Table of Contents
- What is friction stir welding (FSW)?
- Materials suitable for FSW
- Applications of friction stir welding (FSW)
- Certification in friction stir welding (FSW)
- Recent Developments in friction stir welding (FSW)
- Technologies enhancing FSW safety
- Advantages and disadvantages of FSW
- Future trends and innovations in FSW
- Conclusions
- References
Welding is fundamental in many industries, such as automotive, aerospace, and energy, where structural integrity is critical. Traditional methods, such as arc welding, TIG, and MIG, require extreme heat, leading to challenges like thermal distortion and defects in heat-sensitive materials.
This is where friction stir welding (FSW) emerges as a solid-state process that avoids fusion and reduces common issues of traditional welding, providing stronger and more reliable joints without solidification defects, thanks to recent technological advancements and improved energy efficiency by reducing the amount of heat generated in the manufacturing process.
What is friction stir welding (FSW)?
Friction stir welding (FSW) is a process developed in 1991 that, unlike conventional welding, does not melt the materials being joined. This method is based on friction generated by a rotating tool that plasticizes the material and, through stirring, creates a solid, homogeneous weld.
FSW stands out for reducing porosity, cracks, and distortions, offering a more efficient and cleaner solution compared to traditional welding processes. Moreover, continuous technological advancements and industrial automation have enabled this process to achieve a high level of precision and repeatability, significantly improving productivity across various industries. This, combined with the optimization of energy efficiency, makes it a method that minimizes resource use while maximizing reliable results, ensuring structural integrity during the manufacturing process.
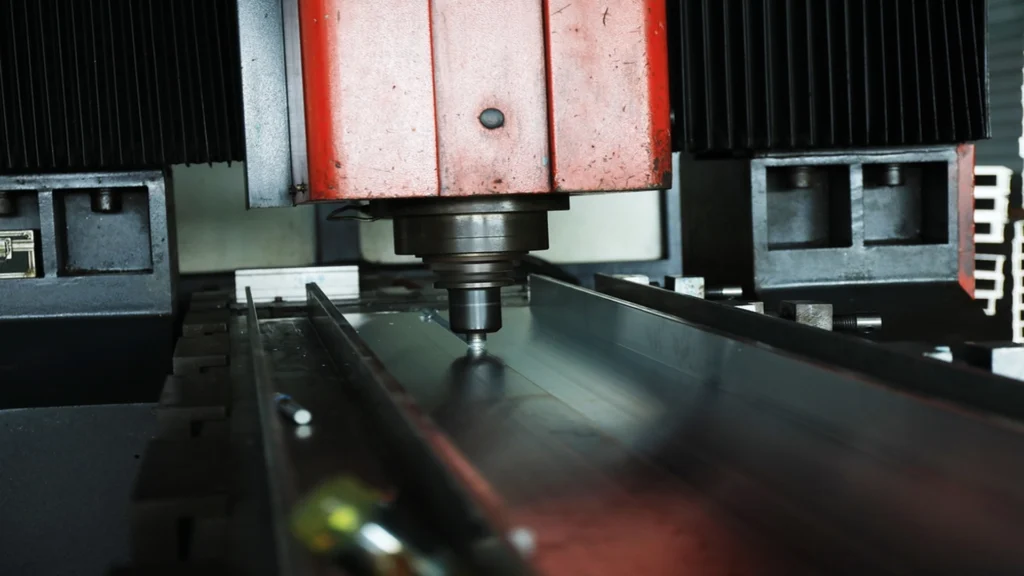
How it works
- A cylindrical rotating tool generates frictional heat when it comes into contact with the material, plasticizing it without melting it.
- The stirring of the softened material by the rotation of the tool forms a solid joint.
- The use of shielding gases or filler materials is not required, making it a more economical and environmentally friendly manufacturing process.
This method is especially beneficial for materials that are difficult to weld by fusion, such as aluminum, magnesium, copper, and titanium alloys. These materials, when welded with FSW, maintain their structural integrity, even under harsh conditions, making the manufacturing process highly reliable.
As a complement to understand the friction Stir Welding process, uses, and applications, watch the following video. Courtesy of: Stirweld.
