Introduction
In the oil & gas industry, efficiency and operational safety are the basis for productivity, environmental sustainability, and structural integrity of the facilities. In these processes and systems, rotating equipment, such as pumps, compressors, and turbines, drive the constant flow of products and power generation, in order to maintain daily operations without interruptions and with high performance. Infrared Technology is a key tool in this context, enabling accurate and non-invasive monitoring of the status of this equipment.
The exigency of operations in the oil & gas sector keeps these equipment under extreme conditions, which increases the risk of failures and, with it, the potential for dangerous consequences. In this context, predictive maintenance becomes an important tool in the early identification of signs of wear or failure before these problems materialize into operational interruptions or accidents. Infrared technology, through thermography, offers an effective way to detect thermal anomalies indicative of problems such as overheating, excessive friction or the presence of leaks, allowing proactive intervention to ensure operational continuity and safety in the oil & gas sector.
The purpose of the article is to highlight the importance of Infrared Technology, specifically thermography, in the predictive maintenance of rotating equipment within the oil & gas sector. To show how this technology can improve efficiency, safety, and operational continuity by early identification of anomalies and potential problems in equipment.
Fundamentals of rotating equipment
Rotary equipment is fundamental to the operations of the oil & gas industry, from extraction to refining. These machines, which include pumps, compressors, and turbines, facilitate the constant and efficient flow of materials, and also ensure the uninterrupted operation of the facilities. The relevance of this equipment lies in its ability to maintain operations at scale, facing challenges ranging from adverse environmental conditions to the demand for near-relentless throughput.
The efficiency and reliability of rotating equipment are critical to operational economics and workplace safety. A failure in these systems can lead to unplanned downtime, significantly affecting production and, in extreme cases, resulting in safety incidents. Maintenance is therefore a matter of operational efficiency and risk prevention.
Predictive maintenance of rotating equipment
Predictive maintenance is a methodology through which equipment failures are detected based on continuous monitoring and analysis of performance data. The effective implementation of predictive maintenance strategies depends largely on technology and diagnostic techniques, in this case the use of infrared thermography is ideal to make early detections and anticipate possible failures, preventing a major problem in the future. It means that thermographic cameras become a tool capable of determining when to carry out effective preventive maintenance.
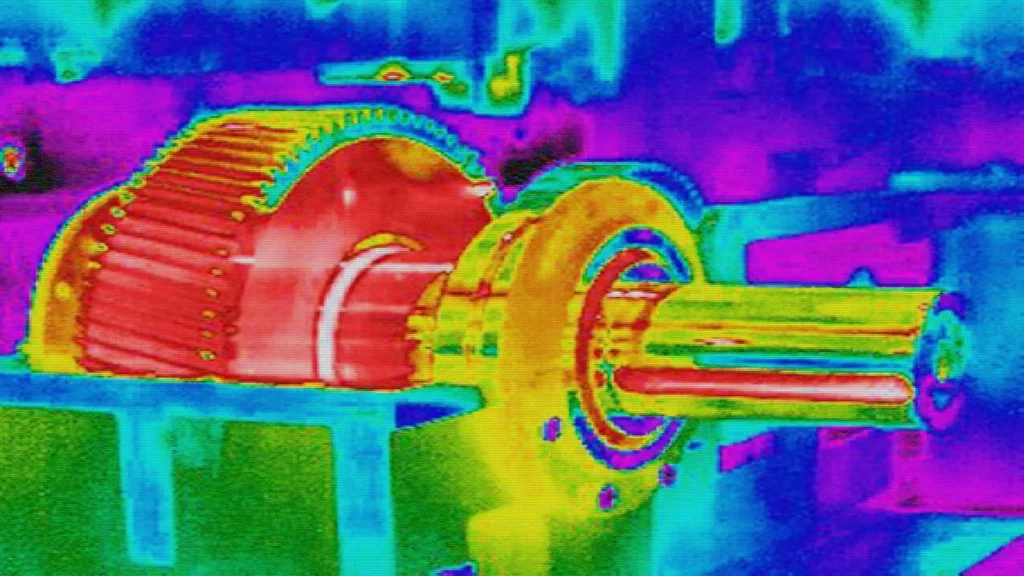
Through infrared image analysis, specialists can detect defects in rotating equipment that would be impossible to identify with conventional methods. This non-invasive approach offers a window into the internal state of the machinery, such as the identification of overheating problems, misalignment, or imbalances, which are indicators of future failures. The adoption of this technology allows optimizing resources dedicated to maintenance, marking a before and after in asset management in the oil & gas sector.
