Table of Contents
- Introduction
- History and evolution of Finite Element Analysis
- Basic principles of the Finite Element Method
- Finite Element Analysis (FEA) Applications
- Finite Element Simulation Software (FEM)
- Benefits of Finite Element Analysis (FEA) in modern engineering
- Common errors in Finite Element Simulation (FEA) and how to avoid them
- Case studies
- Future of Finite Element Analysis (FEA) in Engineering
- Conclusions
- References
Introduction
Finite Element Analysis (FEA) is a computational technique that decomposes a complex problem into smaller, more manageable parts called Finite Elements. Each element is analyzed individually to predict how the system will react under various physical conditions. In the oil and gas industry, FEA is essential for analyzing and optimizing complex structures such as offshore platforms, pipelines, and drilling rigs.
In modern engineering, especially in the oil and gas sector, Finite Element Analysis has become an indispensable tool due to its ability to provide accurate and detailed results. It allows engineers to optimize designs, improve safety, and reduce costs by anticipating problems prior to fabrication or construction. FEA not only saves time and resources but also contributes to faster and more efficient innovations.
History and evolution of Finite Element Analysis
The Finite Element Method (FEM) has its roots in the 1940s, when aerospace engineers were seeking solutions to complex elasticity and structural problems. In 1956, researchers Ray W. Clough and John H. Argyris published seminal papers that formalized the method and made it accessible to a wider range of engineering applications, including the oil and gas industry.
With the advancement of computer science in the 1960s and 1970s, FEM rapidly expanded into other disciplines, including fluid dynamics and heat transfer, areas of great relevance to the oil and gas industry. The increasing capability of computers made it possible to solve more complex and detailed models.
