Introduction
Steel storage tanks are used to store fluids such as crude oil, intermediates, refined products, gas, chemicals, waste, aqueous mixtures, and water. Internal corrosion in storage tanks in hydrocarbon services shortens the life cycle of the tank, generating leaks and the release of hazardous materials into the environment.
Hydrocarbons themselves are not corrosive; fuels like gasoline and diesel are typically non-corrosive to steel. However, during transportation, they absorb water and aqueous solutions (saline, acidic) and settle at the tank bottom, resulting in detrimental internal steel issues. Corrosion is the primary cause of deterioration in steel storage tanks and accessories; therefore, corrosion control and prevention are significant for plant safety and efficient economics.
In this context, the aim of this article is to provide a brief overview of severe internal corrosion issues in tanks and discuss recent technologies and effective methods for controlling corrosion in these storage systems commonly found in oil plants.
Causes of internal tank corrosion
The degree of corrosion inside storage tanks depends on the nature of the stored product and the tank material. Essentially, it involves a combination of sulfurous gases, moisture (aqueous salt solutions), and oxygen present inside the tank. Tanks for crude oil and derivative products are typically constructed from carbon steel. In some particularly corrosive services, it may be necessary to construct tanks from corrosion-resistant materials.
Internal corrosion in tanks, specifically in the areas covered by the stored liquid, is usually caused by acid salts, hydrogen sulfide or other sulfur compounds, as well as contaminated water that accumulates with solids at the bottom of the tank, known as bottom sediment and water (BS&W) (see Figure 1-a). In the vapor space above the liquid, corrosive damage is commonly caused by the presence of hydrogen sulfide vapors, water vapor, and oxygen, as shown in Figure 1-b1.
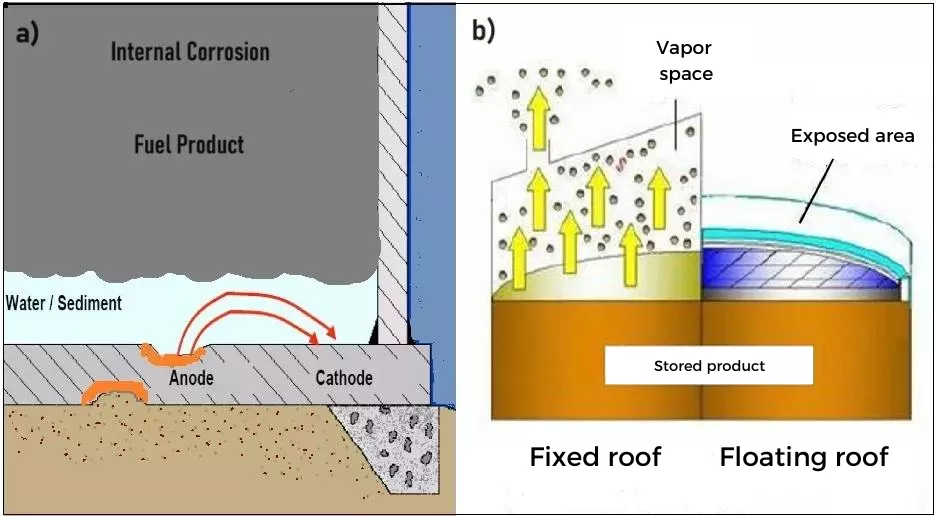
Under this context, it can be stated that the phenomenon of internal corrosion in crude storage tanks specifically occurs in three zones: the tank roof, wall, and bottom, which is the main issue of internal corrosion due to the presence of water accumulation. In the case of the roof, corrosion occurs in the space between it and the hydrocarbon phase, originating from a mechanism where water condenses into a thin film dissolved with aggressive agents. Wall corrosion occurs due to contact with the aqueous phase contained in the crude in the form of droplets.
