Introduction
Today’s metallurgy is evolving towards more environmentally responsible models, facing challenges to maintain industrial efficiency, align with sustainability principles and reduce environmental impact; in this context it is important to analyze how metallurgy contributes to industrial sustainability through the use of innovative materials1.
This approach is limited to a specific stage of the process, and covers the entire life cycle of the metal: from ore extraction and refining, to processing, responsible use and recycling. Its aim is clear: to reduce greenhouse gas emissions, minimize water and energy use, and reduce toxic waste and environmental pollution.
The goal is to provide a comprehensive view of how these advances positively impact the green economy and operational efficiency of modern industry.
What is green metallurgy?
Green metallurgy is a technical and ethical response to the environmental challenges facing the modern metallurgical industry. It is defined as a set of practices, technologies and approaches aimed at the production and transformation of metals with the lowest possible environmental impact, while promoting the conservation of natural resources.
It is an evolution of traditional metal processing, focused on minimizing environmental impact, based on principles such as energy efficiency, the reduction of polluting emissions and the use of metal waste. In addition, sustainable metallurgy also includes the responsible use of metals in products and the ability to recycle them at the end of their useful life. The following image shows a representative illustration of the concept of green metallurgy in environmental sustainability.
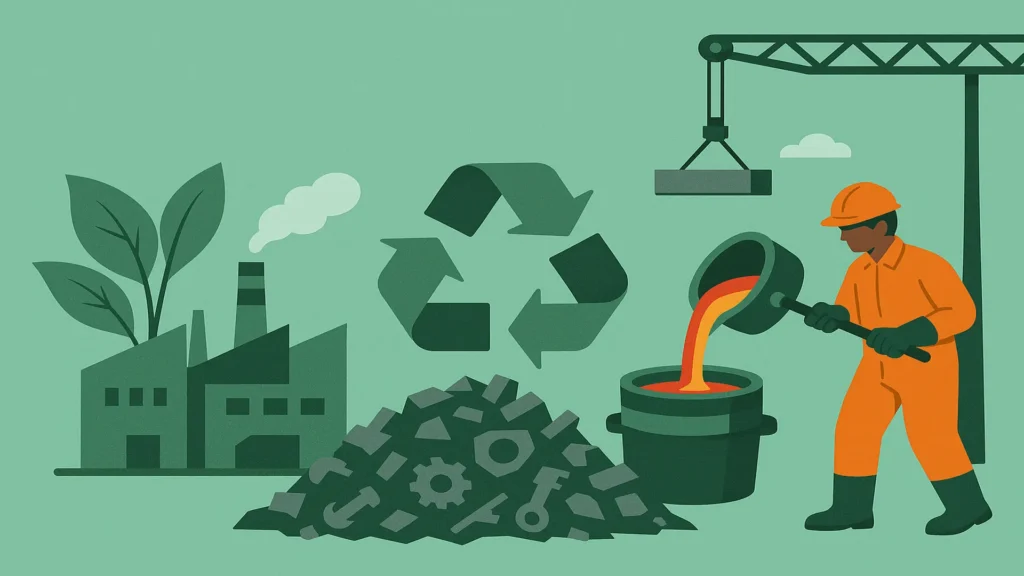
This approach seeks to replace hazardous reagents, reduce fossil fuel consumption and promote the circular economy within the industrial sector.
Sustainable processes in metallurgy
Hydrometallurgy: a key tool for sustainable metallurgy
In the context of the transition to more environmentally friendly industrial practices, hydrometallurgy is an efficient and sustainable alternative to traditional methods of metal extraction and processing. This process, which uses aqueous solutions to recover valuable metals from ores, concentrates or recycled materials, significantly reduces energy consumption and pollutant emissions compared to conventional pyro-metallurgy.
In addition, hydrometallurgy facilitates the use of secondary raw materials, such as electronic waste or industrial slag, which contributes to a circular economy in the metallurgical sector. Operating at low temperatures and with less environmental impact, this approach is consolidating as a strategic tool in the search for a cleaner, more efficient metallurgy aligned with the principles of sustainable development.
Metal recycling: Key to a circular industry
Recycling enables the recovery of critical materials such as aluminum, copper, steel and rare earths with lower energy costs compared to primary extraction. Techniques such as density separation, clean smelting and electrochemical purification ensure the quality of recycled materials2. However, there are still challenges related to cross-contamination and efficiency in the recovery of less common metals.
