Corrosion is a natural process of material degradation, with multiple consequences, not only economic (1), but also environmental and human. Current research has focused its studies on the problems presented by metallic corrosion, caused by the progressive deterioration of the environment. These studies have highlighted the influence of atmospheric pollution, especially in marine, urban and industrial areas, on the corrosion rate of different materials. The results have highlighted the relationship that environmental contamination has on corrosion. However, there are few studies on the reverse case in relation to the effect that corrosion has on the environment.
In this context, a brief review of the means by which corrosion acts on the environment, as well as the effects caused by this action, is presented. At the end, a brief description of the corrosion problems affecting BWR type nuclear power plants is presented.
Most frequent causes of corrosion in different sectors that lead to damage
In the case of nuclear power plants (Figure 1), there is very little information on cases in which corrosion has been the direct cause of radioactivity leakage, possibly due to the strict control of materials and components, as well as the relatively small number of installations. A review of the problems affecting BWR (boiling water) nuclear power plants has recently been carried out.
Intergranular stress cracking cracking failures (IGSCC) in type 304 and 316 stainless steels are very common in certain components of systems used for energy transformation [1]. In the second half of the 1970s, serious problems related to intergranular cracking under mechanical stress appeared in 304 and 316 stainless steel pipes used in boiling water reactor (BWR) nuclear reactors. The failures were specifically located in the areas affected by the heat resulting from a welding process.
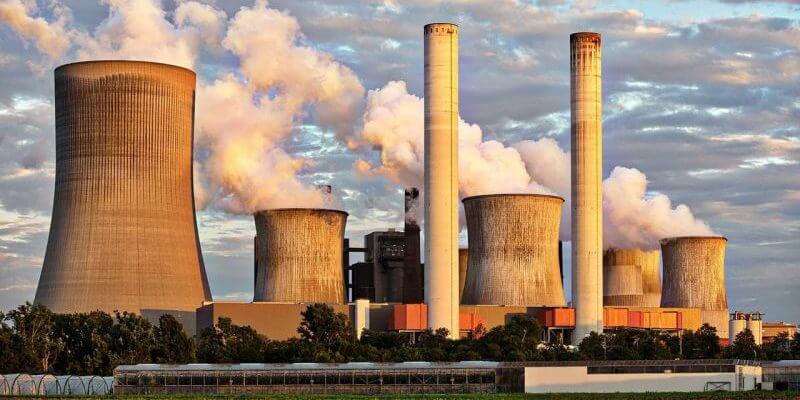
The causes of these failures are the result of the interaction of three factors: a) a tensile stress (close to the source stress), b) the aqueous medium, and c) the presence of chromium carbides precipitated along the austenitic grain boundaries of a stainless steel. This precipitation usually leaves chromium-depleted zones, which are susceptible to severe attack in the environment in which the alloy is found.
The boiling water reactor (BWR) environment consists essentially of pure water with an oxygen content ranging between 0.2 and 0.8 mg/1 at a temperature of 289 ºC. When the system is at lower temperatures, i.e. during start-up and shutdown periods, the oxygen level may reach the higher level of the indicated range. It has been shown that increasing the dissolved oxygen content results in an increase in intergranular stress corrosion.
A sensitized microstructure can be produced in the same flat section of the tube when it is joined to another tube by welding. Material in a zone parallel to, but not adjacent to, the weld bead is usually exposed to the critical temperature range of 430 to 870 ºC. Under these conditions, a mixed precipitation of chromium and iron carbides can occur at austenitic grain boundaries, preferably rich in chromium. However, it has been demonstrated in laboratory tests that significant amounts of precipitated chromium carbides can be produced at temperatures as low as 289 ºC, which corresponds to the normal operating temperature of BWR type reactors. The necessary condition for this precipitation to occur is that some chromium carbide precipitates serving as nuclei must be present beforehand. These may be formed previously during welding or may already be present in parts that have not been properly annealed during the forming process.
During the service inspections to which the systems and circuits of nuclear power plants are subjected, cracks have been detected in some very specific locations. The occurrence of cracks in austenitic stainless steel piping in BWR-type reactors has been occurring since the introduction of the first commercial plant. The cracks are located in the weld-affected heat zone of 304 and 316 steel pipes due to an intergranular stress corrosion cracking mechanism (IGSCC). Although cracks have also been detected in pressurized water plants (PWR), in these the incidence has been lower, since the components affected in this case are almost always in the secondary circuit, and have less impact on reactor safety.
Offshore wells and platforms
In offshore oil wells and platforms, accidents are more numerous (3), causing large crude oil leaks and their causes are usually unrelated to corrosion (human error, structural failures due to storms, etc.).
The sectors where corrosion has had strong consequences and damage to the environment are the chemical and petrochemical sectors. However, no significant information is available on the types or forms of corrosion that have been most frequently involved in these cases. (4).
Environmental pollution is a growing concern worldwide. Figure 2 shows an oil containment boom that limits the spread of an oil leak from a corroded pipeline. During the 1990s, the United States and Canada called for the replacement of all subway storage tanks (USTs) at service stations and similar operating locations with double-lined USTs due to repeated problems with groundwater contamination from leaks from corroded USTs.
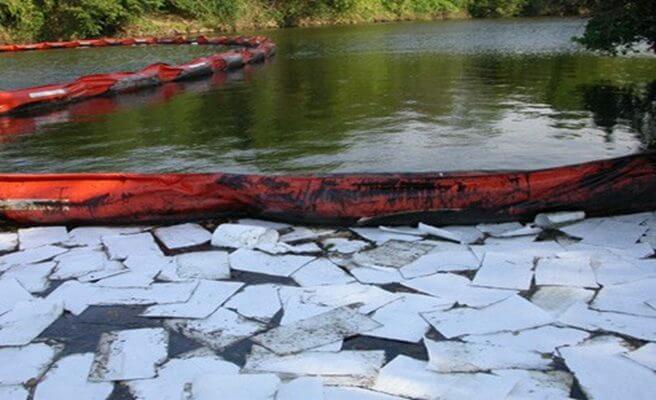
Conclution
In a number of cases, and especially in chemical plants, corrosion can cause or contribute to accidents that have a serious impact on the environment. These accidents are usually of short duration, but of great intensity. In addition to material losses, the consequences on the population can be fatal or long-lasting.
Thus, there is a clear need to take extreme care in preventing corrosion in those plants which, due to the degree of danger of the products processed in them or their storage, are susceptible to this type of accident. This prevention, often present in the initial design, is reduced when the plant undergoes structural and operational modifications that are not in accordance with the initial safety requirements.
Bibliographic references
1. J. Genescá and J. Ávila, “Corrosion of austenitic stainless steels”, in Revista de Corrosión (AMIC), 3(7)23(1992).
3. Offshore Accident Review, O. Fagerjord, vol. 3, No. 2, p.8, 1985.
4. G. Gavelli, C. Scala and V. Colombari, Reliability of Engineering Materials, Eds. A. L. Smith, Butterworths, London, 1982, p.115.
5. A. Romano, N. Piccinini and G. C. Bello, Chemical Engineering, pp. 200, 211, 1985.
6. Bhopal Methyl Isocyanate Incident Investigation Team Report, Union Garbide Corporation, Danbury, Gonn. 1985.