Introduction
Bearings are precision components and the dynamic supports of rotating machinery and can sometimes present premature failures that affect operability and productivity. Today, intelligent bearings solutions make it possible to continuously evaluate the operating conditions of machines, plants, or products and transmit the data to a control unit, immediately detecting many variations in the production process. They also detect changes in bearing wear and lubrication.
Manufacturers of bearings for rotating equipment have specific requirements for the design of these components, including higher speeds, lower torque, noise and vibration reduction, minimum maintenance needs, durability in harsh environments, integration in complex units, among other aspects. Innovations in intelligent bearings have significantly boosted the efficiency of rotating equipment in various industries.
Material innovations for more productive bearings
Ceramic materials such as silicon nitride and zirconium offer lower coefficients of friction, resistance to corrosion and high temperatures, and lower wear compared to conventional steel bearings. These materials minimize frictional energy losses, thus improving bearing performance and increased efficiency of rotating equipment.
Ceramic hybrid bearings using Si3N4 rolling elements, which offer up to 80% less friction and 3 to 5 times longer service life than traditional steel bearings.
Advanced polymer cages (e.g., PEEK) for improved lubrication retention and reduced cage wear.
Nano-composite coatings (e.g., WC/a-C:H) for increased wear resistance and lower coefficients of friction (μ < 0.1).
What is a bearing?
A bearing is a fundamental mechanical component that typically consists of two concentric cylindrical races, known as inner and outer rings. Rolling elements such as spheres or rollers are arranged between these races, allowing relative motion between the outer ring (outer race) and the inner ring (inner race), as shown in Figure 1. This design allows the outer race to rotate relative to the inner race while supporting axially and radially applied loads.
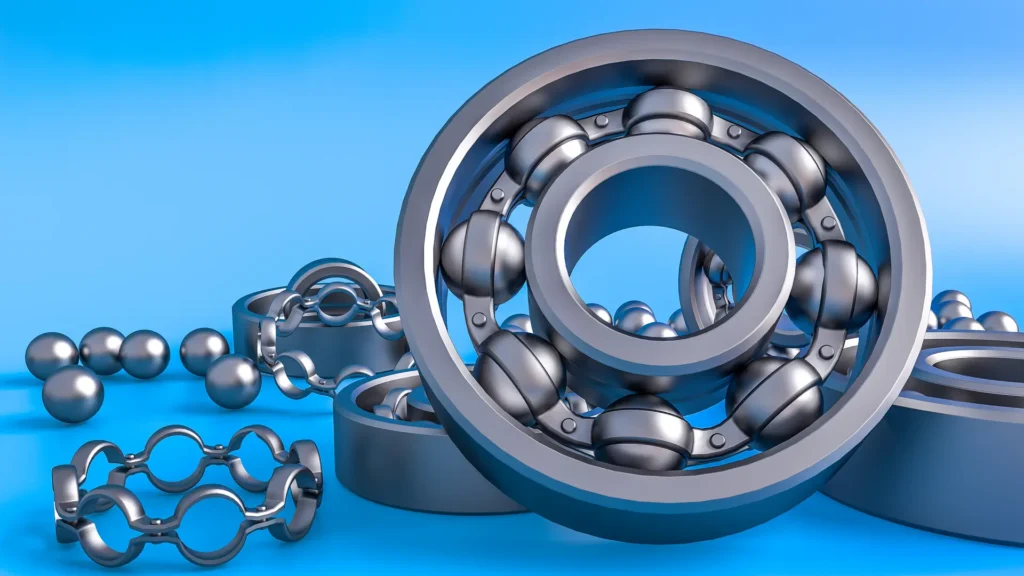
The bearing is commonly mounted on a rotating equipment shaft, allowing the shaft to rotate freely while the bearing rests in its outer race on a static or fixed surface. This bearing-shaft assembly provides stable support and allows the rotational motion essential for machine operation.
Main bearing components
Figure 2 shows the parts that make up a bearing.
