Table of Contents
- What is FRP coating?
- Role of resin and fiber in FRP coatings
- Benefits and importance of FRP coating
- Selection of FRP coatings
- Resin types and fiber applications
- Industrial applications of FRP coating
- Surface preparation
- FRP application methods
- Curing and final protection
- Technological innovations in FRP liners
- Safety and environmental aspects of FRP coating application
- Conclusion
- References
Fiber-reinforced polymers (FRP) are composite materials widely used in various industries due to their high mechanical strength, durability and corrosion resistance. Its application is very common in sectors such as construction, shipbuilding, automotive, hydrocarbon and aerospace, among others, where FRP has allowed the development of lighter and stronger structures that have optimized production processes. Its use in tank coatings provides a durable and reliable barrier that prolongs their useful life, minimizing maintenance costs and operating risks.
In this article, we will explore in detail the concept, characteristics, manufacturing, applications and advantages of FRP coating.
What is FRP coating?
A composite material consisting of a polymeric matrix, generally thermosetting resins such as epoxy, polyester or vinylester, reinforced with high-performance fibers such as glass, carbon, basalt or aramid. The combination of these two materials results in a composite with mechanical properties superior to those of the individual materials.
Role of resin and fiber in FRP coatings
In an FRP system, resin and fiber play complementary roles such as the following:
Fiber: Adds strength and durability, reinforcing the structural component of FRP and contributing:
- Mechanical resistance to loads and stresses.
- Dimensional stability, avoiding deformations under extreme conditions.
- Durability against impacts, high temperatures and aggressive chemical agents.
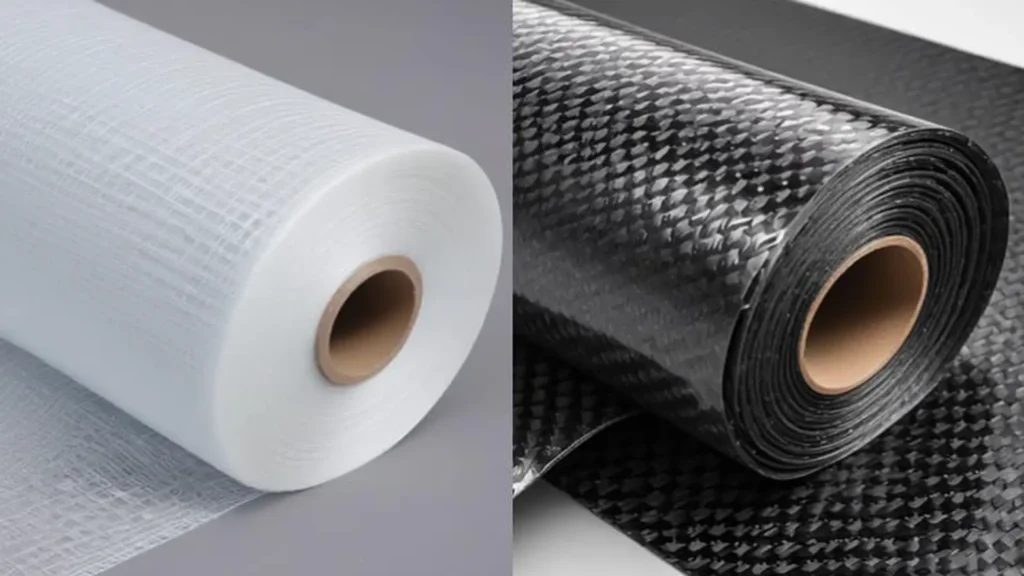
Resin: Gives protection and cohesion, acting as the matrix of the composite, joining the fibers and providing:
- Chemical protection against corrosive agents.
- Waterproofing to prevent liquid absorption.
- Structural adhesion between fibers.
- Thermal resistance according to the type of resin used.
