Table of Contents
- Introduction
- Principles of Magnetic particle Testing (MT)
- Importance of MT in Non-Destructive Testing (NDT)
- Magnetization: Fundamentals and techniques
- New developments in advanced Magnetic Particle Testing (MT) equipment
- Standards governing Magnetic Particle Testing (MT)
- ASNT's role in the development of advanced Magnetic Particle Testing (MT) technologies
- Benefits of new technologies in Magnetic Particle Testing (MT)
- Practical applications and success stories
- Key sectors for the use of Magnetic Particles (MT)
- Success stories with advanced equipment
- Case 1: Airbus improves defect detection in aerospace components
- Results
- Case 2: General Motors optimizes production with automated systems
- Results
- Case 3: Petrochemical Industries Company detects early corrosion in pipes
- Results
- Case 4: Siemens Energy integrates artificial intelligence in inspections
- Result
- Future of Magnetic Particle Testing
- Conclusions
- References
Introduction
Magnetic Particle Testing (MT) is a Non-Destructive Testing (NDT) technique used to detect surface and near-surface defects in ferromagnetic materials. This method is essential to ensure structural integrity in critical components across industries such as aerospace, automotive, and heavy manufacturing, where high standards of quality and safety are indispensable.
In recent years, Magnetic Particle Testing has undergone significant technological advancements. New tools, such as high-resolution sensors, energy-efficient electromagnets, and fluorescent particles, have enhanced the precision and sensitivity of the process, enabling the detection of smaller defects and optimizing inspections even under challenging conditions.
This article addresses key questions to understand the impact of these innovations, such as:
- What are the latest advancements in equipment for Magnetic Particle Testing?
- What benefits do these technologies offer to improve inspections?
- What standards govern this type of testing, and how does regulatory compliance ensure consistency and safety?
As we explore these questions, we will uncover how inspection technologies are redefining quality and efficiency in the application of Magnetic Particle Testing.
Principles of Magnetic particle Testing (MT)
What is Magnetic Particle Testing (MT)?
Magnetic Particle Testing is a specialized method for identifying surface or near-surface discontinuities in ferromagnetic materials. The process involves three main steps:
- Material magnetization: A magnetic field is applied to the component using direct or alternating electrical current, electromagnets, or induction coils.
- Application of Magnetic Particles: Visible or fluorescent particles are dispersed on the magnetized surface. These particles accumulate at defects, forming a visible indication.
- Visual Inspection: Accumulated particles are observed with the naked eye or under ultraviolet light in the case of fluorescent particles, allowing the detection of cracks, fissures, or other irregularities.
Adherence to regulatory compliance ensures that these steps meet industry standards, providing consistent and reliable results. This method is renowned for its ability to rapidly and accurately identify defects in welds, machined parts, and critical components without damaging the inspected material.
To learn more about Magnetic Particle Testing, magnetization and types of magnetization I invite you to watch the following video courtesy of: DG E LEARING ADU ACADEMY.
