Introduction
Hydrocarbon storage tank failure modes refer to the different ways in which these assets can experience failures that compromise their structural integrity, functionality, or safety. This failure process causes serious consequences, such as oil spills, fires, explosions, and production interruptions.
Hydrocarbon tanks are fundamental components in the oil and gas industry, which can fail during their useful life. This article focuses on the identification and prevention of failure modes in hydrocarbon storage tanks, providing an overview of common causes and detection methods. This is done in order to control and take immediate preventive/corrective actions to ensure the structural integrity and proper functioning of these assets.
What are hydrocarbon storage tanks?
They are containers designed to store crude oil and petroleum products. There are different types of tanks, such as steel tanks, subway tanks and above-ground tanks, each adapted for specific applications in the industry. Their size and characteristics vary according to the required storage capacity, the type of product stored and the environmental conditions of the installation site.
Types of storage tanks
- Currently in the market there are 4 types of hydrocarbon storage tanks classified according to the pressure and conditions of the fluid to be handled.
- Atmospheric tank: They can be of floating roof or fixed roof. They work pressures from atmospheric level up to 1.0 psig. It is not recommended to be used for the storage of liquids at temperatures equal or higher than their boiling point.
- Low-pressure tanks: They are built under approved design standards. They can maintain an internal pressure higher than 0.035 kg/cm2 and lower than 1.055 kg/cm2.
- Pressure tank: Pressure tanks are closed containers designed to store fluids at pressures different from ambient pressure; they are usually made of materials such as steel, special alloys, and even glass or reinforced polymers, depending on the application and the fluid to be contained. These can be cylindrical tanks, spherical vessels.
- Refrigerated tanks: They are divided into pressure vessels, pressure spheres and vertical cylindrical tanks. They are used to storing liquefied gases such as LNG or other cryogenic gases for which storage at room temperature is not feasible.
Industry applications
In the production, refining and distribution of petroleum products, tanks of different types and sizes are required for different applications. Small bolted or welded tanks are ideal for production fields, while larger welded storage tanks are used in distribution terminals and global refineries. Product operating conditions, storage capacities, and specific design issues affect tank selection.
Storage tanks are available in a variety of shapes and sizes. Special applications may require rectangular tanks, horizontal cylinders or spherical tanks. Horizontal cylinders and spheres are generally used for full pressure storage of hydrocarbons or chemicals. However, the most common form is the vertical cylindrical storage tank, whose gross capacity can range from 100 barrels to over 1.5 million barrels in a single tank. The sizes of these tanks range from approximately 10 feet in diameter to over 412 feet in diameter for some of the largest floating roof tanks built in the world.
Main factors causing failure in hydrocarbon storage tanks
Failure modes in hydrocarbon storage tanks can be caused by several factors, including:
Structural failures
- Cracks: Breaks in the tank material that can weaken its structure and cause leaks.
- Deformations: Alterations in the original shape of the tank, such as buckling or buckling, which can affect its structural integrity.
- Collapse: Total failure of the tank resulting in the release of stored product.
Causes of structural failure
- Overloading: Storage of a volume of product in excess of the tank’s maximum capacity.
- Excessive pressures: Increased internal tank pressure due to factors such as product expansion or gas accumulation.
- Impacts: Blows or collisions against the tank by equipment or vehicles.
- Corrosion: Deterioration of the tank material due to chemical reactions with the stored product or the environment.
- Fatigue: Gradual degradation of tank material due to exposure to cyclic loading or vibration.
- Manufacturing defects: Errors in the design or construction of the tank that compromise its structural integrity.
Corrosion failures
Corrosion is a process of gradual deterioration of the tank material due to chemical reactions with the stored product or the environment. The two main types of corrosion that are affected are:
- External corrosion: Caused by environmental factors such as humidity, salinity or the presence of polluting gases in the atmosphere (figure 1-a).
- Internal corrosion: Produced by the contact of the tank material with the stored product, especially if it contains corrosive compounds such as hydrogen sulfide (H2S) (figure 1-b).
