Table of Contents
Introduction
The increase in the consumption of hydrocarbons in the world created the need to increase their transport by sea, which was also reflected in the increase in the size of ships, sizes that required appropriate port facilities that facilitate their attention in any sea condition. and taking into account the limitations of the Ports. Likewise, the largest oil deposits are not close to the large consumers, which requires a high hydrocarbon transport service by sea.
This increase in the size of the world tanker fleet brought with it an increase in the risks associated with its operation in areas of high population density and areas of high maritime traffic.
It was then imposed the need to adopt other hydrocarbon transfer systems that would allow the large tankers not to enter the port, but to arrive near it, thus reducing maritime traffic in restricted waters, the risks of marine and river pollution and allowing these large ships to be serviced in deep waters, a necessary condition due to their large drafts.
To this end, several technologies were developed, such as multi-buoy terminals, artificial ports with large breakwaters (a very expensive alternative), artificial islands in the high seas (a high-cost and high-risk alternative), and SPM (single point mooring), among others.
The development of monobuoys or SPM began in the 1920s but it was only in the 1950s that the first patent was registered. The MONOBUOYS basically consist of a cylindrical or square floating body divided into two parts, one that we can call fixed, to which the anchoring systems are incorporated at the bottom, and the other that rotates on top of the previous one, which is the one that supports the boat mooring facilities.
SPM System Overview
A monobuoy is a self-floating structure that allows a tanker to moor and at the same time deliver or receive, through it, any type of hydrocarbon, allowing the attention of large vessels with large drafts, since they can be installed at any depth, being its connection to land through an underwater pipeline.
The monobuoy or “Single Point Mooring” allows the ship moored to it to rotate freely around its structure, locating itself in the same direction of the wind and the sea current, in such a way that the ship moored to the SPM offers the least resistance to the forces of waves, currents and winds (figure 1).
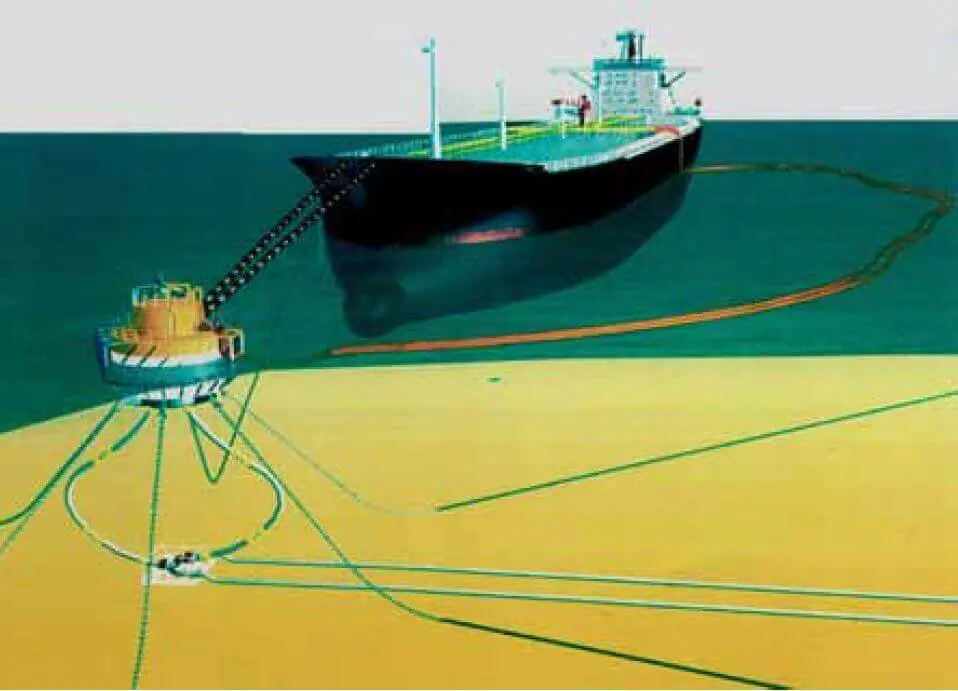
The SPM is widely used, given its relatively low operating cost, its operational safety and its flexibility of use, it basically consists of a circular buoy whose diameter varies from 10 to 17 meters, anchored to the seabed by means of 6 u 8 mooring chains, which are secured to the bottom by anchors or buried piles.
