Table of Contents
Introduction
Petroleum distillation is the process by which crude derivatives are obtained by increasing the temperature to bring the crude oil to different boiling points. It is a unit operation whose definition is as follows: When a liquid containing two or more components is heated to its boiling temperature, the composition of the vapor will normally be different from that of the liquid. This difference in composition in the two phases at equilibrium is the basis for distillation and for this reason this operation is applicable to separate mixtures of compounds due to their different volatilities or their different vapor pressures.
The objective is to extract the hydrocarbons present in the crude by distillation, without affecting the molecular structure of the components. In the Topping units, finished fuels and hydrocarbon cuts are produced that will be processed in other units, to convert them into more valuable fuels. In the Vacuum units, only intermediate cuts are produced that are loaded into conversion units, which are transformed into higher value products that are easy to market.
In oil refining units, crude oil is separated into different products according to their individual boiling ranges. Distillation allows materials to be separated without being subjected to conditions that would cause cracking or decomposition, through two processes, atmospheric distillation and vacuum distillation; Figure 1 shows a schematic of these processes.
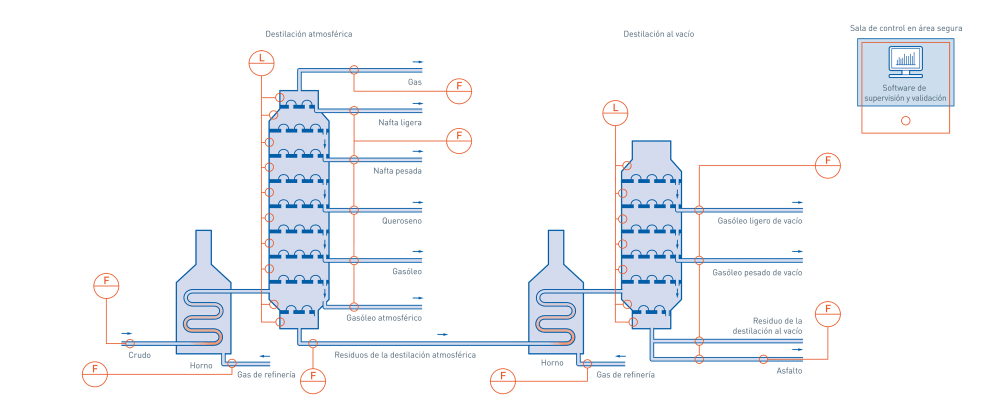
Fundamentals of the Process
The distillation of crude oil is based on the mass transfer between the liquid-vapour phases of a mixture of hydrocarbons.
Distillation allows the separation of the components of a mixture of hydrocarbons, such as oil, based on their boiling temperatures.
In order for the “separation or fractionation” of the cuts to occur, equilibrium must be reached between the liquid-vapor phases, since in this way the lighter components or those with lower molecular weight are concentrated in the vapor phase and, on the contrary, those with higher molecular weight predominate in the liquid phase, in short, the differences in volatility of hydrocarbons are used.
The liquid-vapor equilibrium depends mainly on the thermodynamic parameters, pressure and temperature of the system. The units are designed so that these balances occur in a controlled manner and for the time necessary to obtain the specified fuels.
Basically, the process consists of vaporizing the hydrocarbons in the crude oil and then condensing them into defined cuts. Fundamentally modifying the temperature, along the fractionating column.
Vaporization or vapor phase occurs in the furnace and loading zone of the fractionating column. In the Furnace, the necessary thermal energy is transferred to produce the phase change and in the Loading Zone the pressure of the system is reduced, producing the flash of the load, obtaining the definitive vaporization.
The liquid phase is achieved with reflux or recycling of hydrocarbons returned to the tower. These refluxes are liquid streams of hydrocarbons that are cooled by exchange with oil or coolant fluids. The main function or objective of these is to eliminate or dissipate in a controlled way the energy transferred to the hydrocarbons in the furnace, in this way the vaporized charge is cooled and condensed, in cuts or specific hydrocarbon fractions, obtaining the corresponding fuels.