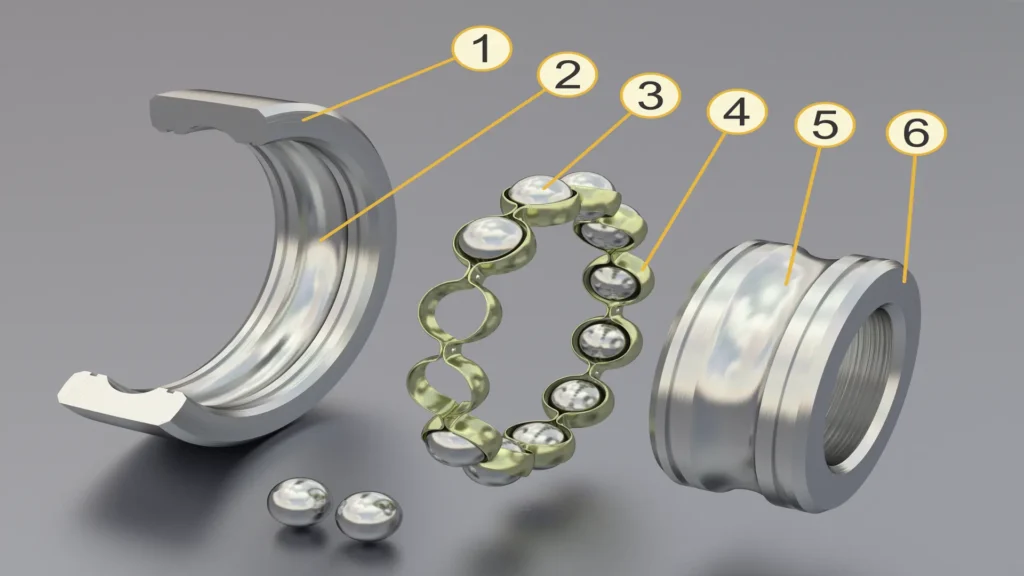
How do roller and ball bearings work?
![]() | Working principle of a ball bearing. The red dots show the direction of rotation. In most applications, one of the parts is fixed, and the other is attached to the rotating component, such as a shaft or bushing. As one of the bearing races rotates, the balls also rotate, resulting in much less friction compared to the sliding of two flat surfaces. This is because the balls are rolling, thus minimizing direct contact between the surfaces. |
For more information, the following video shows how the bearings work: Source: JAES Company English.
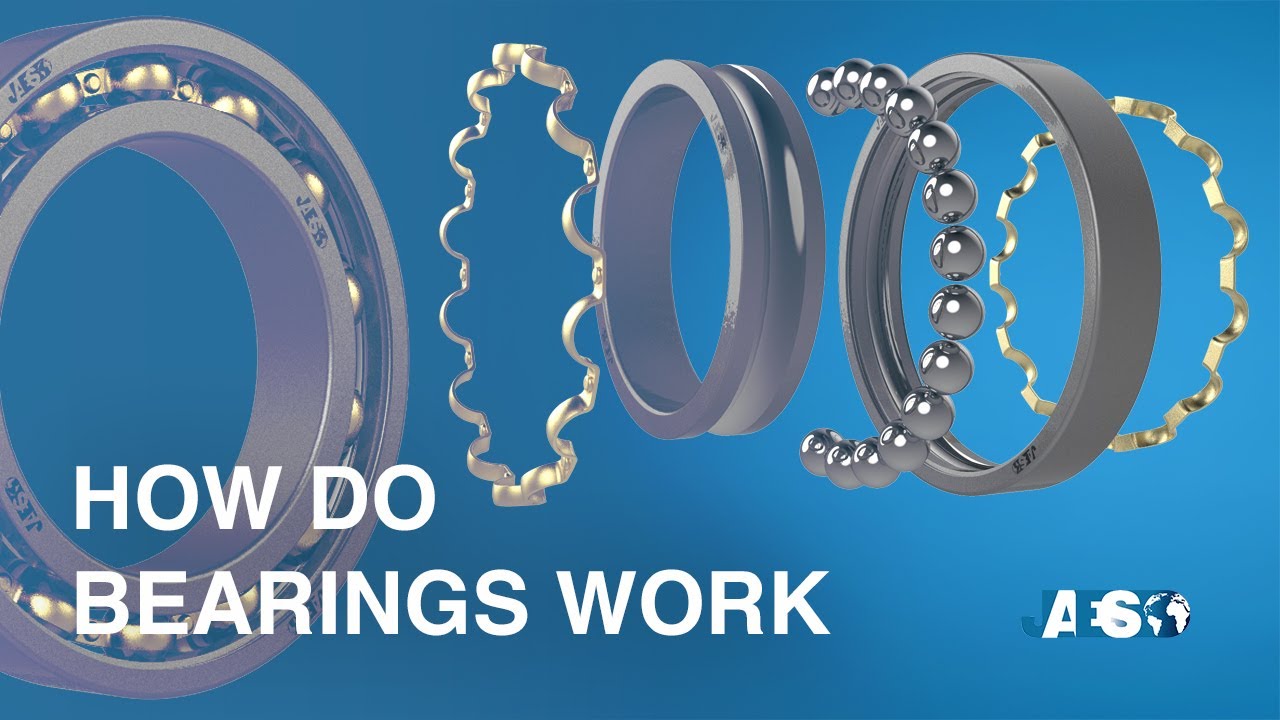
How do ball and roller bearings work?
