Table of Contents
- Operational challenges that stop the progress of maintenance
- Key challenges facing mining operations
- Industrial maintenance best practices for overcoming challenges
- Maintenance planning strategies to optimize mining production
- Optimization of operating systems in mining
- Impact of digital tools on mining
- Conclusions
- References
Industrial maintenance of equipment in mining is not a walk in the park. Unlike a car in your garage, these machines face a unique set of challenges that can ruin even the most solid maintenance plan.
To manage mining operations efficiently, it is essential to integrate strategies that ensure both the safety of workers and the proper maintenance of the operating systems that support these operations. The mining environment, with its inherent complexity and risks, demands advanced technologies and rigorous procedures to ensure smooth, cost-effective, and, above all, safe operation.
In the mining environment, mineral exploration and processing activities involve significant risks, such as exposure to hazardous radiation and fugitive dust, which can compromise both the health of workers and the environment.
Therefore, the implementation of radiation monitors and dust control equipment becomes a central pillar of operations, providing real-time alerts that enable immediate intervention and reduce associated risks.
From an industrial maintenance perspective, technologies applied to mineral analysis, bulk weighing control, and sampling must be constantly reviewed to avoid unplanned downtime. The use of tools such as XRF analysis not only optimizes exploration and ore grade control, but also minimizes environmental impact through regulatory compliance.
Operational challenges that stop the progress of maintenance
Let’s explore some of the main obstacles mining companies face in keeping their equipment running by applying industrial maintenance:
- Mining equipment operates under immense stress, constantly exposed to dust, extreme temperatures, and vibrations. This hostile environment accelerates wear and tear, leading to frequent breakdowns. These breakdowns create a domino effect, disrupting operations, delaying deliveries, and impacting downstream processes.
- Even minor equipment failures can cause significant unplanned downtime. This downtime not only affects production but can also pose safety risks as maintenance teams rush to fix problems under pressure.
- Limited spare parts: Mining operations are often carried out in remote locations, making it difficult to maintain a stock of readily available spare parts. Long lead times for specific components can further delay repairs and increase downtime problems.
- Inexperienced workforce: The mining industry faces a growing shortage of skilled labor, making it difficult to find experienced technicians who can effectively maintain complex equipment. This lack of experience can compromise safety, efficiency, and compliance with industry regulations.
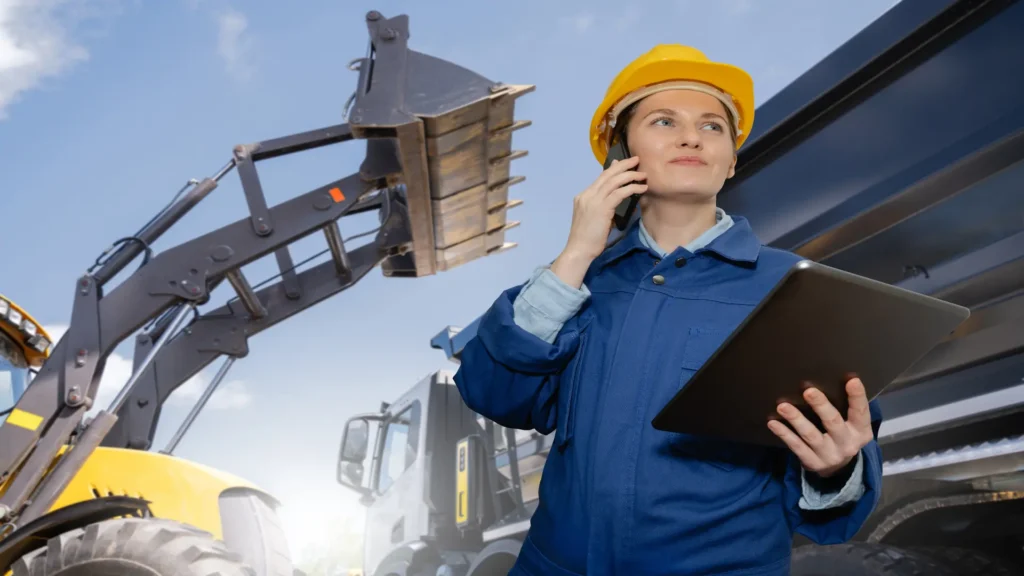
Key challenges facing mining operations
By understanding these obstacles and implementing effective solutions in their industrial maintenance, mining companies can mitigate potential risks, optimize operations, and ensure the continued success of this important industry.