Benefits and applications of Infrared Technology
Infrared technology is based on the detection of thermal radiation emitted by all objects, which makes it possible to visualize and measure heat without the need for direct contact. This principle becomes an important technique in predictive maintenance, especially in the oil & gas industry, where efficiency and safety are paramount. Through thermographic cameras, it is possible to obtain detailed images (thermograms) that reveal anomalous heat patterns, indicative of failures in rotating equipment.
Among the most significant advantages are the following. First, it allows early detection of problems that might otherwise go unnoticed until they cause major failures. Aspects such as overheating of bearings, excessive friction between components or undue heat build-up in certain areas can be quickly identified and corrected. Secondly, as a non-invasive method, Infrared Thermography minimizes the risk of damaging equipment during inspection, an important aspect in maintaining the integrity of expensive and complex machinery.
Below is a video from Fluke Southeast Asia, which shares information about the benefits of using thermography in predictive maintenance.
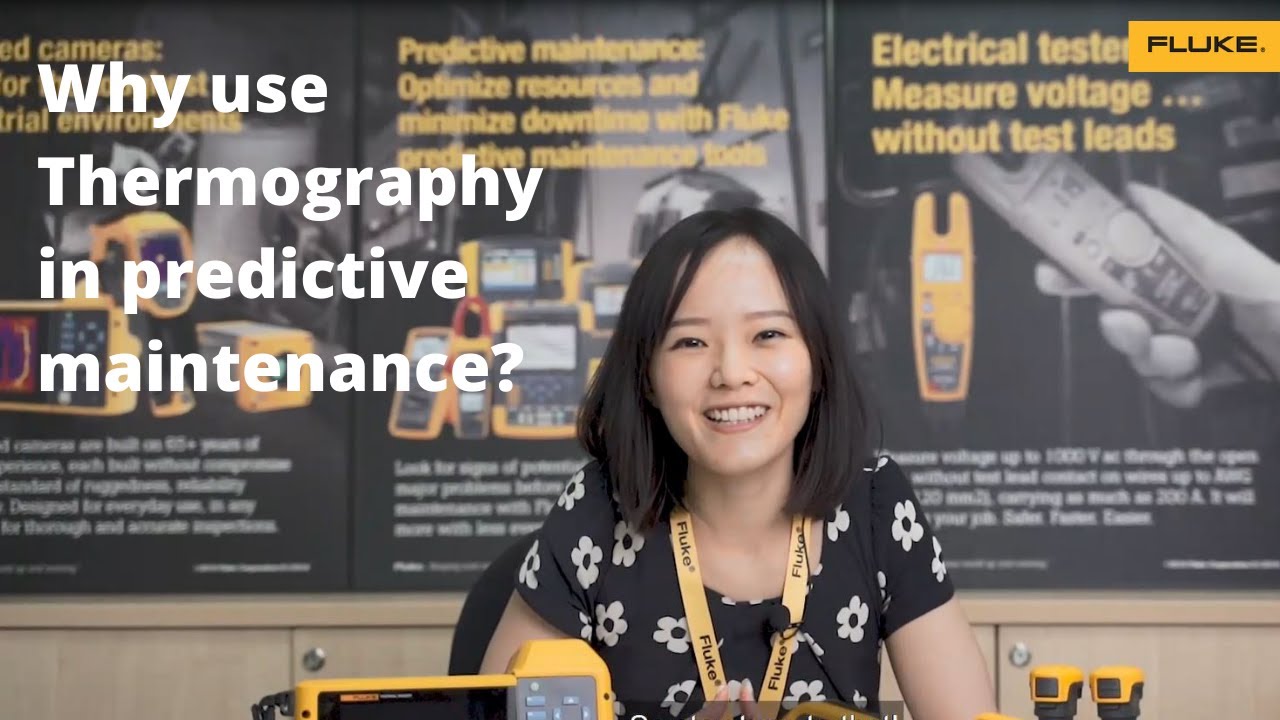
Benefits of Thermography in predictive maintenance.
In the field of application, infrared cameras are versatile tools that are suited to a variety of operational contexts, from routine inspections to specific analyses in response to condition monitoring alerts. For example, in the case of compressors and pumps, thermography can reveal areas of excessive heat on mechanical seals, a common symptom of wear or malfunction. In turbines, infrared imaging can help identify abnormal thermal gradients that suggest problems with lubrication or shaft alignment.