The column has trays or plates where the equilibrium between the ascending vapors and the descending liquids occurs. At exactly calculated points or heights there are collector plates from which the distillate fuels are extracted.
The fundamental difference between the Topping and Vacuum units is the working pressure. The Topping operates with typical pressures of 1 Kg/cm2 (gauge), while the Vacuum works with absolute pressures of 20 mm of mercury. This allows the distilling of high molecular weight hydrocarbons that would decompose or crack thermally, if the normal operating conditions of the Topping were exceeded.
Process variables
The thermodynamic parameters that govern the distillation are the temperature and pressure of the system, for this reason we consider as variables of the process all those that can affect the balance between the vapor-liquid phases.
- transfer temperature. This is the maximum temperature to which the crude is raised to vaporize it, the yield in distillates depends on this variable.
- Work pressure. It is the pressure at which the operation occurs. Although it directly affects the liquid-vapor balance, it generally works at the lowest possible pressure, and therefore it is not changed frequently.
- Head temperature. It is the temperature in the upper zone of the fractionating column, it is controlled with the head reflux, this reflux is the cold source that generates the current of liquids that contact the vapors, producing liquid-vapor balances.
- Cutting temperature. It is the temperature at which the lateral extraction of a fuel is carried out. This temperature is controlled with head reflux and circulating refluxes. The latter have a similar effect as head reflux and also preheat the crude, recovering energy.
- Steam injection. The steam or (non-condensable) in the fractionators lowers the partial pressure of the hydrocarbons, establishing new vapor-liquid balances, favoring the vaporization of the more volatile components. This applies to the main fractionating column as well as to the sidecut strippers.
Distilled products
In the Topping units, the following final products and loads from other processes are obtained.
- Light naphtha, is sent as cargo to isomerization where the RON and MON are improved.
- Heavy naphtha is sent as cargo to Hydrotreatment of naphthas-Platforming, where the RON and MON are improved.
- Kerosene, is sent to dispatch tank.
- Light Gas Oil, is sent to the dispatch tank.
- Heavy Gas Oil is sent as cargo to Isomax, converting it into Gas Oil and JP or to the Fluid Catalytic Cracking units.
On Void units, charges are only gained for conversion units.
- Vacuum light oil gas is sent as cargo to Isomax, where gas oil, JP, naphtha is obtained from hydrotreatment of naphtha and isomerization and propane-butane.
- Heavy vacuum gas oil is sent to the Fluid Catalytic Cracking units, where high RON naphtha is obtained, propane petrochemical load or dispatch, butane load to MTBE-alkylation, fuel gases, diesel oil load to Diesel Hydrotreatment that converts it in gas oil
- Asphalt is sent to the thermal cracking units, where it is converted into naphtha, a charge for Hydrotreatment of naphtha, diesel oil, a charge for Diesel Hydrotreatment, heavy coke gas oil that is charged to the Fluid Catalytic Cracking units, propane-butane coal. and fuel gases.
Crude fractionation processes
The first process that is carried out on crude oil in refineries is its conservative distillation. This operation consists of extracting all those hydrocarbons that can be obtained by distillation, without affecting its molecular structure.
The distillation or fractionation of crude oil is an operation that allows cutting or fuel to be separated from a complex mixture of hydrocarbons, such as oil. The physical principle on which the process is based is the difference in volatility of the components, for this reason in the fractionating columns the thermodynamic conditions are adapted to obtain or “condense” the perfectly specified fuels.
The fractionation of the crude is completed in two stages, firstly, it is processed in atmospheric distillation units or Topping, where the working pressure is typically 1 Kg/Cm2. The fuels obtained by this fractionation are sent to dispatch tanks or as cargo for other units that complete their refining.
Much of the crude processed in the Topping is not vaporized, since to achieve this it is necessary to raise the working temperature above the thermal decomposition limit. For this reason, this atmospheric residue, called reduced crude oil, is pumped to the Vacuum unit, where the pressure is lowered to 20 mm Hg (typical, which allows it to be distilled at higher temperatures without breaking down the molecular structure.
Atmospheric or topping distillation unit
The crude before being fractionated, must be properly conditioned and prepared to achieve an efficient operation. The first stage is carried out in the receiving tanks.