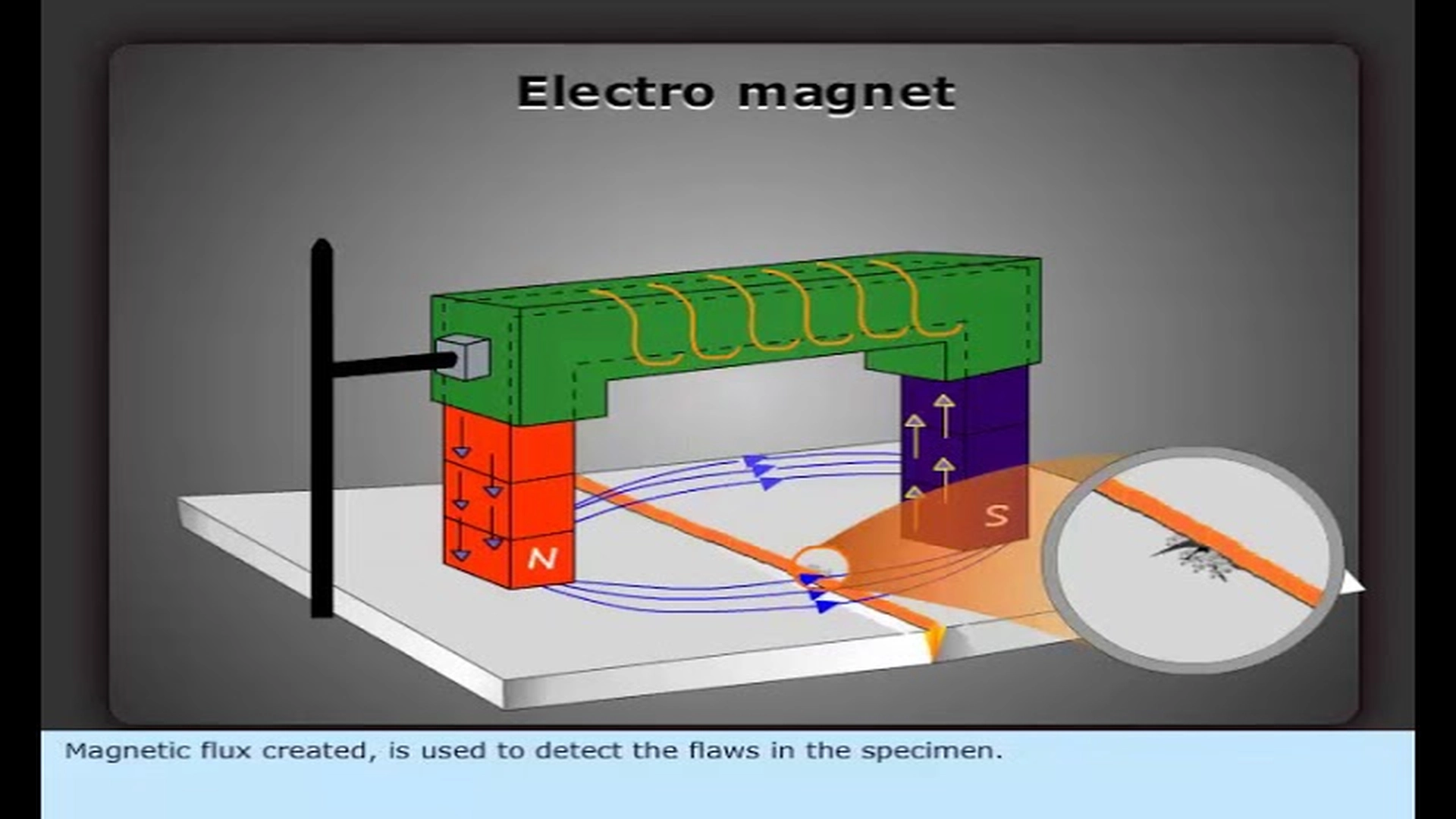
Magnetic Particle Testing.
Importance of MT in Non-Destructive Testing (NDT)
Magnetic ParticleTesting is a cornerstone of NDT, particularly in industries where safety and reliability are paramount:
- Aerospace: Inspection of landing gear and critical parts exposed to extreme loads.
- Automotive: Detection of cracks in shafts and gears, ensuring vehicle functionality.
- Heavy manufacturing: Quality control of welds and structures under high stress.
Through this test, surface defects are detected, avoiding catastrophic failures, which translates into reduced repair costs and quality in the manufacturing and maintenance processes.
Magnetization: Fundamentals and techniques
Magnetization is the foundation of Magnetic Particle Testing. There are two main methods for generating the magnetic field:
- Longitudinal magnetization: The magnetic field is generated along the component’s axis, ideal for detecting defects perpendicular to the field direction.
