In civil engineering, inspection and evaluation of reinforced concrete structures are fundamental to ensure long-term durability and safety. Non-destructive evaluation (NDT) methods play an essential role in providing critical information about the internal condition of these structures without causing damage.
Among the range of NDT techniques, industrial radiography stands out as one of the most reliable and effective, especially for reinforced concrete. This article discusses the concept and principles of the industrial radiography test method, its applications, and the unique advantages it offers for the inspection of reinforced concrete structures.
Importance of NDT in civil engineering
The implementation of NDT in civil engineering is crucial to maintain the safety, durability, and cost efficiency of concrete structures. It ensures that potential failures are identified before they cause structural failure, allowing for timely maintenance and repairs. In addition, NDT plays a vital role in assessing the structural performance of buildings, bridges, dams, and other critical infrastructure.
Reinforced concrete structures degrade over time due to various physical and environmental factors, and it is necessary to inspect them periodically to avoid undesirable consequences. Experience shows that the cost of repairing a damaged structure is much higher than the cost of the protective measures it could have been subjected to when it was sound1, and this damage can be detected before it becomes visually evident with the application of NDT.
Non-destructive evaluation (NDT) of reinforced concrete
Concept and purpose of non-destructive evaluation (NDT)
Non-destructive evaluation refers to a set of methods used to evaluate the internal properties of materials and structures without altering or damaging them. The main objective of NDT is to detect internal defects, learn properties, evaluate the integrity of structures, and verify the quality of construction materials. In the context of reinforced concrete, NDT helps to identify problems such as cracks, voids and imperfections in the concrete and embedded reinforcing steel, evaluate the strength of the material, as well as the correct positioning of the steel frame inside the structure.
In this video, learn why concrete corrosion is a problem and how to evaluate it. Source: Giatec Scientific Inc.
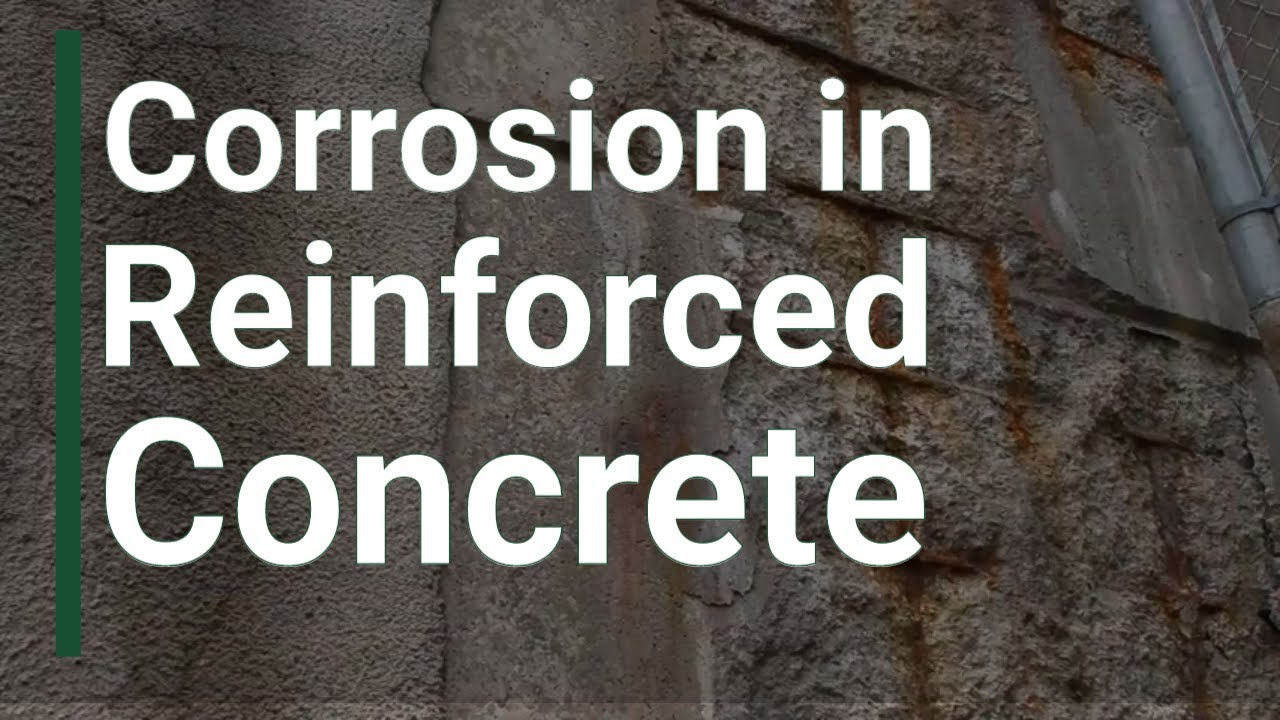
The process of rebar corrosion in reinforced concrete.