Above the buoy there is a rotating structure mounted on roller bearings that allows 360 degree rotation. This rotating structure is equipped with pipes, valves, connections, navigation and control instruments and to which the floating hoses are connected (Figure 2).
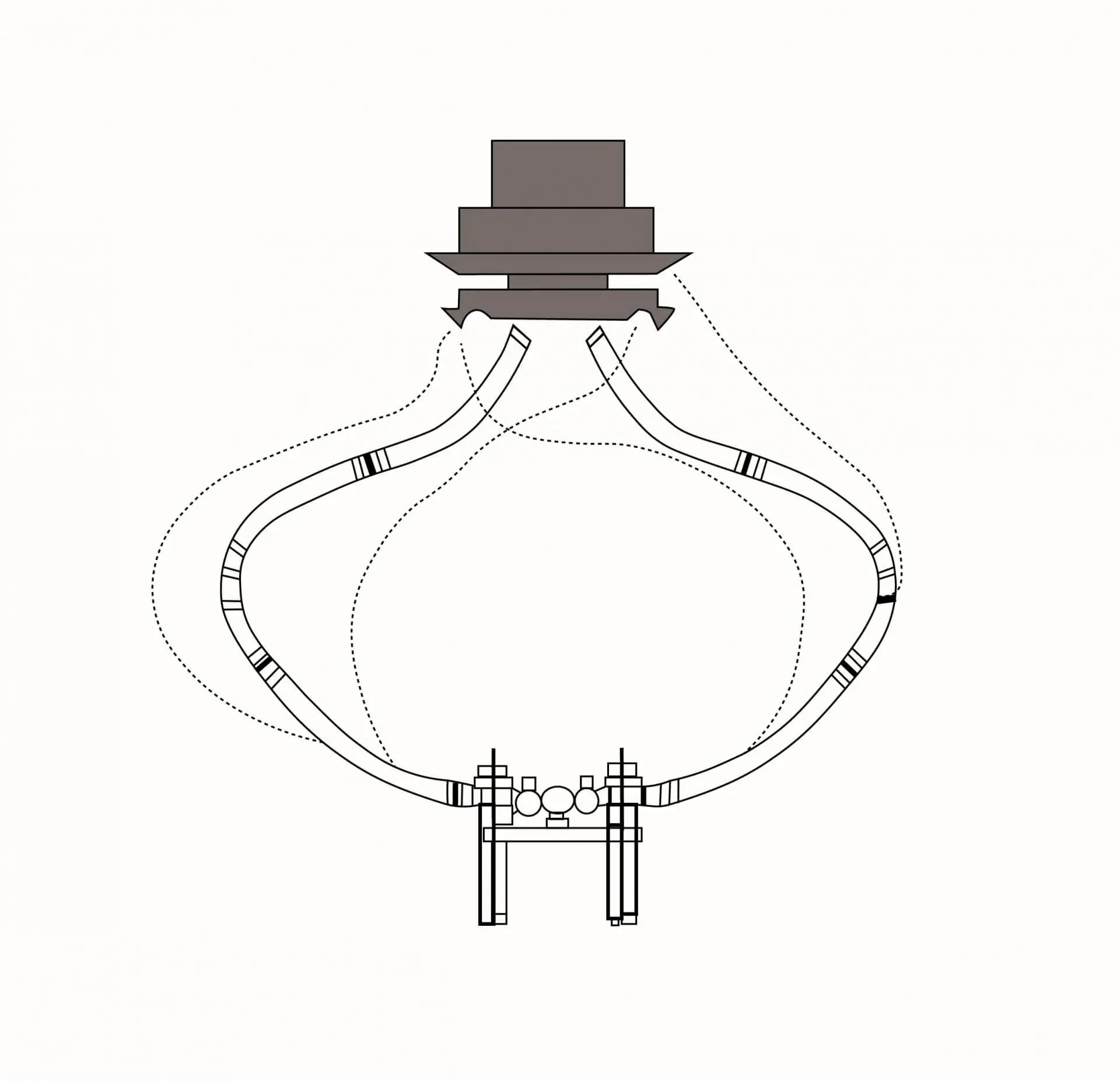
The floating hoses are installed in the rotating cover to a pipe that is located outside the body of the buoy. The length of these hoses is determined by the size of the ship, the location of the multiple mooring equipment available, (figure 3).