What is the function of a bearing?
Bearings play a key role in rotating machinery by supporting shafts with low rolling friction. They vary significantly in size, from 10 mm to several meters in diameter, and can handle loads ranging from a few tens of grams to thousands of tons. They are often equipped with cages that reduce friction and wear between the rollers.
The diversity of applications has driven the development of different bearing configurations. Ball bearings are generally versatile, while cylindrical roller bearings are preferred for high radial loads. For loads combining radial and axial loads, tapered roller bearings are used, and for considerable axial loads, thrust bearings are the right choice.
![]() | The red dots show the direction of rotation. In most applications, one of the parts is fixed and the other is attached to the rotating component, such as a shaft or bushing. As one of the bearing races rotates, the balls also rotate, resulting in much less friction compared to the sliding of two flat surfaces. This is because the balls are rolling, thus minimizing direct contact between the surfaces. |
The raceways, annular in most cases, vary according to the application. For example, ball, cylindrical and tapered bearings use standard annular raceways, while bearings that need to allow for shaft deflections usually have spherical or toroidal raceways. A special type is toothed ring races, which function as epicyclic mechanisms.
Bearings are essential to ensure the stability and operation of rotating shafts in different industrial applications, providing specific capabilities to withstand axial, radial or combined loads, depending on the design and the particular needs of each machine or system.
Characteristics and Bearings types
There are different types bearings, each designed to fulfill specific functions in different applications. Some of the most common are described below:
Tapered roller bearings
These bearings have a conical shape and are composed of tapered rollers and an outer tapered ring, which allows the shaft to move. They are more efficient than ball bearings in supporting heavy and radial loads, and are mainly used in applications requiring high radial and axial loads, such as in vehicle wheel axles.
Cylindrical roller bearings
These bearings have a cylindrical shape and consist of cylindrical rollers and an outer ring. They are used in applications requiring high radial loads, such as heavy machinery axles and construction equipment.
Spherical roller bearings
With a spherical shape, these bearings are composed of an inner ring and an outer ring, both with grooves where spherical rollers are placed. They are ideal for applications requiring high radial and axial loads, such as vehicle axles and construction machinery.
Needle roller bearings
These bearings, characterized by their compact design and high load carrying capacity compared to their size, are ideal for applications requiring high speeds and radial and axial loads. They consist of a series of cylindrical needle rollers arranged in a circular space between an inner and outer ring. They are used in a wide variety of applications, from bicycle axles to electric motors and industrial machinery, thanks to their corrosion resistance and longevity.
Angular contact bearings
These components allow rotational motion on a shaft and have two types of races: internal and external. They offer higher load carrying capacity and accuracy compared to other bearings types, making them suitable for high speed and high load applications. They can support combined radial and axial loads and are available in single and double row versions. Single-row bearings are suitable for light loads, while double-row bearings are suitable for heavier loads and high-precision applications.
