Introduction
Flux-Cored Arc Welding (FCAW) is a widely used process in industry, especially in sectors where fast and tough welding is a necessity. In this article, we will explore the key components of FCAW equipment, its functions, and the maintenance required to optimize its performance and durability in various applications.
What is flux-cored welding equipment?
This process uses a flux-filled cored wire that generates a protective atmosphere as it melts. This process allows welding without the need for additional gas under certain conditions, ideal for outdoor work or environments where wind can disperse the shielding gas.
What is flux-cored wire?
It is a type of electrode used in the FCAW welding process. This wire consists of a hollow metal casing filled with powdered materials such as fluxes and deoxidizers. During welding, these components produce gases and slag that protect the arc and the weld. Its design provides a high deposition rate and is ideal for welding in construction applications, heavy structures, and outdoor work.
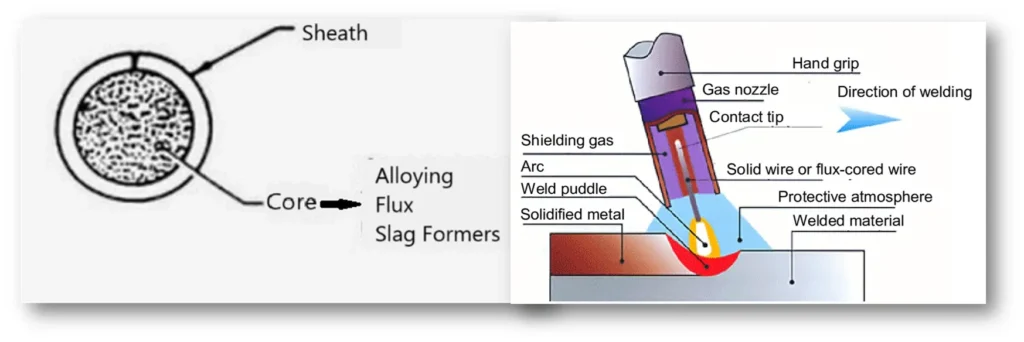
How the flux-cored arc welding process works
The FCAW process uses a flux-cored wire that contains a flux in its core, which, when melted, creates a protective layer around the arc and prevents oxidation of the weld. This mechanism is efficient in environments where other processes, such as MIG welding, may not be effective due to the dispersion of the shielding gas.
Types of FCAW welding process
There are two types of FCAW processes with the following characteristics:
FCAW-S (Self-Shielded Flux-Cored Arc Welding)
- Protection: In this process, the cored wire contains deoxidizing elements and a flux which, when exposed to the heat of the electric arc, generates gases that protect the weld pool without the need for external gas.
- Application: Commonly used in construction work, especially in structural, repair and mining applications. Its portability and lack of additional gas requirements make it very versatile for field work.
- Wire: Consists of a core composed of metal powder, deoxidizing materials and shielding agents that generate the slag and gases necessary to protect the weld.
- Welding positions: FCAW-S allows welding in all positions, although some wire types may be position-specific.
- Advantages: Great outdoor versatility and deep penetration capability make it ideal for welding thicker materials and in less controlled conditions.
- Disadvantages: Because it does not use external shielding gas, it can generate a greater amount of slag and spatter, which requires cleanup afterward and can affect the appearance of the weld.
FCAW-G (Gas-Shielded Flux-Cored Arc Welding)
- Shielding: Unlike FCAW-S, the FCAW-G process requires an external shielding gas (such as carbon dioxide or a mixture of argon and CO₂) to be supplied through the nozzle to protect the weld pool.
- Application: Mainly used on metal structures and in production welding work, where environmental conditions are more controlled, such as in workshops or factories.
- Wire: Like FCAW-S, flux cored wire contains flux which aids in slag formation and arc stability, although the external gas provides the main protection.
- Welding positions: Allows welding in all positions, although the need for shielding gas limits it in windy outdoor applications.