The degassed oil received at the Refineries contains impurities that are detrimental to the equipment, products and processes. The impurities are:
- Salts, fundamentally sodium, calcium and magnesium chlorides, present in the formation water that the crude has, these salts hydrolyze under the process conditions forming hydrochloric acid, which is highly corrosive and therefore extremely harmful to the equipment.
- Iron oxides, equipment corrosion products and means of transporting crude oil from the reservoir, which affect the fouling coefficients of equipment, product qualities and catalysts.
- Clay, sand, solids in general, coming from the producing formation and drilling mud, these fundamentally harm the fouling coefficients of the equipment and affect the quality of the residual products due to the high ash content.
- Organometallic compounds, which affect the catalysts of conversion units, deactivating them.
- Salt crystals or oxides in suspension, affecting both the products and the catalytic processes, the case of sodium compounds is specifically detrimental to the tubes of the furnaces, since they catalyze the formation of carbon, reducing the useful life of the furnace by decreasing of the heat transfer coefficient.
To avoid or minimize the pernicious effects of these impurities, three treatments are fundamentally carried out:
- Decantation in Tanks
- Desalted
- Sodium Hydroxide Injection
Storage tanks
The tank treatment consists of decanting the free water that the crude has by gravity. For this reason, the temperature of the tank is very important at this stage, since the physical property that governs it is viscosity. Obviously, the higher the temperature, the lower the viscosity, and therefore the speed of migration or decantation of the water is improved, but great care must be taken not to exceed the temperature that causes convective currents, which directly harm the decantation.
To prevent loss of volatile hydrocarbons, the tanks have floating roofs that prevent this type of leak. The temperature is controlled with heaters or coils, located in the lower part of the tank. Exhaust steam is used as a heating element. The purged water additionally drags solids in suspension.
This stage is basically carried out with three tanks simultaneously, one receives crude from the reservoir, another is in decanting and the third that contains settled crude is from which the unit aspires.
The “decanted” crude in tanks is sent to the Topping unit, where it is preheated with higher temperature currents, finished products and circulating refluxes, allowing heat energy to be recovered in the exchange circuit.
The function of the exchange circuit is the recovery of energy, generating a thermal gradient along the circuit, which allows minimizing fuel consumption in the heating furnaces. Prior to the oven, two operations of fundamental importance are carried out, the desalting and dehydration of the oil, for which specific thermodynamic conditions are needed.
Crude oil pretreatment
Crude Desalting
The purpose of this process is to eliminate the salts and impurities that the crude oils have, loaded by the Topping units. Suspended solids and dissolved salts in very small drops of water, dispersed within the oil, are extracted in desalination plants since it is uneconomical to decant them and eliminate them by gravity in storage tanks. (Figure 2 below).
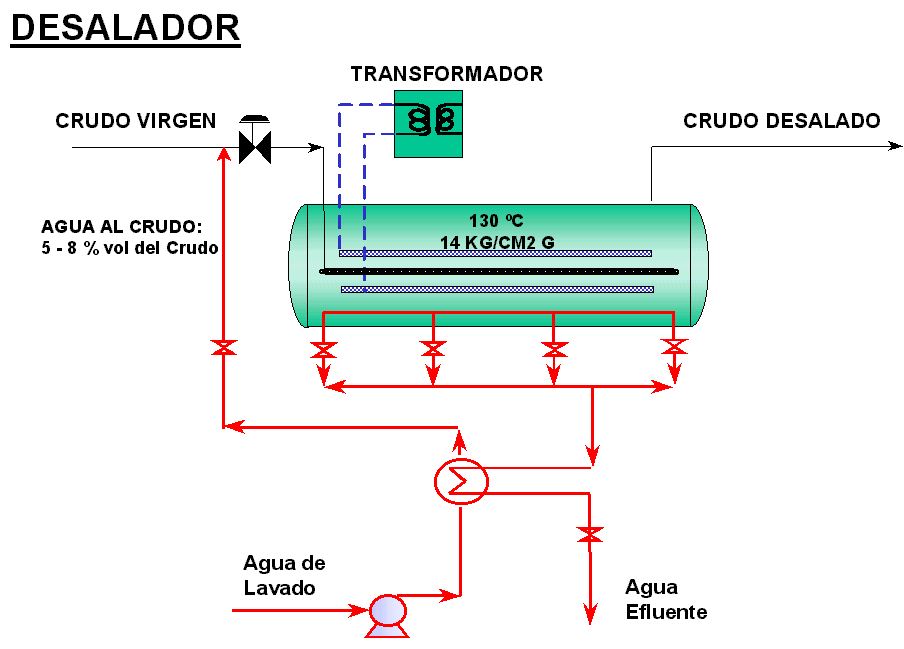
Basically, the desalination process consists of preheating the crude oil to reduce its viscosity, injecting washing or salt-free water, producing an intimate mixture between the two, contacting it with the residual water from the crude oil, and subsequently separating the water containing the highest proportion of impurities. In short, the dissolution of the salts present in the crude is carried out, generating small electrolytes (drops), sensitive to variations in an electric field.