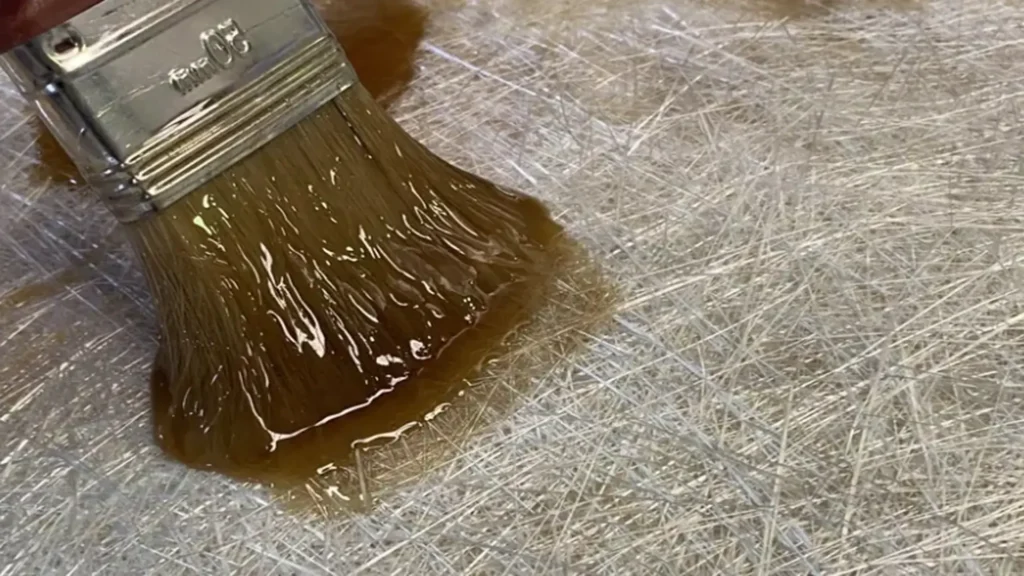
Benefits and importance of FRP coating
- Corrosion protection: Thanks to their chemical composition, FRP tank coatings resist corrosion caused by aggressive chemicals, reducing the risk of leaks and structural failure.
- Lightweight and high strength: Fiber and resin provide a lightweight, yet structurally strong material, facilitating installation and reducing operating costs. Its high resistance to chemical and mechanical agents makes it an ideal coating alternative to protect traditional materials such as carbon steel.
- Durability: Unlike steel, which requires frequent corrosion treatments, FRP coatings can last for several decades with minimal maintenance, resulting in increased operational efficiency and reduced long-term costs.
- Adaptability: They can be applied to a wide variety of industrial storage tanks, from those used in the chemical industry to those for food products.
Selection of FRP coatings
Performance is determined by the proper selection of the resin, the reinforcing fiber and its compatibility with the operating conditions, so the following should be considered:
- Chemical compatibility: Ensure that it is compatible with the products being stored to avoid chemical reactions that compromise their integrity.
- Service temperature and factors affecting thermal resistance: The thermal performance of FRP coatings can be affected by several factors:
- Duration of exposure: An FRP can withstand extreme temperatures for short periods, but prolonged exposure accelerates the degradation of the material.
- Mechanical loading and pressure: Tanks subjected to high loads may have their thermal resistance reduced due to additional mechanical stresses.
- Environmental conditions: Factors such as humidity, UV radiation and the presence of aggressive substances can affect the durability of FRP.
- Coating thickness: Determined according to the severity of the environment and safety regulations.
- Regulations and certifications: Materials must be verified to meet industry standards such as ASTM, ISO, API, ensuring their quality and performance.
