The choice between brazing and soldering is a vital aspect of many industrial processes and can be a challenge if the key differences between the two techniques are not well understood. In the industrial sector, metal welding is fundamental to the manufacture and repair of metal components, and among the most commonly used techniques are brazing and soldering. Each offers specific benefits and is applied in different contexts depending on the needs of the project.
This article provides a detailed comparative analysis of brazing vs. soldering, exploring their differences in terms of working temperatures, compatible materials, industrial applications, and mechanical properties. Case studies and factors to consider when selecting one technique over the other will also be discussed.
What is welding?
Welding is a fixing process in which two or more pieces of a material (generally metals or thermoplastics) are joined together, usually achieved through coalescence (fusion), in which the pieces are welded by melting. A filler material (metal or plastic) can be added, which, when melted, forms a pool of molten material between the pieces to be welded (the weld pool). When cooled, it becomes a fixed joint, which is called a seam.
Key differences between brazing and soldering
In the world of brazing, choosing the right technique is critical to ensure the quality and durability of metal joints. Both brazing and soldering are widely used methods, but their application depends on specific factors that directly influence the performance and efficiency of industrial processes.
Understanding the distinctive characteristics of each technique is essential for making informed decisions on projects that require reliable, high-quality joints. Below, we will explore in detail the key differences between these two welding techniques, analyzing how their properties and applications align with the needs of various industries.
Soft soldering
- Working temperatures: Brazing is generally carried out at temperatures below 450 °C.
- Filler material: Copper, silver, nickel, or aluminum alloys with a higher melting point.
- Compatible materials: This technique is ideal for non-ferrous metals such as copper, brass, and tin. The low melting temperature makes it ideal for applications where it is not desirable to compromise the structure or surface finish of the base material.
- Typical Industry Applications: It is frequently used in the soldering application of electronic component fabrication, plumbing, and precision work where mechanical strength is not a critical factor. Common examples include soldering of printed circuit boards and connection of copper pipes in plumbing systems.
- Advantages: Easy to perform, low cost, excellent corrosion resistance.
- Disadvantages: Lower mechanical strength, risk of lead toxicity (in some alloys), limited to low-temperature joints.
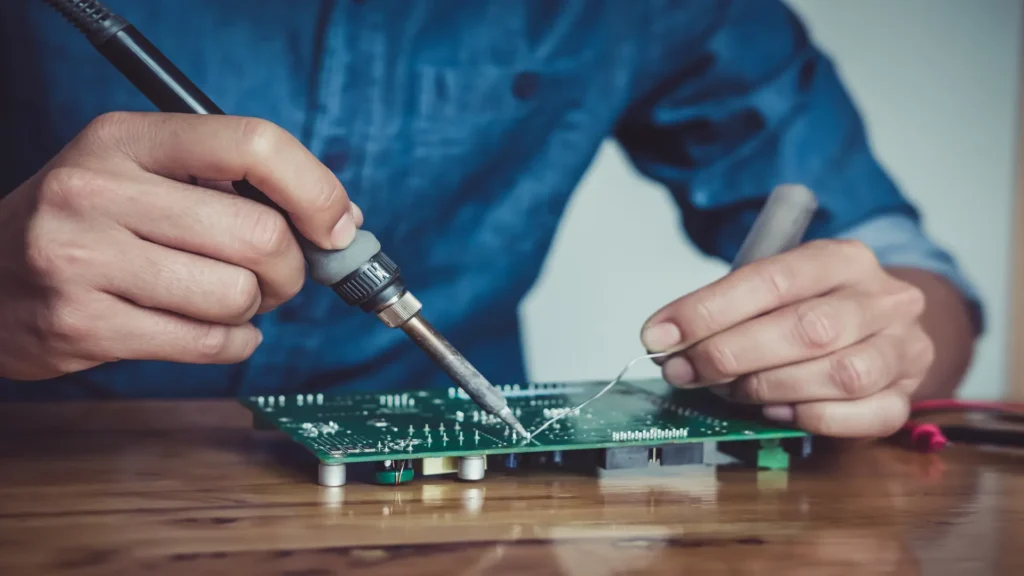
Brazing
- Working temperatures: This solder requires higher temperatures, typically in the range of 450 °C to 900 °C.
- Filler material: Copper, silver, nickel, or aluminum alloys, with a higher melting point.
- Compatible materials: This method is more suitable for use on a wider range of materials, including ferrous metals, ceramics, and glass. The higher melting temperature allows for stronger and more durable bonds, which is crucial in applications that need to withstand extreme conditions.
- Typical industry applications: It is preferred in applications where strong, durable joints are required, such as in the fabrication of metal structures, heat exchangers, and in the welding of metals that will be exposed to high pressures or elevated temperatures. The aerospace and automotive industry are large consumers of this weld due to the demanding conditions in which their products operate.
- Advantages: Increased mechanical strength, high service temperature, ability to join a wide variety of materials.
- Disadvantages: Requires greater temperature control, higher cost, can distort delicate parts.
