Heat treatment is a set of processes in which metals and alloys undergo controlled heating and cooling cycles to modify their mechanical and microstructural properties. In the metallurgical industry, this process is essential to improve hardness, toughness, ductility, and wear resistance, ensuring optimal performance in critical applications.
In sectors like Oil & Gas, where materials are exposed to extreme pressure and temperature conditions, heat treatments play a crucial role in the longevity and safety of equipment such as pipelines, pressure vessels, and valves. Similarly, in materials and mechanical engineering, these processes are used to optimize the characteristics of metals employed in the fabrication of industrial components.
This article will explore the main types of heat treatments, such as quenching, tempering, annealing, and cryogenic treatment, highlighting their applications in improving the mechanical properties of metals and alloys. Key aspects such as heating and cooling rates, phase diagrams, and microstructural changes in materials will also be analyzed.
Heat treatment fundamentals
In heat treatment processes, heating and cooling rates are critical factors that determine the final properties of the material. When a metal or alloy is heated rapidly, its internal structure experiences quick changes affecting its microstructure, such as grain size and phase distribution.
Rapid heating can induce internal stresses, while slower heating allows for a more uniform redistribution of atoms. On the other hand, the cooling rate also plays a vital role; rapid cooling (e.g., in water or oil) can produce a hard martensitic microstructure, while slower cooling results in softer structures such as pearlite or ferrite, with less internal stress.
The phase diagram is a fundamental tool in metallurgy for predicting the behavior of alloys under different temperatures and compositions. It helps select the optimal operating temperatures for each material, ensuring the formation of specific phases that directly influence the mechanical properties. By understanding critical areas of the phase diagram, engineers can avoid the formation of undesirable phases that would compromise the material’s quality. In summary, precise control of these parameters is essential to achieve the desired properties in a heat-treated material.
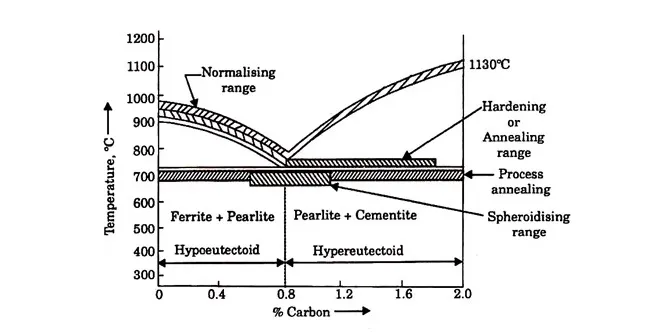
Types of heat treatment
There are several types of heat treatments, each designed to modify the mechanical and microstructural properties of materials, especially metals and alloys. Below are the main types:
Quenching
- Description: The material is heated to a critical temperature and then rapidly cooled, usually in water, oil, or air. This produces a hard and brittle microstructure, such as martensite.
- Application: Improves hardness and wear resistance in components like cutting tools, gears, and parts that require high abrasion resistance.
- Industries: Automotive, heavy machinery, industrial tools, and equipment manufacturing.
Tempering
- Description: A post-quenching process where the material is reheated to a lower temperature and then slowly cooled. This reduces the brittleness induced by quenching, improving toughness.
- Application: Used to balance hardness and toughness, common in heavy machinery parts and components subject to impact or vibration.
- Industries: Automotive, machinery construction, tool manufacturing, and industrial equipment.
Annealing
- Description: The material is heated to a high temperature and then slowly cooled. This relieves internal stresses and improves ductility.
- Application: Facilitates the forming and machining of metals, such as in steel part manufacturing, and restores the material’s workability.
- Industries: Metallurgy, tube and profile manufacturing, sheet and wire processing, and production of metal parts for automotive and appliances.
Normalizing
- Description: Similar to annealing, but with faster air cooling, resulting in a finer and more uniform microstructure.
- Application: Improves the strength and hardness of metals, widely used in structural parts, pipes, and welded components.
- Industries: Construction, pipe manufacturing, energy sectors (nuclear and thermal), and mechanical parts fabrication.
Carburizing
- Description: A process that introduces carbon into the steel’s surface by heating in a carbon-rich environment. This creates a hard and wear-resistant outer layer while maintaining a ductile core.
- Application: Used in components like gears and shafts, where a wear-resistant surface and tough interior are needed.
- Industries: Automotive, industrial machinery, agricultural equipment manufacturing, and power transmission components.
Cryogenic treatment
- Description: The material is cooled to extremely low temperatures, typically using liquid nitrogen, which reduces residual stresses and improves dimensional stability.
- Application: Improves wear resistance and toughness, used in cutting tools, aerospace components, and parts subjected to extreme conditions.
- Industries: Aerospace, defense, precision cutting tool manufacturing, automotive, and medical (surgical instruments).
Austempering
- Description: An isothermal treatment where the material is cooled to an intermediate temperature and held there until a controlled microstructural transformation occurs. This results in a tougher and more ductile structure.
- Application: Improves the toughness and ductility of steels and cast irons, commonly used in springs and automotive parts.
- Industries: Automotive, spring manufacturing, transmission components, and heavy machinery.