- Circular magnetization: Produces a magnetic field that surrounds the component, suitable for detecting radially aligned defects, as shown in Figure1.
To apply these methods, tools such as the following are used:
- Electromagnets: Versatile devices that allow adjustment of magnetic field intensity according to the size and geometry of the component.
- Induction coils: Generate strong and homogeneous magnetic fields, ideal for inspecting large or complex-shaped parts.
The selection of the magnetization method depends on the type of component and the defects expected to be found. These techniques ensure that Magnetic Particle Testing remains an essential tool for inspecting ferromagnetic materials.

New developments in advanced Magnetic Particle Testing (MT) equipment
These testing has evolved significantly with the development of technologies that increase the accuracy, efficiency and adaptability of inspections. Below, we explore the major innovations in modern equipment.
High-resolution sensors
High-resolution sensors have revolutionized the ability of equipment to detect micro-defects that previously went undetected. Through these devices, it is possible to identify extremely small surface cracks, increasing the reliability of the results.
How do they work?
- Data capture
- The sensor takes detailed images or digital records of the inspected area.
- For instance, if a component has a small crack, the sensors accurately detect the concentration of Magnetic Particles in that spot.
- Real-time analysis
- The sensors send the captured data in real time to a computer or analysis system.
- This enables rapid inspection of large surfaces with less manual intervention and greater detail.
Key advantages
- Advanced detection: Capable of identifying microscopic defects, reducing error margins, and providing more detailed analysis.
- Operational efficiency: Modern sensors can operate in real time, speeding up inspections and ensuring digital recording of results for later analysis.
Real equipment examples
- Magnaflux ZB-100F UV Light System: This system uses ultraviolet light combined with sensors to enhance the visibility of fluorescent particles.
- Karl Deutsch DEUTROFLUX UWS: A comprehensive MT testing system with high-resolution digital sensors for inspecting complex components.
These sensors are especially useful in industries such as aerospace and automotive, where precision standards are exceptionally high.
Innovations in fluorescent particles
Next-generation fluorescent particles are designed to offer better adhesion to defects, improving visibility under ultraviolet (UV) light. These particles enable more precise inspections, even under limited lighting conditions or on complex geometries.
Benefits highlights
- Enhanced adhesion: Their advanced design ensures particles concentrate exclusively on magnetic discontinuities, minimizing false positives.
- Versatility: Suitable for irregularly shaped parts or complex materials, increasing inspection reliability.
Fluorescent particles are particularly effective in critical applications, such as inspecting landing gear or automotive transmission components, where even a small defect can compromise safety.
Next-generation electromagnets
Modern electromagnets are designed to provide an optimal balance between power and energy efficiency, enabling uniform magnetization even in large or irregularly shaped components.
Advanced features
- Higher power: Capable of generating intense magnetic fields with reduced energy consumption, lowering operational costs.
- Adjustable configurations: Allow adaptation of magnetic field intensity based on the size, material, and geometry of the inspected component.
These electromagnets are ideal for high-precision inspections in demanding industrial applications, such as pressure vessels or structural components.
Notable equipment: Magnaflux and other leading brands
Magnaflux continues to be a leader in the market, offering portable, high-performance Magnetic Particle Testing equipment. Its systems are known for their functionality, portability and compatibility with fluorescent particles, making them ideal for field and laboratory inspections.
Other notable brands
- Competitors such as Parker Research and Karl Deutsch offer innovative solutions that include automated configurations and integrated sensors, expanding the possibilities of Magnetic Particle Testing.
These brands lead the industry, providing reliable tools to meet the most demanding standards.