Radial and axial bearings
Radial bearings have the highest load carrying capacity and the lowest cross-sectional height. They are preferred for applications with small outside diameters and are used in transmissions and rocker arms. Axial and radial bearings have similar performance characteristics, but radial bearings have higher load carrying capacity and can support very high rotational speeds, as well as being more flexible and quieter due to their large contact surface.
The different Bearings types, with their specific designs and characteristics, offer reliable and durable solutions for a wide variety of applications, enabling Rodamientos de alta eficiencia in all the mechanical components that comprise them.
Benefits of bearing innovation
Bearings offer a number of significant advantages in various industrial and mechanical applications by improving operability and reducing costs and maintenance needs. Some main advantages include:
- High accuracy of fit: The high accuracy of the bearings allows low clearance values in seals and impellers, which reduces volumetric flow losses. This improves the operating efficiency of the systems in which they are used.
- Lower rolling friction: The bearings have lower rolling friction compared to other components, which contributes to smoother and more efficient operation. This is especially useful in applications that require frequent starts and stops or very low speeds, such as variable speed drive systems.
- Ability to handle low viscosities and high oil dilution: The bearings can operate effectively with low viscosity oils and withstand high oil dilution, making them suitable for a wide range of operating environments.
- Reduced lubricant usage and maintenance: In general, bearings require up to 90% less lubricating oil, which reduces the need for lubrication system maintenance and contributes to operational efficiency and sustainability.
- Reduced system complexity and cost: The use of bearings simplifies system layout to handle thrust and combined loads, as well as large misalignments. This reduces both the complexity and cost of the system as a whole.
Advances in intelligent bearings technology
Among intelligent bearings, the most innovative are the magnetic type, which is described below:
Magnetic-type smart High efficiency bearings
Intelligent bearings are advanced devices that use electromagnetic fields to suspend and stabilize a rotating shaft without direct physical contact. An advanced electronic control system adjusts these electromagnetic forces in response to the forces generated by machine operation.
The radial magnetic bearing positions the rotor by means of four electromagnets, each consisting of one stator component and one rotor component. The opposing electromagnets are adjusted to attract each other. When an external force causes the rotor to change position, the movement is identified by position sensors.
The electronic control system responds by adjusting the current flowing through the respective electromagnets, returning the rotor to its original position. The axial magnetic bearing positions a rotor axially using electromagnetic forces that pull in opposition to the collar.
Due to the sensitive nature of magnetic surfaces, active magnetic Intelligent bearings (Figure 5) include auxiliary bearings. These bearings support the rotor when the machine is stopped, in addition to supporting overloads and supporting the rotor in the event of system failure.
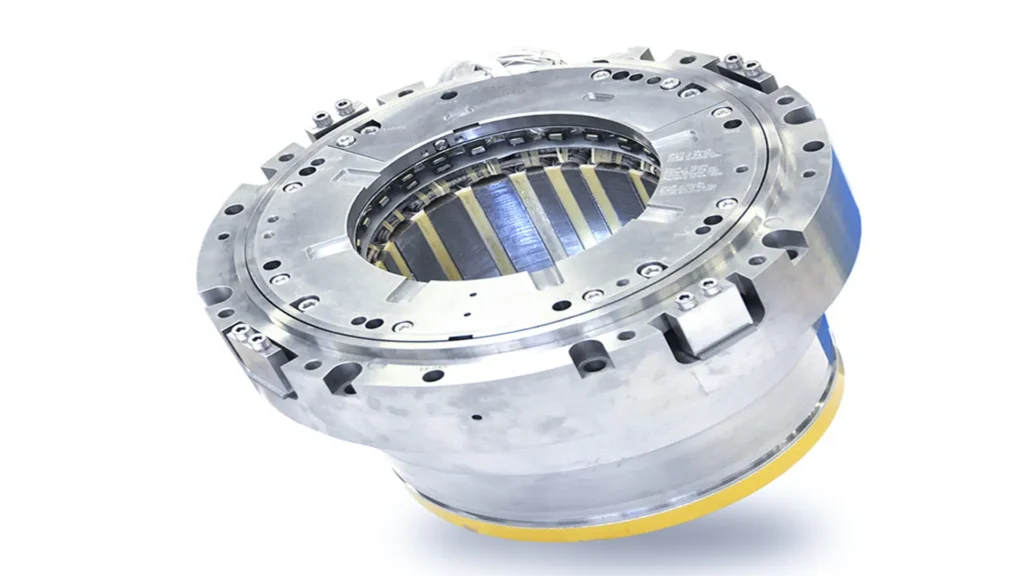
Active magnetic Intelligent bearings (AMB Active magnetic bearing) is a type of bearing that supports a load by magnetic levitation. They use electromagnetic forces to hold a rotating shaft in a precise position without physical contact. This technology provides several advantages, such as reduced friction, no mechanical wear and the ability to operate at high speeds.