Today, FEM is a standard tool in modern engineering, used not only in the oil and gas sector, but also in industries such as automotive, aerospace, and civil. Its continued evolution is marked by integration with emerging technologies such as artificial intelligence and machine learning, promising even more accuracy and efficiency in the future.
Basic principles of the Finite Element Method
The Finite Element Method (FEM) is based on the division of a complex problem into smaller, more manageable pieces called elements. These elements can be of various shapes and sizes, such as triangles, squares or tetrahedrons. The points where the elements are connected are called nodes. Each element and node is defined by mathematical equations that describe its behavior under specific conditions.
In the oil and gas industry, detailed meshes are used to model structures such as offshore platforms, subsea pipelines and drilling components. The mesh is a set of elements and nodes that model the problem domain. Creating an appropriate mesh is critical to the accuracy of the analysis, as a mesh that is too coarse may not capture the necessary details, while a mesh that is too fine may be computationally expensive.
Watch the following video to help you understand this methodology. Source: The Efficient Engineer.
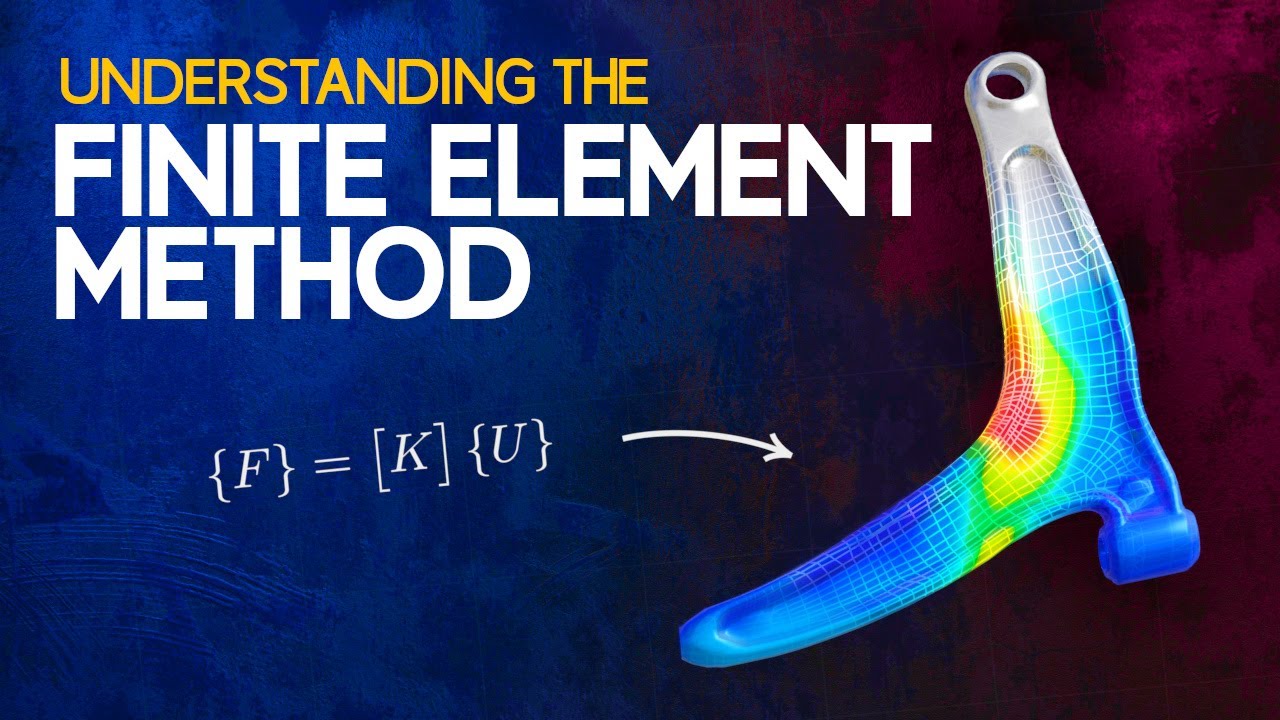
Método de los Elementos Finitos.
In the context of FEM, a coarse mesh refers to a mesh with a smaller number of large elements, which can simplify the model and reduce computational time, but may not capture all the details of the system behavior. On the other hand, a fine mesh has a larger number of small elements, which increases the accuracy of the analysis by capturing more details, but also significantly increases the time and computational resources required to solve the problem.
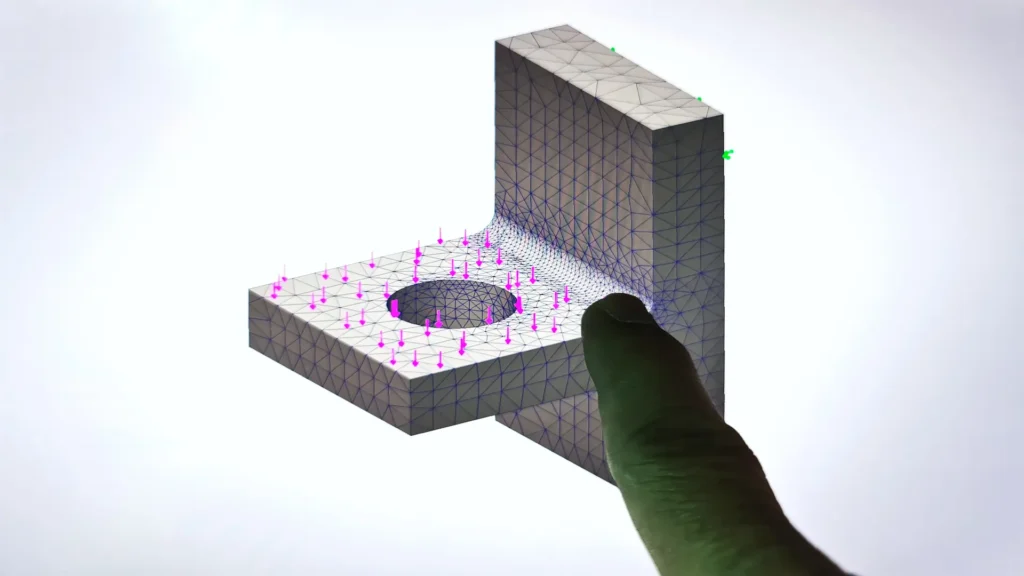
Finite Element Analysis (FEA) Applications
Finite Element Analysis (FEA) is used to solve a wide variety of engineering problems, providing an in-depth understanding of the behavior of structures and systems under various conditions.
