Table of Contents
- What is the Ishikawa Diagram and why is it important?
- Identifying problems and opportunities: The sources of origin
- The Ishikawa Diagram as a key tool in problem resolution
- The Ishikawa Diagram as a key tool in problem resolution
- Constructing the Ishikawa Diagram Step by Step
- Step 1: Identify and define the problem
- Step 2: Form an interdisciplinary team
- Step 3: Drawing the basic structure of the diagram
- Step 4: Select the main categories of analysis
- Step 5: Identify and classify possible causes
- Step 6: Analyze and prioritize identified causes
- Step 7: Develop and implement solutions
- Benefits of the Ishikawa Diagram in quality management
- Conclusions
- References
In any organization, problems and opportunities for improvement are inevitable. From production processes that fail to meet their goals to customers who are dissatisfied with a service, each situation poses a challenge that can impact the efficiency, competitiveness, and reputation of the company. However, addressing these problems in a reactive and superficial manner often leads to temporary solutions, leaving the root causes intact and perpetuating the same problems over time.
In this context, the Ishikawa Diagram represents a key tool to boost quality management and productivity within organizations. This tool allows work teams to clearly and systematically identify the true sources of a problem, providing a solid basis for developing effective and lasting solutions.
What is the Ishikawa Diagram and why is it important?
The Ishikawa Diagram, also known as a cause-effect or fishbone diagram, is a graphical tool used to identify, organize and analyze the root causes of a specific problem or phenomenon. It was developed by Dr. Kaoru Ishikawa, a pioneer in quality management, who designed this technique to facilitate the understanding of the factors that contribute to process performance and help organizations implement effective improvements.
Structure of the Ishikawa Diagram
The design of the diagram is reminiscent of the structure of a fish, where:
- The head represents the main problem or effect to be analyzed.
- The main spines symbolize the main categories of causes (often grouped into areas such as method, labor, machine, material, environment, measurement, management, among others).
- Secondary spines are used to detail sub-causes within each main category, helping to break down the problem into more specific levels
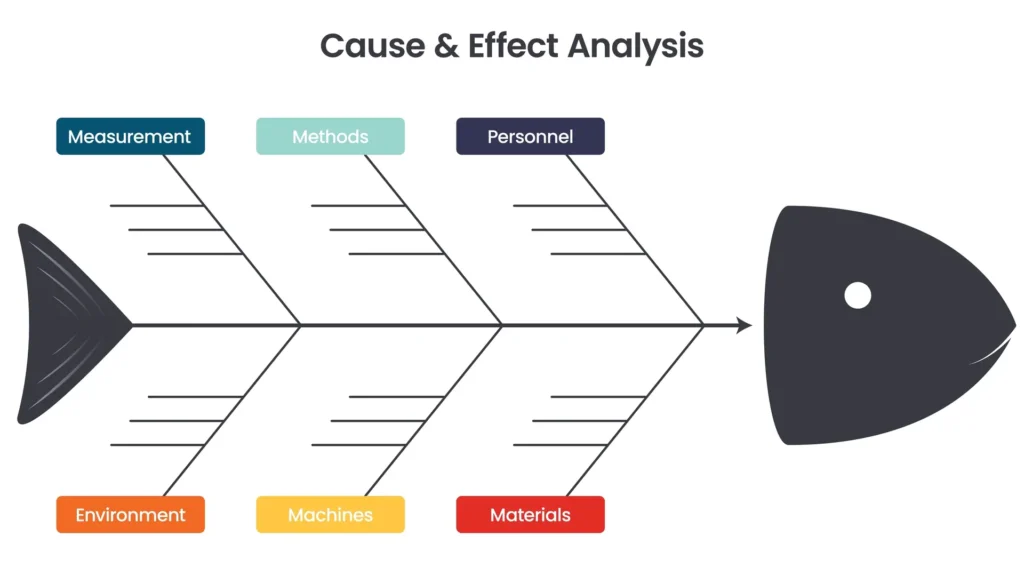
Why is the Ishikawa Diagram necessary?
- Root cause identification: Often, organizational problems are addressed with immediate solutions that treat the symptoms, but not the underlying causes. The Ishikawa Diagram allows for a deeper analysis to identify the real factors that generate the problem, promoting lasting solutions.
- It facilitates collaboration: This tool encourages the participation of multidisciplinary teams, as it gathers diverse perspectives to obtain a complete picture of the problem. This improves the quality of the analysis, and reinforces the team’s commitment to the proposed solutions.
- Clear structure and visualization: Its graphical format simplifies understanding of complex problems and allows stakeholders to easily visualize how different causes are interrelated. This is especially useful in analysis meetings, internal audits or management reviews.
