Non Destructive Testing (NDT) is a crucial component in the maintenance and equipment and pipeline service life in various industries. As the name implies, NDT involves inspecting and evaluating materials, components or assemblies without causing any damage. This method ensures that equipment remains operational and safe while extending its service life. This article explores the different types of NDT, their applications and their significant impact on the service life of equipment and pipelines.
NDT applied to the inspection of equipment and pipelines
In the inspection, monitoring and evaluation of equipment and piping in the different industrial branches, a great variety of non destructive testing techniques are applied. Among the main non-destructive testing methods, the following are mentioned.
Visual Inspection (VT)
Visual inspection is the most basic form of NDT and involves looking for surface defects such as cracks, corrosion or misalignment. Although simple, visual inspection is critical in identifying obvious problems before they become serious problems. Sometimes it may require instruments to observe in inaccessible areas, such as borescopes and videoscopes, and may even require vehicles to access the area of interest, such as crawlers or drones.
Ultrasound Test (UT)
Ultrasonic testing uses high frequency sound waves to detect internal defects in materials through their interaction with the component structure (reflection, attenuation, diffraction, among others). It is widely used for its accuracy in detecting both surface and subsurface defects. UT is particularly effective in identifying cracks, voids and inclusions within metals and composites, as well as in monitoring wall thicknesses in pipes, pressure vessels and storage tanks.
This is one of the most technologically advanced NDT methods in recent years, with advanced techniques such as TOFD, PAUT, FMC/TFM, PWI and PCI. Historically complex problems such as the detection of High Temperature Hydrogen Attack HTHA has found a reliable solution in Phase Coherence Imaging (PCI) technology. Figure 1 shows a B-Scan image (cross section) obtained through PCI with data collection and processing through Planar Wave Imaging (PWI)1.
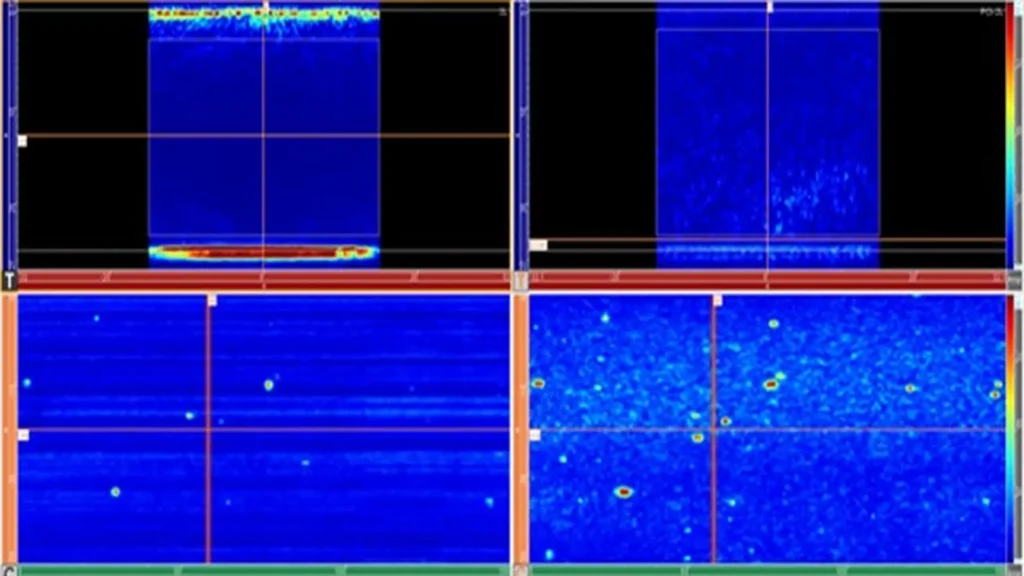
Radiographic Test (RT)
The radiographic test involves the use of X-rays or gamma rays that, due to their high energy, pass through the internal structure of the component, such as welds, tubes, valves, among others, incident this energy on a recording medium such as a radiographic film, which once processed, produce images of the internal structure of the evaluated component. This method is very effective for detecting internal defects such as voids, cracks and inclusions in welds, castings and other materials.
Magnetic Particle Testing (MT)
Magnetic particle testing is used to detect surface and near-surface discontinuities in ferromagnetic materials without necessarily being open at the surface. The process involves applying a magnetic field to the ferromagnetic material component and then spraying tiny magnetic particles onto it. The particles accumulate around the discontinuities, due to the leakage and entry of the magnetic field around the fault, becoming poles of a magnet, making them visible under suitable lighting conditions.