NDT methods applicable to reinforced concrete
There are several NDT methods available for inspection of reinforced concrete, each with specific applications and advantages:
- Ultrasonic testing: This method uses high-frequency sound waves to detect internal defects, measure the thickness of the concrete and evaluate the quality of the bond between the concrete and the reinforcing steel. It is also used to evaluate the level of compaction of the concrete mass by measuring its speed of sound, which is related to the strength of the concrete.
- Magnetic resonance imaging: This technique measures magnetic fields to evaluate the integrity of the reinforcing steel within the concrete, detecting corrosion and other defects.
- Industrial radiography: One of the most accurate NDT methods, radiography uses X-rays or gamma rays to produce detailed images of the internal structure of concrete, revealing cracks, voids, and the placement of reinforcing steel.
What is industrial radiography, and how does it apply to reinforced concrete?
Operating principle of industrial radiography
In the radiographic test, a beam of ionizing radiation is passed through the part to be inspected, then this radiation is projected onto an image detector or recording medium such as a radiographic film, the material of the part will attenuate a part of the radiation due to the density and changes in the thickness of the material and the rest will be projected onto the recording medium. The energy level and intensity of the radiation will depend on the thickness and density of the material, as well as the sensitivity required for the inspection and the recording medium used.
Thicker and denser sections of material will allow less radiation to pass through the sample (higher attenuation). Conversely, a thinner section in the direction of radiation, as in the case of interior faults, as well as the presence of material inclusions of lower density, will cause more radiation to pass through these areas. The image detector records the amount of radiation that is projected on the recording medium showing the internal state of the component once it is processed, which can take a time in minutes in the case of a radiographic film or almost instantaneously in digital radiographs.
Through more advanced techniques such as digital radiography, a greater dynamic range (greater range of thicknesses in an image) is obtained and allows the use of sources of lower activity (gamma rays) or with lower intensity (X-rays), maintaining high quality and immediate or almost immediate results.
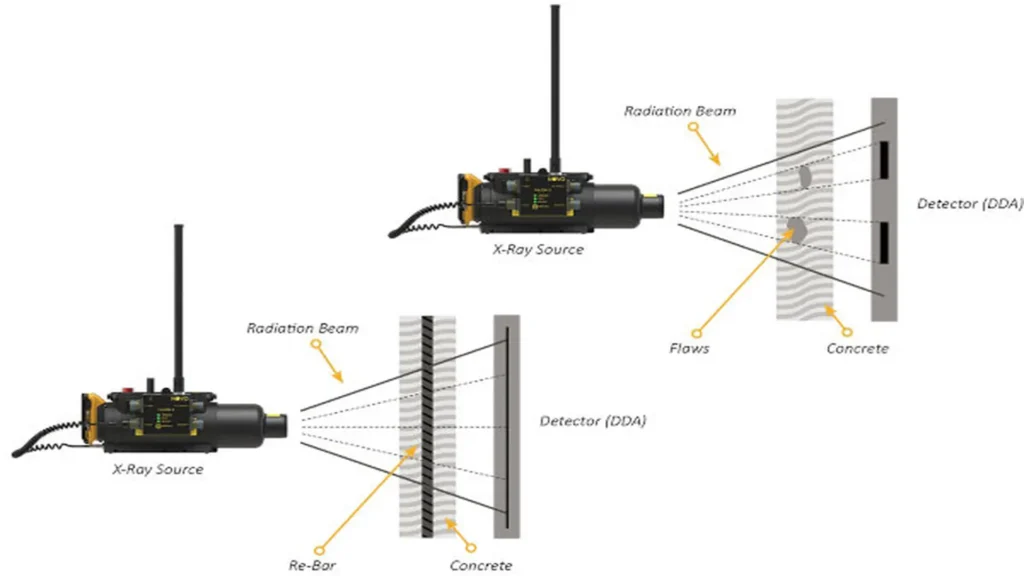
Application of radiography in the inspection of reinforced concrete
Radiography is particularly useful for inspection of reinforced concrete structures where visual inspection or other surface methods are insufficient. Its most common applications include:
- Evaluation of reinforcing steel placement: Radiography provides clear images of the embedded reinforcing steel, allowing engineers to confirm its correct placement and identify any possible misalignment. Triangulation methods or making use of techniques such as stereoscopic radiography can be used for this purpose.
