Table of Contents
- Introduction
- What is Reliability Centered Maintenance (RCM)?
- Advantages of Reliability Centered Maintenance
- Increased efficiency/Optimization of operating costs
- Costs reduction
- Improving productivity
- Replacement of assets
- Improved security
- Greater alignment with regulatory standards
- Disadvantages of Reliability Centered Maintenance
- Continuous maintenance
- Training and start-up costs
- Complexity
- Strategies for implementing Reliability Centered Maintenance
- Simplifying the analysis
- Knowledge-based diagnosis
- Optimizing predictive maintenance
- Evolution of industrial maintenance: From TPM to RCM
- Conclusions
- References
Introduction
Reliability Centered Maintenance (RCM) is an advanced methodology that ensures optimal operation of industrial equipment, increases asset reliability and improves production efficiency. This approach combines various maintenance strategies to optimize investment in preventive , predictive and proactive maintenance programs, ensuring more effective cost control and increased facility capacity.
As industries become more competitive, maintenance management and improving operational reliability have become key areas of focus. Among the different maintenance methodologies, RCM stands out for its comprehensive approach, encompassing both knowledge-based diagnosis and problem solving by identifying functional failures and eliminating them.
What is Reliability Centered Maintenance (RCM)?
It is a maintenance strategy that combines reactive, preventive, predictive and proactive techniques to maximize the reliability of equipment throughout its life cycle. Through an in-depth analysis of possible functional failures and the integration of different approaches, this maintenance strategy provides a complete solution for industrial asset management .
A clear example of this is the maintenance carried out on an oil platform, where crude oil extraction pumps are critical equipment. Previously, the maintenance strategy was reactive.
However, with Reliability Centered Maintenance (RCM) , current platforms employ sensors that monitor the vibration and temperature of pumps, in order to predict failures before they occur ( predictive maintenance ).
This maintenance strategy enables organizations to identify the root causes of system failures and select the best strategies to eliminate them. This reduces downtime, optimizes asset lifespan, and ensures safe and efficient operation.
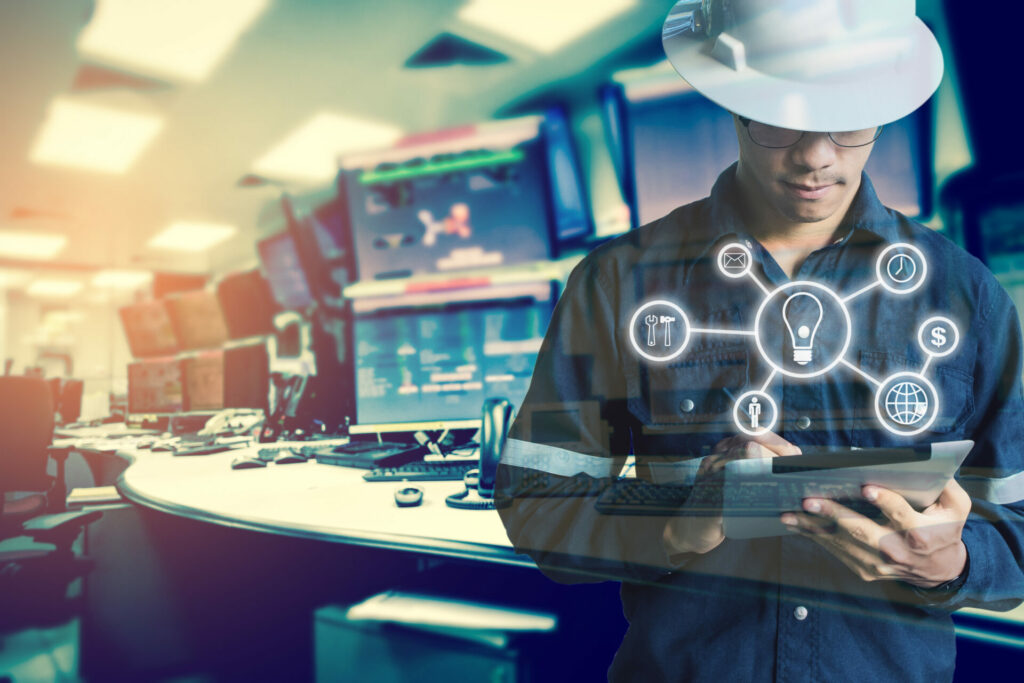
Advantages of Reliability Centered Maintenance
The success of this methodology lies in its multiple benefits, among which the following stand out:
Increased efficiency/Optimization of operating costs
Optimize asset management by eliminating unwanted failures, improving reliability and increasing productivity. By addressing problems before they occur, the frequency of unexpected repairs and downtime is reduced.
A recent study by the World Economic Forum suggests that implementing predictive maintenance and RCM strategies can reduce maintenance costs by 20-30%, and a study by consulting firm Accenture showed that companies that implement the methodology alongside predictive technologies, such as IoT and data analytics, can reduce downtime by 15-25%.