Penetrant Liquid Test (PT)
The liquid penetrant test method is used to detect surface defects in non-porous materials. The process involves applying a highly capillary liquid with a contrasting dye to the surface, which penetrates any open cracks or flaws in the surface. After a certain period of time, the excess liquid is removed and a white developer is applied to extract and contrast the dye from the penetrating liquid to the defects, making them visible and revealing the presence of the discontinuity.
Electromagnetic Eddy Current Testing (ECT)
Eddy current testing is used to detect surface and near-surface defects in conductive materials. This method involves inducing an eddy current in the conductive material and observing the impedance response of the circuit which results from the sum of the resistance of the inducing coil(s) and the reactance of the eddy currents on the probe coil(s). Changes in current flow cause a change in the impedance of the circuit, indicating the presence of discontinuities, which is displayed on a screen representing the impedance plane.
New techniques such as Eddy Current Array Sensing (ECA) and Pulsed Eddy Current Array (PECA) have expanded the application opportunities of the test. This technique also serves to evaluate and measure electromagnetic material properties such as conductivity.
Guided Waves Testing (GWT)
Guided waves are ultrasonic waves that propagate along a structure and are guided by its geometric boundaries. GWT is a technique for finding the location of the defect and estimating the size of the defect using the arrival time and amplitude of the ultrasonic signal, respectively. The operating frequency of GWT is usually low (5 to 250 kHz) compared to ordinary ultrasonic testing. The low frequency operation helps to generate non-dispersive ultrasonic guided waves and reduce attenuation for long-range pipeline inspection.
Acoustic Emission Testing (AET)
Acoustic emission testing is a non-destructive inspection method that uses the release of ultrasonic stress waves to identify defects in materials. These ultrasonic waves are not introduced from an external source, as in ultrasonic testing, but originate from within the material being inspected.
Infrared Thermography Test (IRT)
Infrared thermography is the process of collecting information from the infrared radiation spectrum of the energy emanating from the inspected component through the use of a thermographic camera and converting it into an image of the surface temperature distribution of the component. By means of infrared thermography, problems such as obstructions, internal refractory detachment, operation problems, among others, can be detected in pipes and equipment. Figure 1 shows a typical thermal graphic image in pipelines.
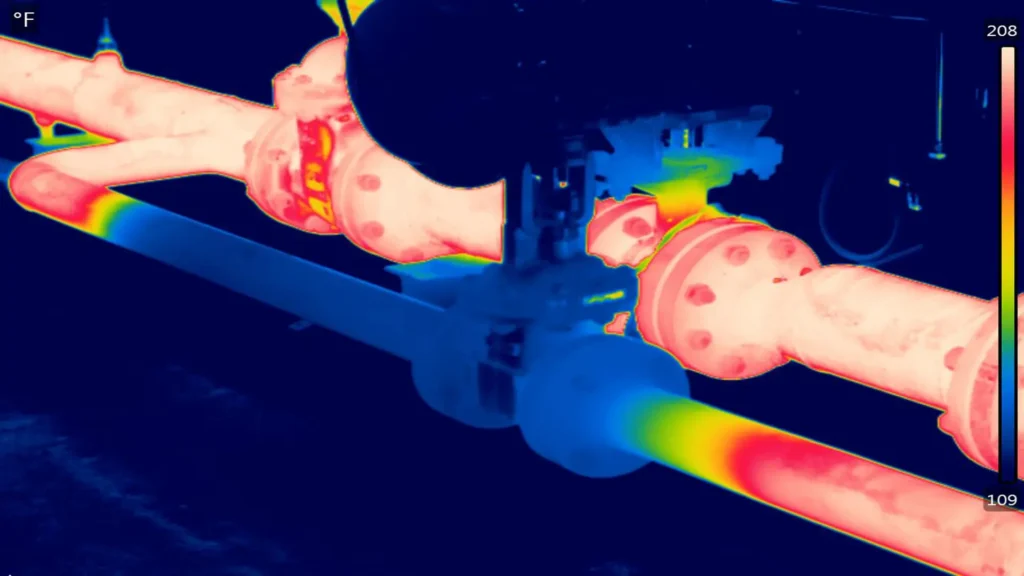
Non Destructive Testing Applications
Manufacturing industry
In industrial manufacturing, NDT is significant in quality control and quality assurance. Components such as gears, shafts and turbines are subjected to NDT to ensure that they meet the required standards. By detecting defects early in the manufacturing process, NDT helps reduce waste, save costs and ensure the reliability of the final product.