Critical parts and predictive maintenance
At the core of the machinery that powers the oil & gas industry, certain critical parts of rotating equipment, such as bearings, shafts, and seals, demand special attention. These components are susceptible to wear and failure due to their constant exposure to demanding operating conditions. Regular inspection and maintenance of these parts is essential to prevent unplanned downtime and to ensure the long-term integrity and reliability of the equipment.
Predictive maintenance, which relies on technologies such as infrared thermography, allows technicians to identify thermal anomalies that indicate potential problems, such as an unusual temperature rise in bearings or shafts, which can signal excessive friction, misalignment, or lack of lubrication. Similarly, defective mechanical seals, prone to leakage, can be quickly detected by observing irregular thermal patterns in infrared images.
Evaluation using Infrared Technology allows early intervention, before these problems evolve into complete failures that could bring operations to a halt. For example, a bearing showing an anomalous heating pattern can be replaced or repaired before it causes equipment failure, thus avoiding costly shutdowns and emergency maintenance. This reduces downtime and prolongs equipment life by preventing excessive wear and damage to other components.
The use of Infrared Thermography in predictive maintenance contributes significantly to the optimization of maintenance resources. By focusing on actual equipment conditions, rather than rigid maintenance schedules, companies can prioritize interventions based on the urgency and severity of the damage detected, minimizing the risks associated with unnecessary or excessive maintenance.
Implementation of Infrared Technology in predictive maintenance
Effective implementation of Infrared Technology in predictive maintenance programs can be broken down into clearly defined steps, each contributing to successful and effective integration:
- Needs assessment: Conduct a thorough analysis to identify critical areas where Infrared Thermography can have the greatest impact. This includes assessing the organization’s current capabilities and specific maintenance needs.
- Strategic planning: Develop a detailed plan that aligns the incorporation of Infrared Technology with the company’s maintenance objectives. This plan should specify how thermographic inspections will be conducted, the interpretation of the data, and the integration of these findings into existing maintenance practices.
- Data systems integration: Establish systems for managing and analyzing thermographic data, enabling trend tracking over time and improving failure prediction capabilities.
- Specialized training: Invest in the training of technical staff to ensure that infrared inspections are performed correctly and that the data collected is interpreted effectively. Training should be viewed as an ongoing investment to keep the team up to date with best practices in Infrared Thermography.
- Iteration and continuous improvement: Treat the implementation of Infrared Technology as an iterative process, constantly looking for ways to improve and optimize the use of this tool within predictive maintenance. This includes regularly reviewing procedures and results to adjust the strategy as needed.
- Effective communication: Establish clear communication channels between the maintenance team, operations, and management to ensure that all levels of the organization are informed about the benefits and progress of the implementation of Infrared Thermography.
Benefits and challenges
Each of the above steps contributes to a solid framework for the integration of Infrared Technology into predictive maintenance efforts. This ensures that the adoption of this tool maximizes operational efficiency, improves safety, and contributes to long-term profitability in the oil & gas sector.
Benefits
- Cost reduction: Implementing Infrared Technology in predictive maintenance helps identify problems before they escalate, avoiding costly repairs and unplanned production downtime. This proactive approach can result in significant long-term savings.
- Improved safety: By detecting potentially dangerous conditions such as overheating or excessive wear early, the risk of accidents is minimized, improving the overall safety of the facility.
- Increased operational efficiency: The ability to schedule maintenance based on actual equipment needs, rather than following a fixed schedule, improves operational efficiency, ensuring that equipment is always in optimal operating condition.
Challenges
- Initial costs: The acquisition of Infrared Thermography equipment and the integration of analysis systems may represent a significant initial investment.
- Need for specialized training: To maximize the potential of Infrared Technology, it is essential to have technical personnel properly trained in its use and in data interpretation, which implies an additional commitment in training and development.
Conclusions
The evolution of predictive maintenance will continue to be closely linked to technological advances, with infrared thermography playing a key role in transforming maintenance practices towards smarter, safer, and more efficient approaches.
The integration of Infrared Technology in predictive maintenance of rotating equipment represents a significant evolution in equipment management in the oil & gas sector, by accurately and early identification of problems, ensuring continuous, safe, and efficient operation, laying the foundation for a more resilient and sustainable industry.
References
Own source