Costs reduction
By preventing major failures and optimizing operations, expenses related to repairs and spare parts are significantly reduced , and by identifying the root causes of failures and managing maintenance appropriately, the useful life of assets is extended. According to data from McKinsey, proper implementation of the method can extend the useful life of equipment by up to 30%.
Improving productivity
Implementing predictive and preventive maintenance strategies prevents unforeseen breakdowns, resulting in greater equipment availability and improved customer satisfaction .
The system focuses on preventing critical equipment failures, resulting in increased operational availability. Companies that have adopted the strategy have reported improvements in asset reliability by 10-15%.
Replacement of assets
If a piece of equipment presents recurring failures or is reaching the end of its useful life, RCM makes it possible to identify the optimal moment for its replacement, avoiding unnecessary interruptions in the production process.
Improved security
Helps prevent catastrophic failures that could put workers or operations at risk. In the energy sector, a reduction in incidents involving critical equipment has been observed by 20% after the adoption of the strategy.
Greater alignment with regulatory standards
It is aligned with international regulations and security standards, allowing companies to more easily comply with audit requirements.
Disadvantages of Reliability Centered Maintenance
While this maintenance strategy offers multiple advantages, it also presents some challenges:
Continuous maintenance
Constant monitoring of equipment and regular maintenance are required, which can be an additional burden in terms of time and resources. In other words, a budget must be set aside for asset management expenses, which for some operators are additional expenses, regardless of the amount of profit it can generate.
Training and start-up costs
Implementing the program involves a considerable initial investment in staff training and in the resources necessary to carry out the reliability analyses.
Complexity
It is a complex system that requires a deep understanding of plant assets and processes. Proper planning and execution of the program can be challenging for organizations without trained personnel.
Strategies for implementing Reliability Centered Maintenance
Implementing this methodology involves a structured and planned approach. Below are some key strategies:
Simplifying the analysis
Preventive analysis should focus on key tasks to reduce the number of unnecessary interventions. Tools such as Preventive Maintenance Optimization (PREMO) have been developed to optimize the number of tasks and reduce costs.
Knowledge-based diagnosis
Failure analysis is fundamental in reliability-centered maintenance. Using tools such as FMECA (Failure Mode, Effects and Criticality Analysis), failure modes can be identified and maintenance interventions prioritized.
Optimizing predictive maintenance
The use of predictive maintenance technologies allows assets to be monitored in real time, anticipating failures and scheduling maintenance efficiently.
Evolution of industrial maintenance: From TPM to RCM
Industrial maintenance has evolved considerably from the simplistic approaches of the past. In the 1980s and 1990s, concepts such as Condition Based Maintenance and Total Productive Maintenance (TPM) were developed, revolutionizing the industry.
Today, the RCM approach offers a more holistic view, allowing organizations to take a proactive approach to maintenance management. This advancement has led to the creation of World Class Maintenance (WCM) systems, which integrate reliability with operational efficiency.
According to a McKinsey report, companies that have integrated this strategy and digital technologies into their maintenance strategies have reduced maintenance costs by 20-30%, with 25% improvements in asset reliability.
A study by the Society for Maintenance & Reliability Professionals (SMRP) reveals that companies that adopt proactive approaches, such as RCM and WCM, experience a 45% reduction in unplanned equipment failures.
Industrial maintenance has evolved from TPM, which involved all levels of the organization in failure prevention, to RCM, which takes a more analytical and reliability-based view. Today, WCM systems, powered by digitalization and real-time monitoring, represent the latest advancement in industrial maintenance, optimally integrating operational efficiency and asset reliability.
Conclusions
Reliability Centered Maintenance It is a fundamental strategy to improve operational efficiency , reduce costs and increase the reliability of industrial assets. Companies that implement it optimize their resources by focusing on the most critical areas, allowing them to reduce downtime and maximize return on investment.
Although this implementation may be costly and complex at first, the long-term benefits more than justify the effort. The methodology’s programs are particularly beneficial for organizations that operate complex assets and seek to improve their operational reliability , safety and efficiency.
In short, maintenance strategy has gained ground not only as a methodology to optimize maintenance processes, but also as a comprehensive asset management approach that seeks to maximize the value of equipment, minimize failures and improve operational safety. Its application continues to expand in critical sectors thanks to its ability to adapt to new technologies such as artificial intelligence and predictive maintenance.
References
DEEPAK PRABHAKAR[1], DHARMARAJ A[2]
[1] Research Scholar, Department of Management, Karpagam Academy of Higher Education, Coimbatore, Tamil Nadu, India
[2]Associate Professor, Department of Management, Karpagam Academy of Higher Education, Coimbatore, Tamil Nadu, India
[3] Turner, S. (2002). PMO Optimization: A Tool for Improving Operations and Maintenance in the 21st Century. International Conference of Maintenance Professionals. Melbourne.