Materials suitable for FSW
Aluminum alloys
Aluminum is one of the most compatible materials for friction stir welding (FSW). In the aerospace industry, FSW is used to join fuselage panels and wing structures, providing greater strength without the issues of thermal distortion, ensuring the structural integrity of critical components. Additionally, it has been adopted in the automotive industry, where weight reduction improves vehicle energy efficiency, a key factor in meeting energy consumption standards.
This type of welding is highly compatible with industrial automation, allowing its application in high-volume production processes. This is another clear example of how technological advancements have improved the quality and efficiency of this welding method, enhancing its use across various industries
Magnesium, Copper, and Titanium Alloys
Magnesium, due to its light weight, is used in the electronics and aerospace industries. Copper, with its high conductivity, is ideal for electrical components, while titanium, known for its strength and durability, is used in aircraft engines and military structures. The ability of FSW to weld these materials without compromising their properties ensures structural integrity, which is one of its main advantages.
Dissimilar materials
FSW also excels at joining metals with different properties, such as aluminum and copper, crucial in sectors like battery manufacturing for electric vehicles. This ability to weld dissimilar materials ensures structural integrity and has a direct impact on energy efficiency, facilitating the creation of lighter and more efficient components. Furthermore, industrial automation has enabled this type of welding to be implemented on a large scale in modern factories.
Applications of friction stir welding (FSW)
Aerospace industry
FSW is key in the manufacturing of structural components for aircraft, such as fuselages, fuel tanks, and wings. NASA has used FSW in rockets like the Space Launch System, thanks to the precision and strength this method provides, ensuring the structural integrity and reliable performance of the components, supported by significant technological advancements that enable lighter and stronger welds. Additionally, the integration of industrial automation allows for faster production with fewer errors, improving both the structural integrity and energy efficiency of aircraft.
Automotive industry
FSW has transformed vehicle manufacturing by allowing the joining of aluminum parts in bodies and chassis. This reduces the vehicle’s weight, improving its energy efficiency. Companies like Tesla and Ford have adopted this process in the production of electric vehicles, leveraging technological advancements that have enabled the joining of materials with fewer defects. In this sector, industrial automation has allowed FSW to be used in mass production, ensuring high precision and consistency in each joint, which in turn improves vehicle safety and performance.
Marine industry
In shipbuilding, FSW is used to manufacture aluminum and steel hulls and decks. This manufacturing process offers greater corrosion resistance in marine environments compared to fusion welding. Additionally, FSW is used in the construction of offshore platforms, where extreme conditions require superior durability.
Rail transportation
The use of FSW in the manufacturing of lightweight train cars has reduced wagon weight, improving energy efficiency and extending the lifespan of rail vehicles. The strong and continuous joints provided by FSW are essential for withstanding long-term stresses.
Energy sector
In the energy industry, FSW is used in the construction of wind turbines, heat exchangers, and subsea pipelines, where it ensures strong, reliable, leak-free joints, which are critical in sectors such as oil and gas. Thanks to industrial automation and recent technological advancements in welding technologies, this process has enabled the creation of more efficient and durable components capable of withstanding extreme conditions. Additionally, by reducing energy losses during the manufacturing process and producing high-quality joints, FSW directly contributes to energy efficiency in the production of equipment for energy generation and transmission.
Certification in friction stir welding (FSW)
Certification in FSW is essential to ensure quality and safety in industrial applications. Organizations such as the American Welding Society (AWS) and The Welding Institute (TWI) offer specialized programs that evaluate operator competencies, from handling welding parameters (such as rotational speed and axial force) to knowledge of material metallurgy and monitoring systems control.
These programs are adapted to current standards, including those related to industrial automation, ensuring that operators work with the most advanced technologies. The certification process includes a theoretical exam and a practical evaluation, where the welder must demonstrate their ability to create high-quality welds under different conditions.
Moreover, certification is crucial in critical sectors such as defense, aerospace, renewable energy, and other industries where precision and structural integrity are key. This certification also promotes a better understanding of how the FSW process can contribute to energy efficiency in various industries, supported by technological advancements.