Resin types and fiber applications
The choice of resin and fiber should consider the chemical and mechanical environment in which it will operate. A guide to strength and application is given in the following tables:
Types of resin and their applications
Resin type | Chemical resistance | Mechanical resistance | Applications |
Polyester | Moderate | Low | Less demanding conditions. Low cost. |
Viniéster | High | Medium | Improves chemical and thermal resistance. Ideal for corrosive environments. |
Epoxi | Excellent | High | Extreme environments with high mechanical loads and intense chemical exposure. |
Types of fibers and their applications
Fiber type | Chemical resistance | Mechanical resistance | Applications |
Fiberglass Type E | Good | Good | General use with good cost-benefit ratio. |
Fiberglass Type E-CR | Good | High (Acid and corrosion resistance) | Application in highly corrosive environments. |
Fiberglass Type S | High | Moderate | Application in high mechanical demands |
Carbon fiber | Excellent | Excellent | High fatigue strength, low density and thermal stability |
Basalt fiber | High | High | Alternative to fiberglass with better thermal resistance |
Aramid Fiber (Kevlar) | Very high (impact resistance) | Moderate | Applications in aggressive and high impact environments. |
Industrial applications of FRP coating
FRP coatings are used in multiple sectors, including:
- Chemical industry: Storage of acids and highly corrosive substances.
- Oil industry: It is used for the protection of hydrocarbon and derivative tanks. It should be considered that, in floating roof tanks, the static current from the roofs is discharged to ground through the tank wall, but when FRP is installed on the inside of the tank wall, the insulating characteristic of this product prevents this dissipation. An alternate static current discharge system should be designed as a precautionary measure to prevent fire.
- Food industry: Safeguarding of products sensitive to metal contamination.
- Water treatment: Lining of potable water and wastewater tanks.
Surface preparation
Before applying an FRP coating, it is essential to prepare the surface to ensure proper adhesion:
- Cleaning: Removal of dust, grease, rust and contaminants.
- Roughness: In metals, sandblasting is recommended to improve adhesion.
- Drying: Surfaces must be completely dry before application.
FRP application methods
Hand lay-up
- The surface is prepared by cleaning and removing impurities.
- A layer of resin is applied with brushes or rollers.
- Fiberglass or reinforcement sheets are placed manually.
- It is impregnated again with resin and the trapped air is removed with a roller.
- It is left to cure until it reaches the required hardness.
- Advantages: Low cost, easy application on large surfaces.
- Disadvantages: Depends on the skill of the operator and can generate variations in thickness.
Spray-up projection
- Spray equipment is used to simultaneously apply resin and chopped fiberglass.
- It is compacted with rollers to improve adhesion and eliminate air bubbles.
- It is left to cure at room temperature or with accelerators.
- Advantages: Higher application speed, ideal for large surfaces.
- Disadvantages: Less control over fiber distribution, which may affect mechanical strength.
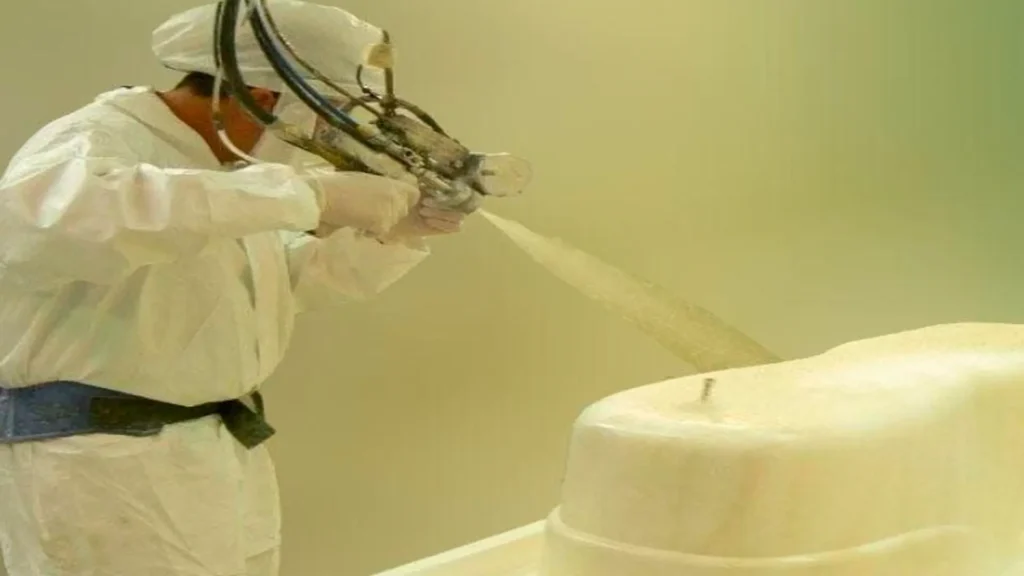
Vacuum Infusion Molding (VIM)
- The dry reinforcement is placed in the mold or surface to be coated.
