Introduction
Galvanic reaction is a fundamental electrochemical phenomenon that occurs when two metals with different electrochemical potentials come into electrical contact in the presence of an electrolyte. This process, also known as galvanic or bimetallic corrosion, has critical implications in engineering, industry and the design of metallic systems, especially those exposed to wet, marine or subway environments. Understanding its principles is essential to prevent structural failure, ensure material integrity and extend the life of metallic assets.
In practice, galvanic reaction can trigger anything from small material losses to costly failures in key infrastructure such as buried pipelines, welded joints, storage tanks or offshore structures. Mastering this phenomenon is therefore not only an academic necessity, but a technical and economic imperative in the most demanding industrial sectors.
What is a galvanic reaction?
A galvanic reaction (also known as galvanic corrosion) occurs when two metals with different electrochemical potentials are in direct electrical contact and immersed in the same conductive medium, such as seawater, soil moisture or atmospheric condensation. In this context, a galvanic cell is formed, where one of the metals acts as an anode (corrodes) and the other as a cathode (is protected)1.
Electrochemical fundamentals
The basis of this phenomenon lies in the concept of standard electrode potential. When two metals are connected:
- The less noble (more active) metal gives up electrons: it oxidizes and acts as an anode.
- The more noble (more passive) metal receives electrons: it is reduced and acts as a cathode.
The flow of electrons between the metals through their electrical connection drives the corrosion process. The greater the potential difference between the two materials, the more intense the galvanic current and, therefore, the higher the corrosion rate of the anode2.
To illustrate the principles of the galvanic reaction, a classical galvanic cell consisting of zinc and copper can be considered. In this system:
- Zinc (Zn) acts as an anode, oxidizing according to the half-reaction: Zn(ac)2++2e−→ E0=−0.7618 V
- Copper (Cu) acts as cathode, reducing the copper ions according to the half-reaction: Cu(ac)2++2e-→Cu(s) → E0=+0.340 V
- The electromotive force (fem) of the cell is the difference between the two potentials: Cell=Ecathode-Eanode=0.340 V-(-0.7618 V)=1.1018 V
Each of the half-reactions occurs in different compartments called half-cells. One consists of a Cu film immersed in a CuSO4 solution and the other of a Zn film immersed in a ZnSO4 solution. The Zn and Cu sheets are called electrodes and are connected by an electrical conductor, forming a galvanic couple, as shown in figure 1.
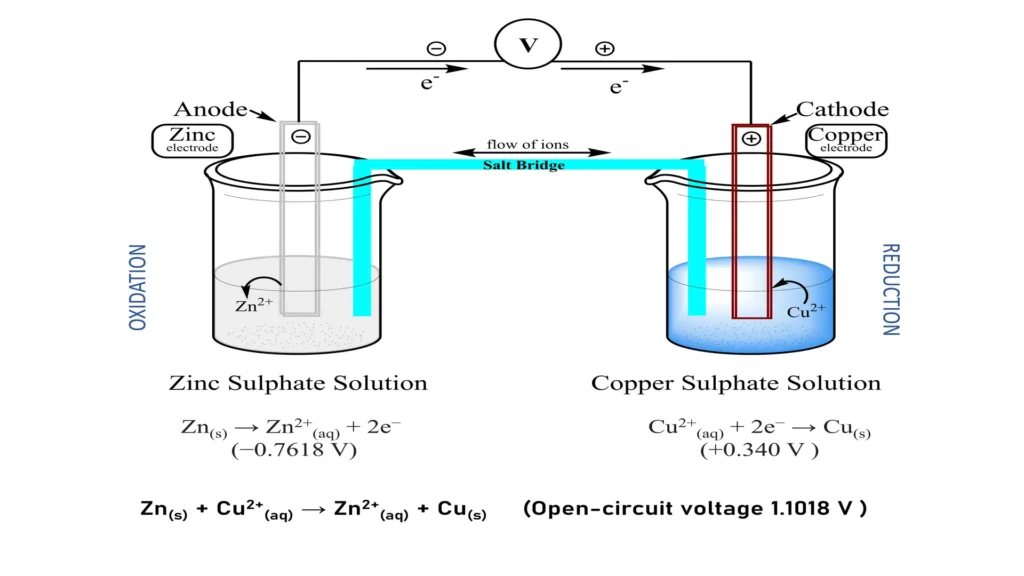
The half-reactions as presented in the picture above (figure 1) occur spontaneously. On the contrary, if metallic Cu is added to a zinc sulfate solution, no reaction occurs because the metallic Cu is not oxidized by the Zn++. The ease of oxidation of metals depends on their standard potential, according to the galvanic series of standard reduction or oxidation potentials.
Implications of the galvanic reaction on metallic materials
This interaction has negative implications, such as accelerated corrosion known as galvanic corrosion, and positive implications when applied to the protection of metallic structures. In this context, its study is fundamental in materials engineering and corrosion protection in industrial applications.
