Stress Corrosion Cracking (SCC) is dangerous because it can destroy a component at stress levels below the tensile strength of an alloy. This phenomenon manifests itself under two main conditions: high pH SCC and almost neutral SCC.
This chemical-mechanical process is complex and results in the formation of cracks in certain alloys when they are subjected to stresses below their strength limit. For it to occur, three elements must come together: a susceptible alloy, the appropriate chemical conditions, and sustained tensile stress.
In sectors such as the oil and gas industry, where pipelines play a central role in operations, the phenomenon of stress corrosion cracking in pipelines often arises. This is due to excessive stresses generated by high pressure and the presence of corrosive factors in the environment. Initially, these cracks are often difficult to detect, but they tend to grow over time. This type of process piping failure can have a significant impact on the functionability and safety of an operation.
Factors that influence its development
Stress-assisted corrosion is an anodic process, which is verified by the applicability of cathodic protection as an effective solution measure. Usually, there is an induction period, during which cracking originates at a microscopic level. This is followed by branching propagation. Eventually, and to a large extent, the cracks can self-arrest, as in the typical multibranched transcrystalline stress corrosion cracking (Figure 1), apparently due to localized mechanical stress relief 1 .
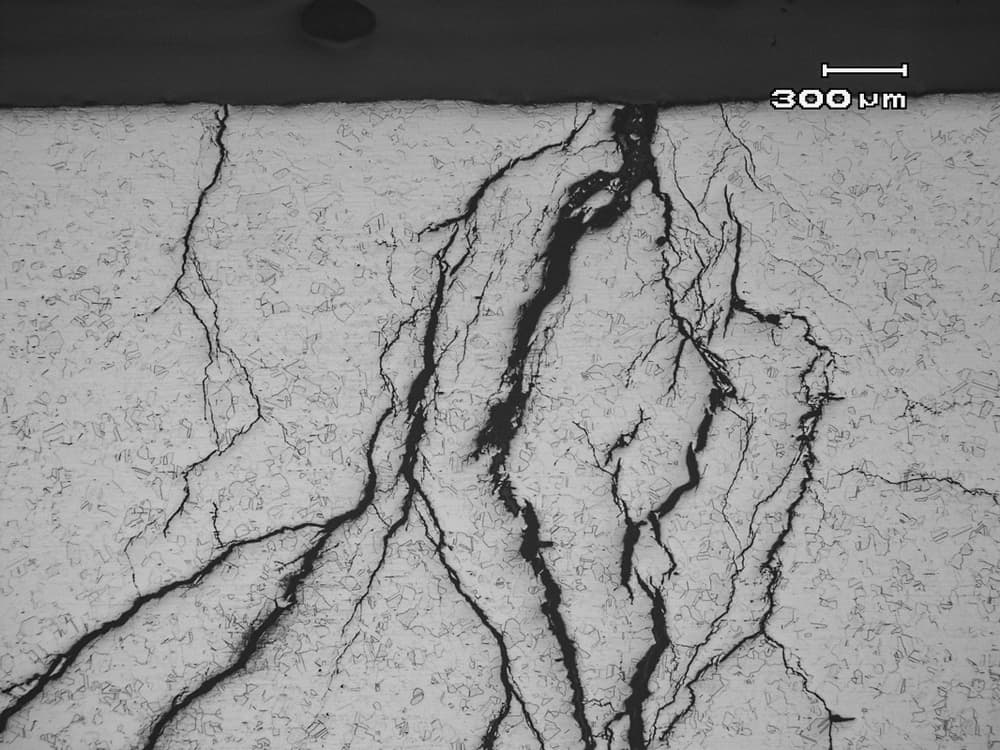
It is a phenomenon that occurs when a steel material cracks when exposed to certain corrosive agents, at stress levels significantly lower than those considered in its design. This process is triggered due to the simultaneous action of the corrosive environment and the mechanical forces to which the material is subjected. The stresses that produce SCC can be residual stresses that persist in the material, applied stresses, or sometimes a combination of both.