- It is sealed with a vacuum bag and connected to a resin injection system.
- The resin is absorbed uniformly by the vacuum, eliminating air bubbles.
- It is cured under vacuum until the final strength is reached.
- Advantages: Improves mechanical strength and reduces porosity.
- Disadvantages: Requires specialized equipment and longer preparation time.
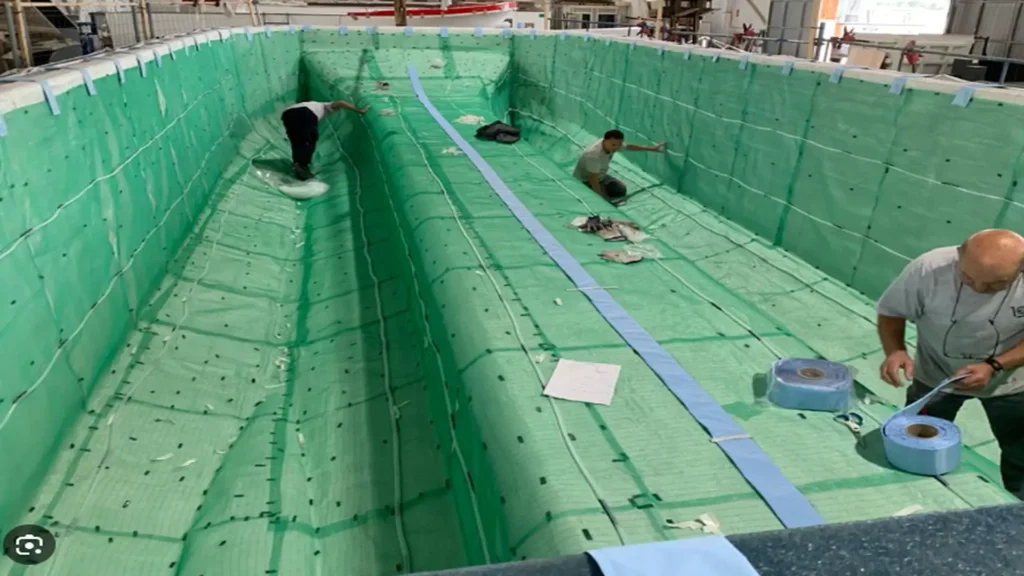
Filament winding
- Continuous fiber yarns are immersed in resin.
- They are wound on a rotating mandrel with a specific pattern.
- It is cured in an oven or with UV radiation to harden the material.
- Advantages: High mechanical strength and precise thickness control.
- Disadvantages: Only applicable to cylindrical parts such as pipes and tanks.
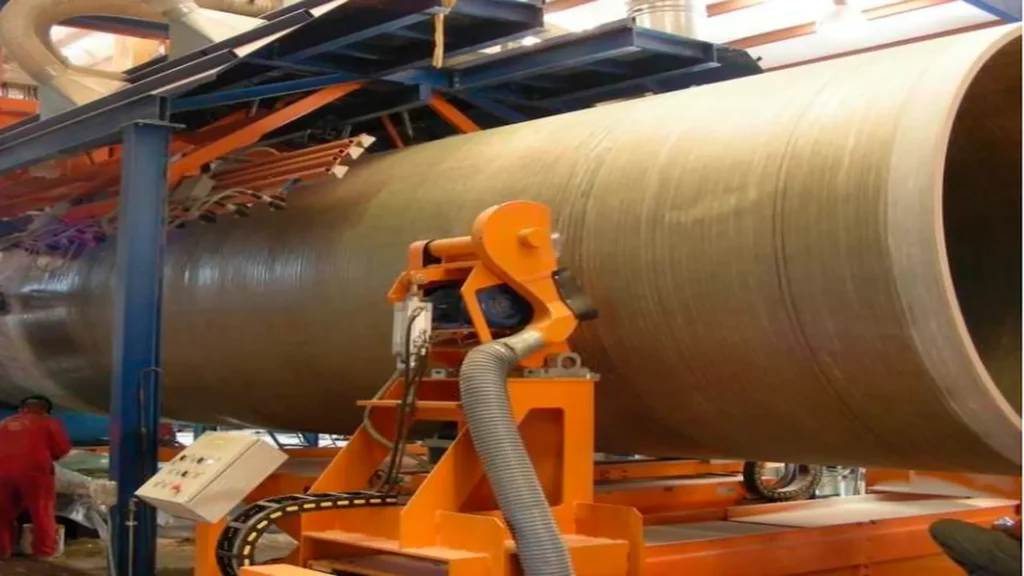
Curing and final protection
Depending on the type of resin, curing can be performed at room temperature or with controlled heat. In addition, in some cases, protective varnishes or additional coatings are applied to increase the chemical and thermal resistance of the FRP.