- Detection of voids or internal cracks: This method can detect hidden voids, air pockets, and cracks within the concrete, which could affect the structural integrity of the building or infrastructure, or heat transfer through these areas.
- Evaluation of repairs: Industrial radiography is used to verify the quality of repairs performed on existing concrete structures, ensuring that no new defects have been introduced during the process.
- Detection of corrosion problems: Apart from the location and measurement of reinforcement, it is also applied to detect corrosion problems and damage.
Figure 1. Digital radiography in the detection of voids (top right) and reinforcing steel (bottom left). https://www.ndt.net/news/images/26218-2.jpg
- X-ray: X-ray radiography is suitable for thinner or less dense concrete structures. X-ray machines can be adjusted to produce the energy levels and intensities needed for different applications, making them ideal for the inspection of small to medium-sized structures or components.
- Gamma rays: Gamma radiation, produced by radioactive isotopes such as iridium-192 or cobalt-60, is used for inspection of thicker or denser concrete. Gamma rays can penetrate through greater thicknesses of material than X-rays produced by conventional machines (X-ray tubes), making them ideal for large structures such as bridges, dams and power plant facilities.
Advantages of using industrial radiography in the inspection of reinforced concrete structures
- Detecting internal defects without damaging the structure: One of the most important advantages of industrial radiography is its ability to reveal internal defects without causing any damage to the structure. This non-invasive approach preserves the structural integrity of the concrete, allowing for periodic inspections over time without the need for costly repairs or invasive procedures.
- Verification of the correct positioning of the steel reinforcement: Through triangulation methods (rigid formula, single marker, and double marker) the depth of the steel reinforcement can be determined, as well as the correct alignment.
- Accurate evaluation of concrete density: Radiography provides highly accurate data on concrete density and composition. Density variations caused by voids, cracks or improper curing can be easily detected through radiographic images. This accuracy is critical to ensure that concrete structures meet required engineering specifications and safety standards.
- Ease of interpretation: The radiograph shows easy-to-understand images that can be understood even by people with no radiographic experience2.
Comparison with other NDT methods
Although industrial radiography is very effective, it is important to compare it with other NDT methods to understand its unique benefits:
- Ultrasonic testing: Ultrasound is excellent for evaluating the level of compaction of concrete, as well as for detecting surface or near-surface defects, but it can be difficult to penetrate these materials because of the high attenuation of ultrasonic waves. In contrast, radiography can penetrate deep into concrete and provide images of both surface and internal defects.
- MRI: MRI is limited to evaluating the reinforcing steel and cannot provide complete data on the concrete itself. Radiography, on the other hand, provides information on both the concrete matrix and the embedded steel.
- Thermal imaging: This method is useful for detecting surface anomalies, such as heat loss or moisture penetration, but lacks the depth and accuracy that radiography offers for internal inspection.
Conclusions
Industrial radiography is a powerful and accurate non-destructive testing method widely used in the inspection of reinforced concrete structures. Using X-rays or gamma rays, radiography can reveal critical internal defects, such as voids, cracks, and improper placement of reinforcing steel, without causing damage to the structure. Its applicability in hard-to-reach areas and its accuracy in assessing concrete density make it an invaluable tool in civil engineering.
When compared to other NDT methods, industrial radiography offers unparalleled depth and clarity, providing engineers with the information they need to ensure the safety, durability, and performance of reinforced concrete structures. As modern infrastructure continues to grow in complexity, industrial radiography will continue to be a valuable tool in civil engineering quality and safety assurance.
References
- CIPRIANO LONDOÑO. Inspección y mantenimiento de estructuras en concreto; Consultado el 16 de Septiembre de 2024. https://360enconcreto.com/blog/detalle/inspeccion-y-mantenimiento-de-estructuras-en-concret/
- NOVO DR, Petah Tikva, Israel; “Concrete Inspections with Digital Radiography”; E-Journal of Nondestructive Testing (eJNDT Articles & News) | Vol. 26(7)