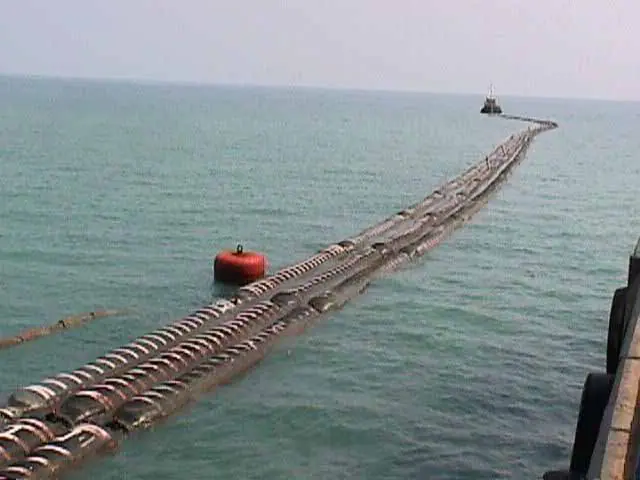
The underwater hoses under the SPM allow the connection between the body of the buoy and the underwater pipeline in the PLEM (pipe line end manifold). (Figure 4).
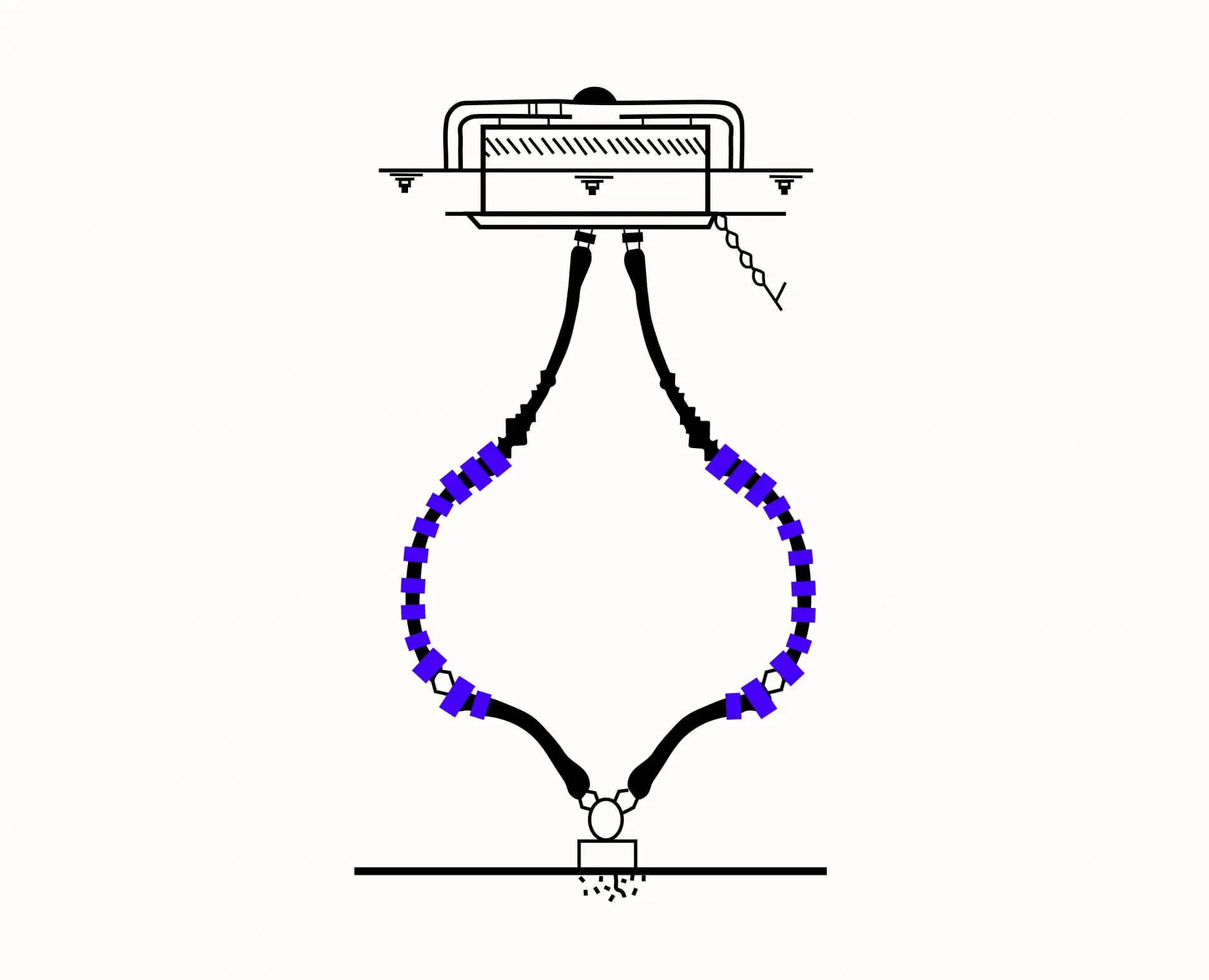
Today the regular channel to acquire a monobuoy is to contact a company that builds (normally they also design) the assets and that has the approval of a certification house, this is an endorsement not only of the design, but also of the quality. construction materials and procedures such as welding and other structural elements.
In summary, three generations of SPM have passed, the first generation was built with wheels and rails, the second was the so-called “turntable” or rotary table, even today these designs are functional and are marketed; and the third generation is the turret, as mentioned above these designs are known as SPM (Single Point Mooring). In figure 5, each type of design is shown.
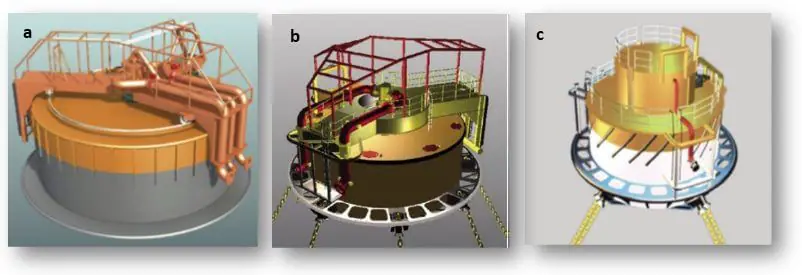
Conclusion
As a final conclusion, it is showing that the transfer of the monobuoy out to sea is very beneficial and efficient in crude oil loading and unloading operations with a larger draft ship.
The advantage of the relocation is to monopolize the total capacity of the ships in the trips that are necessary for the distribution and processing of the raw material.
The Future of Port Facilities for Oil Terminals…! MONOBOYA, the monobuoy is a structure with the greatest advance in evolution and technology in the last 30 years. It offers a large number of benefits such as: ease of maintenance, greater volume and solidity, a high standard in reliability. It can stay in the water for 25 years.
References
- MARPOL 73/78 (International Convention to Prevent Marine Pollution)
Sea by Ships). - ISGOTT 1996 (International Safety Guide for Terminals and Tankers
tankers). - SOLAS (International Convention for the Safety of Life on the Sea).
Mar, 1974). - Turrent Buoy, Technical Description.” https://www.bluewater.com/wp-content/uploads/2013/04/digitale-brochure-TurretBouy-Tech-description.pdf.