Table of Contents
- What is industrial NDT and why is it key to inspection?
- Introduction to Non-Destructive Testing
- Key Non-Destructive Testing (NDT) Methods
- Industrial NDT applications by sector
- Benefits of non-destructive testing in industry
- Certifications and standards in Non-Destructive Testing
- Emerging trends in industrial NDT
- Success stories in the application of NDT methods
- Career prospects and professional demand in NDT
- Conclusions
- References
- Frequently asked questions about industrial NDT (FAQ)
- Which NDT certification is best for the industry?
- What is the average salary for an NDT technician?
- Where is industrial NDT most commonly used?
- Does NDT replace destructive testing?
- What is the difference between a destructive test and a non-destructive test?
- What is the most suitable NDT method for detecting deep internal cracks?
- Is certification required to perform NDT?
- How often should NDT be performed on industrial equipment?
- Can I use visual inspection alone as an NDT method?
What is industrial NDT and why is it key to inspection?
Industrial NDT (Non-Destructive Testing) refers to a set of techniques that enable the non-destructive industrial evaluation of materials and components without affecting their operability. It is essential for detecting surface or internal defects, measuring thicknesses, and ensuring structural integrity without causing any damage.
Its importance in industrial inspection lies in its ability to prevent critical failures, optimize maintenance programs, and ensure compliance with international regulations. Non-destructive testing allows for greater reliability, minimizing costs and risks, especially in strategic sectors such as energy, oil, aerospace, and advanced manufacturing.
In a world of constant progress, with revolutionary technological developments being integrated into industrial inspection, Non-Destructive Testing (NDT) has emerged as a component of great importance in ensuring safety, reliability, and quality. As industries evolve, the demand for more efficient and accurate inspection methods grows, making NDT an essential aspect of modern engineering and manufacturing. This article provides an introduction to NDT, exploring its importance, the various methods used, and the future of industrial inspection.
Introduction to Non-Destructive Testing
NDT is essential for ensuring the operational safety of industrial assets without interrupting processes or compromising structures. These methods are used to detect cracks, corrosion, inclusions, or deformations in critical materials. Their use extends throughout the entire production and maintenance chain.
Industrial non-destructive testing is a practice established in international technical standards such as ISO 9712, ASNT, and API, making it a standardized, reliable, and scalable technical resource for all types of plants, facilities, and complex infrastructures.
Key Non-Destructive Testing (NDT) Methods
Industrial non-destructive testing encompasses a variety of methods adapted to different materials, types of defects, and operating environments. The following describes the most commonly used traditional and modern methods in industrial inspection, highlighting their applications, advantages, and key sectors.
Conventional or traditional techniques
Visual Inspection (VT)
- Direct examination of surfaces with or without optical aids.
- Advantages: Low cost, fast, useful as a preliminary assessment.
- Applications: Metal structures, welds, general maintenance.
Ultrasound (UT)
- Emits high-frequency acoustic waves to detect internal discontinuities.
- Advanced technologies: PAUT, TOFD, TFM.
- Sectors: energy, oil, aeronautics, manufacturing.
Industrial Radiography (RT)
- Use of X-rays or gamma rays to visualize internal defects.
- Advances: Digital radiography (DR), computed tomography (CT).
- Applications: Welds, castings, critical inspection.
Magnetic Particles (MT)
- Application of magnetic fields and ferrous particles to reveal surface discontinuities.
- Limited to: ferromagnetic materials.
- Uses: pipes, structural components.
Penetrant Testing (PT)
- It consists on the application of a developing liquid on non-porous materials to detect open cracks.
- Advantages: Economical, visually clear.
- Sectors: Welding, precision machining.
Induced Currents (ECT)
- Detects variations in electrical conductivity using electromagnetic fields.
- Advances: Eddy Current Array (ECA), PECA.
- Applications: heat exchangers, aeronautics.
Infrared Thermography (IRT)
- Detects thermal patterns that indicate internal defects or loss of efficiency.
- Ideal for: electrical and thermal systems and remote detection.
Guided Waves (GWT)
- Uses ultrasonic waves that propagate along pipes or extensive structures.
- Key advantage: inspection without dismantling.
- Applications: industrial plants, underground networks.
Modern techniques
With technological advances, more sophisticated methods have emerged that enhance non-destructive testing and enable more accurate, safer, and automated inspections:
Acoustic Emission (AE)
- Detects elastic waves generated by microcracks or internal deformations while the material is under load.
- Uses: pressure vessels, tanks, metal structures, operational monitoring.
- Advantage: real-time monitoring, early detection of active faults without stopping the system.
MFL (Magnetic Flux Leakage)
- Detects magnetic flux leakage in ferromagnetic materials.
- Applications: Tank bottoms, pipelines, buried pipes.
- Advantage: Fast coverage of large areas.