Innovative materials for more sustainable manufacturing
Currently, alloys have been synthesized that require less energy to produce or that can be more easily recycled. Similarly, solid-state metallurgy techniques, such as plasma sintering, are being developed that consume less energy than traditional methods.
These innovations, still in the pilot or industrial scale-up phase, represent a decisive step towards a cleaner metallurgy aligned with sustainable development objectives. While the technological and economic challenges are considerable, regulatory pressure, market demand and scientific advances are strongly driving this transformation.
In addition to high-strength alloys such as duplex stainless steel, which combines corrosion resistance and good weldability, the synthesis of fiber-reinforced composite materials is also being investigated, especially for applications with specific mechanical requirements. Where weight reduction contributes to energy savings in transportation and installation. All these materials extend the service life of equipment and contribute to the objectives of sustainable manufacturing.
What innovations are driving green metallurgy?
The metallurgical industry, historically associated with intensive energy consumption and the generation of large volumes of emissions, is now facing a turning point. The context of climate emergency, stricter regulations and increasing pressure from the market have forced it to rethink its fundamentals. From this need arises green metallurgy, a set of technologies and approaches aimed at reducing the environmental impact of metallurgical processes along the entire value chain.
In this transformation scenario, several innovations are playing a key role. Some are already in the industrial implementation phase, while others are rapidly advancing from applied research to commercial viability. The following are the main technologies that are redefining sustainable metallurgy:
1. Substitution of coke with green hydrogen
The use of green hydrogen as a reducing agent in the production of metals – especially in the production of steel from iron ore – represents one of the major advances towards carbon-free metallurgy. Traditionally, coke acts as a reducing agent, emitting large amounts of CO₂. In contrast, hydrogen, when produced from renewable sources, reacts with the oxygen in the ore, generating water vapor as the only byproduct.
Projects such as HYBRIT and H2GreenSteel, both in Sweden, are demonstrating that this technology is technically feasible and commercially promising. Although production costs are still high, cheaper electrolysis and the development of hydrogen infrastructures are expected to accelerate its global adoption.
2. Electrification of thermal processes
Electrification of furnaces and reactors in metallurgy represents a significant process in environmental decarbonization, replacing fossil fuels with renewable electricity. Technologies such as electric arc, induction melting and resistance furnaces make it possible to precisely control temperatures, increase energy efficiency and reduce emissions.
Moreover, in advanced pyrometallurgical processes, such as the electrolytic reduction of aluminum or the extraction of metals from slag, electric power can replace the heat generated by combustion, closing the cycle with a clean energy matrix.
3. Recycling and circular economy
Efficient metal recycling reduces the consumption of natural resources and drastically reduces the emissions associated with extraction and primary processing. In this context, advanced recycling technologies are emerging, such as:
- Automated sorting with spectral sensors
- Intelligent AI-assisted separation
- Optimized flotation techniques for complex metals
Through the appropriate use of these technologies, it is possible to recover materials with greater purity, minimize losses and manage complex waste such as electronic scrap or mixed alloys. The traceability of materials, driven by digital platforms, is also key to closing the production cycle within a circular metallurgical economy.
4. Use of biomass and industrial waste as inputs
Emerging lines of research propose the use of biomass and organic waste as alternative reductants to coke, taking advantage of their renewable carbon content. Although they do not yet reach the thermal efficiency of coal, certain mixtures – such as heat-treated biomass pellets – show good results in laboratory tests and pilot plants.
At the same time, industrial wastes such as sludge, slag and agricultural residues are being valorized and integrated as secondary inputs, reducing the volume of waste and improving the overall efficiency of the process.
5. Digitization, automation and artificial intelligence
Digitization is revolutionizing the way metallurgical plants are operated. Through the use of intelligent sensors, predictive models, big data and digital twins, it is possible:
- Real-time monitoring of critical process variables
- Automatically adjust parameters to maximize efficiency
- Predict failures or deviations before they occur
- Reduce energy consumption and waste generation
In addition, artificial intelligence can identify patterns in large volumes of data to optimize recycling logistics, design more sustainable alloys and plan predictive maintenance.
