Table of Contents
- Introduction
- Basic concepts
- Operational advantages
- Implementation challenges
- Current and future trends
- Featured case studies
- Operational advantages of FPSOs over other offshore platforms
- Conditions favoring the implementation of FPSO vs. fixed infrastructure
- Evolution of FPSOs in the face of sustainability and energy efficiency challenges
- Conclusions
- References
Introduction
Oil and gas operations in offshore environments have evolved considerably in recent decades, driven by the need to access increasingly remote and deeper water reservoirs. Among the various technological solutions developed, FPSO (Floating Production, Storage and Offloading) vessels have emerged as a distinctive alternative to fixed platforms, semi-submersibles and other traditional offshore systems.
These vessels converted or built specifically for oil production represent a significant evolution in the offshore extractive industry, offering a set of operational, economic and strategic advantages that have positioned them as preferred options in numerous projects around the world, especially in regions with challenging conditions or limited infrastructure.
Floating Production, Storage and Offloading Units are critical offshore facilities for the deepwater oil and gas industry. We will explore several aspects of this technology:
Basic concepts
FPSO stands for Floating Production, Storage, and Offloading. It is a floating production facility for the oil and gas industry. FPSOs are used to produce, process and store oil or gas directly at sea and then transfer it to tankers or pipelines that transport the produced oil or gas to land. It consists of a floating structure designed to:
- Receive hydrocarbons produced from subsea wells.
- Process the hydrocarbons by separating oil, gas and water.
- Store the produced oil.
- Transferring the oil to tankers for transportation.
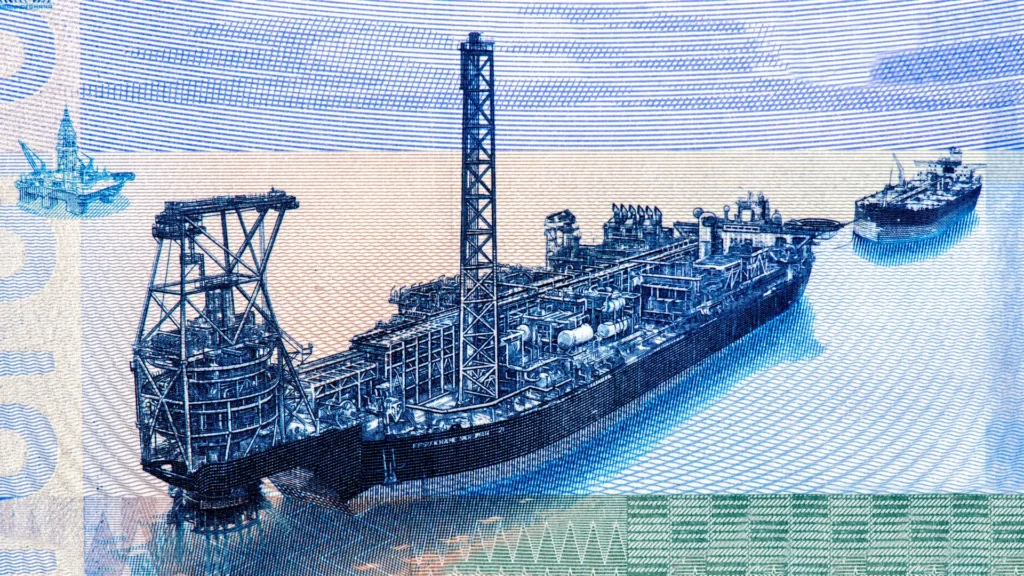
These modern facilities can process between 50,000 and 250,000 barrels of oil per day and store between 500,000 and 2 million barrels.
Main components
- Hull: Generally converted from existing tankers or purpose-built.
- Mooring systems: Rotating turret or distributed mooring.
- Risers: Pipelines connecting subsea wells to the floating unit.
- Process plant:
- Hydrocarbon separators.
- Water treatment systems.
- Gas compressors.
- Water/gas injection systems.
- Storage systems: Specially designed tanks.
- Unloading systems: Arms or hoses for transfer to tankers.
- Accommodation modules: For crew (typically 50-200 people).
- Power generation systems: Generally gas turbines.
- Safety systems: Leak detection, fire suppression, evacuation.
Operational advantages
Mobility and reuse
- They can be relocated to different oil fields once the initial reservoir is depleted.
- They allow the economic exploitation of marginal or small fields.
- They reduce the financial risk by allowing the reuse of the asset.
Operational flexibility
- Ability to operate in virtually any water depth.
- Can be disconnected and moved in case of extreme weather conditions (hurricanes).
- Allow modular expansion of processing capacity.
