Table of Contents
- Introduction
- Importance of energy efficiency in industrial boilers
- How is the efficiency of a boiler determined?
- Efficiency analysis of industrial boilers
- Factors affecting boiler efficiency
- How to improve performance and energy efficiency in industrial boilers?
- Applications of new technologies in industrial boilers
- Conclusions
- References
Introduction
Today, industries face the problem of optimising energy use while minimising their environmental impact. At the heart of this objective is energy efficiency in industrial boilers, equipment designed to convert water into steam by combustion of fuels such as fossil, biomass or renewable sources.
This steam, generated at specific pressures, is used in different industrial processes, including power generation, refining, manufacturing, and heating. Optimising energy efficiency in industrial boilers ensures continuity of operations, reduces operating costs and minimises environmental impact. Operating boilers at optimal levels and with the correct load reduces fuel consumption and greenhouse gas emissions, which are key factors for industrial sectors.
The purpose of the article is to address the importance of energy efficiency in industrial boilers, outline the factors that affect their performance, and offer recommendations for improving performance and energy efficiency. It also explores the applications of new technologies in this specific field.
Importance of energy efficiency in industrial boilers
It is basically defined as the efficiency of the equipment during the process of converting the energy contained in the fuel needed to produce steam. For this reason, steam generation systems require the best possible use of the fuel used, with the aim of minimising thermal waste and consequently increasing energy efficiency.
From an economic perspective, the importance of maintaining the efficiency of this equipment is based on reducing operating costs through energy consumption, since the energy they consume represents a large part of the costs of production processes. In environmental terms, energy efficiency is related to improving the profile of greenhouse gas emissions by reducing the demand for fossil fuels for power generation. In addition, when boilers operate efficiently and perform the complete combustion process, energy consumption and thus pollutant emissions are minimised.
In water-tube boilers, a furnace heats the gas that circulates through the tubes containing water. The heat is transferred through the walls of the tubes, heating the water inside the tubes until steam is produced (Figure 1). Watertube boilers are designed to generate considerably more pressure than firetube boilers1.
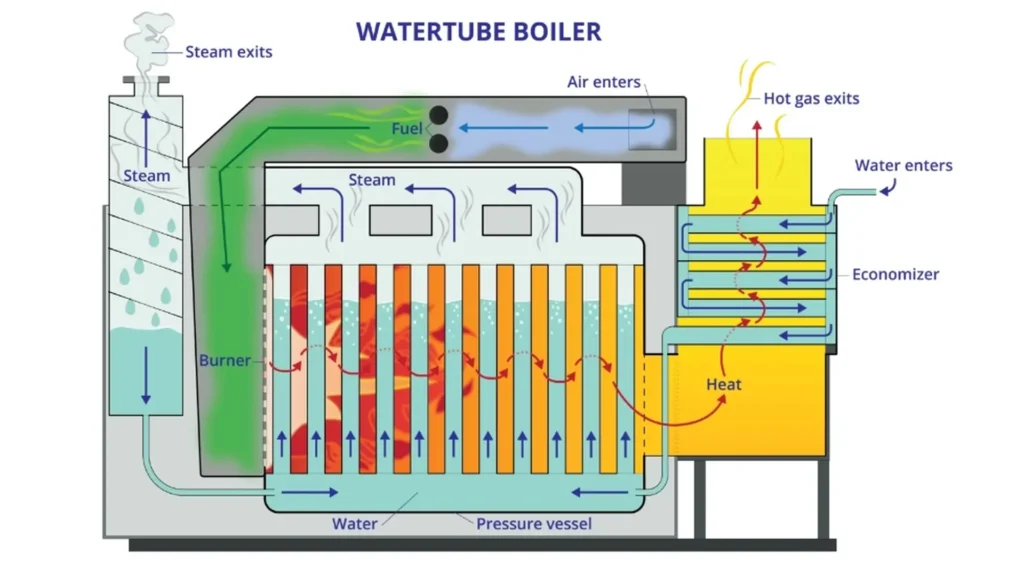
How is the efficiency of a boiler determined?
