The oil industry continues to be the main source of energy worldwide, although extraction and production processes are becoming increasingly costly and complex. In the face of these challenges, technological advancements in drilling techniques are imperative for the optimization and transformation of these operations. Furthermore, these innovations aim to ameliorate environmental impacts and augment operational efficiency, thereby meeting the burgeoning global energy demand.
This article delves into the contemporary trends in oil well drilling, accentuating the significance of advanced drilling methodologies such as extended reach drilling and enhancements in conventional techniques like rotary drilling; concurrently, it addresses the impact of digital technologies on the drilling and production of petroleum.
Basic oil well drilling process
The process commences with a planning and design phase, wherein geological and geophysical surveys are conducted to ascertain the optimal well location and to assess hydrocarbon presence. The execution of oil well drilling projects entails considerations of depth, rock type, and the prevailing pressure and temperature conditions to aptly design the well.
Subsequent to defining these parameters, drilling equipment, inclusive of the derrick and drill, is installed to initiate the soil penetration, employing specific drilling methods and apparatus to traverse the earth’s strata and stabilize the well through the installation of casing pipes.
Upon attaining the targeted depth, the well is subjected to evaluative testing to ascertain its productive viability. If deemed profitable, the transition is made to the completion phase, wherein additional apparatus are deployed for secure oil extraction. This phase concludes with the production stage, during which the extracted crude is dispatched to refineries for processing. Ultimately, upon cessation of the well’s productivity, the closure phase is initiated, entailing the sealing and dismantling of the site to alleviate environmental impacts.
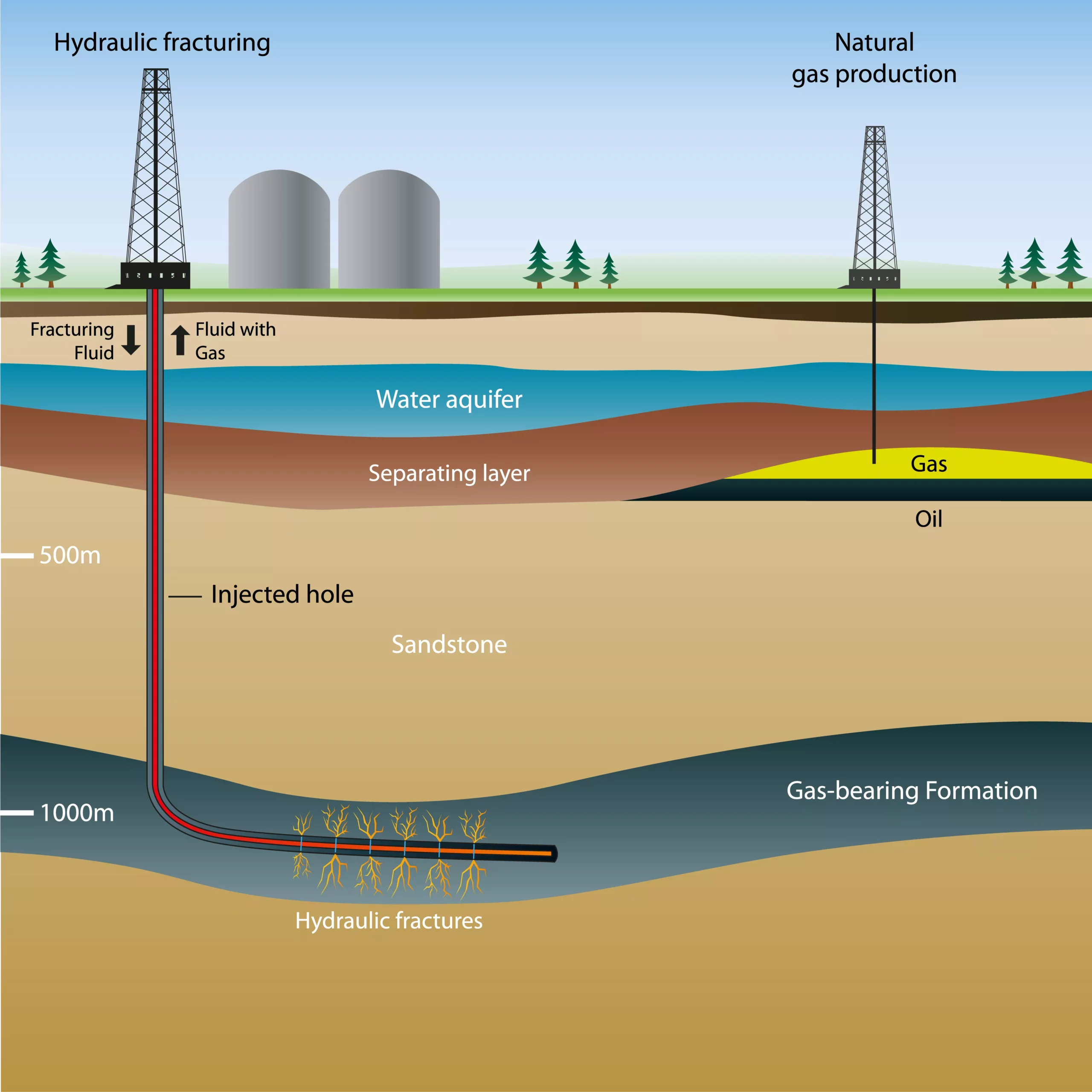
Importance of oil drilling and production for the global economy
Oil drilling and production are pivotal for global economic growth. Countries with substantial oil reserves rely on this resource as primary income sources, fostering international trade and influencing economic relations between nations and investment in industry-related infrastructure.