In the automotive industry, FEA is used for collision analysis, chassis design optimization, and component durability evaluation. In the aerospace industry, it is used to simulate the behavior of aircraft and spacecraft under different aerodynamic and thermal loads, ensuring the safety and efficiency of designs.
In the civil sector, FEA is fundamental to the analysis of structures such as bridges, buildings, and dams, helping engineers to predict how these structures will behave under static and dynamic loads. In the oil and gas industry, FEA is applied to optimize the design of offshore platforms, subsea pipelines, and drilling rigs, ensuring their integrity and operational efficiency under extreme conditions.
FEA is also used in the biomedical industry to design prostheses and medical devices, in the electronics industry to analyze the thermal behavior of components, and in renewable energy to optimize the design of wind turbines and solar panels.
Finite Element Simulation Software (FEM)
There are several leading software packages available on the market to perform FEM simulations, each with its own features and advantages.
- ANSYS is one of the best-known and most widely used, offering a wide range of solutions ranging from structural mechanics to fluid dynamics and electromagnetics. Its intuitive interface and ability to handle complex models make it ideal for large-scale projects in a variety of industries.
- Abaqus is another prominent software, known for its ability to perform nonlinear and contact analysis, which makes it especially useful in the automotive and aerospace industries. Abaqus is valued for its robustness and accuracy in simulating complex behaviors, such as impact and advanced material behavior.
- COMSOL Multiphysics excels in its ability to perform multiphysics simulations, allowing engineers to model and solve problems involving multiple physical phenomena in a coupled manner. This is particularly beneficial in applications where the interaction between different types of analysis is critical, such as in the electronics and renewable energy industries.
Each of these software packages offers specific advantages that make them suitable for different types of Finite Element Analysis. The choice of software depends on the specific requirements of the project and the characteristics of the problem to be solved.
Benefits of Finite Element Analysis (FEA) in modern engineering
Finite Element Analysis (FEA) offers numerous advantages in modern engineering. One of the main ones is the accuracy in predicting the behavior of structures and systems under various conditions. This allows engineers to identify and solve potential problems before they occur, resulting in improved safety and reliability of designs.
Another significant advantage is efficiency. FEA allows engineers to optimize their designs, reducing the time and costs associated with developing physical prototypes. This not only speeds up the development process, but also minimizes the risk of costly failures during the production phase.
In addition, Finite Element Analysis facilitates innovation by allowing the exploration of new ideas and materials. Engineers can simulate different scenarios and evaluate the impact of various variables without the need for expensive physical experiments. This encourages a more creative and experimental approach to design and engineering.
Finally, the flexibility of FEA allows its application in a wide range of industries, from automotive to biomedical, demonstrating its versatility and ability to address modern engineering challenges.
Common errors in Finite Element Simulation (FEA) and how to avoid them
Despite its advantages, Finite Element Analysis (FEA) simulation can be subject to common errors that can compromise the accuracy of the results. One of the most frequent errors is the creation of an inadequate mesh. A mesh that is too coarse may not capture the necessary details of the model, while a mesh that is too fine may be computationally expensive and difficult to handle. To avoid this, it is crucial to find a proper balance and use mesh refinement techniques in critical areas.
Another common error is the incorrect definition of boundary conditions and applied loads. An inaccurate representation of real-world conditions can lead to erroneous results. Engineers must ensure that these conditions accurately reflect the operating environment of the system under study.
Incorrect selection of materials and physical properties can also be problematic. Using inaccurate or unrepresentative material data can lead to erroneous conclusions about system behavior. It is vital to use accurate and up-to-date material properties.
To avoid these errors, it is advisable to cross-validate with experimental results and to use high-quality FEM software that offers advanced tools for model verification and validation.