Standards governing Magnetic Particle Testing (MT)
Compliance with regulations is critical to ensure the quality and safety of non-destructive Magnetic Particle Testing. The following are the main applicable rules and regulations:
Main international standards
a) ASTM E1444/E1444M: Establishes standard procedures for performing Magnetic Particle Testing on ferromagnetic materials. It includes guidelines on component preparation, magnetization, and defect evaluation.
b) ISO 9934: This international standard provides specific requirements to ensure the safety and accuracy of Magnetic Particle Testing, covering everything from equipment to the particles used.
c) ASME BPVC Section V: Primarily applied in the pressure vessel and boiler industry, this section establishes technical requirements for inspecting critical components using MT.
Sector-specific regulations
a) Aerospace: The NAS 410 standard regulates the certification of NDT technicians, including Magnetic Particle Testing. It requires advanced competencies to ensure accuracy in critical parts such as landing gear and structural components.
b) Automotive: Original Equipment Manufacturers (OEMs) implement internal standards for quality control, ensuring that parts like shafts and gears meet rigorous specifications.
Importance of regulatory compliance
Compliance with standards such as ASTM E1444/E1444M, ISO 9934 and ASME BPVC Section V ensures quality inspections, and supports regulatory compliance by aligning practices with internationally accepted guidelines.
Key advantages
- Quality assurance: Certifies that inspection processes meet the highest standards.
- Risk reduction: Prevents catastrophic failures and ensures the reliability of final products.
- Environmental compliance: For example, the use of specific fluorescent particles helps meet EPA (Environmental Protection Agency) regulations, reducing the environmental impact of industrial operations.
Regulatory compliance is essential to maintaining competitiveness and ensuring trust in inspection processes.
ASNT’s role in the development of advanced Magnetic Particle Testing (MT) technologies
The American Society for Nondestructive Testing (ASNT) has been a key player in the advancement of nondestructive testing (NDT), including Magnetic Particle Testing (MT). Its work focuses on setting global standards, and driving technological innovation and strengthening professional competencies in this critical area.
Promoting technological innovation
Through specialized publications, conferences, and technical symposia, ASNT creates spaces for manufacturers, researchers, and end users to collaborate on improving MT equipment, such as those mentioned in this article. This technical exchange has been instrumental in developing more precise tools, such as high-sensitivity fluorescent particles, adjustable electromagnets, and high-resolution sensors.
Establishing global standards
ASNT is responsible for issuing essential standards such as SNT-TC-1A, which defines requirements for training and certifying technicians specializing in MT. This standard ensures professionals are trained to operate the most advanced equipment, guaranteeing consistent and reliable inspections.
In addition, ASNT works closely with international organizations such as ISO (International Organization for Standardization) to align inspection best practices globally. This approach fosters interoperability and ensures that testing techniques meet the highest quality standards in regulated industries.
Training and certification
ASNT has also been crucial in professionalizing NDT technicians. Through training courses, certification programs, and educational materials, it has elevated the quality of inspections by equipping specialists to effectively implement advanced technologies.
ASNT is more than a regulatory body: it acts as a driver for technological and professional transformation in Magnetic Particle Testing.
Benefits of new technologies in Magnetic Particle Testing (MT)
Technological advancements in equipment for non-destructive testing with Magnetic Particles (MT) have transformed the way inspections are conducted, offering key benefits that enhance precision, efficiency, and adaptability across a variety of industrial applications.
Enhanced sensitivity
Innovations in high-resolution sensors and fluorescent particles enable the detection of smaller defects, such as micro-cracks and incipient surface fissures. This increased sensitivity ensures more reliable inspections, reducing the likelihood of structural failures in critical components. This is particularly valuable in sectors like aerospace and heavy manufacturing, where even minor defects can have significant consequences.
Increased productivity
New automated systems and advanced sensors have significantly reduced the time required for inspections. Modern equipment allows for real-time analysis, eliminating the need for lengthy and repetitive procedures. For example, a high-resolution sensor can capture detailed images of defects in seconds, optimizing maintenance processes and reducing downtime in industrial plants.
Energy efficiency and sustainability
Current equipment is designed with a focus on sustainability. Low-energy consumption electromagnets and reusable Magnetic Particle reduce the environmental impact of inspections. Additionally, lower electricity consumption not only reduces operational costs but also helps meet increasingly stringent sustainability standards.