To achieve mixing, emulsifying valves or static mixers are used. Later it is sent to an accumulator where the current is made to flow uniformly through a high voltage electric field (20,000 V), generated by pairs of electrodes. Electrical forces within the field cause small water droplets to coalesce, forming larger droplets that can settle on the equipment. Salt-free crude oil (desalted crude oil) exits through the upper part of the equipment.
The coalescence of the droplets in the desolator is caused by electrical forces generated between the water droplets. The electric field induces the small droplets to become electric dipoles, which interact with each other, generating attractions between the droplets, grouping them into larger drops, which can settle due to gravity. The alternating field effect causes the droplets to move (vibrate) in phase with the field, favoring droplet coalescence.
The third stage of conditioning of the -crude is the injection of sodium hydroxide, this operation, unlike the previous two, does not eliminate the contaminants, but rather the effect is minimized by transformation of less harmful salts.
Dosage of sodium hydroxide to crude oil
All the salts are not removed from the crude effluent from the desalination plants since these equipments have an average desalination efficiency of 95%, for this reason a caustic solution is injected to transform the calcium and magnesium chlorides into sodium chlorides. . Sodium chloride has a lower hydrolysis constant than the other salts, which minimizes the generation of hydrogen chloride and therefore the corrosive attack on the unit.
Hydrogen chloride gas condenses in the cold areas (upper part) of the tower and in contact with water hydrochloric acid is formed, which is highly corrosive, for this reason it is essential to minimize its presence or effects.
The added caustic replaces the magnesium and calcium cations with sodium, converting most of the chlorides to sodium chlorides, minimizing acid formation.
Cl 2 Mg + H2O ————– 2ClH
Cl 2 Mg + H2O ————– 2ClH + MgO
C12Ca + H2O ————– 2ClH + CaO
For each molecule of calcium or magnesium salt, twice as much acid is generated than, in the case of sodium chloride, on the other hand, the latter begins hydrolysis at the threshold of 300 °C, while at these temperatures the other two have hydrolyzed 10% and 90% respectively.
The substitution is carried out according to the following reactions.
NaOH+ C 12 Ca ————- Na Cl + (HO) 2 Ca
NaOH+ C 12 Mg ———— Na CL + (HO) 2 Mg
Corrosion control is complemented by the use of chemical products, based on amines, which neutralize the acid and form protective films on the walls of the equipment.
Once the impurities have been removed from the crude, it continues to be preheated and is sent to the preflash tower, where the thermodynamic conditions are such that the crude partially vaporizes. The vaporized fraction is sent directly to the fractionating column, which makes it possible to reduce the load on the furnaces, reducing fuel consumption (typical conditions, 200 °C and 1.5 kg/cm2).
Once the maximum heat recovery has been reached, the crude oil is pumped to the furnace, where the necessary energy is transferred to it to achieve the required vaporization, in the feeding zone of the fractionating tower. The fractionation of hydrocarbons is carried out in this column. Typical load zone conditions 370 °C and 0.800 kg/cm2 pressure (Figure 3 below).