To know the real efficiency of a boiler, it starts with an accurate measurement of the combustion gases emitted by the burner. This would be the first step to be executed to detect the factors that influence the operating efficiency of the boilers.
The main gases emitted during combustion include CO2 (carbon dioxide), O2 (oxygen) and CO (carbon monoxide), which are indicative of boiler operating efficiency; high concentrations of CO indicate incomplete combustion, while adequate proportions of CO2 and O2 indicate efficient and complete combustion. By correctly monitoring these gases, the quality of combustion is detected, it is known whether the heat is being used efficiently and whether the amount of air supplied is ideal for the process.
The analysis of the gases emitted determines the actual energy efficiency of the boiler. It is important to know the model of the boiler, fuel used and processes carried out, to facilitate the proposal of improvements and adjustments required in case of finding deviations during the measurements.
Efficiency analysis of industrial boilers
The efficiency of a boiler is measured by its ability to convert the energy contained in the fuel into useful heat over a given period. Thermal efficiency, a common measure in this context, reflects the ratio between the amount of useful heat generated and the total energy consumed, usually expressed as a percentage and can range from 50% to 98%.
To further analyze boiler efficiency, the indirect method, also known as the heat loss method, is used. This focuses on identifying and quantifying the various heat losses within the boiler system, such as flue gas losses, blowdown losses, radiation losses, among others. This detailed analysis identifies specifically where and how heat is lost, being a required study to know the boiler efficiency analysis and formulate improvement strategies.
The following video shows how to calculate the efficiency of a boiler by the indirect and direct method, specifying all the necessary parameters, courtesy of Electrical Hub.
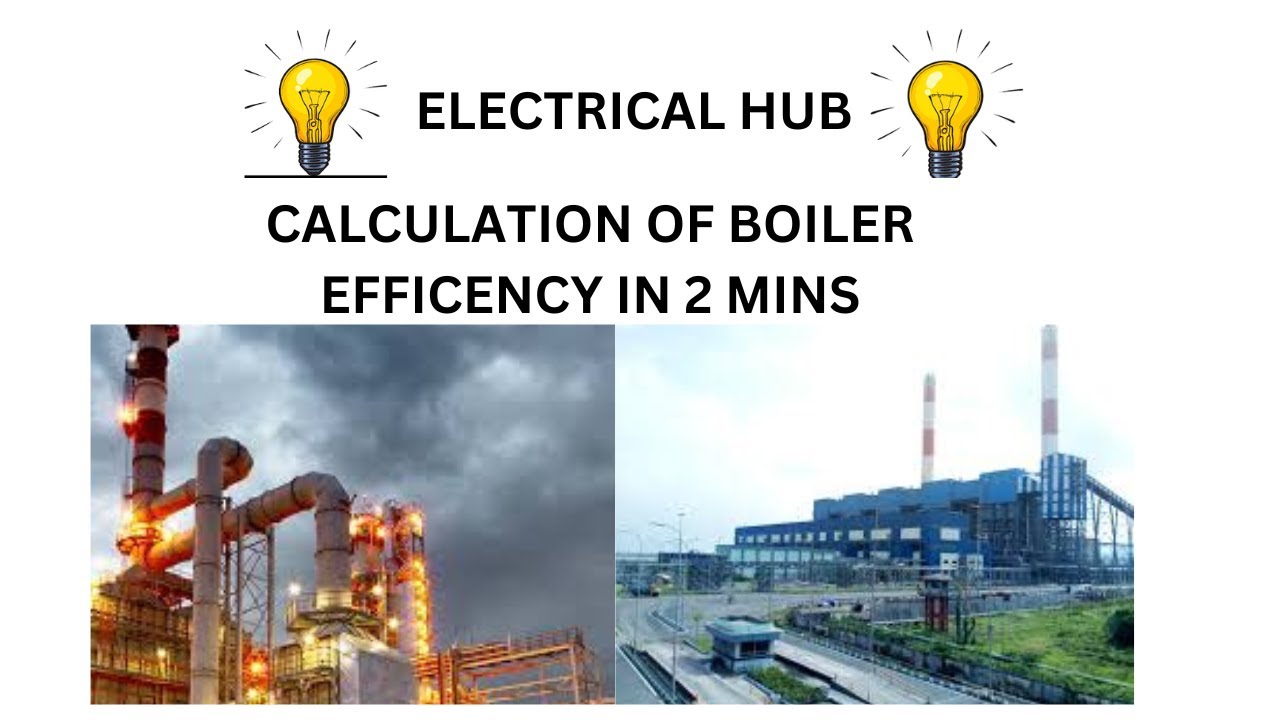
Calculation of boiler efficency.