Recent Developments in friction stir welding (FSW)
Friction stir spot welding (FSSW)
This variant of FSW has emerged as a result of technological advancements and is used in the automotive industry to join aluminum body panels, replacing resistance welding. This development has allowed for greater efficiency in parts production.
Robotic FSW
The automation of FSW has been made possible through technological advancements in robotics and process control, allowing for greater precision and repeatability in welds. This is particularly useful in the aerospace and automotive industries, where high-quality joints are required in complex geometries.
FSW in additive manufacturing
FSW has been integrated into additive manufacturing processes, improving the quality of joints between layers, a feat achieved through recent technological advancements in combining these processes.
Hybrid FSW techniques
Hybrid techniques combining FSW with methods like laser or arc welding are expanding the applications of this process. These combinations allow for the welding of harder materials and more complex geometries, making them particularly useful in the defense and shipbuilding industries.
Technologies enhancing FSW safety
Temperature sensors and real-time monitoring
The use of thermal sensors has been a direct result of technological advancements. These sensors allow for real-time monitoring and adjustment of welding parameters, ensuring defect-free welds.
Feedback control and advanced automation
The integration of feedback systems enables FSW machines to automatically adjust speed, heat, and force during welding, improving precision and reducing the risk of errors.
Non-Destructive Testing (NDT) systems
Techniques like ultrasound and X-rays allow for the verification of weld quality without compromising the structure. These inspections ensure that each weld meets the required quality standards.
Advantages and disadvantages of FSW
Advantages
- Higher strength: Operating in a solid state, FSW produces stronger and fatigue-resistant welds, avoiding common defects like porosity and solidification cracks.
- Eco-friendly and efficient process: No shielding gases or filler materials are required.
- Ability to Join Dissimilar Materials: FSW is ideal for joining materials that are difficult to weld by fusion, such as aluminum and copper.
Disadvantages
- Limited in complex geometries: FSW is more suitable for linear or flat welds.
- High initial costs: Specialized machinery and tools are expensive.
- Limited application in extremely hard materials: Although new tools are being developed, FSW has difficulties with materials like superalloys.
Future trends and innovations in FSW
- Automation and robotic FSW: The integration of artificial intelligence into robotic systems is optimizing FSW, allowing for real-time adjustments of welding parameters, such as rotational speed, axial force, and temperature. This not only improves productivity but also ensures that each weld meets the required quality standards. In industries like automotive and aerospace, where consistency is critical, robotic FSW ensures unparalleled precision in mass production of complex parts. Robots can perform welds in challenging geometries, optimizing both the quality and speed of production processes.
- Expansion of FSW in new industries: FSW is expanding its use in sectors requiring highly reliable and durable welds, such as electronics and battery manufacturing. For example, in the electric vehicle industry, FSW facilitates the joining of dissimilar materials like aluminum and copper in battery systems, where the differences in thermal expansion coefficients of these metals can be an issue in other welding methods. Additionally, the growing adoption of FSW in the production of medical devices and electronic components shows how this technology continues to evolve and find new applications.
- Advanced materials for tools: One of the key advancements in FSW is the development of tools made from harder, more wear-resistant materials, such as tungsten carbide or high-durability ceramics. These materials allow FSW to be used in welding harder materials, like superalloys and titanium, which previously posed significant challenges. As research in this field advances, it is likely that the range of materials that can be welded using FSW will expand even further, opening new possibilities for its application in critical industrial sectors, such as aerospace and defense.
Conclusions
In conclusion, friction stir welding (FSW) has proven to be a revolutionary solution in the welding industry, standing out for its ability to join complex materials efficiently and reliably. By eliminating common defects in traditional methods, such as porosity and cracks, FSW offers a superior alternative that has been adopted in critical sectors like automotive, aerospace, and energy.
The growing adoption of industrial automation and technological advancements continues to push this process toward new frontiers, allowing for greater precision, cost reduction, and production consistency. Additionally, the focus on energy efficiency makes FSW a key tool for industries looking to reduce their environmental impact and improve sustainability.
With the development of new technologies, such as robotics and artificial intelligence, the future of FSW promises even more innovations, solidifying its position as an essential technology to meet the demands of an ever-evolving global industrial landscape.
References
Own source