Economic advantages
- Lower cost and development time compared to fixed platforms.
- Do not require extensive subsea infrastructure such as long distance pipelines.
- Significantly reduce decommissioning costs at the end of field life.
Global applicability
- Effective in remote regions without existing infrastructure.
- Ideal for developing countries without refining capacity or extensive transportation.
- Operable in diverse environmental conditions, from Arctic to tropical waters.
Implementation challenges
Despite their advantages, they face significant technical and operational challenges:
Technical challenges
- Stability: Maintain operation in adverse weather conditions.
- Mooring system design: Critical for safety and operability.
- Structural integrity: Fatigue from cyclic movements and marine corrosion.
- On-site maintenance: Perform complex repairs in remote locations.
- Space constraints: Optimize complex processes in a confined space.
Operational challenges
- Logistics: Personnel, supplies and spare parts turnover in remote locations.
- Transfer systems: Risk during offloading operations to tankers.
- Water production management: Increasing volumes as the field matures.
- Emissions and energy efficiency: Gas flaring reduction and energy optimization.
- Aging asset management: Life extension beyond original design.
Regulatory and environmental challenges
- Regulatory compliance: Significant variation between jurisdictions.
- Spill risk: Robust prevention and contingency systems.
- Atmospheric emissions: Increasingly stringent greenhouse gas regulations.
- Decommissioning: End-of-life environmental considerations.
- Marine biodiversity: Protection of sensitive ecosystems.
Current and future trends
Technology continues to evolve to meet new challenges:
Recent technological innovations
- Enhanced disconnectable mooring systems for hurricane/cyclone prone areas.
- Digitalization and digital twins for operations optimization.
- Automation and remote operation solutions.
- Specific designs for arctic and ultra-deepwater conditions.
Sustainability
- Integration of renewable energies to reduce emissions.
- Advanced vapor recovery systems.
- Energy efficiency technologies.
- Reduction of the overall environmental footprint.
Economic
- Standardized designs to reduce construction costs.
- Smaller and more modular for marginal fields.
- Leasing and as a service business models.
- Integration with intelligent subsea infrastructures.
Featured case studies
Prelude FLNG (Shell)
Although it is technically a FLNG (Floating Liquefied Natural Gas) unit and not an FPSO, it represents the evolution of the concept. It is the largest floating facility ever built, at 488 meters in length. Prelude is an operational floating liquefied natural gas plant located in the offshore area northeast of Broome, Western Australia. It is designed to extract, liquefy and store natural gas at sea before shipping it to its customers.
Pioneiro de Libra (Petrobras)
First in the Brazilian pre-salt field, using advanced technology to handle the high CO2 content of the associated gas. The Brazilian pre-salt fields are oil fields located in the Atlantic Ocean, in ultra-deep water. They are located in the Santos Basin and Campos Basin. The Pioneiro de Libra FPSO (PDL) is an active facility of the Altera & Ocyan joint venture.
Egina FPSO (Total)
The Egina FPSO is a floating production, storage and offloading unit that is part of an oil field in Nigeria operated by TotalEnergies. It is the largest FPSO ever built by TotalEnergies.
Operating in Nigeria, with 200,000 barrels per day of capacity and 65% local content in its construction, setting new standards for local industrial participation.
Liza Destiny (ExxonMobil)
The Liza Unity represents the second production unit deployed in Guyana’s Stabroek block, specifically for the development of Phase 2 of the Liza field. This project was developed by ExxonMobil (operator) in partnership with Hess Corporation and CNOOC Limited, and marks a significant milestone in the emerging oil industry of Guyana, a country that until recently was not on the world energy map.
It is the first FPSO in Guyana’s waters, initiating production in a country with nao previous experience in offshore production.
Operational advantages of FPSOs over other offshore platforms
A tensioned leg platform (TLP) is a floating structure anchored to the seabed by tendons. TLPs are used for offshore oil and gas production, and are also being considered for wind turbines.
FPSOs offer several distinct operational advantages when compared to other offshore solutions such as fixed platforms, semi-submersibles or TLPs (Tension Leg Platforms):
Integrated storage
The built-in storage capacity (between 500,000 and 2 million barrels) is a key advantage. Other platforms require additional infrastructure for storage or immediate pipeline transportation.
Logistical independence
FPSOs can operate in extremely remote locations without the need for subsea pipelines. Oil is stored and then periodically transferred to shuttle tankers, eliminating reliance on fixed transportation infrastructure.
Adaptability to deep and ultra-deep waters
While fixed platforms are practically unfeasible beyond 500 meters, FPSOs can operate at depths greater than 3,000 meters, connecting to wells via flexible riser and subsea systems.