Post-weld heat treatment (PWHT)
- Description: PWHT is a process performed after welding to reduce internal stresses caused by the thermal cycle of welding. This heat treatment involves applying controlled heating and cooling cycles, using equipment connected to electrical resistances to precisely heat the weld and heat-affected zones. The goal is to improve mechanical properties such as toughness and ductility, avoiding the brittleness that can result from the welding process.
- Application: PWHT is primarily used in welded components that operate under extreme conditions, such as high-pressure pipelines, pressure vessels, heat exchangers, and other equipment requiring superior structural integrity.
- Industries Oil & Gas: In the manufacture and repair of pipelines, pressure vessels, and other equipment where welds are exposed to high pressures and temperatures..
- Petrochemical: In refineries and chemical plants, where welded equipment is exposed to extreme thermal variations and corrosive substances.
- Energy: In the construction and maintenance of boilers, heat exchangers, and turbines, where weld integrity is crucial to prevent catastrophic failures.
Each of these heat treatments has a distinct impact on the material’s microstructure, optimizing properties like hardness, toughness, wear resistance, and ductility according to the specific application.
Want to learn more about the different heat treatments? Watch the following video courtesy of: James Sword Engineering.
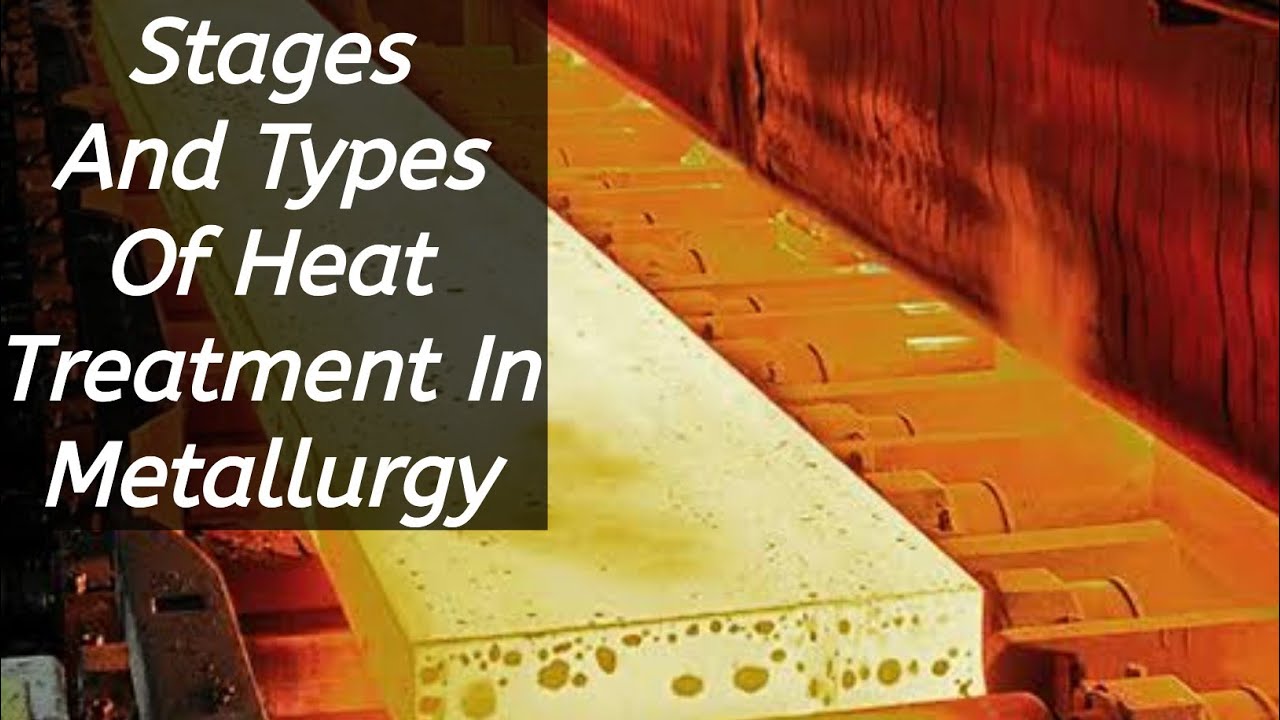
What is the different types of heat treatment in metallurgy?
Mechanical properties and microstructure affected by heat treatment
Heat treatment has a direct impact on two key properties of metallic materials: hardness and toughness. Hardness, which measures a material’s resistance to deformation and wear, significantly increases through processes like quenching, where rapid cooling forms a harder martensitic microstructure.
This is crucial in industrial applications where materials are subjected to constant abrasion or impact, such as in machinery components and cutting tools. However, high hardness often comes at the expense of reduced toughness, which is the ability of the material to absorb energy before fracturing. That’s why processes like tempering are used to balance these two properties, reducing the brittleness induced by quenching and enhancing the material’s ability to withstand impacts without breaking.
The microstructure of metals is intrinsically linked to their mechanical properties. Through heat treatments such as annealing, quenching, and normalizing, microstructural transformations are induced, modifying the material’s behavior under various service conditions. Grain size and shape, phase distribution, and the presence of inclusions are controlled through these processes.