Types of corrosion in storage tanks
There are different types of corrosion in storage tanks, such as, for example:
- Vapor phase corrosion: Occurs in the upper areas near the roof where metals are exposed to high temperatures and gases from stored products, leading to uniform, pitting, and localized corrosion depending on temperature and material characteristics.
- Liquid-gas interface corrosion: Occurs inside the tank where corrosion rates can increase due to oxygen or moisture concentration gradients on the tank’s inner wall, caused by the storage of corrosive gases. Types of corrosion include general (uniform) and pitting corrosion.
- Aqueous-phase corrosion: Arises from contaminants like sludge and deposits, causing general (uniform) and pitting corrosion on the tank bottom. Additionally, under anaerobic conditions, Microbiologically Influenced Corrosion (MIC) can occur. These problems are exacerbated by metal stresses due to fluctuations in stored liquid levels.
Figure 2, illustrates the most common types of corrosion in storage tanks2: a) stress corrosion under the floating roof, b) pitting corrosion in a coating defect, c) pitting corrosion in poorly coated irregular welds, d) abrasion corrosion in the heat-affected zone after abrasive cleaning.
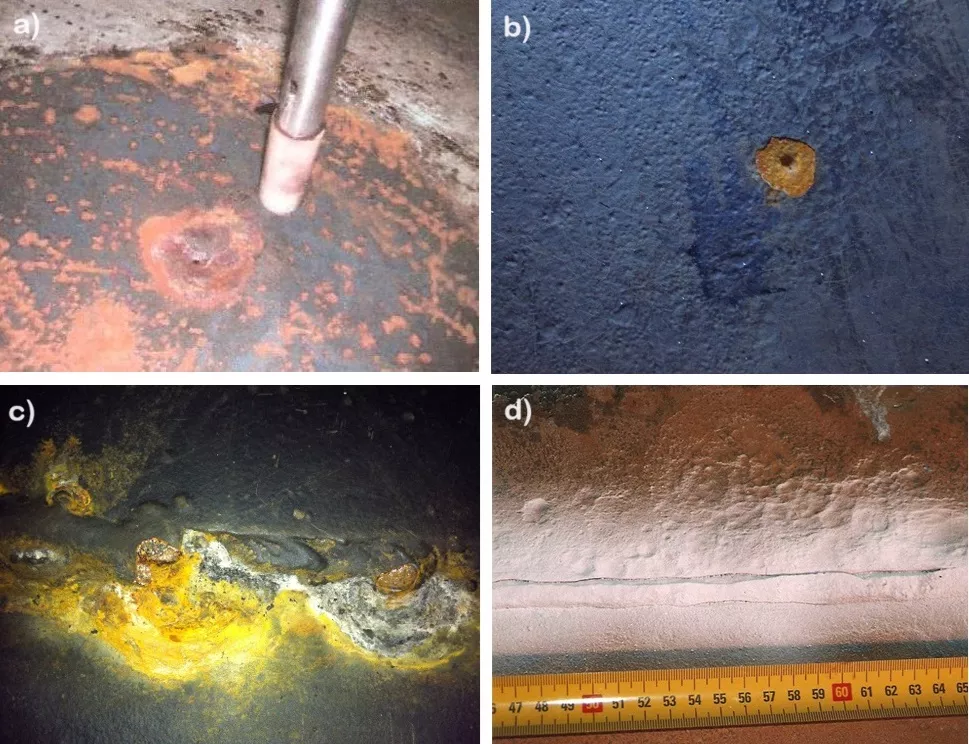
Protection against internal corrosion in storage tanks
Currently, advanced technologies have been developed to provide the required protection based on the type of substance to be stored, environmental conditions, and expected service life, ensuring high productivity during application3. The primary methods of protecting against internal tank corrosion are coatings, cathodic protection, and in some cases, corrosion inhibitors. However, only innovations in coatings will be addressed, as it is the most widely used method for controlling internal corrosion in storage tanks.