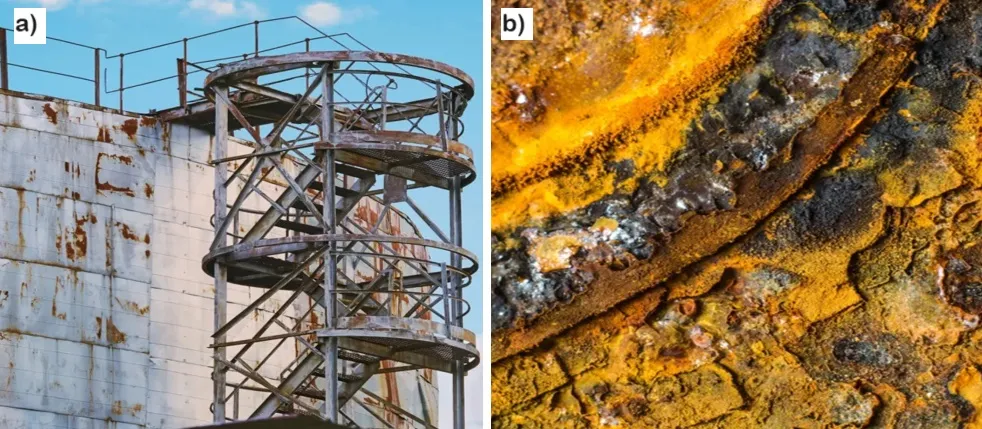
Factors contributing to corrosion
- Type of product stored: Some products, such as sour crude or high sulphur fuels, are more corrosive than others.
- Environmental conditions: Humidity, temperature, salinity, and the presence of polluting gases in the atmosphere accelerate corrosion.
- Corrosion protection: The lack of adequate corrosion protection, such as paint or special coatings, increases the tank’s susceptibility to corrosion.
Operational failures
Operational failures are those caused by human error or inadequate practices in the operation and maintenance of these storage assets. Some examples of operational failures are:
- Overloading: Storing a volume of product in excess of the tank’s maximum capacity.
- Excessively rapid filling and emptying: These operations can generate abrupt changes in pressure and temperature that fatigue the tank material.
- Lack of maintenance: Regular preventive and corrective maintenance is essential for early detection and correction of potential problems that could lead to failures.
- Improper operations: Errors in the operation of valves, metering systems or control equipment can cause spills or explosions.
Explosions and fires
- Accumulation of flammable vapors: Accumulation of flammable vapors in or around the tank can lead to explosions if an ignition source is found.
- Electrostatic discharges: Electrostatic discharges generated during filling or emptying operations may cause sparks and, in the presence of flammable vapors, fires, or explosions.
Failure of secondary containment systems
- Damage to berms and dikes: Secondary containment structures, such as berms and dikes, can fail due to lack of maintenance, inadequate design or physical damage, allowing spills to spread beyond controlled areas.
Difficulties with valves and fittings
- Failures in safety valves: Pressure relief valves and other safety valves can fail due to malfunction or improper maintenance, which can result in overpressure and tank ruptures.
- Leaks in fittings: Connections, hoses and other tank fittings may develop leaks due to wear, improper installation or seal failure.
Failures due to environmental factors
- Impact of climatic factors: Factors such as earthquakes, floods, storms, and extreme temperature changes can affect the integrity of the tank, causing cracks, displacements, and other structural damage.
Types of storage tank failure modes
According to the above, several factors, such as: Environmental (cyclones, hurricanes, earthquakes) and human errors (bad design, faulty construction, inefficient maintenance, loading and unloading maneuvers), cause failures that produce economic losses and can cause fatal accidents to workers near the tanks. Some types of failure forms are shown in the following image.
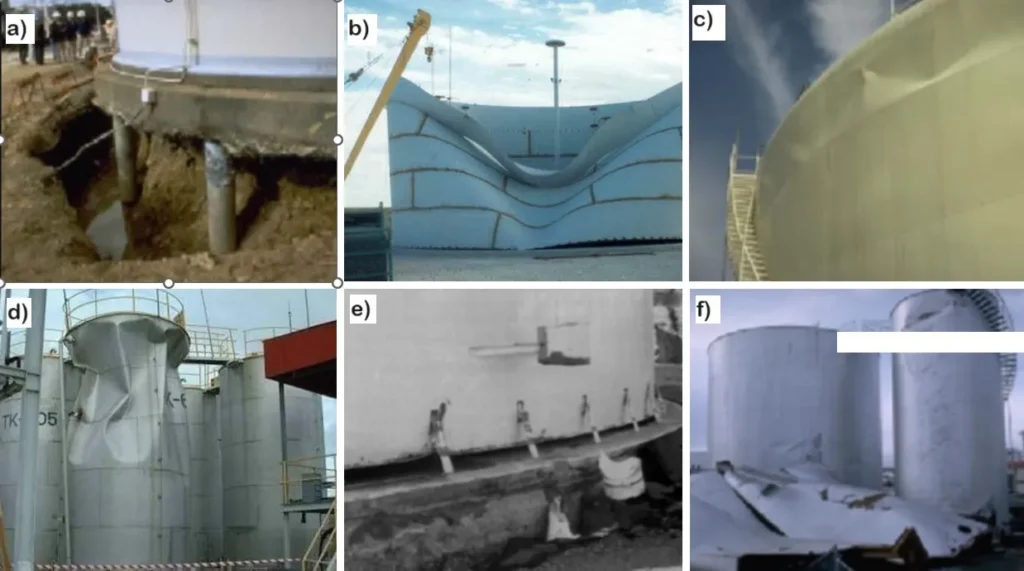
Description of each of the failure modes shown in the image above
a) Buckling Failure: (Failure due to soil settlement), in tanks supported by piles, the failure occurs in the lower part of the tank due to soil settlement, which caused the rupture of the lower or base ring which originated differential settlements in the tank.
