas under supports can be inspected in detail when combined with EMAT technology for ultrasonic wave generation. Figure 3 shows an application of SRGWT in the inspection of the area below the pipe on the support.
- Inspection of the annular section of tank floors: By means of Short Range Guided Waves (SRGWT), the annular area of the floor inside the storage tank next to the wall can be inspected. This inspection is performed from the outside of the tank by sweeping the transducer over the outer lip of the annulus.
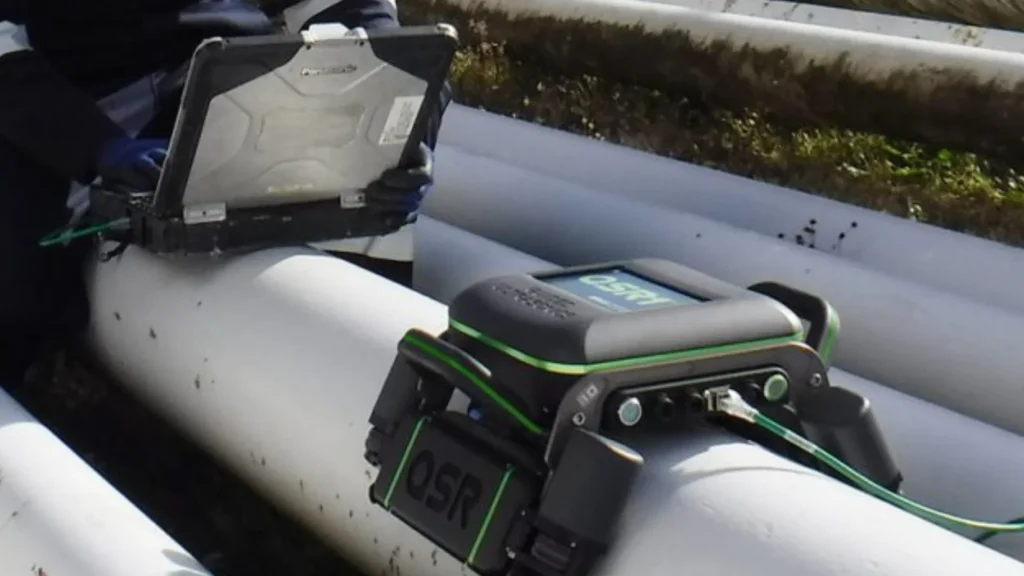
Figure 3. Inspection of under pipe on support by SRGWT. (Source: Guided Ultrasonics)
Conclusions
Non-Destructive Testing plays a vital role in the oil industry by ensuring the integrity and safety of equipment and structures. Each method has its unique advantages and applications, making them suitable for different types of inspections. By employing these NDT methods, the oil industry can maintain high safety standards, prevent costly failures, and ensure the reliable operation of its critical infrastructure.
The implementation of Non-Destructive Testing is crucial to the ongoing maintenance, safety inspections, and overall operational integrity of the oil industry primarily with a predictive approach by implementing inspection plans for early detection of defects. By implementing and upgrading to new technological advances in NDT, the oil industry can achieve greater reliability and safety in its critical infrastructure, ultimately contributing to a safer and more sustainable energy future.
References
- EVIDENT. Using the Total Focusing Method to Improve Phased Array Ultrasonic Imaging; Consulted on July 15, 2024. https://www.flir.com.mx/discover/professional-tools/thermal-camera-specs-you-should-know-before-buying/
- JESÚS CONTRERAS. Advanced NDT techniques for the detection of Corrosion Under Insulation (CUI); Consulted on July 16, 2024. https://inspenet.com/en/articulo/advanced-ndt-techniques-for-the-detection-of-corrosion-under-insulation-cui/