Introduction
Robotic innovation has revolutionized procedures related to the preparation of metal surfaces, the application of coatings and inspection in the industrial field. The incorporation of robots has contributed to greater efficiency, precision and substantial cost reduction, while improving the quality of final products.
One of the crucial procedures in applying paint to metal surfaces is the correct preparation of the surface to be protected. This stage is essential to achieve an optimal result in the installation of a coating system; However, despite the insistence on its importance, its planning and execution are often neglected.
For the preparation of metal surfaces there are several types of cleaning such as; Shot blasting, Sand Blasting, Waterjetting, Dry-Ice Blasting and laser cleaning, among many others. This requires advanced methods that make them efficient in all aspects and in this case the robotic innovation It is allowing the automation of critical and complex tasks, making them more precise and safe and they are also demonstrating their value in one of the most important processes such as shot blasting, which will be the topic that we will focus on in this article.
What is grit?
Grit or shot are abrasives used in numerous applications such as preparing surfaces for painting. This preparation is known as the shot blasting process. Shots are generally manufactured in a spherical shape and from different materials (carbon steel, stainless steel, plastic, aluminum, glass, copper, among others), roughness, grain sizes and hardness, which make excellent results possible in different shot blasting applications. , such as preparing surfaces for paintings, among others. In the figure. 1, a type of shot can be observed.
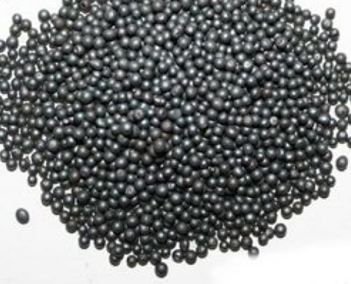
Figure 1. Group of spherical grit with smooth surfaces.
What is shot blasting?
Shot blasting is the most important process in surface preparation, before applying coatings. It consists of projecting abrasive particles at high speed (65-110 m/s) on the surface of an object to remove impurities, rust, old paint and other imperfections and at the same time give it a roughness or anchor profile that will allow the coating or paint to has good adhesion that guarantees the durability of the coating.
In the shot blasting process, the force of the abrasive hits the surface to be cleaned, removing contaminating materials. The shot is collected through the recovery channel and can be used later. Polluting particles are eliminated by means of a dust collector. It should be considered that with frequent use of this system it will end up wearing out and it will be necessary to replace it by adding new particles.
Robotic innovation in Shot Blasting Systems
Robotic shot blasting is an advanced method for cleaning metal surfaces safely, precisely and efficiently. A robotic blasting system removes the operator from the environment keeping them out of harm’s way while allowing continuous operation to maximize uptime and productivity. The remote control system allows adjustment of nozzle speed and trajectory, while a dust collector and media reclaimer capture particles and allow abrasives to be recycled.
Robots can precisely control the direction and speed of shot shots, ensuring high-quality, uniform surface preparation. In addition, robot programming allows the process to be adapted to different shapes and sizes of parts efficiently, reducing the need for expensive equipment and manual adaptations.
Robots can perform dangerous tasks in hostile environments without risk to workers. This is especially relevant in offshore applications, where exposure to corrosive and extreme environments is common. They can also be operated continuously and consistently, minimizing downtime and increasing production efficiency.
Advantages of robotic innovation in shot blasting
- Improved quality results, reliability, safety and great versatility make the robotic shot blasting process very reliable. This modern method is becoming increasingly requested in the preparation of surfaces for paint and coating application in the shipping, oil, gas, petrochemical and construction industries, among others, which consider some of these benefits:
- Improved Quality – Using a robotic system allows for consistent surface quality that meets the strict specifications of each project. You can eliminate errors due to human supervision and ensure you are working at the right angle to get the best results.
- Cost savings: Process automation reduces labor and material costs and minimizes waste.
- Increased Productivity – The ability to operate continuously with reduced labor requirements helps increase flexibility and increase productivity. Robotic abrasive blasting systems can exponentially increase capacity and speed up processes while improving accuracy. You can benefit from faster time to market and better results.
- Durability: Robotic shot blasting equipment can withstand the toughest jobs and most aggressive environments. These units are designed to keep out dust and moisture and resist impacts for long life.
- Increased Efficiency – Innovative abrasive blasting systems increase product throughput and flow while reducing costs related to maintenance and material loss. The compact size reduces space requirements, while precision robotics eliminates errors and rework.