Oil and gas industry
The oil and gas industry relies heavily on pipelines to transport crude oil and natural gas, as well as pressure vessels during processing and storage equipment. NDT methods such as ultrasonic and radiography testing are used to inspect the integrity of pipelines, pressure vessels, boilers, storage tanks, among other equipment. By detecting corrosion, cracks and other defects, NDT helps prevent leaks and ruptures, thus avoiding damage to facilities and personnel, production downtime, environmental disasters and costly repairs.
The following video shows the importance of NDT in the oil industry. Source: Fujifilm NDT.

How is NDT used in the oil and gas industry?
Aerospace industry
In the aerospace industry, the safety and reliability of aircraft components are paramount. NDTs are widely used to inspect parts such as wings, fuselage and engines for signs of fatigue, cracks or corrosion. Regular NDT inspections ensure passenger and crew safety by preventing catastrophic failures.
Power generation
Power plants, whether nuclear, fossil fuel or renewable, rely on NDT to maintain the integrity of critical components such as boilers, pressure vessels, piping, turbines and generators. NDT helps identify potential problems before they lead to unplanned outages or accidents, ensuring a continuous and safe supply of energy.
Infrastructure and construction
In construction, NDTs are used to inspect the integrity of structures such as bridges, dams and buildings. Testing methods such as ultrasound and radiography are used to detect internal defects in concrete, steel and other materials. This ensures the safety and durability of structures, protecting lives and property.
Impact of NDT on equipment and pipelines
Extension of equipment and pipeline service life
One of the most significant impacts of NDT is the extension of the useful life of equipment and pipeline service life. By inspecting and detecting defects early through the implementation of inspection plans, maintenance work can be performed before minor problems become major issues. This proactive approach prevents premature failures and prolongs the operational life of assets.
Improved safety
Safety is paramount in industries where equipment failure can have catastrophic consequences. NDT improves safety by ensuring that components are free of defects that can cause accidents. For example, in the oil and gas industry, NDTs help prevent pipeline leaks that could lead to explosions and environmental damage with resulting economic losses.
The use of NDTs in industries can prevent catastrophic failures and identify and resolve disastrous problems, thus ensuring people’s lives2.
Downtime reduction
Unplanned downtime can be costly and disruptive. NDT helps identify potential problems before they lead to equipment failure, enabling planned maintenance. This reduces the likelihood of unexpected breakdowns and minimizes downtime, ensuring continuous, productive operation.
Cost savings
While the initial investment in NDT equipment and training can be significant, the long-term cost savings are substantial. By detecting defects early and performing timely maintenance, NDT reduces the need for costly repairs and replacements. They also help avoid fines and penalties associated with environmental incidents or regulatory non-compliance.
To maximize investments and reduce operational and maintenance costs, it is essential to perform proper NDT and inspections by appropriately qualified personnel during all stages of manufacturing, construction and operation of pipelines, pressure vessels, storage equipment, among others.
Improving reliability
Reliability is critical in all industries, where component failure can have serious consequences. NDT improves the reliability of equipment and pipelines by ensuring that they are free from defects that could lead to failure. This is particularly important in high stress environments where components are subjected to extreme conditions.
As a highly accurate and repeatable process, NDT can provide objective and reliable quality measurements. Rather than relying on visual inspection, NDT can provide images as evidence of structurally sound piping and equipment3.
Regulatory compliance
Industries today are subject to strict regulations regarding the safety and integrity of equipment and pipelines. NDT helps companies comply with these legal provisions by providing documented evidence of inspections and maintenance. This ensures that companies meet the required standards and avoid legal and financial penalties.
Conclusions
Non destructive testing (NDT) is fundamental for the optimization of maintenance and longevity of equipment and pipelines in different industries. Through the inspection and evaluation of materials, the safety and reliability of assets is guaranteed, which translates into a significant extension of the useful life of assets, reduction of downtime and savings in operating costs, significantly important in the efficiency and continuity of industrial operations.
In the context of Industry 4.0, where interconnectivity and automation are paramount, NDTs play an increasingly important role. Performing accurate and reliable inspections without disrupting operations is vital to meet new technological and operational challenges.
References
- https://blog.eddyfi.com/hs-fs/hubfs/PWI.png?width=999&height=430&name=PWI.png
- TWI GLOBAL. Why is NDT important?; Consultado en fecha 24 de junio de 2024. https://www.twi-global.com/locations/south-east-asia/faqs/why-is-ndt-important
- FUJIFILM. How Is NDT Used in the Oil Industry?; Consultado en fecha 24 de junio de 2024. https://ermak.com/common-metal-casting-defects/#:~:text=Core%20Shift%20%E2%80%93%20A%20core%20shift,cast%20at%20the%20parting%20line.