Stress corrosion represents a significant risk as it can lead to component failure in a surprisingly short period of time. Often, the presence of SCC is not evident to the naked eye, making it particularly dangerous when colonies of cracks form in the material, because these cracks can cause ruptures in the component when a change in pressure occurs. the one who is subjected. In most cases, these ruptures cause serious consequences in terms of safety and operability 2 .
In addition to stress, other factors can accelerate or aggravate this type of corrosion. The temperature of the environment plays a significant role, since it influences the corrosion rate and the diffusion of corrosion products. Environments with a high concentration of the corrosive solution also tend to accelerate the process, due to which there is an increase in the rate of localized corrosion and, therefore, the propagation of cracks.
The mechanism of SCC is a major challenge in the industry as it can occur in a variety of conditions and materials. Understanding the mechanisms that cause it and the factors that influence its development is essential to implement effective prevention and mitigation strategies for this type of corrosion in a wide range of industrial applications.
SCC control and mitigation strategies
Effective control of stress corrosion cracking (SCC) is a critical component in managing the integrity of structures exposed to this phenomenon. Given that in most cases the influencing factors remain relatively constant, this problem requires specific maneuvers to prevent and mitigate its harmful effects. Below are some strategies to mitigate this type of corrosion.
- Minimize or control the stress level: Through stress-relieving heat treatments, shot peening, or by designing components to distribute stress evenly.
- Selection of resistant materials: The choice of materials plays a considerable role in preventing Stress Corrosion. These materials generally have greater resistance to stress corrosion and, consequently, are less susceptible to crack formation.
- Apply protective coatings: Providing a barrier to the corrosive environment, reducing the likelihood of SCC.
- Environmental control: Control temperature, humidity and concentration of corrosive species.
- Regular inspections: These inspections may include nondestructive evaluation techniques, such as radiography, ultrasound, and visual inspection.
- Cathodic Protection (CP): It is a valuable tool in the control and mitigation of corrosion. This technique consists of applying electric current to polarize metal structures and reduce the rate of corrosion. Through this control method, the electrochemical potentials of metal surfaces are modified, reducing the formation of cracks. CP is particularly effective in environments where stress corrosion is a recurring problem.
The control and mitigation of SCC are critical aspects in managing the integrity of structures and components exposed to this phenomenon. The combination of strategies including maintenance of potentials, selection of resistant materials, regular inspections and cathodic protection are essential to control stress corrosion problems and ensure the safety and durability of structures in a variety of industrial applications.
Practical cases
Additional examples of situations in which cases of SCC have occurred in various alloys are presented below.
- In steel with less than 0.01% carbon, along with small amounts of manganese, sulfur and silicon, in a high-temperature ammonium nitrate solution.
- In commercial titanium containing 600 ppm oxygen and 100 ppm hydrogen in specific environments.
- Cracking of copper containing 0.004% phosphorus or 0.01% antimony in the presence of ammonia (NH 3 ) or ammonium ions.
- In stainless steel, austenitic in chemical process applications, where the presence of chlorides in an aggressive environment triggers SCC.
- Cracking of aluminum alloys in marine environments, particularly in components exposed to salinity and humidity.
- In duplex steel in offshore oil and gas applications, where the combination of chlorides and sulfides in acidic environments can trigger SCC.
- Cracking of carbon steel in drinking water pipes containing traces of ammonia, resulting in stress corrosion in non-corrosive environments.
These case studies demonstrate the diversity of situations in which SCC can occur and highlight the importance of comprehensive corrosion management to prevent integrity problems in a wide range of industrial applications.
Conclusion
Stress Corrosion cracking is a critical phenomenon in the integrity of materials and structures, particularly in industries such as oil, gas and energy. Understanding its mechanisms is essential to implement effective control and mitigation strategies.
Bibliographic references
- BORN; “Basic Corrosion Course, NACE International, 2004”, 01/15/04; p. 5-45
- Herbert H. Uhlig; Corrosion and corrosion control; Urama Editions SA