Full processing capacity
Modern FPSOs incorporate comprehensive processing capabilities, including:
- Oil, gas and water separation.
- Produced water treatment.
- Gas compression and reinjection.
- Crude oil stabilization.
- Chemical treatment.
This integration reduces the need for additional support facilities.
Flexibility in extreme weather conditions
FPSOs equipped with disconnectable mooring systems can disengage and sail to safety in the face of hurricanes or severe cyclones, something impossible for fixed platforms. The Kikeh FPSO in Malaysia and several in the Gulf of Mexico incorporate this feature.
The Kikeh FPSO is a floating production, storage and offloading vessel (FPSO) located in the Kikeh oil and gas field in Malaysia. It was the first deepwater FPSO in Malaysia and Asia.
Mobility and reuse
At the end of a field’s productive life, an FPSO can be repositioned to another field. The Firenze FPSO unit operated in Italy, then reconfigured to serve in the Ivory Coast, and later in Indonesia, significantly extending its economic life.
The FPSO Firenze is a floating production, storage and offloading (FPSO) vessel that was used in the Adriatic Sea and Ivory Coast.
Conditions favoring the implementation of FPSO vs. fixed infrastructure
The choice between FPSO and fixed infrastructure depends on multiple technical and economic factors:
Reservoir characteristics
Favorable for FPSO:
- Small to medium fields: Reservoirs with reserves of 50-300 million barrels are often too small to justify fixed platforms or extensive pipelines, but ideal for FPSOs.
- Dispersed fields: When several small reservoirs are in relative proximity, an FPSO can be repositioned sequentially.
- High reserve uncertainty: If there is significant uncertainty about recoverable volume, the lower initial capital commitment and relocation flexibility make an FPSO preferable.
Unfavorable for FPSO:
- Giant fields with productive life >30 years: In these cases, fixed platforms may offer lower long-term cost.
- High gas volume: Fields with extremely high gas-to-oil ratios may require specific solutions such as FLNG.
Environmental and geographical conditions
Favorable for FPSO:
- Deep and ultra-deep water: From 500m depth, FPSOs become progressively more competitive with fixed solutions.
- Remote areas without infrastructure: In regions with no existing pipeline network.
- Areas prone to extreme weather events: With disconnectable mooring systems, FPSOs can avoid severe damage.
- Complex seabed: When geological conditions make it difficult to install fixed platforms.
Unfavorable for FPSO:
- Extremely turbulent waters: In conditions of constant severe waves, other solutions such as TLPs may offer better stability for continuous operations.
- Permanent arctic zones: Although there are FPSOs capable of operating in arctic conditions (such as the Goliath in the Barents Sea), permanent ice remains a challenge.
The Goliath oil field is located in the Barents Sea, north of Norway and Russia, 50 kilometers southeast of the Snøhvit field. The water depth is 360-420 meters. The field is developed with a floating production, storage and offloading facility (FPSO Sevan 1000).
Economic and strategic factors
Favorable for FPSO:
- Need for accelerated development: FPSOs can reduce development time by 1-2 years compared to complex fixed solutions.
- Capital constraints: Leasing model significantly reduces initial investment.
- Countries with limited refining capacity: Storage capacity allows for direct export.
- Emerging markets: Reduces the need for extensive coastal infrastructure.
Unfavorable for FPSO:
- Regions with extensive pipeline networks: In mature areas such as parts of the North Sea or Gulf of Mexico where there is established infrastructure.
- Tax conditions favoring CAPEX over OPEX: Since FPSO leasing contracts are usually accounted for as an operating expense.
Evolution of FPSOs in the face of sustainability and energy efficiency challenges
FPSOs are undergoing a significant transformation to address environmental and energy challenges:
Reduction of greenhouse gas emissions
Current solutions:
- Partial electrification: Substitution of gas turbines for more efficient electrical generation.
- Advanced vapor recovery systems: Reduction of fugitive emissions of volatile organic compounds (VOCs).
- Gas flaring optimization: Implementation of flare recovery systems and zero routine flaring policies.
- Heat integration: Use of waste heat to reduce overall energy consumption.
Emerging developments:
- Connection to offshore power grids: FPSO Jotun B in Norway is being modified to connect to an offshore power grid partially fed by hydropower.
- Integration of renewables: Pilot projects with floating solar panels and even small complementary wind turbines.
- Energy storage systems: Large-scale batteries for load optimization and peak response.
Jotun is a deposit located in the central part of the North Sea, 25 kilometers north of the Balder deposit. The water depth is 125 meters.