- Broad applicability: The Ishikawa Diagram is not limited to one industry or problem resolution. It is a versatile tool that can be used in quality management, problem solving in different functional areas, indicator improvement or even customer feedback.
The Ishikawa Diagram in the context of continuous improvement
When organizations seek to improve, whether in response to internal audits, unfavorable performance indicators or customer complaints, deviations in production, the Ishikawa Diagram becomes a fundamental piece of the process. By structuring and analyzing the possible causes of a problem, it helps to establish priorities and guide efforts toward effective solutions that not only solve the current problem, but also prevent its recurrence. This tool transforms complex problems into opportunities for learning and improvement, strengthening an organization’s ability to achieve its quality and efficiency objectives.
Identifying problems and opportunities: The sources of origin
One of the first steps in applying the Ishikawa Diagram effectively is to clearly identify the problems or opportunities for improvement that require analysis. This involves understanding the root sources that feed the detection of these critical points. In this context, organizations have multiple channels to identify problems or areas for improvement that can be systematically addressed.
Common sources of problems and opportunities for improvement
- Internal audits: Internal audits of systems, processes or products are a key source for identifying and managing nonconformities, as well as for determining weaknesses in procedures and areas that do not comply with established standards, providing an objective view of critical points that need immediate attention or continuous improvement.
- Performance indicators: Key performance indicators (KPIs) allow monitoring the performance of organizational processes. Results below established targets or negative trends in indicators such as productivity, quality, or customer satisfaction are clear signals of the need for analysis and correction.
- Management review: During periodic senior management reviews, progress toward strategic objectives is analyzed. These meetings are opportunities to identify deviations or potential improvements that align processes with the organization’s strategic direction.
- Customer feedback: Customer complaints, suggestions, and opinions provide valuable information to detect problems related to product or service quality. This type of feedback allows identifying the causes behind dissatisfaction and improving the customer experience.
- Stakeholder observations: Employees, suppliers, partners and other stakeholders can also be important sources of information. Their observations and comments may reveal operational, logistical or communication problems that have not been formally identified.
- Production variances: Production deviations are a critical source for identifying problems that directly affect efficiency, quality, and operating costs. These deviations may include out-of-specification products, equipment failures, material waste or longer than expected cycle times.
Transforming problems into opportunities for improvement
It is significant to emphasize that not all problems should be perceived as threats. By identifying their origin and analyzing their root causes, organizations turn these challenges into opportunities to optimize processes, increase stakeholder satisfaction and strengthen their competitive capability.
Detailed root-cause analysis, combined with the use of the Ishikawa Diagram, allows problems to be addressed in a structured and proactive manner, achieving significant progress towards continuous improvement.
The Ishikawa Diagram as a key tool in problem resolution
The Ishikawa Diagram is one of the most powerful tools for identifying and analyzing the root causes of a problem. Its visual and organized structure allows teams to systematically explore the factors contributing to a specific situation, thus facilitating an effective and sustainable solution.
Why is the Ishikawa Diagram key to problem resolution?
- Clear visualization of potential causes: By graphically representing the possible causes contributing to the problem, the diagram helps teams take a holistic view and avoid superficial or assumption-based solutions.
- Encouraging collaborative analysis: Its use in group sessions promotes the active participation of team members, which increases the likelihood of identifying causes that might be overlooked in an individual analysis.
- Systematic approach: The categorized structure of the diagram (usually in areas such as method, machinery, materials, environment, labor, among others) guides the analysis so that it is complete and organized.
The Ishikawa Diagram as a key tool in problem resolution
The use of the Ishikawa Diagram is strategically inserted into each stage of the problem resolution process, which can be divided into the following steps:
- Define the problem: Before drawing up the diagram, it is important to establish a clear and specific description of the problem. For example, “Increase in the percentage of defects in production” or “Decrease in customer satisfaction in the last quarter”.
- Form a cross-functional team: Bringing together people with different perspectives and roles within the organization ensures a diversity of ideas during the development of the diagram.
- Construct the Ishikawa Diagram:
- Write the identified problem on the far right side of the diagram, as the “head of the fish.”
- Draw main lines (the “major spines”), representing the general categories where the causes could be found, such as: method, machinery, materials, environment, labor and measurement.
- Add sub-lines (the “minor thorns”) to detail specific causes within each category.
- Analyze the identified causes: Once the diagram is completed, the team evaluates each cause to determine which are the most likely or relevant; this involves collecting additional data or making direct observations.
- Prioritize root causes: Not all causes will have the same level of impact on the problem. Using additional tools, such as Pareto analysis or affinity diagrams, can help focus efforts on the most critical causes.