Oil, as one of the world’s most critical commodities, positively impacts various sectors. Oil market prices and dynamics significantly affect drilling and extraction processes by promoting technological innovation, enhancing efficiency, and sustainability. Furthermore, the oil industry must maintain capital discipline and prioritize viable drilling and extraction projects with low carbon emissions to sustainably meet global energy demand.
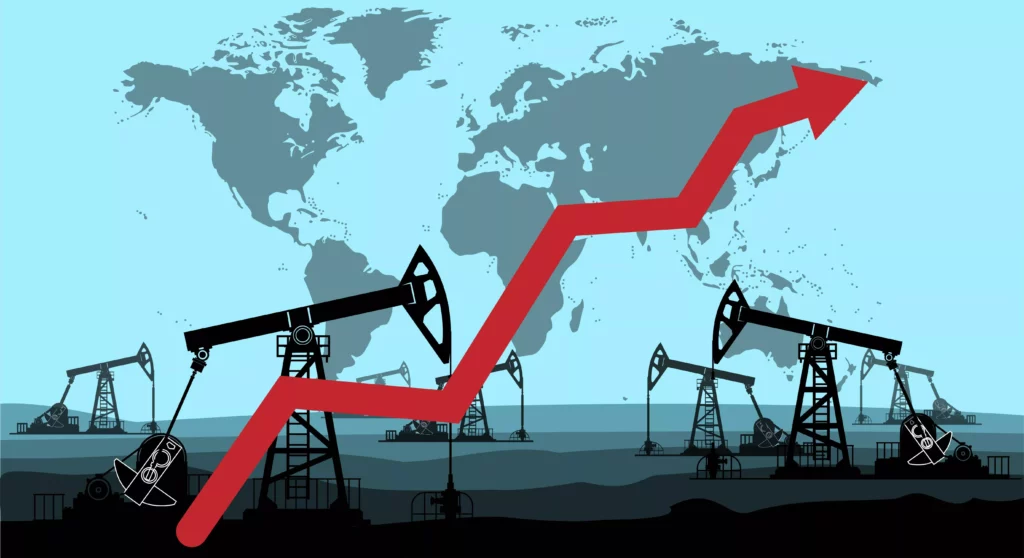
A notable transformation in the offshore drilling market is expected, with its value projected to increase from 36.520 billion dollars in 2023 to 65.630 billion by 2030. This growth is driven by several factors, including rising global energy demand and advances in drilling technologies. Despite challenges such as environmental regulations and high costs, the offshore drilling market is anticipated to expand, fueled by investments in advanced technology to optimize operations and minimize environmental impact1.
Current trends in oil well drilling techniques
Technological advancements in oil well drilling methods have enhanced efficiency and safety while reducing the costs associated with the exploration and exploitation of petroleum. Noteworthy among these are:
- Robotic drilling systems: These systems automate and enhance the efficiency of rotary drilling operations. Featuring advanced capabilities such as autonomous navigation and the manipulation of pipes and tools, these systems streamline field operations. Concurrently, artificial intelligence (AI) refines predictions on hydrocarbon extraction from wells, especially post-hydraulic fracturing, enabling more effective fracturing programs and improved ecological management of resources.
- Directional drilling and horizontal wells: Directional drilling techniques, surpassing conventional vertical methods, facilitate access to reservoirs situated beneath natural barriers or in complex areas. Horizontal drilling has emerged as a paradigm within the sector, allowing a single well to access a larger area of the reservoir, optimizing contact with hydrocarbon-bearing strata to maximize petroleum extraction.
