In the world of engineering and asset management, fitness-for-service (FFS) assessments stand as a fundamental pillar to ensure the longevity and operational efficiency of equipment and facilities. Fitness for service evaluation procedures provide a means to help process plant operators make decisions to determine whether equipment can continue to operate safely to primarily avoid injury to personnel, the environment, and unexpected downtime.
These assessments, at their core, represent a proactive approach to maintaining structural integrity in industrial environments. From damage identification and analysis to risk assessment, each phase contributes to informed decision making. In this article, we will deeply explore the complex world of fitness for service, highlighting its importance, applications and key considerations, including the relevance of the API 579-1 regulation.
What is fitness for service (FFS)?
Fitness for service refers to the systematic evaluation of components, equipment or structures to determine whether they can still perform their intended functions safely and efficiently despite certain defects or damage. This approach is crucial to ensure the continued and safe operation of industrial assets, from petrochemical facilities to critical infrastructure. Fitness for service (FFS) evaluates the remaining resistance of the equipment in its current operating condition, which may be degraded from its original conditions.
The FFS includes the evaluation of various damage mechanisms, among others, such as thinning due to metal loss, pitting, Hydrogen damage (HIC, blisters, SOHIC), cracks, laminations, among others. The characterization of the defects determined by non-destructive testing techniques and the design, construction, operation and maintenance information, provide information for the evaluation by FFS, obtaining the results for appropriate decision making, to define whether damaged equipment can be be put into service, continue operating or replaced.
Importance of fitness for service
The importance of fitness for service lies in its ability to extend the life of assets and reduce costs associated with premature replacement. By allowing engineers to evaluate the suitability of a component rather than simply replacing it, substantial savings can be realized. Additionally, FFS contributes to operational safety by identifying and addressing potential problems before they become catastrophic failures.
The level of risk due to explosions, leaks and unexpected shutdowns of equipment in processing, transport and storage facilities for pressurized liquids and gases is high for the safety of the facility and personnel; it is important to reduce these risk levels. Design codes and standards are intended to ensure safe operation of new construction equipment, but do not guarantee component service against deterioration or damage generated by service.
The fitness for service methodology per API 579-1/ASME FFS-1 [1] can be used to evaluate these components for deterioration or service damage. Aside from the safety benefits in the facility from fitness for service damage assessment, there are economic benefits by reducing unexpected equipment stoppages, which have great economic implications in terms of production losses.
API 579-1 Regulation
The API 579-1 regulation has become a reference standard in the field of FFS. Developed by the American Petroleum Institute (API), it provides detailed guidelines for performing fitness-for-service evaluations consistently and reliably. Familiarizing yourself with these regulations is essential for those looking to work in API-regulated industries.
Fitness applications for service
The applications of fitness for service are broad and cover various industries. For reliability professionals, understanding these applications can open up opportunities in sectors such as oil and gas engineering, the chemical industry, power generation, and more. Some of the common applications include the evaluation of pressure vessels, pipes, metal structures and various equipment.
FFS evaluation procedures may be used for evaluations of equipment designed and built to the following codes:
- ASME B&PV Code, Section VIII Div. 1
- ASME B&PV Code, Section VIII Div. 2
- ASME B&PV Code, Section I
- ASME B31.1
- ASME B31.3
- ASME B31.4
- ASME B31.8
- ASME B31.12
- API STD 650
- API STD 620
- API STD 530
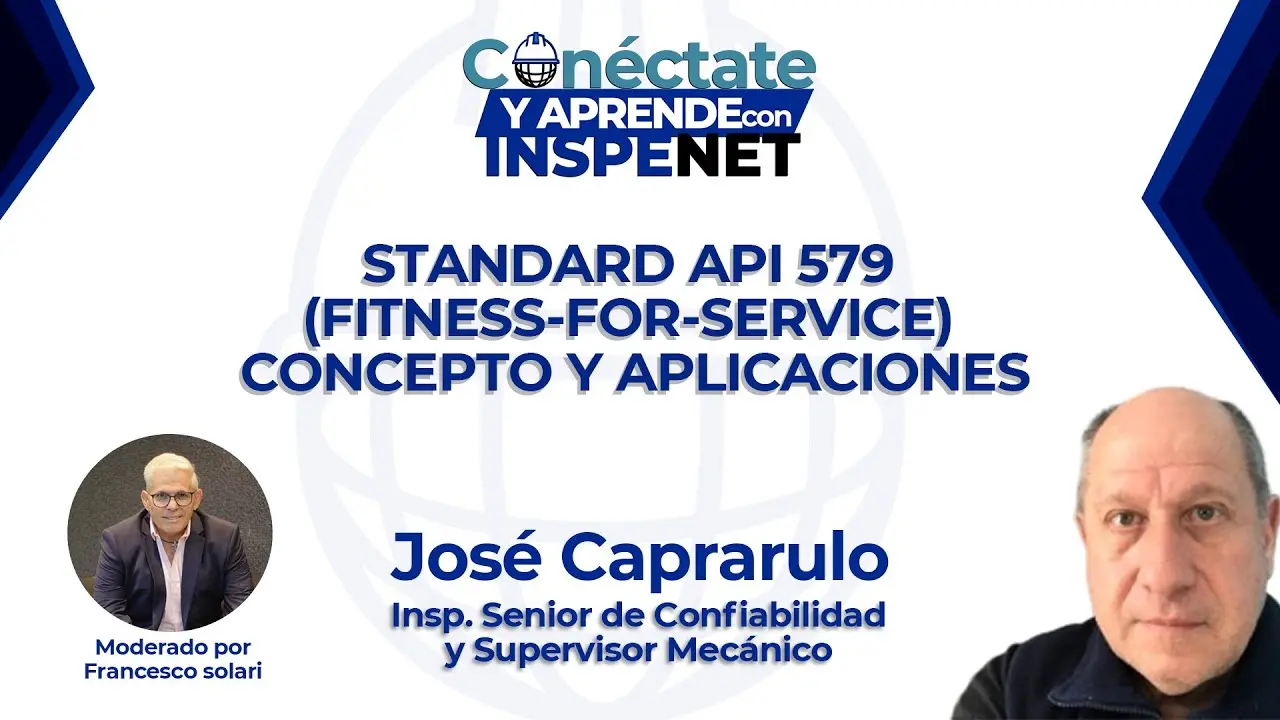
API 579-1 Standard (Fitness for Service), Concept and Applications
FFS Fitness for Duty Evaluations: A Multidisciplinary Team
Fitness-for-service evaluations are performed through a combination of structural analysis, engineering calculations, and material integrity considerations. It is essential to understand the nature of the damage or defect and evaluate its impact on the functional capacity of the component. This involves not only evaluating the geometry of the damage, but also considering factors such as operating load, temperature and environmental conditions.
A typical evaluation by FFS (Fitness For Service) involves various engineering disciplines and requires the collection of data from different sources or areas of knowledge, some of these areas of knowledge that can be part of an evaluation by FFS are those described below. continuation.
Stress analysis
An approximate estimate of the stresses acting on the component of interest is necessary to evaluate the structural integrity and remaining life.
Materials engineering/metallurgy
The performance of different materials subject to specific environments, as well as the temperature and stress levels that they resist, are essential to guarantee safe and reliable operation.
Mechanical Integrity
Detected damage must be carefully characterized by non-destructive testing before it is evaluated. The most appropriate inspection technology depends on a variety of factors, including the type of defect or damage present and the accessibility of the area of interest. An evaluation of the mechanical integrity of the findings is carried out using the applicable codes.
Corrosion
Knowledge of environmental damage mechanisms is a prerequisite for evaluation. This knowledge is useful for recommending appropriate remedial measures.
Process engineer
Interaction with plant personnel is of utmost importance to understand the operation of the equipment of interest. Temperature information, pressures, operating cycles, and process currents are key data for evaluation by FFS.
FSS application procedure
Identification of the defect and/or damage mechanism
The first step in a fitness for service evaluation is the identification of the type of damage and the cause that causes it. Design and manufacturing practices, as well as service history and environmental conditions can be used to determine the probable causes of damage. Identification of the defect and/or damage mechanism leads to the selection of the evaluation procedure.
Applicability and limitations of each evaluation procedure
The fitness for service methodology is applicable to evaluate equipment that is in service such as pressure vessels, pipes, boilers, storage tanks and components such as flanges and nozzles. Each procedure has a scope of application that the FFS analyst must be clear about to determine the application of the methodology.
Data requirements
The data required for a fitness for service evaluation depends on the type of defect or damage mechanism being evaluated. Required data could include: original design of the equipment, information pertinent to maintenance and operational history of the equipment, expected future operation, and specific information such as defect sizing, stress status, and material properties. For the interpretation and sizing of the defect or damage, the necessary inspection techniques must be applied that present the greatest possible information for the evaluation.
To detect superficial or subsurface damages or defects, techniques such as visual inspection, penetrating liquids, magnetic particles, among others, can be used. To characterize the depth and configuration through the thickness of the defect or damage, industrial ultrasound, radiography or other volumetric inspection techniques can be applied. The personnel who carry out these characterizations must have extensive experience in damage identification and characterization.