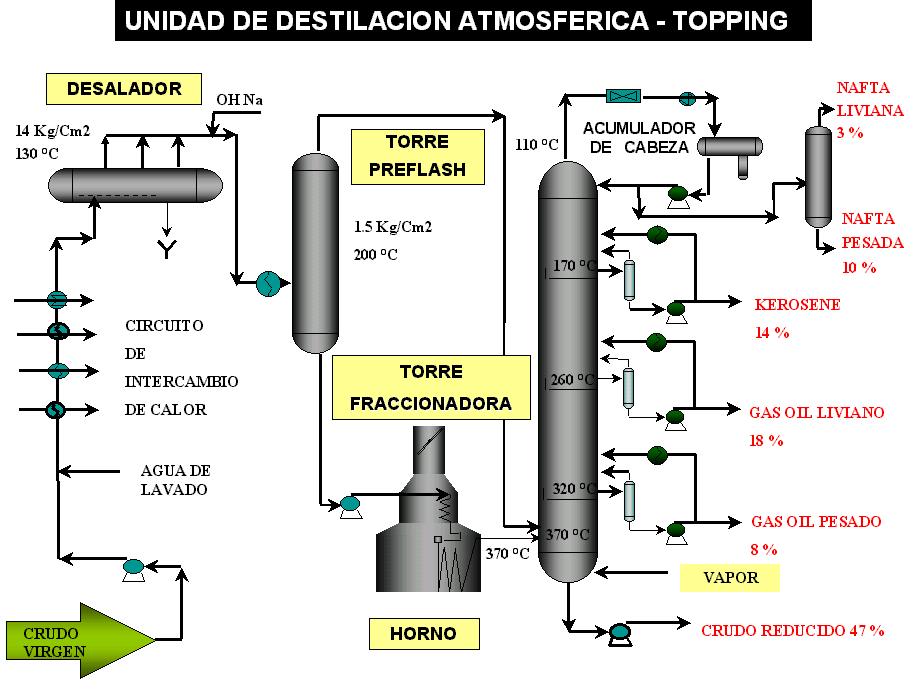
Atmospheric crude oil distillation
Distillation allows the separation of the components of a mixture of hydrocarbons, such as oil, depending on their boiling temperatures, taking advantage of their differences in volatility.
The partially vaporized charge enters the flash zone or charge zone. The vaporized hydrocarbons rise through the fractionating column through fractionation trays or plates, where liquids and vapors are intimately contacted, producing the mass and heat transfer necessary to fractionate the different fuels (see Figure 4). These are extracted laterally through collector plates and sent to stripping towers, strippers, where the flash point of the cuts is adjusted.
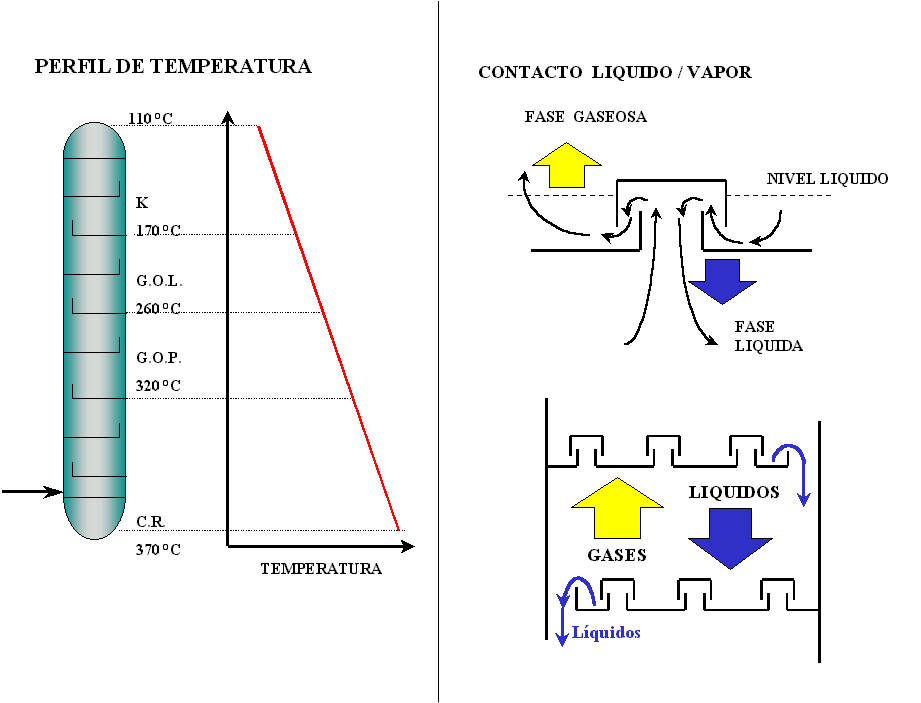
The products obtained by the upper part or head are gases and naphtha. The gas is compressed and sent to gas concentration units. Nafta is fractionated again to obtain two cuts. The light naphtha that is sent to isomerization or tank as a petrochemical load and heavy naphtha that is sent to the Hydrotreatment units where the contaminants, poisons, of the Platforming catalysts are eliminated.