- Work without dust through a closed circuit: These devices are connected to a vacuum cleaner to guarantee a dust-free environment.
- Safer Workplaces: With robotic innovation in this area the potential for worker injury is significantly decreased and exposure to harmful contaminants is eliminated, so additional safety clothing and accessories are not needed to protect personnel from hazardous exposures. Robots can perform dangerous tasks in hostile environments without risk to workers.
Robotic coating application
After a good surface preparation, the next step is the application of coatings, which is another of the critical stages in the protection of corrosion surfaces. Uniformity in application is essential to ensure the quality and durability of the coating. The integration of robots in this process guarantees precision and uniformity, which leads to a significant improvement in the quality of the final product.
Robots can precisely control the amount of coating applied, the travel speed and the angle of application. Additionally, robots can apply them in hard-to-reach areas, such as pipe interiors or components with complex geometries, where human labor would have difficulty achieving the desired uniformity.
Efficiency in the application of coatings also translates into material savings. Robots can optimize paint usage, reducing waste and associated costs. Additionally, robot programming allows for quick switching from one type of coating to another, increasing production flexibility.
An exemplary case of robotic coating application is the shipbuilding industry. Ships face extreme environmental conditions and must be uniformly and durably coated to resist corrosion. Figure 2 shows the application of a robotic coating.
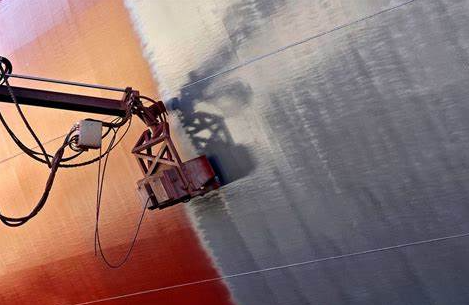
Figure 2. This image shows robotic coating application to a boat.
Automated inspection
Robotic innovation has also revolutionized this aspect by allowing high-precision automated inspections. Robots equipped with advanced sensors can detect defects and anomalies consistently, eliminating human subjectivity and improving the reliability of inspections.
With robots, component inspections can be carried out, locating imperfections in coatings and paints in real time. The information collected can be used to make decisions about required corrections. Additionally, automated inspection saves time and reduces costs. Robots can perform inspections continuously and efficiently, without the need for prolonged production stops. This is especially valuable in the automotive industry, where vehicle quality and safety are of utmost importance.
There are two different types of robotic inspection:
- Mobile robots: Generally involves the use of small mobile robots or drones to perform visual inspections at large sizes. For example, to inspect long pipes and structures.
- Metrology robots: They are measurement equipment used by inspection professionals. Robotic metrology normally implies connecting a metrology sensor to the end of a robotic manipulator for measurements.
Recent developments and future trends
Robotic innovation continues to advance the shot blasting, coating application and inspection processes. Some of the developments and trends to watch include:
- Collaborative Robots (Cobots): Cobots work in collaboration with humans and are ideal for tasks that require interaction between the two, such as applying coatings in hard-to-reach areas.
- Mobile Robots: Mobile robots can move from one location to another in the factory, increasing flexibility and versatility in process automation.
- Advanced Sensors: Incorporating more advanced sensors allows robots to perform more precise and detailed inspections, even in complex environments.
- Remote monitoring and management systems: These advanced systems allow robots to be monitored and controlled remotely, improving efficiency and responsiveness. One of the latest technological developments in this field was made by Aegion Coating Services which uses in-house robotic coating equipment that travels inside the pipe, finds the weld and then cleans, vacuums and coats the area. The robots transmit a real-time video image to the operator, which is then used for control and inspection.
- Companies such as Blasting Experts Inc, have developed portable equipment that is capable of performing shot blasting in vertical and horizontal positions on flat and cylindrical areas (pipes), and can also be used for work in plants and in the field. It is a very versatile piece of equipment since it can carry out all these activities without the need to invest in other equipment.
- Aegion Coating Services developed a robot whose main objective is to detect defects in pipe coatings. It is part of a robotic system that internally cleans, coats and inspects, measuring dry film thickness and locating any damage to the coating.
Conclusions
Automating critical and complex tasks using robots not only optimizes production but also ensures worker safety in hazardous environments. Recent developments and future trends promise to continue improving these processes, supporting efficiency and innovation in the industry. Robotic innovation is a clear example of how technology is transforming manufacturing and leading the way towards a more efficient and sustainable future.