Greater reliability in demanding environments
New technologies are designed to operate in extreme conditions, such as high temperatures, high humidity, and corrosive environments. This enables Magnetic Particle Testing equipment to be effective even in challenging scenarios, such as petrochemical plants or heavy manufacturing industries. The robustness and adaptability of modern equipment ensure accuracy in any environment, increasing the reliability of inspections.
Practical applications and success stories
Key sectors for the use of Magnetic Particles (MT)
Magnetic Particle Testing has critical applications across various sectors:
- Aerospace: Inspection of landing gear and components subjected to high stress ensures structural integrity and in-flight safety.
- Automotive: Detects cracks in shafts, gears, and other transmission elements, guaranteeing the durability and performance of vehicles.
- Heavy manufacturing: Controls the quality of welds and large parts used in critical structures, preventing catastrophic failures during operation.
Success stories with advanced equipment
The implementation of advanced equipment for Magnetic Particle Testing has resulted in significant improvements across various industries. Below are real and verifiable examples that illustrate the impact of these technologies:
Case 1: Airbus improves defect detection in aerospace components
Airbus, one of the leading aircraft manufacturers worldwide, incorporated advanced Magnetic Particle Testing equipment featuring high-resolution sensors and next-generation fluorescent particles to inspect critical components like landing gear and structural parts1.
Results
- Increased precision: Successfully detected micro-defects and surface cracks that previously went unnoticed.
- Cost reduction: Lowered costs associated with repairs and unscheduled maintenance.
- Enhanced safety: Improved the reliability and safety of its aircraft, meeting strict international standards.
Case 2: General Motors optimizes production with automated systems
General Motors (GM) implemented automated Magnetic Particle Testing systems in its production lines, using high-resolution sensors and state-of-the-art electromagnets for the inspection of components such as axles and gears2.
Results
- Operational efficiency: Reduced inspection time by 30%, speeding up the production process.
- Improved quality: Reduced the number of rejected parts and rework, ensuring higher quality vehicles.
- Sustainability: Adopted energy-efficient equipment, reducing electricity consumption and environmental impact.
Case 3: Petrochemical Industries Company detects early corrosion in pipes
Petrochemical Industries Company (PIC), a petrochemical production company, faced challenges in detecting corrosion and cracks in its pipelines. By incorporating advanced equipment with fluorescent particles and adjustable electromagnets, it significantly improved its inspections3.
Results
- Leak prevention: Identified incipient defects, avoiding potential spills and economic losses.
- Increased safety: Significantly improved operational safety and compliance with environmental regulations.
- Maintenance optimization: Planned more effective preventive interventions, extending the useful life of its facilities.
Case 4: Siemens Energy integrates artificial intelligence in inspections
Siemens Energy adopted Magnetic Particle Testing systems equipped with artificial intelligence for the inspection of turbine and generator components4.
Result
- Analysis automation: Through the use of AI, results were interpreted automatically, reducing human error.
- Increased speed: Shortened inspection time by 40%, increasing equipment availability.
- Accurate documentation: Detailed and traceable reports were generated for audits and regulatory compliance.
These case studies demonstrate how the implementation of advanced technologies in Magnetic Particle Testing generates concrete benefits, optimizing defect detection, operational efficiency and regulatory compliance. Leading companies in their respective sectors have strengthened the quality of their products and services, thus consolidating their competitive advantage in the market.
Future of Magnetic Particle Testing
Technological innovations on the horizon
The future of Magnetic Particle Testing will be shaped by the integration of disruptive technologies:
- Analysis automation: Through the use of AI, results were interpreted automatically, reducing human error.
- Increased speed: Shortened inspection time by 40%, increasing equipment availability.
- Accurate documentation: Detailed and traceable reports were generated for audits and regulatory compliance.