b) Structural failure mode: : Structure collapsed by load, in which the lifting of part of the weld between the first level and the bottom of the tank can be appreciated.
c) Collapse in the upper ring of the tank: The effect of the liquid, called “sloshing”, determines the height of the free surface waves and causes damage to the roof and the upper ring of the tank. The liquid moving close to the free surface causes this failure in the last ring of the tank.
d) Tank collapse due to vacuum pressure: Large storage tanks are designed to withstand only a small amount of internal pressure, not vacuum (external pressure on the tank wall). It is possible to collapse a large tank with only a small amount of vacuum.
e) Failure of anchorages by uplift at the base: Failure between the base and the tank wall. This occurs when flammable vapors contained in atmospheric storage tanks explode, dislodging the joint between the bottom plate and the shell. These failures cause the tank to rupture and, in some cases, to be thrown through the air.
f) Collapse failure: According to studies carried out, it is caused by buckling of the walls and lifting of the anchorage. The shear force at the base can cause the tank to fail by sliding. The uplift of the base may cause: (1) rupture of the pipe connections coming out of the tank due to vertical displacements, and (2) rupture of the junction of the base plate with the tank shell.
How to detect failures in these assets
Performing a tank integrity assessment, taking into account a structural evaluation of the main components in the detection of failures, is significant to prevent spills, fires, and other serious incidents. Non Destructive Testing techniques allow a structural evaluation and integrity assessment of tanks without affecting their performance. Some of the most commonly used NDT techniques in these storage assets are:
- Visual inspection: is a simple and effective way to detect early signs of failure, such as cracks, deformation, corrosion or leaks. Regular visual inspections should be performed on both the exterior and interior of the tank until a tank integrity assessment is obtained, paying special attention to the areas most susceptible to failure.
- Ultrasound: This technique uses ultrasonic waves to detect defects in the tank material, such as cracks, porosities or inclusions, and to measure the remaining thickness of the walls, roof, and floor.
- Radiography: Radiography uses different ionic sources to penetrate the tank material and create a radiographic image to detect internal defects. It is mainly used to evaluate welds.
- Magnetic Particle and Liquid Penetrant: This technique is used to detect cracks in ferromagnetic materials, such as stee.
- MFL: It is used for a 100% structural evaluation of the tank floor conditions.
- Vacuum box: They allow to perform inspections of defects in welded joints in tanks, pipes, and many welded structures in a fast and safe way.
- Acoustic Emission: Allows non-intrusive analysis of the condition of in-service tanks, without affecting their operability.
- Measurement of the verticality of the tank: The verticality to detect internal and/or external deformations is determined by plumbing to the vertical construction plane of the tank. The determination of the roundness of the tank allows us to know if there are increases or decreases in the different levels.
Part of this structural evaluation is what is required by API 653 in the inspection, ensuring that it is performed by qualified personnel and complies with the different criteria of this standard when it enters into service and API 650 in its construction/manufacturing.
Here is a video, where you will find a summary of the fundamental aspects of the inspection of storage tanks according to API 653. Source: Codeware.