Factors affecting boiler efficiency
The efficiency of a boiler is represented by the efficiency with which it converts fuel energy into useful heat for a specific process.
This performance is generally affected by factors such as: quality of the fuel supplied, which may contain moisture, sulfur and mineral residues; the treatment and quality of the water, as well as the atomization arrangement, which is affected by the fractionation and distribution of the droplets, viscosity, and exploitation factors and atomization steam temperature. Another factor is the thermal load of the furnace and the residence time of the gases in the furnace; on the other hand, excess and infiltration of air and deposits and incrustations on the heat transfer surface decrease the operating efficiency of the boilers2.
Likewise, factors such as design capacity, response to load variations, operational stability, and the efficiency with which the boiler withstands changes in operating parameters without compromising product output. Mechanical failures, structural integrity and corrosion in components are factors that impact performance.
How to improve performance and energy efficiency in industrial boilers?
The design and technical development of boilers faces the inevitable energy inefficiency during the processes, urging that even the most technologically advanced boilers do not reach 100% efficiency due to energy losses. To control these losses and improve efficiency, there are several strategies:
- Fuel and combustion control: Proper control of combustion and emissions by using high-efficiency burners and adjusting the air-fuel ratio provide better performance and control energy waste. Advanced control systems monitor and adjust fuel supply.
- Waste heat recovery: This technique involves the use of economizers and preheaters to capture and reuse exhaust gas heat. Doing so reduces the amount of wasted thermal energy, reducing heat loads and increasing process efficiency.
- Optimize the distribution system: Ensuring that the steam or hot water distribution system is properly sized and insulated minimizes heat losses from the boilers.
- Regular maintenance and inspections: Preventive maintenance prevents the build-up of scale and soot, which decrease heat transfer and boiler operating efficiency, in conjunction with scheduled inspections to verify system integrity. For example, inspections or replacements of condensate traps and condensate return pumps prevent water waste, maximizing operating efficiency.
- Water treatment: Proper control of water quality, suspended solids concentration inside the boiler and good blowdown practices are effective measures to increase boiler operating efficiency.
- Automation of controls: Implementing automated controls such as energy monitoring systems, which adjust operating parameters according to steam demand needs, improves system response and efficiency.
- Thermal insulation: Insulation reduces heat loss by convection and radiation. That is to say, to properly insulate the outside of the boiler, as well as the accessories and pipes that transport hot water or steam, in order to make the best use of the heat generated.
- Heat management and recovery in blowdown processes: Heat recovery in blowdown water by means of exchangers or flash tanks to reuse energy and also regulate the blowdown rate minimizes heat losses and avoids impurities and dissolved solids; this action reduces the risks of failure due to scaling and raises the operating efficiency of the boilers.
- Updating boiler systems: If the boiler has been in service for more than a decade, it is advisable to evaluate the investment in modern and more efficient systems. Although the initial investment will be high, the long-term benefits in terms of energy savings and reduced operating costs will compensate for the investment.