Intelligent bearings incorporate miniaturized MEMS (Micro-electromechanical Systems) sensors capable of measuring multiple parameters simultaneously. These include:
- Accelerometers for vibration analysis (range 0.1-20 kHz)
- Thermocouples or RTD for temperature monitoring (±0.1 °C accuracy)
- Strain gauges for load measurement (0.1% full scale accuracy)
- Capacitive sensors for oil film thickness measurement (range 1-100 μm)
Why is bearing lubrication important?
Bearings are designed to facilitate smooth and efficient motion by minimizing friction between moving parts. However, without proper lubrication, the metal surfaces of the bearing can come into direct contact, increasing friction and accelerating wear. Applying a good lubricant forms a separating film between these surfaces, decreasing friction and preventing wear, thus ensuring optimum performance of the rotating equipment3.
Lubrication forms a thin film between the balls and bearing races, minimizing friction and thus the associated energy losses. This reduction in friction allows the bearing to operate more efficiently.
The selection of the proper lubricant and lubrication method (such as mineral oil, synthetic oil or grease) is critical and must consider variables such as specific operating conditions, speed, load and bearing temperature.
Bearings often operate in harsh environments, including moisture, dust and chemicals. An excellent lubricant acts as a protective barrier, preventing moisture and contaminants from reaching the surfaces of rolling elements and causing corrosion. This is especially crucial in industries where equipment is exposed to corrosive substances or operates in high humidity conditions.
During operation, bearings generate heat due to friction. Excessive heat can deteriorate bearing materials, causing premature failure. Applying a quality lubricant facilitates heat dissipation by absorbing heat and moving it away from bearing surfaces, keeping them within their optimum temperature range.
Properly lubricated bearings operate more quietly and with less vibration. Noise and vibration can indicate bearing problems, such as misalignment or excessive wear. By maintaining scheduled lubrication, these problems can be mitigated, ensuring smoother and quieter operation of machinery.
The durability of bearings is closely linked to the quality and consistency of their lubrication. Regular and adequate lubrication prevents premature wear, reduces the risk of contamination and minimizes the likelihood of overheating. This, in turn, prolongs the service life of the rotating equipment they support, resulting in lower maintenance costs and higher productivity.
Conclusions
Innovations in intelligent bearings have significantly improved the efficiency of rotating equipment in various industries. A key advance is the use of ceramic materials such as silicon nitride and zirconium, which offer lower coefficients of friction, better resistance to corrosion and high temperatures, and lower wear compared to traditional steel bearings. These materials not only reduce frictional energy losses, but also improve bearing performance and service life, meeting the requirements of equipment manufacturers and contributing to technological progress in multiple sectors.
Certain applications such as; precision equipment, offshore platforms and FPSO units, hermetic compressors, take advantage of the key benefits of magnetic Intelligent bearings, such as non-contact operation, elimination of the need for lubrication, ability to operate in extreme conditions and reduced maintenance. Their use is growing in industries seeking greater efficiency, reliability and performance in challenging conditions.
It is important to note that magnetic bearings require a constant supply of electrical power and a sophisticated control system to maintain rotor stability. In addition, mechanical backup bearings are usually included in case of electrical system failure or overload.
References
- https://es.wikipedia.org/wiki/Rodamiento_de_bolas#Condiciones_de_funcionamiento
- https://evolution.skf.com/es/rodamientos-magneticos-a-toda-prueba/
- J/E Bearing & Machine Ltd., “Plain or Rolling Bearings – Which is Best?”