1. Negative implications: Galvanic corrosion
Galvanic reaction can have a significant impact on material and structural integrity. The occurrence of this reaction between dissimilar metallic material systems in an electrolyte medium accelerates the corrosion process of one of the metals, known as galvanic corrosion, due to the electronic transfer (electric current) between the two metals; leading to structural failure and degradation of materials, functional damage to metallic components, weakening materials, affecting the integrity of structures and equipment; it can also compromise the safety and durability of materials in construction, industry, and transport. Preventing this phenomenon is key to preserving the efficiency and lifetime of metallic materials.
2. Positive implications: Cathodic protection by sacrificial anodes
Although it seems contradictory, the galvanic reaction can contribute to the preservation of materials. This electrochemical mechanism is used in cathodic protection by sacrificial anodes, where highly active metals (with a greater tendency to corrode), such as zinc, aluminum or magnesium, are coupled to steel structures or other less reactive (more noble) metals. In this process, in this case the more active material acts as an anode and corrodes instead of the metal to be protected, mitigating corrosion and extending the life of the structure. This system is applied on ships, offshore platforms, storage tanks and buried pipelines, providing an effective defense against metal degradation.
Galvanic corrosion
What is galvanic corrosion?
Galvanic corrosion, also called bimetallic corrosion, is an electrochemical phenomenon that occurs when two metals of different electrochemical potential are in direct contact within a conductive medium or electrolyte. The potential difference between the two metals generates a transfer of electrons, thus establishing a galvanic cell in which the less noble metal acts as the anode and undergoes an accelerated dissolution process. The more noble metal becomes the cathode, favoring reduction reactions that limit its degradation. In the following image (Figure 2), a graphic representation of the electrochemical process of this type of corrosion is shown.
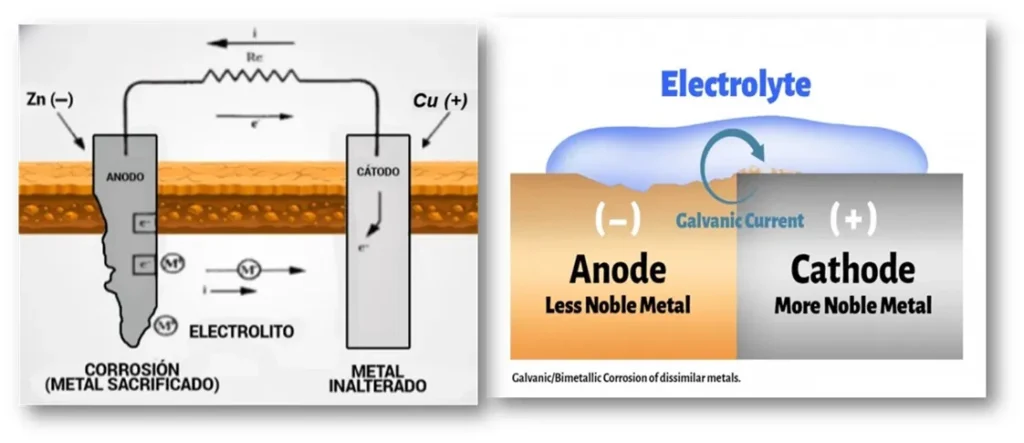
The electrochemical process involved is driven by the difference in electrode potentials between the two metals, where the metal of higher potential represents the cathode, and the metal of lower potential is the anode. Electrons flow from the anode to the cathode through the electrical connection, while ions move through the electrolyte, closing the electrical circuit.
Galvanic series or electromotive force series
The galvanic series is a classification of metals and alloys according to their electrochemical potential in a specific medium (Table 1), and is a fundamental concept for understanding galvanic corrosion. Metals at the bottom of the series, such as magnesium and zinc, are more anodic and prone to corrosion, while those at the top, such as gold and platinum, are more cathodic and corrosion resistant.
Table of standard reduction potentials (V) at 25 °C
Metal / Electrode | Standard Potential (V) |
Litio (Li⁺/Li) | -3.040 |
Magnesio (Mg²⁺/Mg) | -2.370 |
Zinc (Zn²⁺/Zn) | -0.7618 |
Hierro (Fe²⁺/Fe) | -0.440 |
Níquel (Ni²⁺/Ni) | -0.250 |
Hidrógeno (H⁺/H₂) | 0.000 (referencia) |
Cobre (Cu²⁺/Cu) | +0.340 |
Plata (Ag⁺/Ag) | +0.799 |
Oro (Au³⁺/Au) | +1.498 |
The more negative the potential, the greater the tendency of the metal to oxidize (behave as an anode).
How is the galvanic series related to the corrosion of metals?
The galvanic series helps to predict the behavior of metals at different galvanic potentials according to the position they occupy in the galvanic table or electromotive force series, when they are in contact in the presence of an electrolyte. The potential difference between the metals in the galvanic series determines the speed and severity of the corrosive attack, the greater the separation in the series, the more intense the corrosion of the anode.