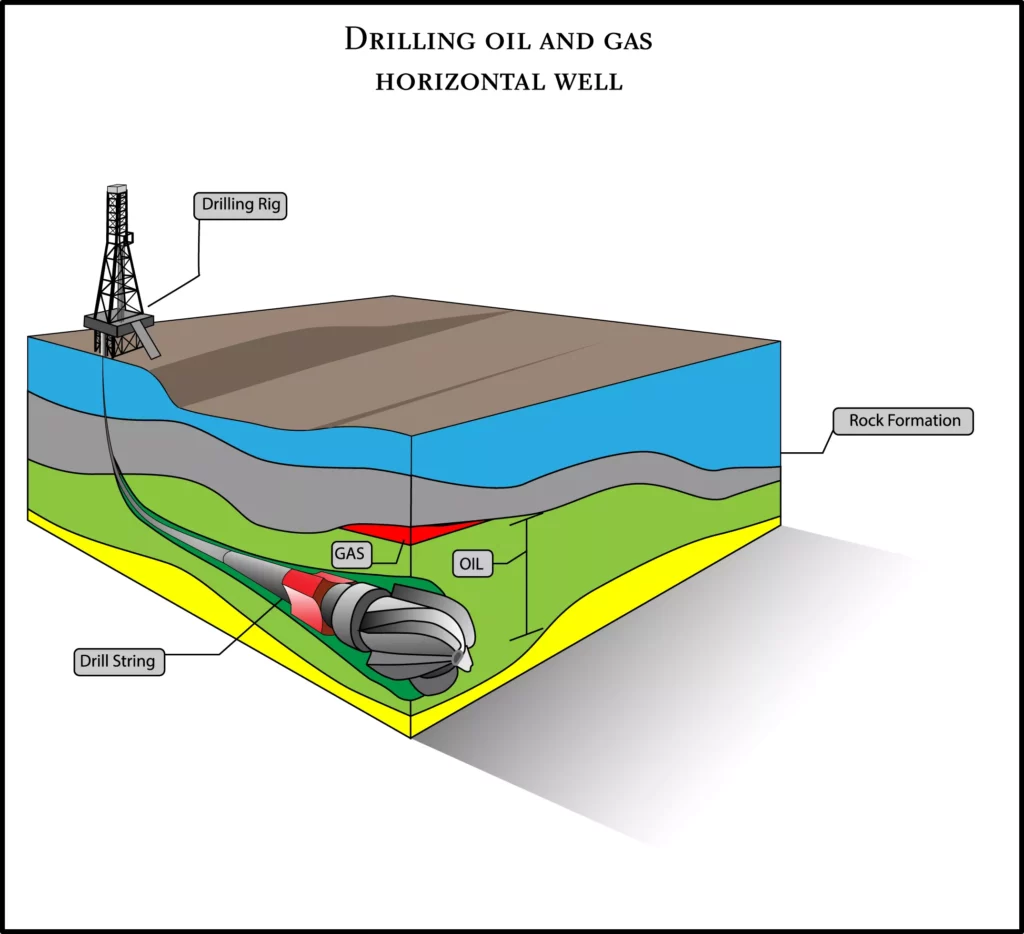
- Extended reach drilling (ERD): This technique surpasses the technological limitations of traditional drilling, allowing access to distant reservoirs from the drilling platform, often several kilometers away. It enhances the ability to exploit reserves in hard-to-reach or environmentally sensitive areas, such as urban regions or deep marine environments, enabling viable offshore production in challenging locales like the Arctic.
- Drilling fluid technology: Advances in this technology have resulted in more eco-friendly formulations that improve well stability and allow operation under extreme high-pressure and temperature conditions. Fluids based on enhanced oil and water formulations have been developed, incorporating nanotechnology for more efficient drilling and smart systems that adapt their properties in real-time.
- Rotary drilling: One of the most traditional drilling methods, it has seen improvements recently, such as the implementation of automated and digitally controlled systems that increase precision and reduce drilling time. Rotary drilling equipment has been optimized to withstand extreme conditions, allowing access to deeper and more complex reserves; these are categorized into onshore or offshore drilling rigs.
- Automated systems in oil well drilling: Well automation has optimized the process and improved safety. With the use of advanced sensors and computer systems, it is possible to monitor and adjust drilling parameters in real-time, actively adapting to operational needs. In complex drilling environments, this automation contributes to greater accuracy and reduces the likelihood of incidents.