Case studies
An outstanding case of the use of FEA is the design of the Gjøa offshore platform in the North Sea. This project, carried out by TechnipFMC, involved detailed simulation of loads and stresses under extreme conditions. Using FEA, engineers were able to optimize the platform structure to withstand cyclonic forces and strong sea currents, ensuring its integrity and operational safety. The results showed a significant reduction in the weight of the structure without compromising its strength, leading to a decrease in fabrication and erection costs.
Another example is the analysis of a subsea pipeline used in the transfer of natural gas. Using software such as ANSYS, engineers were able to simulate the behavior of the pipeline under various pressures and temperatures. The simulations helped identify critical stress points and design specific reinforcements, improving the life of the pipeline and reducing the risk of failure.
These case studies demonstrate how FEA can lead to safer, more efficient, and cost-effective engineering solutions.
Future of Finite Element Analysis (FEA) in Engineering
The future of Finite Element Analysis (FEA) in engineering is marked by integration with emerging technologies such as artificial intelligence (AI) and machine learning. These technologies promise to improve the accuracy and efficiency of simulations by automating mesh creation and design optimization.
In addition, increased computational capacity will enable more detailed and complex simulations to be performed in less time. The use of advanced materials and 3D printing is also expected to drive new applications of FEA in a variety of industries, from automotive to biomedical.
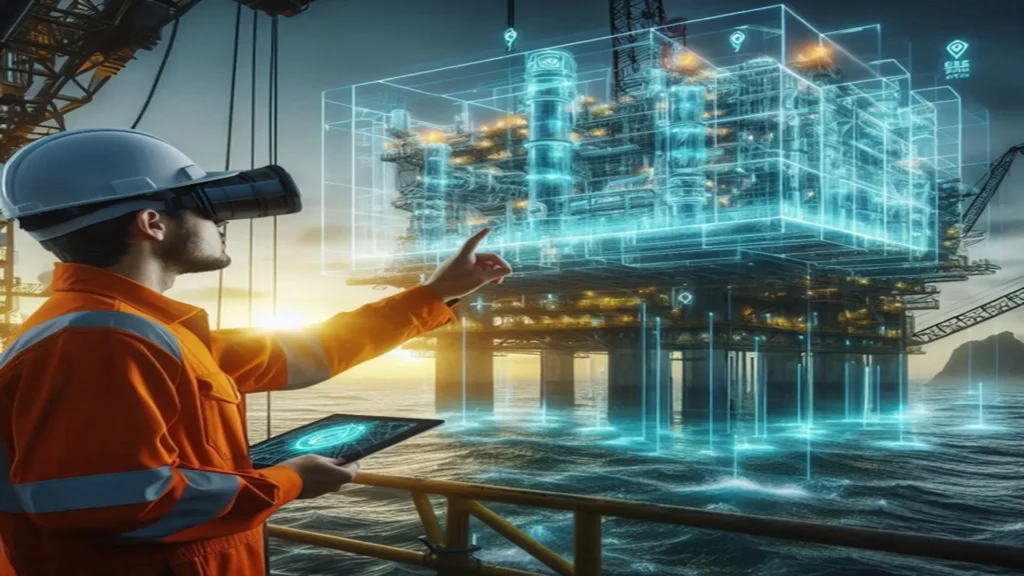
Conclusions
Finite Element Analysis (FEA) has revolutionized modern engineering, providing a fundamental tool in the analysis and optimization of designs in different industries. In the oil and gas sector, FEA has enabled significant advances in the safety and efficiency of offshore platforms, subsea pipelines, and drilling rigs by transforming complex problems into manageable elements, leading to greater accuracy in predictions and identification of potential failures prior to construction.
The integration of FEA with emerging technologies such as artificial intelligence and machine learning promises an even brighter future by automating critical processes, improving the accuracy of simulations, and accelerating the development of innovations. Case studies on offshore platforms and subsea pipelines underscore the importance of FEA in creating safer and more cost-effective engineering solutions.
With the continuous advancement in computational capabilities and the use of advanced materials, FEA will continue to be a fundamental pillar in engineering, driving innovation and efficiency in complex projects globally. In short, FEA is not only a powerful tool, but also a guarantee of accuracy, safety, and success in modern engineering.
References
Own source