Obsolete equipment: Many mining operations rely on obsolete equipment, often beyond their expected useful life. While these machines may still operate, they are more susceptible to breakdowns and require greater industrial maintenance efforts.
Hostile environments: Mining environments are inherently hostile and unforgiving, subjecting equipment to extreme temperatures, dust, and constant vibration. These factors accelerate wear and significantly increase maintenance requirements.
Inefficient industrial maintenance procedures: Outdated and inefficient maintenance procedures can contribute significantly to equipment problems. In addition, lack of planning and preventive maintenance strategies can lead to reactive maintenance, which addresses problems only after they arise. This reactive approach is often more costly and disrupts operations unnecessarily.
Industrial maintenance best practices for overcoming challenges
Implementing a comprehensive preventive maintenance (PM) program is critical to combating equipment problems. This proactive approach involves regular inspections, maintenance, and lubrication to detect and address potential problems before they become failures.
While maintaining older equipment can be tempting, investing in new, modern equipment can offer significant benefits. Newer machines often offer greater reliability, efficiency, and service life, ultimately reducing industrial maintenance needs and downtime.
Performing periodic inspections allows early detection of potential problems. This can be expedited by adopting condition-based maintenance (CBM) techniques, where real-time data from sensors and equipment monitoring systems are used to detect and address problems based on actual operating conditions rather than relying solely on traditional calendar-based industrial maintenance schedules.
Maintenance planning strategies to optimize mining production
Planned maintenance is an important part of any mining operation. It can help reduce costs by minimizing the frequency of unplanned downtime, as well as transform productivity through increased uptime. Planned industrial maintenance also increases safety by reducing the risk of accidents caused by worn equipment.
To optimize operational systems in the mining sector, it is essential to develop an approach that integrates cutting-edge technologies, process refinement, and strategic management practices. The mining industry, facing increasing efficiency, sustainability, and safety pressures, can benefit greatly from the implementation of a comprehensive system designed to meet these evolving demands.
One of the most critical aspects of streamlining mining operations is the implementation of advanced process control systems. These systems are essential for refining mining operations procedures, where the use of optimization algorithms and control technologies provides the selection of the most efficient operating parameters.
For example, mining processes, such as ore extraction and material transport, can be adjusted to reduce energy consumption and maximize throughput, all while adhering to necessary operational constraints.
Remote operation capabilities are becoming essential, particularly in hazardous environments where human intervention must be minimized. IoT systems that provide real-time telemetry data can positively improve both safety and efficiency by monitoring key environmental factors and operational metrics.
Optimization of operating systems in mining
Modern mining safety solutions can integrate advanced collision avoidance systems for heavy vehicles, reduce accidents, and make operational safety more controllable.
Portable technologies that monitor worker health and safety in real time are also transforming safety management, enabling automated emergency responses and strengthening overall site safety protocols.
Advanced energy management systems that track and regulate energy consumption can significantly reduce the energy footprint of mining operations. The use of renewable energy sources, such as solar and wind power, can further reduce reliance on traditional energy sources, particularly in remote locations.
For example, hybrid power systems can reduce the cost and environmental impact of energy consumption, which is particularly critical in regions where mining operations are off-grid. In addition, optimizing ventilation systems in subway mines can reduce energy use and ensure that air quality remains high, providing operational and health benefits.
A sophisticated communication infrastructure is vital for the seamless coordination of mining activities. Real-time reporting systems and unified communication platforms ensure that operators, managers, and industrial maintenance teams are well coordinated. Subway mines, in particular, benefit from robust communication networks that enable instantaneous reporting, reducing delays and reinforcing decision-making.
In terms of fleet management, the integration of GPS tracking, telemetry systems, and automated dispatch systems intensifies the use of mining vehicles, ensuring that haul routes are efficient and vehicle utilization is maximized.
Another vital aspect is effective water management, which is essential in mining, where advanced systems for treating water from mining operations such as tailings reuse can reduce water use and prevent environmental degradation.