Impact on the industry
The implementation of these technologies will reduce operational costs by optimizing inspection times and minimizing errors. Additionally, increased precision will ensure greater safety in inspected products, reinforcing consumer trust and compliance with industrial regulations.
Future challenges
Despite these advancements, significant challenges remain:
- Global standardization: International standards must be established to regulate the use of new technologies in Magnetic Particle Testing.
- Continuous training: Nondestructive testing (NDT) technicians must stay updated to operate more sophisticated equipment and interpret data generated by advanced systems.
Magnetic Particle Testing will continue to evolve, ensuring its relevance in an increasingly demanding and technologically advanced industry.
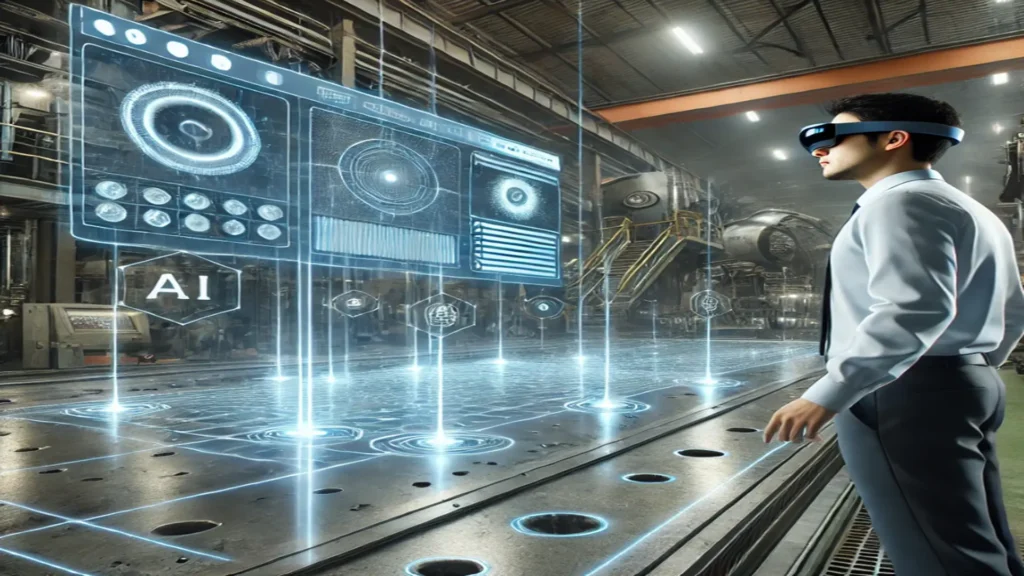
Conclusions
Magnetic Particle Testing has significantly evolved with the introduction of advanced technologies such as high-resolution sensors, next-generation fluorescent particles, and adjustable electromagnets. These innovations have enhanced precision and efficiency in defect detection for ferromagnetic materials. They have transformed inspections, enabling the identification of micro-defects with greater sensitivity, optimizing operation times, and ensuring more reliable results in critical sectors such as aerospace, automotive, and heavy manufacturing.
Compliance with international standards, such as ASTM E1444/E1444M, ISO 9934, and ASME BPVC Section V, not only ensures the quality of processes but also protects businesses from operational and legal risks, while strengthening consumer confidence and supply chains. Additionally, organizations like ASNT have played a vital role in standardizing practices, fostering technological innovation, and professionalizing NDT technicians, creating a safer and more efficient inspection environment.
Adopting these technological and regulatory advancements is not merely an option but a strategic necessity to remain competitive in an ever-evolving industry. Integrating advanced tools and committing to high-quality and safety standards are essential steps for success in a demanding global market.
The future belongs to those willing to lead change, and Magnetic Particle Testing will remain a cornerstone in this industrial transformation.
References
- Airbus Annual Report
- GM Sustainability Report
- PIC Annual Report
- Siemens Energy Press Releases