- Advantages: The combination of flux and shielding gas provides a cleaner weld, with less slag and spatter. In addition, the shielding gas helps to improve arc control and stability, making it easier to obtain high quality welds and finishes.
- Disadvantages: It is less practical to use outdoors, as wind can interfere with the shielding gas. It also requires additional equipment, such as gas supply and cylinders.
Main components of flux-cored welding equipment
- Welding power source: Generates the electric arc between the flux-cored wire and the workpiece. It can be direct current (DC) and is generally used in direct (DCEN) or reverse polarity (DCEP), depending on the welding requirements.
- Wire feeder: The wire feeder ensures a constant flow of wire to the welding gun. Modern wire feeders allow the wire speed to be adjusted to suit different materials and thicknesses, improving efficiency and reducing interruptions in industrial applications.
- Welding gun: The welding gun guides the wire into the base metal and facilitates control of the position and direction of the weld and the nozzle, which is the part of the gun, directs the gas into the weld pool.
- Flux-Cored Wire: This is the main element of the process and is composed of an outer metallic layer and a core containing compounds that generate a slag that helps protect the weld pool. There are two types of flux-cored wires:
- Self-shielded wire: Ideal for outdoor work or windy conditions.
- Externally gassed wire: For controlled environments where higher weld quality is required.
- Cooling system: The cooling system prevents overheating of the equipment, especially in continuous work processes. Liquid cooling systems are common in industrial environments due to their effectiveness in maintaining optimum equipment temperature.
- Shielding gas: For use in the FCAW-G process. It requires an external shielding gas, usually carbon dioxide (CO₂) or a mixture of argon and CO₂. This gas is supplied through the welding gun nozzle and covers the weld pool, protecting it from air contamination (mainly oxygen and nitrogen).
- Wire feed system: This is a mechanism that pushes the tubular wire from the spool to the tip of the welding gun. This system must be accurate and adjustable to control the wire feed speed.
- Parameter control system: Adjust and control various parameters, such as voltage, wire feed speed, and shielding gas flow.
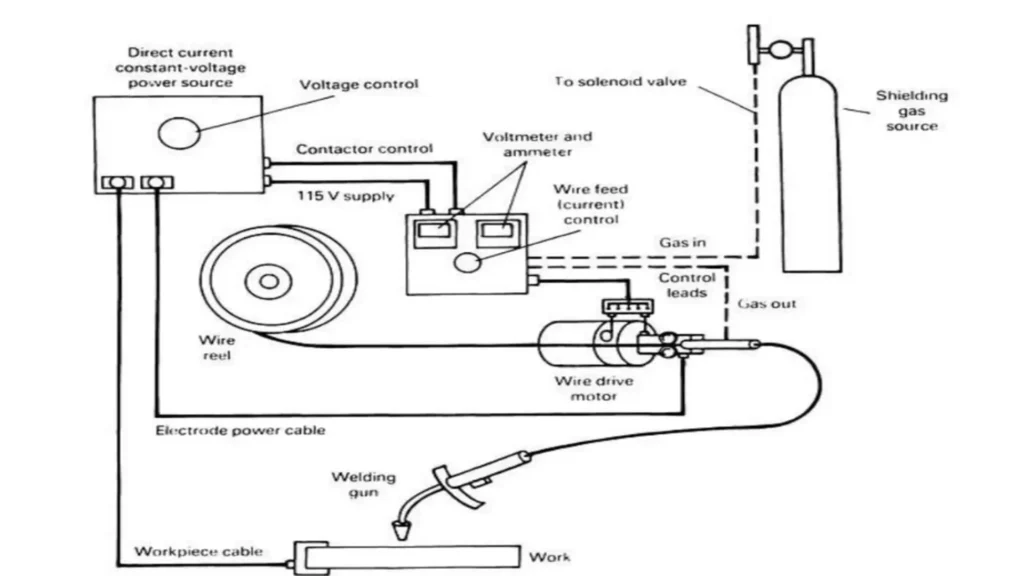
Comparison of flux-cored welding and other welding types
Welding processes with some similarities to FCAW are the following two:
MIG/MAG welding (Metal Inert gas/Metal Active Gas)
The most important similarities and differences between FCAW and MIG/MAG processes are:
- Similar equipment: Both processes use similar welding power sources, wire feeders and welding guns.