- Implement solutions: Once root causes have been identified, the next step is to develop and implement specific corrective actions, making sure to monitor their effectiveness in real time.
It is important to note that the Ishikawa Diagram is an analysis tool, and a key piece in the proactive management of quality and continuous improvement, by allowing organizations to address problems in a comprehensive and effective manner.
Constructing the Ishikawa Diagram Step by Step
The Ishikawa Diagram is a simple tool to use, but its effectiveness depends on a structured approach and careful execution. Below, we guide you step-by-step through its construction, ensuring that the analysis is thorough and focused on solving problems or seizing opportunities for improvement. Video courtesy of: Harvard Online.
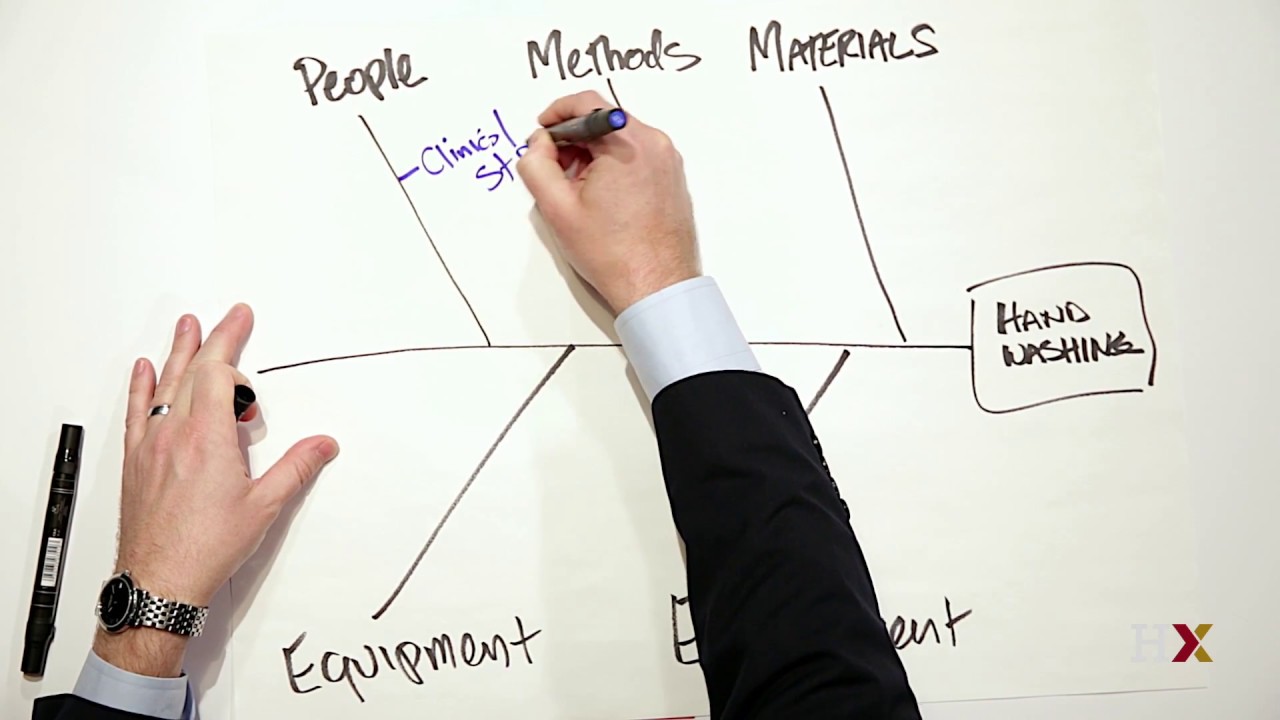
How to create Cause-and-Effect Diagrams?
Step 1: Identify and define the problem
Before starting the construction of the diagram, it is essential to clearly define the problem or opportunity for improvement to be analyzed. To do so, it is essential to make a formal analysis of the available information, including process, product and service statistics.
- Example: “Increase in the percentage of defects in final products”. The problem must be specific, measurable and relevant to the organizational context.
Step 2: Form an interdisciplinary team
Assemble a working group with representatives from different areas involved in the process or activity related to the problem.
- A diverse team ensures multiple perspectives and increases the likelihood of identifying all potential causes.
Step 3: Drawing the basic structure of the diagram
- Draw a horizontal line in the center of a sheet (the “backbone” of the fish).
- On the far right, write the defined problem inside a rectangle or circle (the “head of the fish”).
- Draw diagonal lines from the backbone to the sides (the “main spines”), which will represent the categories of causes.
Step 4: Select the main categories of analysis
Key categories are broad areas where the causes of the problem may originate. Although the categories may vary by industry or process, some common ones are:
- Method: Procedures, policies or standards that guide the work.