IRIS (Internal Rotary Inspection System)
- Uses rotating ultrasound to measure the internal thickness of pipes.
- Ideal for: inspecting heat exchanger pipes.
- Accuracy: High axial resolution for corrosion detection.
SAT (Structural Acoustic Testing)
- Applies controlled mechanical vibrations to assess structural integrity.
- Applications: aerospace components, composites, and wind structures.
- Advantage: non-contact assessment.
EMAT (Electromagnetic Acoustic Transducer)
- Generates ultrasonic waves without physical coupling, ideal for aggressive or hot environments.
- Uses: rolled steel, high-temperature structures, corrosion detection.
- Advantage: speed and safety in extreme environments.
Digital Radiography (DR)
- Digital version of the RT that allows real-time images with better resolution and automated processing.
- Advantage: reduced time, digital storage, and traceability.
Shearography
- Optical technique that measures surface deformation under load.
- Application: inspection of composites, laminates, and aerospace structures.
- Notable for: sensitivity to internal delamination without contact.
Computed Tomography (CT)
- High-resolution three-dimensional volumetric scanning.
- Uses: complex parts, aerospace, automotive, critical castings.
- Advantage: detailed layer-by-layer analysis and 3D reconstruction.
These modern NDT technologies represent the future of non-destructive testing by combining precision, automation, and advanced analysis, making them key to demanding and regulatory industrial processes.
Industrial NDT applications by sector
NDT methods are applied in sectors where component reliability is critical. Their versatility makes them key allies in keeping complex systems operational without compromising safety.
- Inspection of welds, pipes, tanks.
- Prevention of leaks and critical failures.
Aerospace
- Inspection of composite materials and structural components.
- Extensive use of UT and EMAT.
Manufacturing
- Quality control in production processes.
- Thickness and finish control.
Nuclear and thermal energy
- Fatigue, corrosion, and crack monitoring.
- Continuous assessment of critical assets.
Construction and civil infrastructure
- Inspection of bridges, dams, and metal structures.
- Application of ultrasound, thermography, and magnetic particles.
Benefits of non-destructive testing in industry
The implementation of non-destructive testing provides strategic benefits in any industrial environment:
- Prevention of accidents and operational failures.
- Reduction of costs associated with unplanned downtime.
- Increased service life of critical equipment.
- Compliance with international regulations and standards.
- Improved decision-making based on real data.
- Direct contribution to operational sustainability.
Certifications and standards in Non-Destructive Testing
Professionals who apply non-destructive testing techniques must have recognized certifications. The most commonly used ones are listed in the table below:
Comparative table of standards applicable to industrial NDT
Standard | Scope of application | Relationship with industrial NDT |
ASNT SNT-TC-1A (EE. UU.) | Internal certification of NDT personnel (USA) | Establishes guidelines for training and qualifying personnel in NDT techniques. |
ISO 9712 (International) | International third-party certification | Defines competency levels (I, II, III) for NDT certified personnel |
API 510 / 570 / 653 | Inspection of pressure equipment, pipes, and tanks | Requires the application of NDT methods to ensure the integrity of industrial assets. |
ASME Section V | Code for technical requirements for NDT methods | Specifies procedures, materials, and technical acceptance for applying NDT methods in industry. |
These standards ensure technical competence, legal compliance, and reliability in industrial inspection results.
Emerging trends in industrial NDT
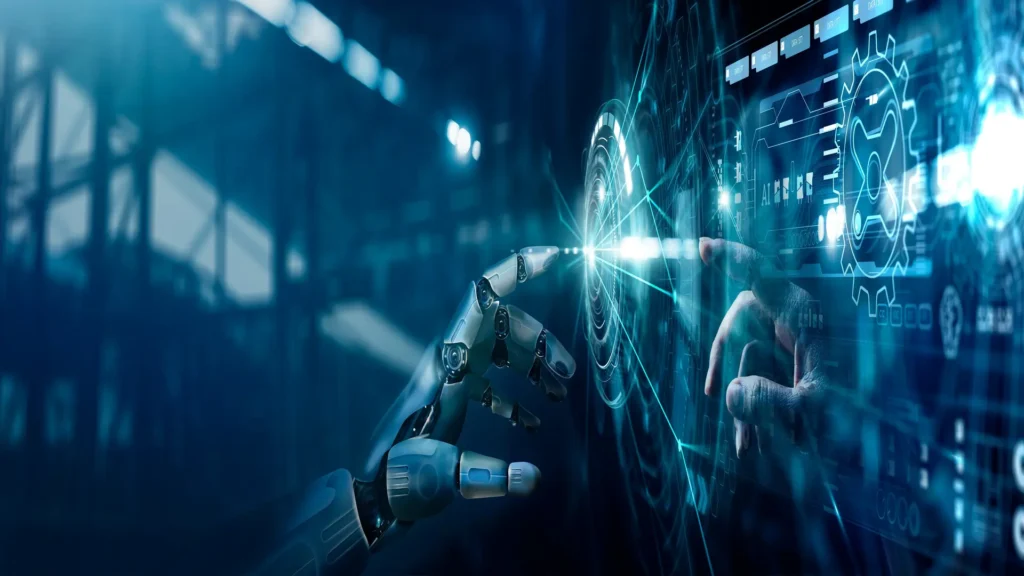
Digital transformation and Industry 4.0 are revolutionizing the field of industrial non-destructive testing:
- Digitization and automation: robots, 3D scanning, digital twins.