The first lateral cut is the kerosene, which is sent to the tank. It previously exchanges heat with crude oil and is cooled to storage temperature using air coolers and water coolers.
The second side cut is light gas oil, which is treated similarly to kerosene.
The third and last lateral cut is the heavy gas oil from Topping, which is sent as a load to the Isomax or Fluid Catalytic units.
The bottom product is the residue that was not vaporized in the furnace, since it would be necessary to raise the temperature above the cracking threshold or thermal decomposition of high molecular weight hydrocarbons. For this reason this current is sent to the Vacuum unit.
Vacuum distillation unit
The purpose of the Vacuum Distillation Unit is to distillate the hydrocarbon fractions that cannot be distilled in the atmospheric stage because the high temperatures that would be required would produce their thermal decomposition. It is the complementary operation to atmospheric distillation. To achieve this, the working pressure is lowered until reaching absolute pressures of a few mm Hg in the loading area of the distillation column. To achieve this, the working pressure is lowered until reaching absolute pressures of 20 mm Hg in the loading zone of the distillation column. Vacuum is obtained with steam ejectors. (see figure No. 5).
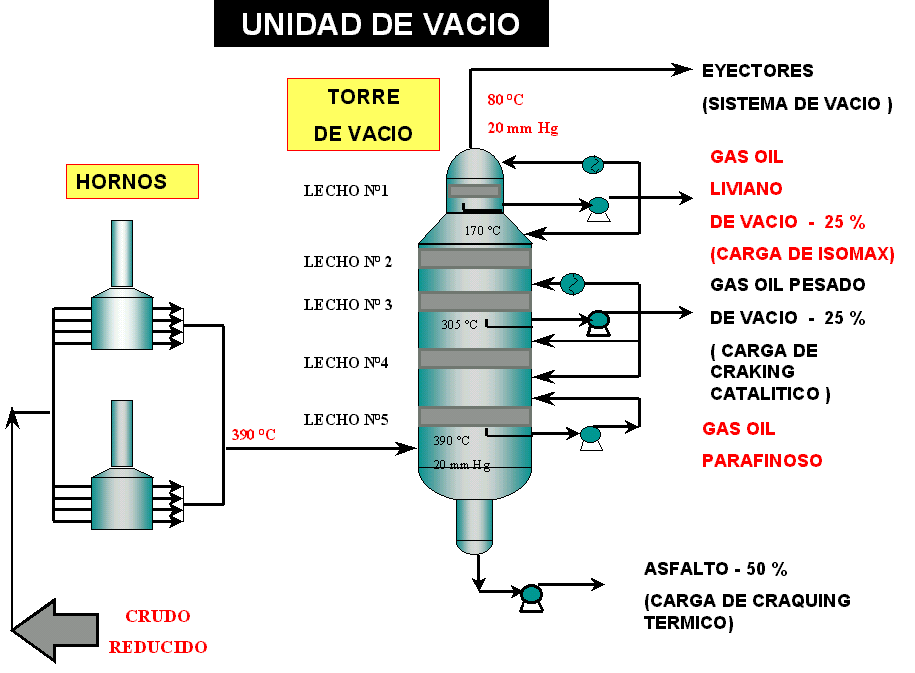
In this unit, the energy necessary to vaporize the reduced crude oil is supplied entirely in furnaces, designed to minimize load loss (loss of pressure) in order to operate with the lowest possible pressure at the points where vaporization begins. The partially vaporized load is sent to the flash zone of the distillation column, where an ascending current of vapors and a descending current of liquids are produced. In these columns the principle of operation is the condensation of vapors.
