Table of Contents
- Introduction
- Key technologies that are shaping the industrial future
- Benefits of digitalization in the industrial pumps market
- The industrial pumps market: A fundamental element
- The use of AI and machine learning
- Technological innovations in pumping systems for industrial processes
- How is this essential element transformed in Industry 4.0?
- Conclusions
- References
Introduction
The ever-evolving industrial pump market is undergoing a transformation phase, significantly driven by cutting-edge technological advancements and changing dynamics of the industrial environment. In the complex landscape of industrial operations, pumps play a fundamental role in a variety of processes, being essential elements for the circulation, transportation and efficient management of fluids in various sectors.
The critical importance of industrial pumps in these operations has led to a growing interest in exploring and implementing innovations that improve the efficiency and functionality of traditional pumping systems. This article takes an in-depth look at the latest technological developments that are shaping the next generation of these key pieces of equipment in the industry.
Key technologies that are shaping the industrial future
- Digitalization and Internet of Things (IoT): The integration of IoT technologies is revolutionizing the pump industry by allowing real-time monitoring of parameters such as pressure, temperature and vibration. This data is analyzed to optimize pump configuration and control strategies, resulting in better performance and cost savings.
- Energy efficiency and renewable energy integration: Pump manufacturers are increasingly incorporating renewable energy sources, such as solar and wind, to operate pumps that use clean, sustainable energy.
- Advanced materials and technologies such as: 3D printing, augmented reality (AR), virtual reality (VR) in pump design: The advance in 3D printing of this equipment is generating new opportunities for innovation, customization and profitable manufacturing in the industry of bombs. AR and VR are being applied in training, maintenance and problem-solving processes, transforming the way pumps are designed, operated and maintained.
- Expansion of the industrial pumps market globally and regional opportunities: Suppliers of this equipment are experiencing constant growth globally, with notable opportunities in various regions.
Benefits of digitalization in the industrial pumps market
The benefits derived from digitalization in the industrial pump market are significant and encompass increased operational efficiency, improved maintenance strategies and increased reliability. Some of the key advantages of digitalization in this market include:
- Digital twins: Through this technology, pump operators can obtain detailed information about their performance, identify potential problems and optimize maintenance strategies. This technology enables predictive maintenance, reducing downtime and improving overall operational efficiency.
- IoT Sensors: Digitalization enables real-time monitoring of pump performance through IoT sensors, giving operators an immediate view of pump operation; which facilitates proactive decision making and timely detection of possible problems.
- The integration of IoT and wireless communications technology enables remote monitoring and control of pumps, giving operations managers the ability to evaluate equipment performance and make decisions from virtually any location about how the industrial pump market fluctuates.
- Digital monitoring and control technologies: Enable optimization of pump operation, resulting in improved energy efficiency and reduced operating costs. For example, speed adjustments can be linked to changes in power, enabling significant energy savings.
The industrial pumps market: A fundamental element
The industrial pumps market plays a fundamental role in various sectors, being an important element for the efficient operation of numerous industrial processes. These pumps, designed for the transfer of fluids, cover a wide range of applications, from pumping water to handling chemicals and oil.
The variety of pumps available on the market allows adaptation to the specific needs of each industry, guaranteeing optimal performance and effective management of resources. Furthermore, technological evolution has driven innovation in the design and efficiency of pumps, contributing to the continuous improvement of industrial processes.
