Table of Contents
Introduction
In the current era, characterized by rapid technological advancements, digital transformation has revolutionized countless sectors, and corrosion management has not been an exception in enhancing efficiency, precision, and outcomes in this critical field. With the integration of digital technologies, employing corrosion monitoring and data-driven corrosion management, industries are making strides that promise to extend asset lifespan and reduce operational costs.
This article examines the digital transformation in corrosion management, the impact of these advancements, and the advantages that digitization brings to corrosion management.
Digital transformation in corrosion management
Corrosion, the gradual deterioration of materials (primarily metallic) due to chemical or electrochemical reactions in their environment, poses a significant challenge in terms of safety, economic costs, and environmental sustainability. Traditionally, corrosion management has relied on physical inspections, periodic testing, and a reactive approach to problems. However, digital transformation and advancements in corrosion management are enabling a shift towards more proactive and predictive strategies, thanks to the incorporation of advanced technologies such as the Internet of Things (IoT), Artificial Intelligence (AI), data-driven corrosion management, and cloud computing.
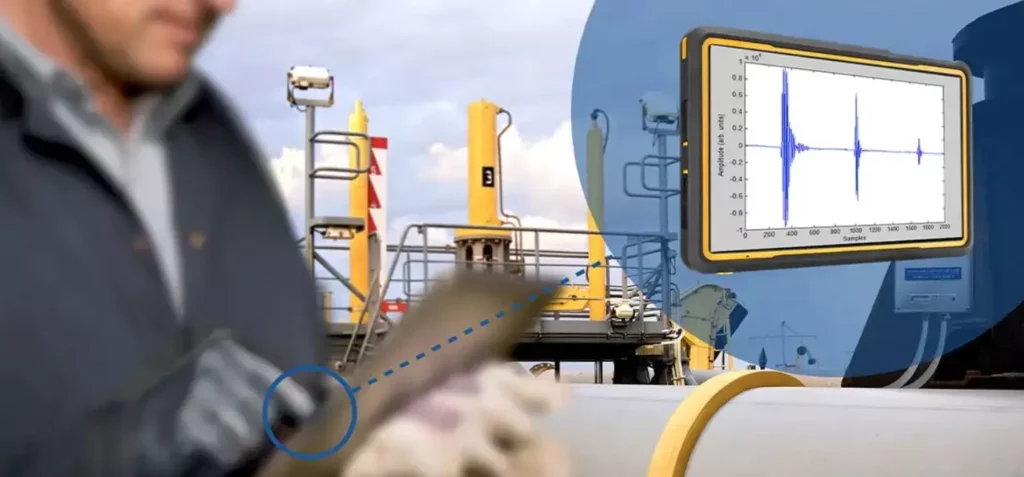
Internet of Things (IoT): The IoT has enabled the implementation of sensors in structures and equipment susceptible to corrosion, collecting real-time data on conditions that can accelerate corrosion, such as humidity, salinity, temperature, and the presence of corrosive agents. This information allows engineers to monitor corrosion and environmental conditions to adjust protection strategies more effectively, even remotely.
Artificial Intelligence (AI) and Machine Learning (ML): AI and ML are transforming corrosion management through advanced analysis of large volumes of data collected by IoT sensors. These technologies can identify patterns and predict areas of high corrosion risk before a failure occurs. Machine learning algorithms can also optimize the selection of materials and protective coatings based on specific operating conditions, thereby improving corrosion prevention.
Data-driven corrosion management: Predictive analysis uses historical and real-time data to predict when and where corrosion is most likely to occur. This approach helps to plan preventive maintenance more effectively, reducing costs associated with unplanned shutdowns and extending the lifespan of assets.
Augmented Reality (AR) and Virtual Reality (VR): These technologies offer new possibilities for personnel training and corrosion inspection. By using these technologies, engineers, and technicians can visualize corrosion on virtual or augmented assets without being physically present, improving the efficiency and safety of inspections. Additionally, training in virtual environments allows professionals to experiment with different corrosion scenarios and learn mitigation techniques without risks.