For instance, quenching produces a hard martensitic microstructure, while annealing results in a more balanced microstructure, with larger grains that improve ductility. These microstructural changes allow materials to be adapted to specific application demands, optimizing performance and durability in sectors like Oil & Gas and mechanical engineering.
Applications of heat treatment in industry
In the metallurgical industry, heat treatments are fundamental to the fabrication of critical components used in sectors like Oil & Gas, mechanical engineering, and other industrial fields. For instance, quenching and tempering are employed to enhance wear resistance and hardness in parts like valves, pipes, and machinery components. Annealing and normalizing, on the other hand, are used to relieve internal stresses and improve ductility, which is crucial in manufacturing processes that require forming and machining.
Various metal alloys, such as steel, aluminum, and titanium, significantly benefit from heat treatment. Steel, for example, is widely treated through quenching to increase hardness and wear resistance, making it ideal for use in highly abrasive environments. Aluminum, used in aerospace and automotive components, is heat-treated to improve strength and dimensional stability. Titanium, known for its excellent strength-to-weight ratio, undergoes heat treatment to optimize its toughness and durability, making it indispensable in the aerospace and medical industries.
Practical examples
- Oil & Gas sector: Heat treatments are applied to components subjected to extreme conditions, such as high-pressure pipelines or pressure vessels, to ensure their resistance to fatigue and corrosion.
- Automotive industry: Heat treatment improves the strength of engine components, extending their lifespan under high-stress conditions.
- Aerospace industry: Heat treatments enhance the strength and stability of critical components like engine parts and aircraft structures, which must operate under extreme temperature and pressure conditions.
- Energy sector: Heat treatments ensure the longevity of materials in turbines and generators exposed to high temperatures and corrosion in nuclear and thermal power plants.
- Construction industry: Heat treatments are applied to the manufacture of metal structures that must support heavy loads and endure environmental variations, such as beams and supports.
- Medical industry: Heat treatments ensure that surgical devices and metal prosthetics meet standards of hardness, toughness, and biocompatibility.
Benefits of heat treatment
Heat treatment offers several fundamental benefits that enhance the durability and strength of metallic materials, extending the service life of components and equipment in industrial applications. Processes like quenching and tempering increase wear resistance and improve the material’s ability to withstand high loads and extreme service conditions. This is particularly important in sectors like Oil & Gas, where materials face aggressive conditions of high pressure and elevated temperatures.
Another key benefit is the optimization of mechanical properties. Heat treatment allows for the adjustment of properties such as hardness, toughness, and fatigue resistance so that materials can meet the specific requirements of each application. For instance, tempering reduces the brittleness induced by quenching, balancing hardness and toughness, enabling components to resist impacts and vibrations without breaking.
Additionally, heat treatment, particularly annealing, helps reduce internal stresses that can cause deformation or premature failure in materials. By aligning the material’s microstructure, residual stresses are eliminated, improving dimensional stability and the ability to withstand prolonged loads.
In summary, heat treatment not only improves the material’s capacity to withstand adverse conditions but also optimizes its mechanical properties for specific applications..
The future of heat treatment
Heat treatment remains an essential technology in the manufacturing of metallic materials, but its evolution continues. As the metallurgical industry and other areas such as Oil & Gas and materials engineering face increasingly demanding requirements, advances in heat treatment techniques open new opportunities for improving material performance.
One of the most promising developments is the advancement of cryogenic treatments. These processes involve lowering materials to extremely low temperatures, typically using liquid nitrogen, which allows for microstructural transformation of residual phases and the elimination of internal stresses.
Cryogenic treatments significantly improve the mechanical properties of metals, such as wear resistance, dimensional stability, and thermal fatigue resistance, which is crucial in applications requiring extreme durability. For instance, these treatments are increasingly applied to high-precision components like engine parts, cutting tools, and in the aerospace industry, where material reliability under extreme conditions is paramount.
Moreover, the trend towards advanced materials, such as lightweight alloys and composites, is driving research and development of new heat treatment methods. These materials, used in high-tech sectors like aerospace, defense, and energy, present unique challenges regarding thermal processing. Advances in microstructure control and the implementation of hybrid thermal processes, which combine several stages of precise heating and cooling, allow for the optimization of these materials’ properties for more specialized applications.
Advanced thermal simulation techniques are also revolutionizing the way heat treatments are applied. By using software and simulation tools, engineers can more accurately predict the microstructural and mechanical changes that will occur during the process, allowing for greater control over the final outcome. This not only reduces costs and production time but also improves the quality and consistency of the final products.
Conclusion
Heat treatment is a process applied in order to improve the mechanical and microstructural properties of metallic materials, ensuring their performance under extreme conditions. As the industry moves forward, innovations in thermal techniques and the development of advanced materials present new opportunities to further improve component performance. In this context of technological evolution, it is vital that industry professionals explore how to apply these advances to optimise their processes and improve the efficiency of their operations.
Consider adopting the right heat treatment to maximise the benefits and ensure the durability of your materials and equipment.
References
Own source