- Specialized tools for wellbore analysis: Downhole tools, including logging and measurement while drilling technologies, provide valuable information to operators. These technologies offer real-time insights into the geology and characteristics of the well formation during the drilling process, facilitating data acquisition that improves the precision of well placement and minimizes risks. Industry-leading companies like Halliburton develop and implement these technologies.
- Sustainable drilling strategies: Growing environmental awareness has prompted the implementation of sustainable drilling strategies, focusing on increasing energy efficiency through the reduction of pollutant emissions, waste reduction, and the incorporation of renewable energies in the drilling processes.
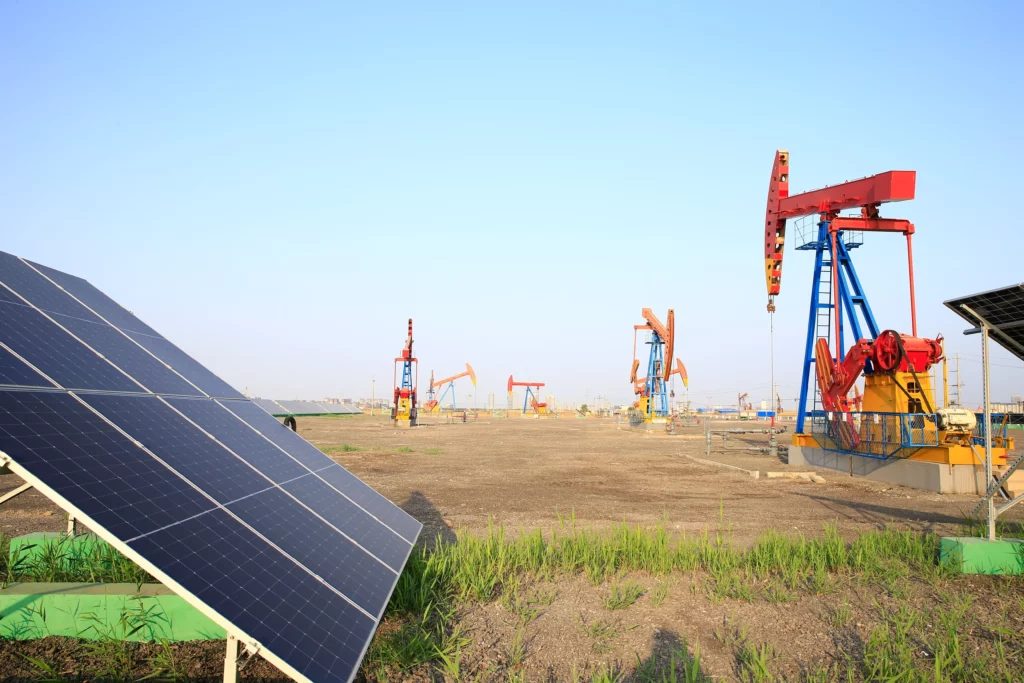
- Detailed reservoir simulation: Enhanced by artificial intelligence (AI), this approach utilizes data analytics and machine learning to generate accurate representations of oil reservoirs. These simulations provide an improved understanding of well characteristics, enabling the prediction of oil flow behavior. Consequently, operators can precisely tailor drilling and production strategies, optimizing operational efficiency and effectiveness.
- Corrosion-resistant materials and alloys: The construction of wells necessitates materials and alloys that are resistant to corrosion, capable of withstanding the extreme subsurface conditions, where high levels of CO2, along with elevated pressures and temperatures, can cause corrosion. Corrosion-resistant steels, such as coated carbon steel, as well as stainless steels 304 and 316, are employed. Furthermore, to mitigate the corrosive effects of these harsh conditions, the injection of corrosion inhibitors is implemented as a control strategy at the wellbore.
The following video highlights significant advancements in offshore drilling, featuring the world’s first eighth-generation drill ships, the Titan, and the Atlas, both specialized in deep-water operations. This content is provided courtesy of Transocean.

The future of offshore drilling.
Conclusions
Given the significant impact of oil on the global economy and its status as one of the most coveted commodities, continual technological innovation in drilling methods reflects a commitment to innovation, adaptability, and effective utilization of global petroleum resources.
The oil drilling and production industry is moving towards a future where resource optimization and reducing the ecological footprint are paramount. This underscores the enduring importance of oil in our energy landscape and the necessity of implementing advanced extraction strategies with technical excellence that balance resource demand with efficiency and environmental stewardship.
References
- Oil Drilling in United States Market Overview 2023-2027; Market Overview Report; August 2023.
- https://www.americanmudpumps.com/es/post/los-sistemas-de-perforaci%C3%B3n-rob%C3%B3tica