- Continuous electric arc: Both processes use semi-automated or automated welding.
- High deposition rate: Both are ideal for fast, high-productivity welding.
- Gas-shielded and gasless welding: FCAW can be used without gas, thanks to its shielding flux, or with additional gas in controlled environments. MIG/MAG are used with gas only.
- Wire composition: MIG/MAG uses a solid wire, whereas FCAW uses a tubular wire with a protective flux core, which allows it to work without protective gas.
- Application conditions: FCAW is ideal in windy or outdoor environments, where the gas in MIG/MAG could be dispersed.
- The main difference between these two processes is that the wire in FCAW contains a flux core that generates slag, protecting the molten metal and improving strength in certain applications.
TIG welding (Tungsten Inert Gas)
Flux-cored and TIG welding have important differences due to their specific characteristics, advantages, and limitations such as the following:
- Electrode and shielding: FCAW uses a flux-cored wire with internal flux that protects the weld and can be used with or without additional gas. TIG uses a non-consumable tungsten electrode supplemented with external filler rods that are melted to create the joint, always requiring inert gas protection (such as argon).
- Speed and quality: FCAW is fast and suitable for outdoor work or structural materials, but generates slag. TIG is slower, but offers high-precision welds and a clean, dross-free finish.
- Applications: FCAW is ideal for structural and high-productivity work. TIG is used for delicate materials and precision applications, such as in the aerospace and medical industries.
- Speed and productivity: FCAW is faster and features a high deposition rate, while TIG is a slower process, due to its focus on precision and control.
- Weld quality and finish: FCAW generates slag, which must be removed after welding. Although tough and suitable for thick materials, the finish is not as precise or aesthetically pleasing as TIG which produces clean, high-quality dross-free welds with a smooth finish.
- Materials and applications: FCAW is excellent for outdoor work and thick materials, such as carbon steel and some stainless steels. It is commonly used in construction, pipe repair, and structural applications, while TIG is preferred for more delicate materials and high-precision applications, such as aluminum, stainless steel, copper, and nickel alloys. It is ideal for welding in aerospace, medical and component industries that require high integrity and precision.
Basic maintenance of flux-cored welding equipment
To maximize the lifetime of FCAW equipment and to ensure its optimum performance, the following regular maintenance is recommended.
- Cleaning the wire feeder: Regularly clean the wire feeder to prevent the accumulation of dust or debris that can obstruct the wire flow and cause irregularities in the weld.
- Inspection of cables and connections: Check power cables and connections to ensure that they are in good condition, free of wear and damage. Damaged cables can cause loss of power and affect weld quality.
- Cooling system maintenance: On equipment with cooling, it is important to check that the system is working properly to avoid overheating, which can reduce its service life. Clean and, if necessary, replace the coolant.
- Cleaning the welding gun: Flux residues can build up in the gun nozzle, influencing wire flow and arc stability. Clean the nozzle regularly to avoid clogging.
- Check and replace flux cored wire: Replace the wire when defects are observed in the weld, such as porosity or inconsistencies, which may indicate problems with the wire.
- Gas flow check (if applicable): In case of FCAW-G (with gas), check that valves and connections are in good condition and that the flow is adequate to ensure a stable protective atmosphere.
Conclusion
FCAW welding is a versatile and robust technique, particularly suitable for industrial applications in outdoor environments. With its specialized components and its ability to weld without the need for shielding gas in some cases, it offers a flexible and effective solution. Proper preventive maintenance of welding equipment is essential to prolong equipment life and maintain optimum weld quality.
References
- https://www.researchgate.net/figure/Flux-cored-wire-a-3-FCAW-principle-b-4_fig1_328896813
- https://es.slideshare.net/slideshow/fcawppt/254988567#9