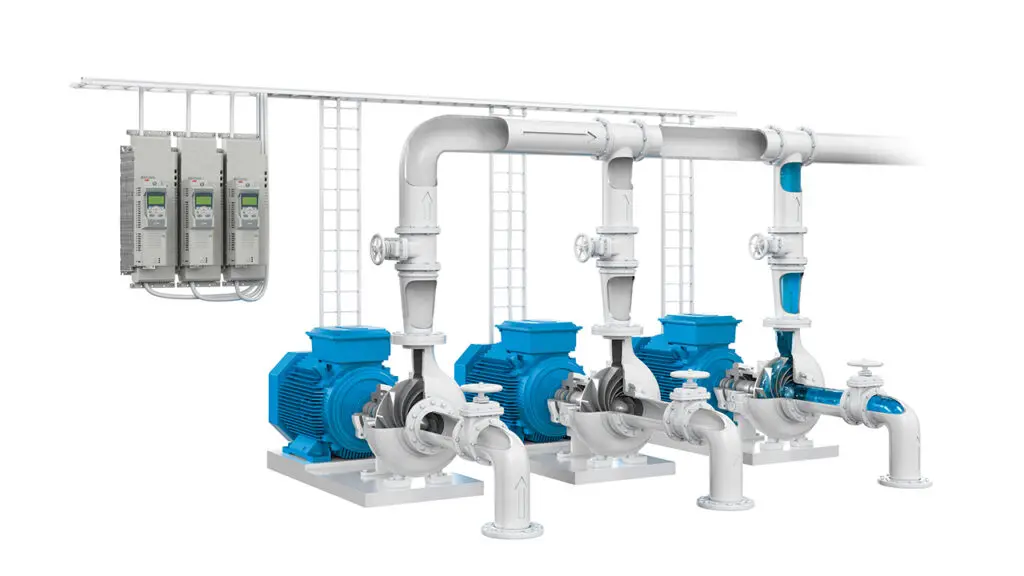
According to studies by companies in the industry, it is estimated that the industrial pumps market will reach $100.76 billion by 2032, with an annual growth of 4.9% between 2022 and 2032.
Likewise, the Indian market is projected to reach $1,140.5 million in the next five years, showing a CAGR of over 4.8% from 2023 to 2028. Centrifugal pumps lead the market with a 64.3% share in 2022, while Asia-Pacific accounts for 47.3% of revenue in that year.
The industrial pump market is transforming due to the growing demand for efficient and sustainable solutions. Among the trends that define its future, digitalization plays a key role.
The use of AI and machine learning
Artificial intelligence (AI) and machine learning (ML) technologies are increasingly integrated into the industrial pump market with the aim of optimizing their performance and efficiency. AI and ML algorithms have the ability to examine significant volumes of data collected from pumps, identifying patterns, irregularities and potential areas for improvement.
These technologies support predictive maintenance, allowing operators to detect potential problems before they become major problems, minimizing downtime and ensuring system reliability. Additionally, AI and machine learning are useful in optimizing pump configurations and control strategies, leading to better performance and cost savings.
Technological innovations in pumping systems for industrial processes
Smart pumps, defined by their integration of digital technologies, improve monitoring, control and predictive maintenance. Features such as sensors, data analytics, and automated functions are explored that optimize performance and minimize downtime.
The evolution of energy-efficient pump designs encompasses advances in motor technologies, variable frequency drives (VFDs), and innovative materials. These contribute to reducing energy consumption, operating costs and promote environmental sustainability.
Using the concept of digital twins applied to pumping systems, they use digital models and simulations to create virtual representations of pumps. This facilitates predictive maintenance, performance optimization and troubleshooting.
The influence of automation and robotics on pumping operations, how automated systems and robotic solutions are optimizing processes, guaranteeing precision and increasing safety in the execution of complex pumping tasks.
Expected future trends in pumping technology, such as advancement in AI-based optimization, inclusion of blockchain for supply chain transparency, or other emerging innovations.
How is this essential element transformed in Industry 4.0?
The history of pumps in engineering is now at the turning point towards the digital age. This analysis explores how a hydraulic pump can be designed adapted to the demands of digitalization.
Pumps can lose efficiency over time or even when newly installed, deviating from the optimal operating point. For years, rotating equipment experts have looked for ways to optimize these machines without the need for complex analysis or costly replacements.
Digitalization is presented as a solution. However, developing new approaches and applying them takes time. There are different technologies on the market that are being applied today to adapt this rotating equipment to market demands.
The ” PumpMeter “, which is the digital monitoring unit (developed by KSB), offers a window into the inner workings of the pump. Equipped with pressure sensors and an analysis unit, this pump-mounted unit monitors suction and discharge pressures 24 hours a day.
Using this data, the PumpMeter calculates the differential pressure and determines the operating point in real time. A graphical representation shows the current operation of the pump in a four-quadrant graph, indicating whether the pump is in its optimal range or needs adjustment.
