Table of Contents
In a reformer furnace repair or maintenance, it is essential to replace the tubes once the indicated time of their estimated useful life has ended. What would happen in the supposed case if its maintenance is required to advance due to some unplanned operational factor?
Once the unit (reformer furnace) is stopped and ready for personnel to enter, the corresponding evaluations are carried out through visual inspection; to determine in the first instance the most prominent imperfections in the tubes, where damage due to thermal creep or slow creep (Creep) can be seen; either manifested as a diametral widening “Bulging” (see figure 1) or as a longitudinal deformation or bowing of the tube “Bowing” (see figure 2).
Hot spots can also be observed that could be generated by the incidence of the flame towards the tube due to possible problems with the burner, points of oxidation, or perhaps an unusual factor that could present the precipitated degeneration of the catalyst inside the tube, which produces an obstruction or poor circulation of the fluid and therefore, deficiency in the transfer of heat that generates the beginning of a deformation of the tube or in the worst scenario a possible cracking or rupture of it.
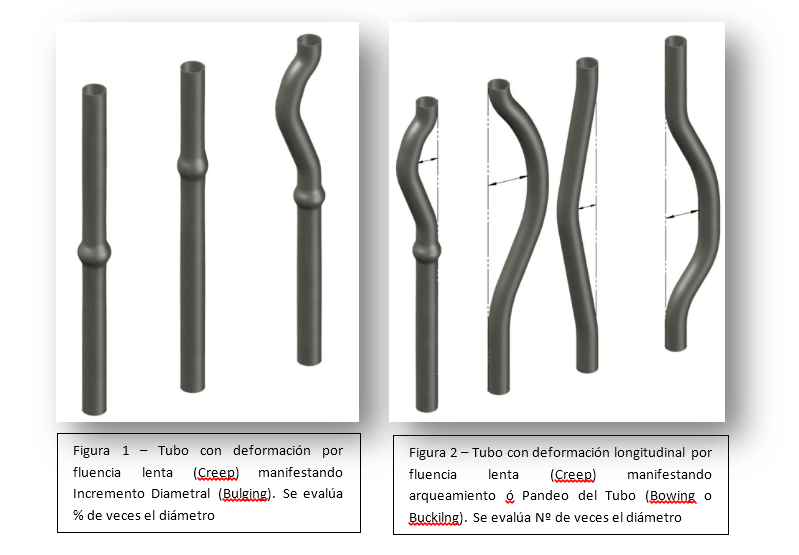
Recommended regulation
When the facilities are given in their entirety (scaffolding assembly and lighting), a verification of the diametral widening of all tubes along these is carried out, with the use of a gauge either made to scale or graduated in percentage form with respect to to the diameter of the tube, a method known as “pass-fail” according to API-573; the deflection or bowing of the tube can be taken as a reference with the use of a plumb line to quantify said deformation.
Taking into account the damage found, based on what criteria should the inspector carry out the partial replacement of tubes, if the number of those with damage was not in its entirety? When speaking of an emergency stop, it is considered that the unit was stopped as a result of an unplanned event, either; due to poor design, a manufacturing defect or operational deviations induced during the process. For this reason, the characterization of the damages found is of great importance, quantifying the level of affectation that they present.
The inspector could question, to what extent is a deflection of the tube permissible? Or the diametral widening, what percentage of its diameter can be within what is accepted? These could be some of the questions asked, in addition to evaluating what factor originated said condition, taking into account the urgency for the delivery of the unit, for its subsequent commissioning. Since the fact that the unit is stopped could mean large economic losses due to lack of production.
During the inspection of this type of furnace during planned maintenance, the installation of new tubes replacing short segments of the existing tube inside the radiant chamber, this action could have the intention of eliminating dead weight if the tube presented relevant damage.
API 573
Indicates that damage due to diametral growth or widening is more relevant than that manifested as buckling, deflection or bowing of the tube, as long as its flaccidity is not directed to make contact with another tube, this code recommends performing Laser Profilometry due because with this technique it is possible to measure the diametral dimensions either from the outside of the tube or from its inside if the tube does not have a catalyst inside it, however, this technology cannot always be counted on, in addition to this technique it is also recommended Evaluation with Refracted Longitudinal Waves and TOFD, Radiographic Inspection and Eddy Currents.
API 579-1
Its part 10, provides evaluation procedures to determine the remaining life of a component that operates in the creep regime.
API 573
In its table 4, it establishes recommended inspection and acceptance criteria for deterioration mechanisms in furnaces and boilers, indicating that for widening or bulging the acceptance criterion is 1% to 5% growth in the diameter of the tube and for flaccidity maximum allowable bowing is 5 times the pipe diameter.
Conclusion
In these processes it is difficult to get enough information to determine what is permissible in this type of reforming units, so the experience and best practices carried out within the oil and gas industries will be an indispensable reference to establish more adjusted criteria according to the operational parameters handled by the processing unit.