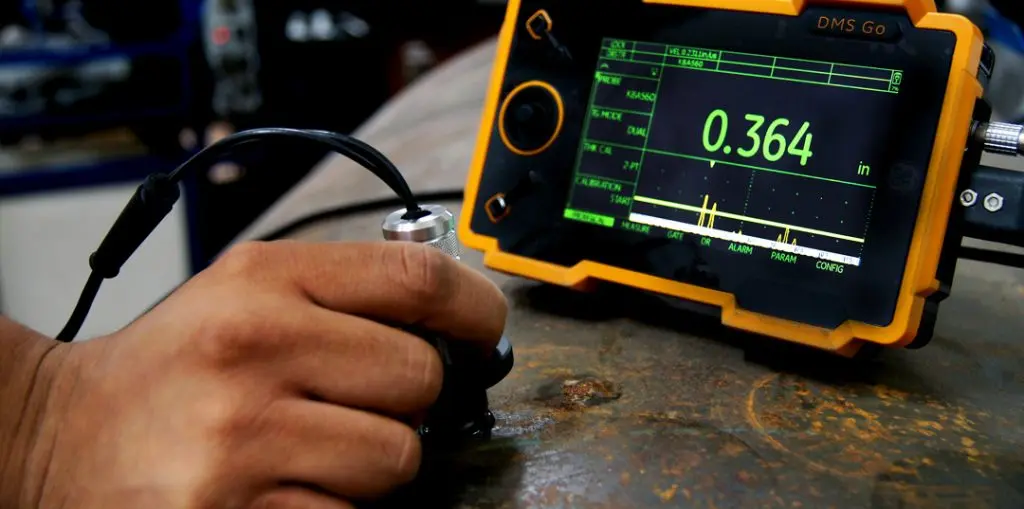
Evaluation level and acceptance criteria
The fitness for service methodology per API 579-1/ASME FFS-1 includes three levels of evaluation for defects or damage. Each level of assessment provides a balance between conservative and non-conservative analysis, the amount of information required for the assessment, the skill of the staff performing the assessment, and the complexity of the analysis being performed. The level of complexity, as well as the amount of information and personnel skill required for the evaluation, increases with increasing level of evaluation.
The levels of evaluation (level 1, level 2, and level 3) provide a balance between conservationism, the amount of information required for the evaluation, the skill of the personnel performing the evaluation, and the complexity of the analysis being developed.
- Level 1: This level of evaluation provides the most conservative criteria that can be used with the least amount of information about the component, in addition to the fact that the personnel who perform the evaluation can be inspection personnel or plant engineers.
- Level 2: This level provides a more detailed evaluation, so it provides more accurate results than the level 1 evaluation. The staff performing the level 2 assessment may be a plant engineer or specialist engineer with more experience and knowledge in developing level 2 assessments.
- Level 3: It is a more detailed and more precise evaluation than the level 2 evaluation; requires more detailed inspection information and component information. In the level 3 evaluation, analysis procedures based on numerical techniques such as finite elements and/or materials tests are recommended. The personnel carrying out the evaluation must be a specialist engineer with extensive experience and knowledge in FFS evaluations.
Remaining life evaluation
Remaining life is established once the defective component has been determined to be acceptable following fitness for service evaluation and is used to establish an appropriate inspection interval, an in-service monitoring plan, or the need for remediation. It is not intended to provide a precise estimated time to failure of the component with the defect.
Remediation
In some circumstances where the component is not accepted in its current condition, or where it is difficult to estimate a remaining life or as a means to mitigate the growth of damage, it is necessary to have remedial alternatives that can maintain or restore the component in service. The remeasurement alternative will depend on the type of damage present, which may range from the application of organic coatings, epoxies, reinforcement patches, reclassifications and/or repairs, to the replacement of the component.
In-service monitoring
Typical methods used for in-service monitoring include corrosion testing to determine corrosion rate, testing to evaluate hydrogen activity, measurement of growth in metal loss or cracking activity by ultrasonic examination methods, and acoustic emission testing. , among others.
Documentation
To develop a fitness for service evaluation, as much information as possible must be collected on the design, process and maintenance history of the component under evaluation. This same information, as well as that generated by the evaluation methodology (field readings obtained by NDT, maintenance, remaining life calculations, pressure and temperature conditions, remediation and monitoring recommendations, among others), must be sufficiently documented such that the analysis can be repeated later and a component evaluation file can be integrated.
Conclusion
In the world of engineering and asset management, Fitness for Service Assessments (FFS) stand as a fundamental pillar to ensure the longevity and operational efficiency of equipment and facilities. These assessments, at their core, represent a proactive approach to maintaining structural integrity in industrial environments. From damage identification and analysis to risk assessment, each phase contributes to informed decision making. In this article, we will thoroughly explore the complex world of fitness for service , highlighting its importance, applications and key considerations, including the relevance of the API 579-1 regulation.
References
- ÁNGEL M. PEREZ SARMIENTO, JUAN A. LARA MAGALLANES, JESÚS H. GARCIA ORTIZ. Application of the Fitness For Service Methodology to an Acid Gas Discharge Separator; Consulted on December 11, 2023; https://www.ndt.net/article/panndt2011/papers/140_Perez%20Sarmiento.pdf
- INSPENET: API RP 579-1/ASME FFS-1: Fitness-For-Service; Consulted on December 12, 2023; https://inspenet.com/articulo/api-rp-579-1-asme-ffs-1-fitness-for-service/
- INSPECT. Fitness for Duty Assessment FFS API 579; Consulted on December 12, 2023; https://www.inspectra.com.bo/images/recursos/ingineering-and-inspection.pdf