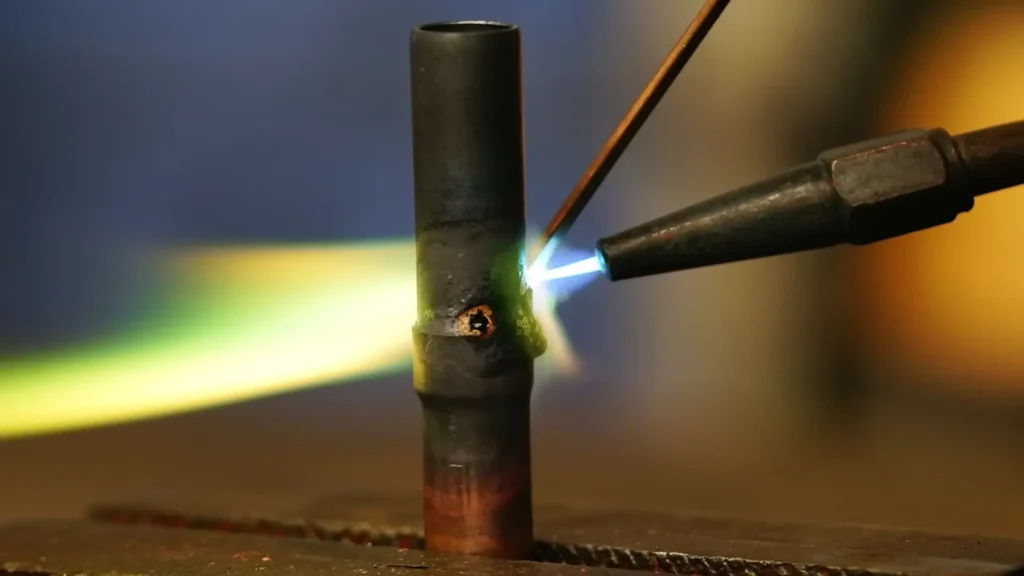
For more content on the subject of the key differences between the welds mentioned above, see the following video courtesy of Rajib Bhowmik to reinforce the above.

Brazing vs. soldering.
Comparison of the mechanical properties of brazing vs. soldering
Welding is a vital technique in the manufacture and repair of metal components, and the choice between brazing and soldering affects not only the integrity of the joint but also its ability to withstand extreme conditions. The mechanical properties of each technique, such as strength and durability, play an essential role in determining its suitability for different applications.
Soft soldering
- Strength and durability: Although easier to apply and repair, this weld offers lower strength, making it more suitable for applications where mechanical loads are minimal and exceptional durability is not required.
- Application conditions and performance: It performs well in less demanding environments, such as electronic systems or water pipelines, where high temperatures or extreme pressures are not expected.
Brazing
- Strength and durability: Thanks to the high melting temperatures and complete fusion of the filler materials, the joints created by this weld are more robust. This is essential in environments where long-term durability and structural integrity are critical.
- Application and performance conditions: It is best suited for severe conditions, such as systems operating under high pressure, extreme temperatures or constant exposure to corrosive agents. Its ability to maintain integrity under these conditions makes it ideal for critical industrial applications.
Analysis of brazing vs. soldering cases
When choosing between brazing and soldering, it is advisable to understand their specific applications. Each technique is best suited for different scenarios, from electronic component fabrication to building robust structures. Below, we will discuss specific cases where each type of soldering is preferable, and the key factors that guide this decision, such as required strength, material sensitivity and process efficiency.
Soft soldering applications
Common in applications where a fast and effective technique is needed to join components without compromising the integrity of the base material. Examples include:
- Printed circuit boards: This soldering application is essential in the electronics industry, where precision is required and where high temperatures could damage sensitive components.
- Copper pipes: In plumbing, it is used to join copper pipes, as the low melting temperature prevents damage to the base material and ensures a tight joint.
Brazing applications
It is the preferred technique in scenarios where maximum strength and durability are required. Some examples are:
- Metal structures: In the construction of structures that must withstand heavy loads and adverse environmental conditions, this welding is the most recommended to guarantee structural integrity.
- Automotive and aerospace industry: To create components that must operate under extreme stresses, ensuring long-term safety and performance.
Factors to consider for selection between brazing vs. soldering
- Strength required: If the application requires withstanding heavy loads or resisting extreme conditions, brazing is the obvious choice.
- Material sensitivity: For jobs involving heat-sensitive materials, brazing is more suitable to avoid thermal damage.
- Cost and efficiency: Brazing is usually cheaper and faster to apply, making it a preferred choice in less demanding applications.
Conclusions
Brazing vs. soldering offers a common dilemma in the industry, each technique has its own advantages and ideal applications. Brazing is perfect for jobs that require precision and where strength is not the primary factor. On the other hand, brazing is indispensable in applications where maximum durability and strength are demanded.
Understanding the differences between these two techniques and their applications is essential to making informed decisions that optimize the application of brazing on any project. With the right knowledge, industry professionals can select the technique that best suits their needs, ensuring optimal performance and extended life of their metal components.
Choose the ideal welding technique for your project! Find out which one best suits your needs.
References
Own source