In the future, instead of relying on wet sensors for measurements, it is planned to record vibrations and transfer this data to the cloud via mobile communication. This offers two significant advantages: First, it avoids the complexity of conventional measurements with wet sensors, especially in environments where chemicals are pumped.
Second, cloud access gives technicians the ability to monitor the status of pumps from any location, eliminating the need to be physically on site.
The operational data is sent to the cloud through a portal, where the company processes it and automatically generates a PDF report with clear recommendations and, where appropriate, suggestions for improvement for the pump.
Now, how would these suggestions for improvement be implemented? The traditional way would involve a visit from a technician. However, what if it were possible to tune the pump using software instead of manually changing the impeller?
Previously, for fixed speed pumps, the impeller was adjusted to match the flow and head to the calculated operating point. Now, the pump speed is adjusted by changing the motor speed.
MyFlow technology (KSB Group) presents potential practical advantages, the IE5 synchronous reluctance motor modulates its operating voltage through the frequency inverter, it can operate in various electrical networks. The KSB FlowManager app displays an overview of all relevant parameters and information of your pump directly on your mobile device.
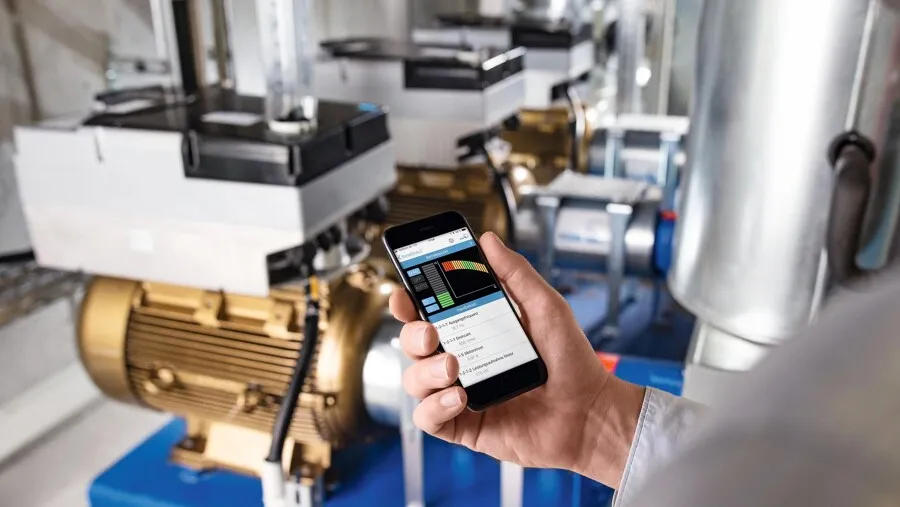
This could be particularly useful for global contractors, eliminating the need to consider local voltage when selecting pumps. Additionally, the direction of rotation is set at the factory, saving time and costs associated with conventional rotation checks.
Optimization through virtual adjustment of the impeller is a key aspect for adapting pumps to Industry 4.0 standards. This approach allows the speed of the pump to be adjusted throughout its life cycle using a smartphone application, known as “Pump Optimization with Virtual Impeller Adjustment”. Unlike mechanical adjustment of the impeller, this technique does not interrupt the ongoing process.
Conclusions
In the current era of digitalization, advanced control technologies, virtual simulations and intelligent algorithms, the industrial pump market could achieve higher levels of efficiency, reliability and sustainability. Sustainability and energy efficiency have also emerged as key factors. Modern industrial pumps are designed to minimize energy consumption and reduce their environmental impact, aligning with growing demands for responsible industrial practices.
Adopting these trends will not only drive innovation but also ensure a competitive position in an ever-evolving industry. Navigating the future of the industrial pump market requires staying abreast of new technologies and taking advantage of the opportunities they offer.
References
1.-www.ksb.com/en-pt/magazine/innovation-and-progress/benefits-of-pump-digitalisation
2.-https://new.abb.com/news/detail/80775/ie5-synchronous-reluctance-motors
3.-www.linkedin.com/pulse/top-6-trends-shape-future-industrial-pump-market