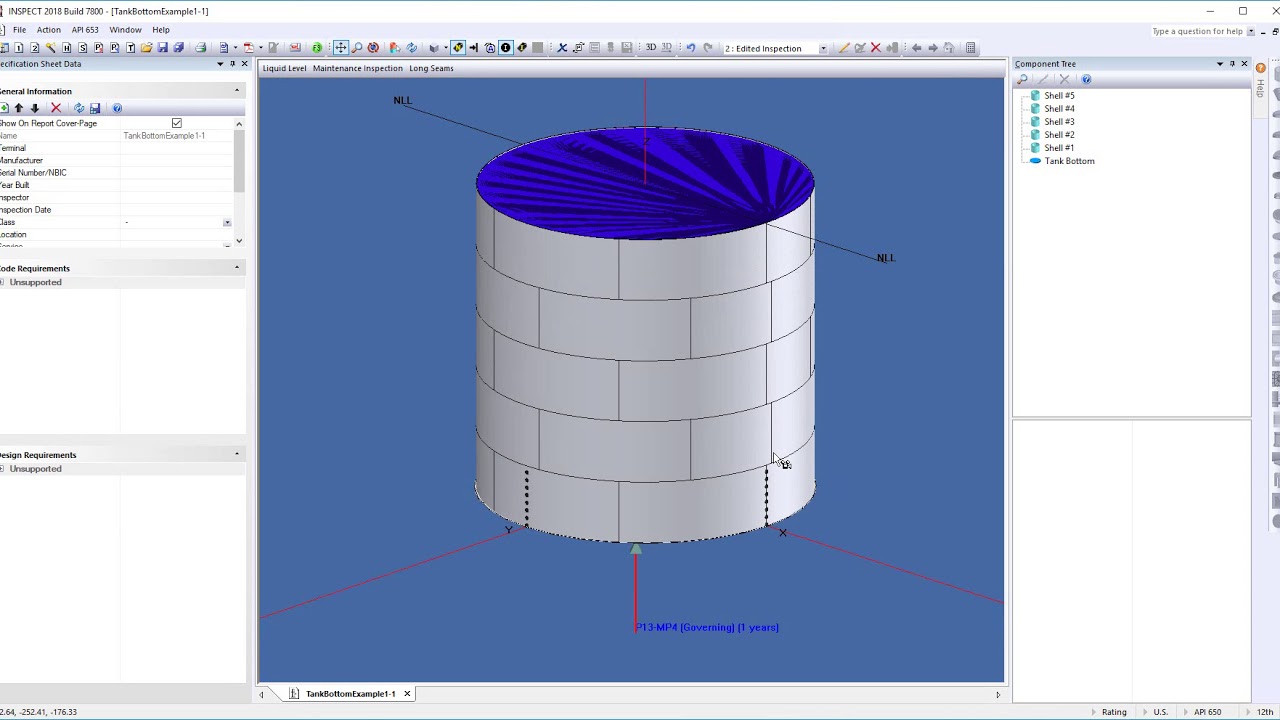
API 653 storage tank evaluations.
Leak detection system
The maintenance of storage tanks is important to prevent failures and protect both the environment and the economic resources of companies. Leak detection systems play a fundamental role in the early identification of possible spills of stored products, allowing a quick and effective intervention.
Among the most common leak detection systems, we find:
- Containment barriers: These barriers are built around the tank to contain any spill in case of failure. They act as a first line of defense, preventing the spilled product from spreading and causing further damage.
- Sump well monitoring: Sump wells are installed under the tank and allow early detection of leaks. By collecting any leaking liquids, these wells make it easier to identify problems before they become major disasters.
- Gas detection sensors: These sensors are crucial for detecting the presence of vapors from stored product in the air. Early detection of vapors can indicate a leak, allowing immediate action to be taken to prevent the problem from escalating.
Maintaining these detection systems in optimal condition is necessary to ensure their effectiveness. Regular maintenance includes the review and testing of each component to ensure proper operation. In addition, it is important to keep detailed records of all maintenance activities and any problems detected and resolved.
Lack of proper maintenance can lead to catastrophic failures, with serious consequences for human health, the environment, and the economy. Spills of stored products can contaminate soil and water, generating clean-up costs and significant fines for the companies responsible.
Investing in regular maintenance of storage tanks and their leak detection systems is an indispensable measure to prevent failures and ensure the safe and efficient operation of facilities. This practice not only protects the environment and resources, but also contributes to the sustainability and reputation of companies.
Conclusions
Proper management of failure modes in hydrocarbon storage tanks is part of effective tank integrity assessment management, fundamental to ensure environmental safety, protection of people and property, and operational efficiency. Early identification and prevention of tank failures are essential to avoid spills, fires, explosions, and other serious incidents.
By implementing inspection programs, efficient structural assessment, monitoring, and proper maintenance, companies can significantly reduce the risk of failure in these storage assets and ensure their safe and reliable operation.
Ensure the integrity of your hydrocarbon storage tanks by implementing effective failure detection and prevention methods!
References
- https://docplayer.es/64566822-Instituto-politecnico-nacional-analisis-estructural-en-la-junta-techo-envolvente-de-tanques-atmosfericos-de-almacenamiento-de-crudo-de-560-barriles.html