Produced water management
Produced water management is the process of treating, reusing, recycling, or disposing of water generated by the oil and gas industry. The objective is to meet regulatory and operational needs.
With the aging of the fields, the management of produced water becomes critical:
- Advanced treatment technologies: Improved hydrocyclone systems, membrane filtration and biological treatment that exceeds current regulatory standards.
- Optimized re-injection: Systems that require less energy consumption for high volume re-injection.
- Continuous quality monitoring: Real-time sensors ensure ongoing environmental compliance.
Digitization for operational efficiency
Digital transformation is optimizing energy efficiency:
- Digital twins: Complete virtual replicas that enable continuous process optimization.
- Advanced Analytics: Predictive algorithms that identify operational inefficiencies.
- Predictive maintenance: Reduction of unscheduled shutdowns that usually involve gas flaring.
- Remote operations: Reduction of onboard personnel reduces logistics footprint.
Premier Oil’s FPSO Catcher incorporated a full digital twin that enabled energy consumption to be reduced by approximately 15% over the base design.
The BW Catcher FPSO is a floating facility that produces, stores and offloads oil and gas in the Catcher field in the central North Sea. It is operated by BW Offshore and is leased to Premier Oil.
Design for sustainability
The new FPSOs incorporate environmental considerations from their conception:
- Optimized hull design: Reduced hydrodynamic resistance that minimizes consumption during repositioning.
- Advanced materials: Reduced weight and improved durability.
- Modularization: Facilitates technology upgrades during operational life.
- End-of-life planning: Design provides for eventual dismantling and recycling.
Industry initiatives and case studies
- SBM Offshore FPSO ZERO: Concept that seeks carbon neutral operation through a combination of efficiency, electrification and offsets.
- FPSO Liza Unity (Guyana): First FPSO to receive ABS SUSTAIN-1 certification, which verifies sustainability aspects throughout its life cycle.
- Equinor’s “Next Generation FPSO” program: Focused on reducing emissions by 40% compared to conventional designs.
The Johan Castberg FPSO is a Floating Production, Storage, and Offloading (FPSO) operated by Equinor, located in the Barents Sea. It entered the market in March 2025 and is expected to produce oil for 30 years. Equinor’s FPSOs contribute to sustainability by optimizing hydrocarbon extraction and transport, thereby reducing environmental impact and improving energy efficiency

Remaining challenges and innovation areas
- Technical-economic balance: The most environmentally advanced solutions still face cost barriers.
- Carbon sequestration: Small and medium-scale technologies adapted to the offshore environment.
- Adaptation to alternative fuels: Research on potential use of hydrogen or ammonia for power generation.
- Extended Reach Subsea: Reduction of floating infrastructure by connecting wells at greater distances.
Conclusions
The evolution of the offshore industry towards deeper and more isolated areas has driven the adoption of versatile and efficient technological solutions such as FPSO vessels. These floating units, capable of integrating production, storage and offloading processes, have proven to be instrumental in maintaining profitability and operational continuity in challenging offshore environments.
Their modular design, adaptability to different production volumes and compliance with strict safety and environmental regulations make FPSOs an indispensable component in the sustainable development of the offshore oil and gas sector. In this context, their role will continue to be decisive for the future expansion of the offshore energy industry.
The evolution of FPSOs illustrates how the offshore industry is adapting to an operating context where energy efficiency and sustainability have become both economic and regulatory imperatives. Innovations emerging in this sector have the potential to influence the entire energy value chain.
References
- ExxonMobil. (2025, 22 de febrero). Guyana project overview. https://corporate.exxonmobil.com/locations/guyana/guyana-project-overview
- TotalEnergies. (2025, 16 de abril). Egina: A Flagship Offshore Project in Nigeria. https://totalenergies.com/energy-expertise/projects/oil-gas/deep-offshore/egina-nigeria
- Offshore Technology. (2025, 16 de abril). Pre-salt oil region: tracing the history of exploration in Brazil. https://www.offshore-technology.com/features/pre-salt-oil-region-brazil
- Brazil Energy Insight. (2023, 4 de diciembre). FPSO Pioneiro de Libra completes six years of production. https://brazilenergyinsight.com/2023/12/04/fpso-pioneiro-de-libra-completes-six-years-of-production/
- Offshore Energy. (2025, 16 de abril). Six-year extension for ‘largest deepwater FPSO in Malaysia’. https://www.offshore-energy.biz/six-year-extension-for-largest-deepwater-fpso-in-malaysia/
- Norsk Petroleum. (2025, 16 de abril). Norwegianpetroleum.no – facts about Norwegian petroleum activites. https://www.norskpetroleum.no/en/