Implementing these strategies increases the operating efficiency of boilers and optimizes the profitability and sustainability of operations.
Applications of new technologies in industrial boilers
Today, boilers are complex integrated units with the most advanced technology. Boiler manufacturers are continually designing innovative technologies that advance boiler reliability and operating efficiency, factors demanded by modern industry for improved energy efficiency. Among the new technologies in industrial boilers, the following stand out:
- Energy-efficient boilers: Known as energy-efficient boilers, they are distinguished by their ability to make maximum use of fuel energy, minimizing losses and converting a greater proportion into useful heat. They achieve thermal efficiencies in excess of 90%, meaning that more than 90% of the energy in the fuel is converted into useful heat.
- Condensing technology: Condensing boilers recover waste heat from flue gases that is lost through the chimney in traditional boilers. By condensing the water vapor in the flue gases, the boilers recover latent heat, increasing their energy efficiency.
- Low-emission burners (Low-NOx): These are designed to reduce the production of nitrogen oxides, a pollutant that is harmful to the environment. They use techniques such as exhaust gas recirculation and staged combustion technology to achieve more efficient and cleaner combustion.
- Waste heat recovery systems: These are designed to capture process heat that would otherwise be lost and use it to preheat feedwater or for other thermal processes within the plant, thus improving the operating efficiency of the boilers.
- Integration of renewable energy: Using renewable energy sources, such as biomass, solar or geothermal heat, in boiler systems reduces dependence on fossil fuels and reduces carbon emissions.
The following video shows how a biomass boiler works, courtesy of HoSt Group – Bioenergy Systems.

How Is Renewable Energy Produced From Biomass?
- Automation and intelligent control systems: Having systems with integration of state-of-the-art algorithms and sensors based on Artificial Intelligence, Internet of Things (IoT), Big Data and Machine Learning for intelligent process control, regulates operations, optimizing energy consumption and improving response to changing plant loads3.
- Hybrid boilers: Combining combustion technologies with heat pump systems offers high efficiency, especially in climates where changing conditions affect the performance of traditional systems.
- Software to optimize boilers: Software is available to evaluate closed fuel and air circuits in real time, and all operating loads. These systems control air-fuel ratios and heat transfer between flue gases and steam, with the purpose of improving boiler productivity, steam temperatures and emissions3.
- Advancement in electrified boilers: The company AtmosZero has developed one of the newest boiler technologies, the innovative electrified boiler known as Boiler 2.0, which is an all-electric heat pump system that produces steam for industrial processes at temperatures between 100 and 200 °C. It uses a cascade system that produces steam at temperatures between 100 and 200 °C. It uses a cascade system that combines low and high temperature circuits, obtaining double efficiency compared to other electric boilers and represents a green alternative to traditional fossil fuel burning boilers4.
Conclusions
Energy efficiency in industrial boilers is an operational necessity that responds to environmental and economic requirements of industrial sectors. Through the analysis of operating conditions and the use of new technologies and energy management strategies, industries reduce operating costs and pollutant emissions.
Advanced technologies such as energy-efficient boilers, condensing boilers and new heat recovery systems, together with the integration of renewable energy sources and advanced automation, optimize boiler performance and set new standards in sustainable industrial production. These innovations promise more efficient and intelligent machinery that drives industrial innovation and supports global climate goals, standing out in a market increasingly focused on green performance.
References
- https://miuraboiler.com/steam-boilers-101/. Accessed May 27, 2024
- https://slideplayer.es/slide/2269282/. Accessed May 22, 2024.
- https://www.ge.com/digital/applications/operations-performance-management-opm/boiler-plant-optimization-steam-plant-efficiency. Accessed May 21, 2024.
- https://ecoinventos.com/startup-desarrolla-nueva-bomba-de-calor-alimentada-por-aire-que-genera-vapor-para-uso-industrial/#AtmosZero_innovacion_en_calderas_electrificadas. Accessed May 23, 2024.