Real-time monitoring of water quality and consumption provides mines with the ability to comply with environmental regulations while rationalizing water use for mineral processing. Recycling water in flotation, leaching, and dust suppression processes reduces the need for fresh water and improves operational sustainability.
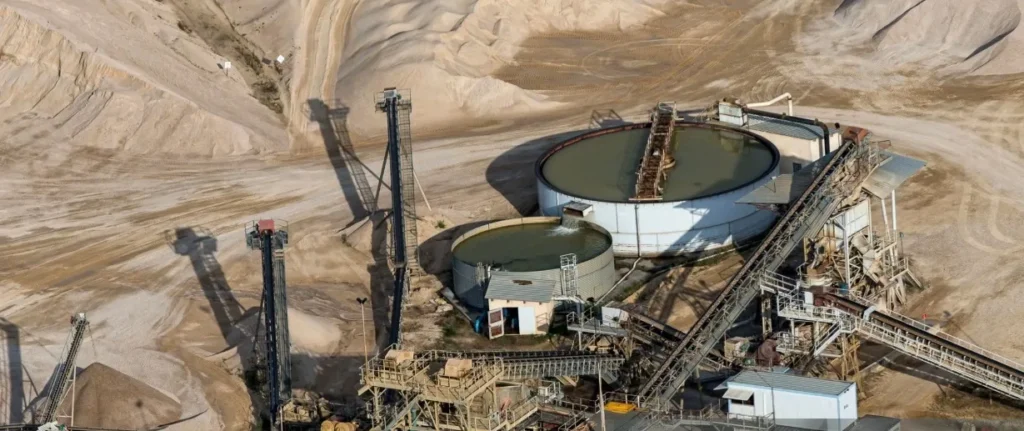
Impact of digital tools on mining
Digitization and the implementation of robotic tools in mining have profoundly transformed the way operations and resources are managed. In this context, digital tools emerge as key pieces to optimize performance, improving not only the efficiency of operations but also their sustainability and safety.
- Optimization through data analysis: The use of digital tools makes it possible to collect large amounts of real-time data on various phases of mining operations, from exploration and material transport to equipment safety and maintenance. By analyzing this data using advanced algorithms, such as machine learning or stochastic optimization techniques, it is possible to detect patterns that provide valuable information on operational efficiency, resource management, and asset condition.
- Predictive and planned maintenance: One of the great technological advances in mining is the implementation of predictive maintenance systems. These systems, based on the collection and analysis of data from sensors installed in machinery and critical equipment, allow to anticipate failures before they occur. By planning and executing industrial maintenance before an asset fails, unplanned shutdowns are reduced, increasing equipment availability and reducing emergency repair costs.
- Reliability management: Digital tools also bring substantial benefits in equipment and asset reliability management. Through simulation models and component lifetime analysis, it is possible to predict asset performance over time and adjust replacement or maintenance strategies, thus optimizing the lifetime of each machine and its components.
- Data-driven strategic planning: The use of these tools also has a significant impact on strategic decision-making. By analyzing historical trends and real-time data, mining operations can identify areas where they can optimize the use of resources and assets. This is particularly crucial in planning new investments or project expansions, where the right allocation of resources can make the difference between the success or failure of an operation.
Conclusions
Optimizing operational systems in the mining sector requires a complex and integrated approach. By implementing advanced technologies, ranging from process control systems and IoT integration to energy management and environmental sustainability, operations can achieve substantial improvements in efficiency, safety, and sustainability. Developing a well-coordinated strategy that addresses these various components will enable mining companies to maintain their competitive edge while meeting the growing demands for responsible resource extraction.
The synergy between safety, predictive maintenance, and robust operating systems is crucial to achieving productivity and sustainability goals in mining operations. Implementing technologies that enable fast and accurate real-time decisions based on reliable data is the key to operating effectively and safely in an environment that demands precision and accountability.
The use of digital tools and the integration of robotics in the mining sector are essential to ensure more efficient, safe, and profitable operations. These technologies enable more informed decision-making, optimal resource management, and continuous improvement in equipment reliability. Mining, a traditional labor- and resource-intensive industry, is in a transformation phase that, thanks to digitization, promises a more sustainable and agile operation, ready to face the challenges of the future.
References
- https://www.planradar.com/au/digital-mining-management-optimise-maintenance/
- https://link.springer.com