Figure 3, shows a representative image of the galvanic corrosion process between steel and copper3. In this interaction, the less noble metal (anode) corrodes faster, while the more noble metal (cathode) is protected. Representation of galvanic corrosion between two dissimilar metals: the steel (less noble) acts as an anode and corrodes, while the copper (more noble) remains protected. This type of galvanic couple can be found in buried structures, pipes or metal joints exposed to electrolytes such as ground water or salt water.
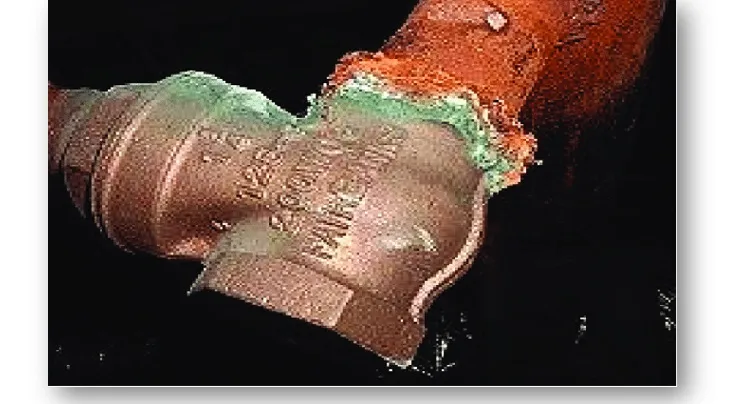
This principle is significant in the design of metallic structures, selection of compatible materials and application of protection methods, such as cathodic protection with sacrificial anodes. Understanding this electrochemical mechanism in corrosion engineering is important to avoid this type of corrosion by means of the most appropriate control methods.
Factors affecting the severity of galvanic corrosion
- The voltage difference between the two metals in the galvanic series: This is the main factor with the greatest impact on the acceleration of the corrosion rate; a greater difference generally leads to faster corrosion.
- The nature and aggressiveness of the medium: The environment also plays a significant role; the presence of the electrolyte is to facilitate the flow of ions between the anode and cathode, completing the electrochemical circuit. The conductivity of the electrolyte, influenced by its composition and temperature, affects the corrosion rate, for example, the presence of chloride ions in seawater can accelerate galvanic corrosion.
- Anode/Cathode area ratio: An important consideration is the area ratio of the contact zone between the materials, which is another critical factor; a small anode area in relation to the cathode can lead to severe corrosion. The higher the ratio of anode to cathode, the faster the corrosion process occurs.
How to avoid galvanic corrosion?
Galvanic corrosion is a phenomenon that can be avoided or mitigated by taking appropriate measures to prevent interaction between dissimilar metals and exposure to an electrolyte.
- Selection of compatible materials: Choose metals that are close in the galvanic series or that have a low electrochemical potential.
- Protective coatings: Applying protective coatings, such as paints, varnishes or zinc coatings, to metals can provide a barrier between the metals and the electrolyte, thus reducing the possibility of galvanic corrosion.
- Electrical insulation: If possible, non-conductive materials, such as plastics or rubbers, can be used to electrically insulate metals that could come into contact. This prevents electron transfer and reduces corrosion.
- Corrosion inhibitors: Chemical corrosion inhibitors can be used to reduce the rate of galvanic corrosion. These chemicals are applied to the surface of metals and form a protective layer.
- Use sacrificial metals: In some cases, sacrificial metals that are more active than the parent metal can be used. These metals will preferentially corrode instead of the parent metal. For example, in marine applications, zinc or aluminum anodes are used to protect steel structures.
- Physical separation: Physically separating metals with insulators or non-conductive gaskets can prevent direct contact between them and thus reduce galvanic corrosion. Washers of other material, in joints of various metals, is a clear example of physical separation to prevent galvanic corrosion.
- Engineering design: Designing components and structures so that water and moisture do not accumulate or become trapped between metals in contact can help reduce galvanic corrosion.
- Monitoring and maintenance: Performing regular monitoring and preventive maintenance can help detect and address corrosion problems. It is important to keep in mind that prevention of galvanic corrosion is critical in applications where corrosion can have serious consequences, such as in the marine industry or in metallic structures exposed to the environment. The appropriate choice depends on the specific application and the nature of the materials involved.
Conclusion: importance of galvanic reaction in metal design and protection
Galvanic reaction is a key phenomenon in the degradation of metallic structures, especially when dissimilar materials are combined in conductive environments. Understanding its fundamentals – such as the potential difference between metals, the galvanic series, the relationship between anodic and cathodic areas, and electrolyte conditions – is critical to preventing accelerated corrosion.
From materials engineering to critical infrastructure protection, the analysis and control of galvanic corrosion allows strategic decisions to be made in the design, material selection and implementation of cathodic protection systems or coatings. Integrating this technical knowledge in early project phases reduces premature failures and optimizes the useful life of industrial assets.
Anticipating galvanic corrosion requires understanding its mechanisms and applying control measures at the design stage.
References
- https://en.wikipedia.org/wiki/Redox
- Bockris, J. O’M., & Reddy, A. K. N. (1970). Modern Electrochemistry. Springer.
- Introduction to corrosion and corrosion inhibitors”; Materials Science, Engineering, 2015.