6. Emerging low-impact processes
New metallurgical processes that operate at low temperatures, with fewer intermediate steps and lower energy consumption are under development, such as:
- Spark Sintering (SPS)
- Powder Metallurgy
- Ionic Liquid Extraction
- Solid State Extractive Metallurgy
These methods, together with additive manufacturing (3D printing of metals), make it possible to reduce emissions and design metal components with greater efficiency in the use of raw materials.
Importance of sustainable metallurgy in modern industry
Green metallurgy, understood as the set of technologies and practices aimed at reducing the environmental impact associated with the production and transformation of metals, represents a strategic point in the transition to a more sustainable and circular metallurgical industry. It is aligned with the principles of energy efficiency, decarbonization, and resource conservation.
This discipline constitutes an environmental adaptation of traditional metallurgy, and an integral reformulation of pyrometallurgical, hydrometallurgical and electrometallurgical processes under criteria of technical, economic and ecological sustainability.
Reducing the environmental footprint of extractive and refining processes
The primary extraction of metals from ores traditionally involves high energy consumption and significant greenhouse gas (GHG) emissions, especially in operations involving carbothermal reduction, such as blast furnace steel production or copper smelting. Green metallurgy proposes the substitution of fossil reducing agents with renewable sources or alternative technologies, such as:
- Use of green hydrogen as a reductant instead of metallurgical coke, which eliminates CO₂ emissions by direct reaction.
- Electrical energy from renewable sources in electrometallurgical processes, such as aluminum electrolysis, allowing the energy intensity of the final product to be reduced.
- Selective leaching technologies with biodegradable reagents instead of aggressive mineral acids, minimizing toxic effluents and improving trace element recovery.
Metal recycling as the backbone of the circular economy
In the context of progressive depletion of high-grade mineral reserves and rising extraction costs, post-consumer and post-industrial metal recycling is positioned as a strategic alternative. Secondary metallurgy allows:
- Reductions of more than 90% in energy consumption compared to primary production (case of recycled aluminum versus primary aluminum).
- Revaluation of scrap metal using electric arc furnaces, rotary furnaces or induction melting technologies.
- Efficient recovery of critical metals and rare earths from electronic waste, lithium-ion batteries or industrial catalysts through advanced hydrometallurgical processes.
Sustainable metallurgical process design
Process design under the green metallurgy paradigm involves a holistic integration of principles such as:
- Minimization of solid, liquid and gaseous waste through zero waste schemes.
- Implementation of waste heat recovery and cogeneration systems in metallurgical plants.
- Use of metallurgical by-products such as slag, dust or sludge for applications in cement plants, construction or soil stabilization, promoting industrial symbiosis.
Innovation and technical standards
The development of new metallic materials with better mechanical and thermal performance, but with a lower associated environmental footprint, as well as the standardization of metallurgical sustainability indicators (e.g. carbon footprint per ton of metal produced), are key aspects for traceability and global competitiveness. Certifications such as ISO 14001, ESG (Environmental, Social and Governance) frameworks and the mining sustainability guidelines promoted by the ICMM (International Council on Mining and Metals) reinforce the industry’s regulatory commitment to responsible metallurgical practices.
Conclusions
The transformation to green metallurgy is not an abstract concept, but an evolving reality. The innovations described above are setting the course towards cleaner, safer and more efficient processes, in which respect for the environment is not an obstacle, but an opportunity for technological and competitive improvement. Although the challenges of scaling up, investment and regulatory adaptation still persist, the industry’s commitment, together with scientific progress and social pressure, are pushing metallurgy into a new era: an era where industrial progress and environmental balance can and must go hand in hand.
Green metallurgy is a structural necessity for a resilient, competitive and environmentally responsible industry. Change is afoot, and those who embrace sustainability will lead the next era of metallurgical transformation. Adopting green metallurgy practices reduces carbon footprint, reduces toxic waste and enables compliance with stricter environmental regulations. It also strengthens corporate image and reduces long-term operating costs, especially in contexts where energy is a critical factor
Sustainable metallurgy represents a technical response to today’s environmental challenges, and a structural transformation for the modern metallurgical sector. Its effective implementation makes it possible to significantly reduce the ecological impact of metal production, optimize resources through recycling and close material cycles in an increasingly regulated, demanding and sustainability-oriented industrial environment. In short, it is the strategic way to ensure the operational and ethical viability of metallurgy in the 21st century.
References
- “Green steel: Achieving sustainable steelmaking requires small steps and big leaps”; Nature & Biodiversity, 6 July 2023.