How to protect tanks? Innovations in oil and gas tank coatings
To control corrosion caused by the severe chemical processes described earlier inside the tank, anticorrosive coating technology is most recommended. Several factors must be considered when specifying the most suitable coating system, such as performance, temperature, chemical tolerance, and corrosion resistance. It is also necessary to consider the different corrosive chemicals and fuels stored in the tank; all these factors dictate the type of tank coating needed to protect storage tanks.
In terms of material selection, it is advisable to choose coatings with high resistance to acidic and alkaline corrosion and strong adhesion. Below are some innovations in internal coatings for storage tanks designed to meet the demanding requirements of the oil, petrochemical, and chemical industries:
1. Nanomaterial-based coatings
Graphene is the most revolutionary nanotechnological additive for the coatings and paints industry, enabling the development of coatings with extraordinary anticorrosive protection, antimicrobial properties, and improved substrate adhesion. In this regard, graphene oxide (GO) has proven to be a new additive that helps inhibit or reduce the flammability of coatings for the production of effective flame-retardant coatings.
Its efficiency is associated with graphene oxide’s strong barrier effect, high thermal stability, and great surface absorption capacity, which are favorable for effectively reducing heat and mass transfer. Graphene creates highly tortuous pathways, preventing water molecules, oxygen, and/or chemical agents from diffusing through the surface of metallic materials, thereby protecting the metal against oxidation and corrosion4.
2. Epoxy-polyurethane systems
This system consists of an epoxy primer and polyurethane (finish), coatings designed to protect metal surfaces exposed to highly corrosive and chemical environments. Both coatings offer high adhesion, extraordinary chemical resistance, high wear resistance, and impermeability to enhance the life of any metal surface. They are used in severe or critical environments where infrastructure or equipment is exposed to an industrial atmosphere with high contamination (highly corrosive vapors). These resin-based coatings are used to protect steel in internal tank linings and on surfaces requiring excellent chemical resistance.
3. Epoxy coatings and carbon nano polymers
Epoxy coatings and carbon nano polymers are widely used in the corrosion treatment of storage tanks due to their excellent high-temperature resistance. The polymer system (resin) was optimized to provide chemical resistance without compromising flexibility, a key requirement for long coating life, durability, and curing time. Among these, mention is made of the new Novolac Type coatings called “Next Generation”5 coatings. These are epoxy novolac resin-based coatings used for steel protection in internal tank linings, containers, and surfaces requiring excellent chemical resistance.
Conclusions
Controlling internal corrosion in storage tanks requires the implementation of specific technologies for each situation. One aspect to consider is improving the quality of stored products and using highly corrosion-resistant materials in tank construction based on international standards and regulations.
In today’s oil and gas sector market, it is crucial for applicators and asset owners to quickly adapt to changing demands, minimize downtime, and optimize resource usage to ensure profitability. They must also adhere to the rigorous standards of the American Petroleum Institute (API)). Choosing the most suitable technology for internal corrosion control in storage tanks results in significant long-term savings for both parties. Therefore, understanding technology, modern or “next-generation” developments is crucial to achieving these goals effectively and efficiently.
References
- API Recommended Practice 575, “Inspection of Atmospheric and Low-Pressure Storage Tanks,” American Petroleum Institute, first edition, (1995).
- Martinez S; “Estimation of Internal Corrosion Rate and Internal Inspection Interval of Hydrocarbon Storage Tanks on the Surface”; goriva i maziva, 52, 2 : 134-143, 2013.
- Sachin Sharma, Ashok Kumar, Shahid Bashir, K. Ramesh, S. Ramesh, Progress in Organic Coatings, 154, (2021).
- Chang, C.-H. et al. Novel Anticorrosion Coatings Prepared from Polyaniline/Graphene Composites. Carbon N. Y. 50, 5044–5051 (2012).
- Michael Harrison, Sherwin-Williams; “Innovation in Oil and Gas Tank Coatings in an Ever-Evolving Industry”; https://bit.ly/3HPVFuL