The tower has particular characteristics that differentiate it from atmospheric fractionators. The devices or mechanical elements to produce liquid-vapor contact are special fillers (flexi rings, located in ordered beds) that allow the interface surface to be increased, favoring mass transfer (see figure 6). The diameter of the column is different in the condensation zone, with respect to the upper or lower zone of the same.
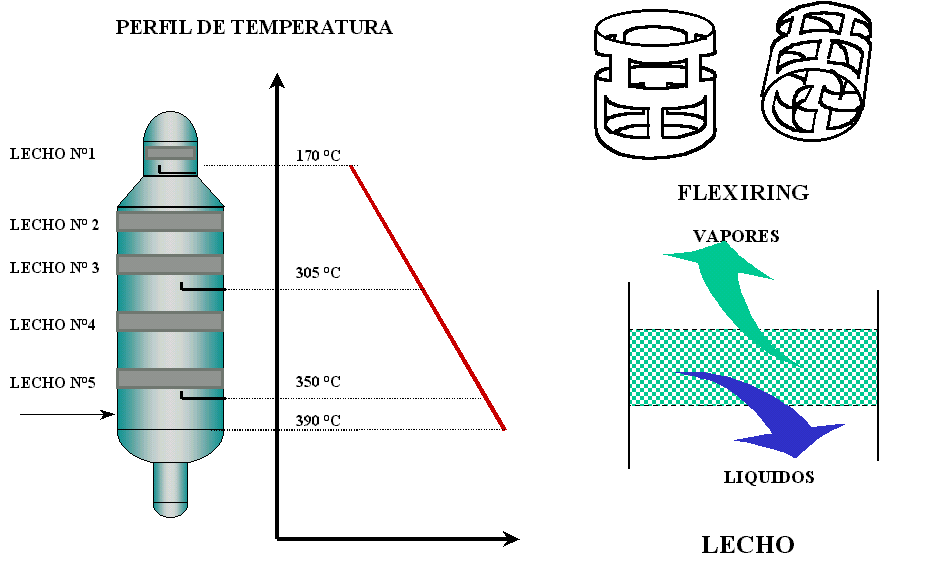
The condensation or fractionation zone has the largest diameter since the load losses must be negligible to maintain a homogeneous vacuum throughout the entire tower. The head zone has a smaller diameter since the vapor flow in this zone is very low due to the fact that the products are only obtained laterally and not by head. The bottom of the column has the smallest diameter, since the residence time of the asphalt must be minimized to avoid thermal decomposition and carbon formation in the tower.
The first side cut produced is Vacuum Light Gas Oil, which is loaded from the Isomax or FCC unit. Due to the characteristics of the Isomax (Hydrocracking) process, the specifications of the products are very important, since the performance of that unit is strongly affected if the catalyst is damaged.
The second lateral cut is the Heavy Vacuum Gas Oil, this product exchanges heat with the crude from the Topping unit and is the load par excellence of the Fluid Catalytic Cracking units. As a fundamental quality parameter, the content of Conradson Carbon (< 0.5%) is controlled in the cut. This parameter directly affects the carbon balance and therefore the heat balance of these units, which modifies their performance.
The bottom product is asphalt residue, which is sent to the Thermal Cracking units.
Conclusion
The fractional distillation of oil is generally used in refineries for the treatment of crude oil and which gives rise to the different fossil derived products. However, the efforts of the big oil companies in recent years is to work with oil in a cleaner way, with the intention of being able to not only reduce polluting emissions from vehicles, but also those derived from oil treatment.
References
- Treybal Robert (2001). Mass transfer operations. Publisher: McGraw Hill. Mexico. ISBN 968 6046 34 8
- Umberto Kunt (2010). Main oil refining and distillation processes. UCV. Publications.