Cloud Computing: This digital tool facilitates remote access to corrosion data and analytical tools, enabling teams to collaborate and make data-driven decisions more effectively, regardless of their location. This is especially valuable for companies with operations in multiple sites or remote locations.
What is the impact of digitalization on corrosion management?
Digitalization has had a significant impact on corrosion management, enhancing the methodologies and strategies employed in the industry. Here are some of the most notable effects of digitalization in this area:
- Improved data collection: Digitalization has enabled the use of sensors and IoT (Internet of Things) devices to monitor real-time conditions affecting corrosion, such as humidity, temperature, and the presence of corrosive agents. This allows for precise and continuous data collection, which is crucial for corrosion analysis and prevention.
- Advanced data analysis: With the advent of big data and advanced analytics tools, it is possible to process and analyse large volumes of corrosion-related data. This leads to the identification of trends and patterns that were previously difficult to detect, allowing for better corrosion prediction and prevention.
- Modeling and simulation: Digital tools enable the creation of complex models and simulations that can predict how corrosion will behave under different conditions. This is particularly useful for designing new materials and structures, as well as planning preventive measures.
- Asset management and predictive maintenance: Integrating asset management systems with corrosion data allows companies to implement predictive maintenance strategies. Instead of performing maintenance based on fixed intervals, companies proactively invest when data indicates a risk of corrosion, thus optimizing resources and extending the lifespan of assets.
- Collaboration and information sharing: Digitalization facilitates the exchange of information and knowledge about corrosion among different stakeholders, including companies, researchers, and regulators. This promotes a better understanding and management of corrosion on a global scale.
- Training and education: The availability of digital educational resources, such as online courses, webinars, and electronically accessible specialized literature, enhances the training of professionals in corrosion management. This is vital to stay up to date with the latest technologies and methodologies in a constantly evolving field.
Advantages of digitalization in corrosion management
Digitalization en compasses a broad spectrum of benefits for corrosion management. By facilitating real-time corrosion monitoring and data-driven corrosion management, companies can now make informed decisions more quickly, improving the accuracy in risk identification and the effectiveness of corrective measures.
Moreover, the ability to analyse large volumes of historical and real-time data enhances understanding of the conditions conducive to corrosion, enabling the development of more robust predictive and preventive maintenance strategies. These advantages not only reduce the cost associated with maintenance and repair of corrosion damage, but also significantly enhance worker safety and environmental protection.
Recent developments and applications
Recent technological advances in corrosion management include the development of advanced sensors capable of detecting and measuring corrosion factors with unprecedented accuracy. These devices, along with powerful data analysis systems, have enabled organizations to monitor the integrity of their assets in real-time preventively and continuously, reducing corrosion failures, decreasing maintenance costs, and extending the lifespan of their assets by several years. This success underscores the potential of digitalization to transform corrosion management across various sectors.
Challenges and future of digitalization in corrosion management
Despite its clear advantages, the adoption of digitalization in corrosion management is not without challenges. Resistance to change, the need for significant investments in technology and training, concerns about data security or cybersecurity management, and data standardization are common obstacles.
However, with the continued evolution of digital technologies and a growing understanding of their benefits, these challenges are expected to be gradually overcome. The future of advancement in corrosion management points towards greater integration of artificial intelligence and machine learning, promising not only to further optimize monitoring and prevention, but also to revolutionize how industries manage this inevitable phenomenon.
Conclusion
Digital transformation in corrosion management is redefining the landscape of this area, offering innovative solutions with more proactive and predictive approaches that enhance efficiency, safety, and sustainability. Through real-time corrosion monitoring and data-driven corrosion management, organizations are much better equipped to tackle this persistent challenge, and as technologies continue to evolve, we will see more innovations and applications in this field. The key point for future success will be organizations’ ability to adapt, invest, and harness these digital technologies in their fight against corrosion.
References
Own source.