Technological innovations in FRP liners
Advances in composite materials have led to improved properties of FRP coatings. Some innovations include:
- New resin formulations: Improved chemical and thermal resistance of protective coatings.
- Advanced application techniques: Methods such as spray spraying or automated lamination ensure uniform, defect-free coverage.
- Real-time monitoring systems: Sensors embedded in FRP tank liners allow detecting structural changes and preventing premature failures.
Safety and environmental aspects of FRP coating application
Safety in the application process
FRP tank lining installation involves the handling of chemical materials and specialized tools, which requires strict safety protocols such as:
- Use of personal protective equipment (PPE): Gloves, safety glasses, masks with filters for organic vapors and protective clothing should be used to avoid contact with resins and solvents.
- Adequate ventilation: During resin application and curing, vapors are generated that can be toxic. Adequate air extraction must be ensured to avoid the accumulation of hazardous volatile compounds.
- Prevention of flammability hazards: Some resins, especially polyester and vinylester resins, contain flammable solvents. Ignition sources should be avoided in work areas.
- Personnel training: Applicators must be properly trained in chemical handling, application techniques and emergency response.
Environmental considerations
The environmental impact of the FRP coating application process should be minimized through responsible practices:
- Hazardous waste management: Leftover resin, solvents and contaminated materials must be disposed of in accordance with current environmental regulations.
- Reduction of volatile organic compound (VOC) emissions: The use of resins with low VOC content and the implementation of vapor capture technologies are recommended.
- Minimization of material waste: Proper planning reduces the waste of fiberglass and resin, optimizing its use and reducing the environmental impact.
- Use of environmentally friendly alternatives: Some modern resin formulations are designed to be more environmentally friendly, reducing their impact on air quality and ecosystems.
Post-application safety
Once the FRP coating is installed, it is essential to ensure its safety and performance over time:
- Periodic inspection: Visual evaluations and adhesion tests should be performed to detect possible failure or premature wear.
- Operational condition monitoring: Monitor temperature, pressure and chemical composition of stored contents to avoid liner damage.
- Compatible substances handling: Ensure that the tank only stores products compatible with the type of resin used in the coating.
Conclusion
FRP coating has established itself as an effective solution for the protection of structures and industrial storage tanks. Its corrosion resistance, durability and adaptability make it a superior alternative to conventional materials, reducing maintenance costs and extending the useful life of the structures. The correct selection of resins and fibers, together with an adequate application and compliance with regulations, guarantees its optimum performance in various industries. Its use continues to expand due to the operational and safety benefits it brings to industrial processes.
References
- https://www.cladescomposites.com/tienda/fibra-de-vidrio-vs-fibra-de-carbono/
- https://www.plaremesa.net/resina-para-fibra-de-vidrio/
- https://www.directindustry.es/prod/matrasur-composites/product-41028-377660.html
- https://www.astilleros-nicolau.com/3d-infusion-4-0/
- https://www.directindustry.com/prod/vem-spa/product-68234-505567.html