- Artificial intelligence: predictive analytics, automated detection.
- Remote and cloud-based inspection: traceability and global data management.
- Non-contact techniques: EMAT, IRT, ideal for hazardous environments.
- Integration with IoT and cybersecurity.
Success stories in the application of NDT methods
NDT methods are successfully applied in critical sectors, where early detection of defects makes a key difference in safety, efficiency, and savings.
Ultrasonic (UT) inspection of gas pipelines
- Sector: Energy and gas transportation
- Technique used: In-line ultrasound with automated scanning
- Description: A 290 km section was inspected without stopping operations, covering 100% of the internal surface.
- Results: Early detection of internal cracks and corrosion; basis for predictive maintenance.
- Source: NDT Global – Case Study
Success story: Digital radiography in subsea pipelines
- Sector: Offshore oil
- Technique used: Digital Radiography (DR)
- Description: Evaluation of welds in subsea pipelines without interrupting production.
- Results: Improved maintenance planning and increased structural reliability.
- Source: Baker Hughes / SVK Electronics
Career prospects and professional demand in NDT
With the growth of industrial automation, more stringent regulations, and greater awareness of operational safety, industrial NDT is experiencing global expansion. Companies demand professionals trained in techniques such as UT, RT, ECT, and MFL, both for field inspections and for digital analysis in remote or automated environments.
Industrial non-destructive testing has established itself as a career with a future: it offers job stability, competitive salaries, and opportunities for international specialization. ISO, ASNT, and API certifications have become key differentiators in the technical job market.
Conclusions
Industrial NDT is not only a set of advanced techniques, but also a strategy for quality, safety, and sustainability in increasingly demanding industrial environments. Its implementation allows for extending the useful life of assets, preventing catastrophic failures, and complying with global standards.
From basic visual inspection to technologies such as MFL, IRIS, or computed tomography, non-destructive testing is transforming how operational integrity is managed in critical sectors. Adapting to these tools is not optional: it is a competitive advantage.
References
- GOOGLE CLOUD. What is Cloud Storage?; Accessed on August 26, 2024. https://cloud.google.com/learn/what-is-cloud-storage?hl=en
- VIDAL INTERNATIONAL. The Future of NDT: How Advanced Technologies are Shaping the Industry. Accessed on August 26, 2024. https://vidalinternational.in/the-future-of-ndt/#:~:text=Incorporating%20robotics%20in,may%20be%20limited.
Frequently asked questions about industrial NDT (FAQ)
Which NDT certification is best for the industry?
It depends on the country and sector. The most widely recognized globally are ISO 9712 (international) and ASNT SNT-TC-1A (US), in addition to API-specific standards for oil and gas.
What is the average salary for an NDT technician?
In the US, the average ranges from USD 60,000 to 90,000 per year, and can exceed USD 100,000 with experience and level 2 or 3 certifications. In Latin America, it varies by country and sector.
Where is industrial NDT most commonly used?
NDTs are used in high-risk sectors and critical assets: energy, oil, aerospace, manufacturing, construction, mining, and shipbuilding.
Does NDT replace destructive testing?
No. They complement each other. Non-destructive testing is used to detect defects without damaging components, while destructive testing validates mechanical behavior under stress. They are commonly referred to as material testing and analysis.
What is the difference between a destructive test and a non-destructive test?
Destructive testing involves damaging or destroying a sample to evaluate its properties, while NDT allows inspection without affecting the integrity of the component, which is key for assets in operation.
What is the most suitable NDT method for detecting deep internal cracks?
Ultrasound (UT) is the most effective technique for quantifying and delimiting the depth of internal cracks and identifying other deep internal discontinuities, depending on the type of material and geometry of the part.
Is certification required to perform NDT?
Yes. Most methods require personnel to be certified under standards such as ISO 9712, ASNT SNT-TC-1A, or API, ensuring technical competence and regulatory compliance.
How often should NDT be performed on industrial equipment?
It depends on the type of asset, operating conditions, inspection plan, and applicable regulations. For example, pressure vessels are typically inspected every 3 to 5 years, according to codes such as API 510.
Can I use visual inspection alone as an NDT method?
Visual inspection (VT) is essential as a first level of control, but in most cases it must be supplemented with advanced methods (UT, RT, MT, etc.) for a complete evaluation.