- Machinery: Tools, equipment or technology used.
- Materials: Inputs, raw materials or components.
- Manpower: Training, skills and performance of personnel.
- Environment: External conditions, climate, physical space or operational context.
- Measurement: Control systems, data accuracy and instrument calibration.
Step 5: Identify and classify possible causes
- Brainstorm with the team to identify possible causes within each major category.
- Add secondary lines (“minor thorns”) in each category to detail specific causes.
- Example: In the category “Materials,” a minor thorn could be “variation in supplier quality.”
- Constantly ask “why?” to drill down to possible root causes.
Step 6: Analyze and prioritize identified causes
- Evaluate the identified causes to determine which have the most significant impact on the problem.
- Use complementary tools, such as Pareto analysis, to focus efforts on the most critical causes.
Step 7: Develop and implement solutions
Once root causes have been identified, develop an action plan to address each one.
- Design specific, measurable solutions to eliminate or mitigate the causes.
- Be sure to assign clear responsibilities and timelines.
The Ishikawa Diagram, properly applied, becomes a transformative tool that drives continuous improvement and effective organizational problem solving.
Benefits of the Ishikawa Diagram in quality management
As already stated, the Ishikawa Diagram is a powerful tool in quality management, allowing you to effectively identify, analyze and solve problems. Its use has several key benefits that have a considerable impact on continuous process improvement and quality optimization within an organization. Below, we explore the main benefits of the Ishikawa Diagram in quality management:
- Clear identification of root causes: One of the major benefits of the Ishikawa Diagram is its ability to help organizations identify the root causes of problems rather than treating only the symptoms.
- It facilitates fact-based decision making: The Ishikawa Diagram provides a clear and structured view of the potential causes of the problem, which facilitates more informed, fact-based decision making, rather than assumptions or intuition.
- Improves collaboration and teamwork: The Ishikawa Diagram construction process requires the collaboration of several people within the organization, which encourages teamwork and the integration of different points of view.
- It facilitates the visualization of the problem and its interrelationships: The Ishikawa Diagram helps to visualize how various causes interrelate to contribute to a specific problem, which allows a better understanding of the complexity of the processes and facilitates a comprehensive solution.
- Promotes continuous improvement: The Ishikawa Diagram is a tool that is not only used to solve specific problems, but also promotes a proactive approach to continuous improvement within the organization, being a key tool in process management.
- Improves communication and clarity: The visual format of the Ishikawa Diagram facilitates the understanding of problems and solutions among the different levels of the organization.
- Supports compliance with regulations and quality standards: In quality management, compliance with international regulations and standards (such as ISO 9001) is crucial to maintain competitiveness. The Ishikawa Diagram is a useful tool for meeting these requirements by facilitating a thorough analysis of processes, which in turn helps demonstrate the organization’s commitment to continuous improvement and quality.
- Encourages a preventive rather than reactive approach: The Ishikawa Diagram is not only used to solve current problems, but also to prevent future problems, allowing the identification of weaknesses in processes before they become serious problems.
Conclusions
The Ishikawa Diagram is not only an effective tool for solving quality problems, but it also plays a critical role in transforming those same problems into valuable opportunities for improvement and growth within the organization.
Every time a team uses the Ishikawa Diagram to identify the underlying causes of a problem, they are not only solving a one-time issue, they are learning about the organization’s processes, systems and resources. This continuous learning not only prevents problems from recurring, but drives the company’s ability to adapt, innovate and improve. Problems that were once considered barriers or brakes to progress become opportunities to reinforce the organizational culture of continuous improvement.
The Ishikawa Diagram not only solves isolated problems; it provides a solid foundation for a proactive and continuous approach to quality management. Every root cause analysis, every improvement process implemented, contributes to the virtuous cycle of continuous improvement, which is fundamental to the long-term sustainability of the organization. Problems, far from being insurmountable obstacles, become stepping stones to progress, an opportunity to optimize processes, improve products and strengthen organizational culture.
References
- Ishikawa, K. (1986). What is Total Quality Control? The Japanese Way. Prentice Hall.
- Juran, J. M. (1998). Juran’s Quality Handbook (5th ed.). McGraw-Hill Education.
- Gitlow, H. S., Oppenheim, A. J., Oppenheim, R. & Levine, D. (2005). Quality Management: Theory and Applications. Prentice Hall.
- Lugo Marín, J. (2023). La Gestión por Procesos. Herramienta clave para la competitividad. Inspenet
- Montgomery, D. C. (2009). Introduction to Statistical Quality Control (6th ed.). John Wiley & Sons.
- Oakland, J. S. (2014). Total Quality Management and Operational Excellence: Text with Cases (4th ed.). Routledge.