Introduction
Corrosion is a natural and spontaneous process that consists of the process of deterioration of metallic materials through chemical and electrochemical reactions; whereby metals always return to their most stable or lowest energy state, in their oxidized form. This article focuses on the description and mechanism of corrosion and control methods for its prevention.
The effect of corrosion in the oil industry leads to the failure of facilities and therefore to the closure or stoppage of industrial plants. However, periodic and optimal maintenance; as well as adequate protection of metal structures, it can delay the start of corrosion in structures for a long time.
Corrosion is one of the most persistent natural problems in any company and the oil industry is not the exception of the corrosive processes of metallic structures, producing economic losses in the replacement of structures, pipes, equipment, apart from other costs that are more difficult to detect associated with indirect losses due to product spills, risk of accidents in oil pipelines, and stoppages of industrial plants due to breakdown of equipment, such as: boilers and heat exchangers, etc. Generating great disasters to humanity and deterioration of the environment.
Costs associated with corrosion damage
Since the beginning of the 20th century, concern about the costs of corrosion has been increasing over time, therefore, several measures have been taken to try to control the losses caused by corrosion, thus reducing the costs associated with this. process.
Several investigations have been carried out in order to determine the costs associated with corrosion, especially by the studies collected by NACE. The study which is called “Corrosion Costs and Preventive Strategies in the United States”, conducted by Koch et al. in 1988 [1], who estimated the cost for corrosion control methods and services. They reported the economic impact of corrosion for specific industry sectors, in which the annual direct cost was $276 billion dollars, equivalent to 3.1% of the Gross Domestic Product (GDP), due to the problems caused by corrosion.
This study published in 2002 by NACE examines each sector in depth, providing discussions on the causes, costs and results of corrosion. For this reason, the importance of controlling and dealing with this deterioration is highlighted, since it is an important industrial problem, which can affect both the safety and the assets of a company.
The corrosion process is classified according to form and medium. Regarding the form, it can be classified as uniform or localized and according to the medium: chemical, also called dry corrosion, and electrochemical or wet corrosion. Uniform corrosion occurs when the material does not exhibit differences in its microstructure and the environment in which it is immersed has a uniform composition. This corrosion extends over the entire surface and the damage it causes to the element is foreseeable. This type of corrosion is less damaging than localized corrosion.
Corrosion mechanisms: Corrosion as an electrochemical process
The degradation mechanisms are associated with a damage morphology that involves a series of chemical reactions that depend on the exposure environment, temperature and operational parameters in service. Depending on the nature of the environment, corrosion can be dry or wet: At high temperatures the system is dry and obeys the laws of the kinetics of heterogeneous solid-gas reactions, among the most common mechanisms are carburization and decarburization. In the presence of moisture, anodic and cathodic reactions occur at the metal interface with acidic, basic or neutral media (electrochemical mechanisms).
Most of the electrochemical corrosion processes in metals involve the transfer of electronic charge in aqueous solutions, which, in turn, are generated by the reactions that occur between the metal surface and the solution. This electrochemical process requires anodes and cathodes in electrical contact and a transfer of ions through an electrolyte, so that the transfer of electrons between the surfaces of the anode and the cathode can be carried out; the velocity of this flow corresponds to the rates of the oxidation and reduction reactions that occur at the surfaces[2].
Figure 1 shows a simple representation of the oxidation of iron, to illustrate this type of electrochemical corrosion. In the presence of an aerated [H2O] aqueous medium, iron[Fe] turns into ferrous ions [Fe2+], which act as the anode (oxidation reaction). Electrons are transported to the cathode, where in the presence of oxygen [O2], iron oxides are formed.[FexOx] , as rust deposits or precipitates (reduction reaction). A byproduct of the reaction at the cathode is hydroxyl ions.[OH–] (hydrated oxides) resulting from the reduction of hydrogen peroxide.
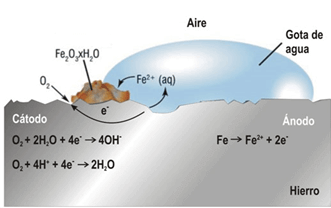
To understand corrosion processes, it is important to understand the degradation mechanisms that cause and favor this phenomenon, in order to apply the most appropriate control method. In the oil and gas industry, the most frequent types of corrosion are: exposure to carbon dioxide [CO2, sweet corrosion], hydrogen sulfide [H2S, acid corrosion] and oxygen [O2], and microbiological corrosion [3]. Iron in the absence of O2 and in environments containing CO2 and H2S, can react forming ferrous carbonate [FeCO3 ] and iron sulfides [FexSx] respectively, the cathodic reaction can generate hydrogen gas [H2].
The CO2 in contact with water in oil and gas production or transportation systems, it affects the innermost parts of the well (production string), collection networks and conduction lines, generating reaction products such as carbonic acid, ferrous carbonate [FeCO3] and hydrogen gas [H2][4], This type of corrosion occurs at a gas partial pressure of 21 kPa. [3 lpc].
To prevent this type of corrosion, operators normally use organic films that act as barriers and inhibitors that neutralize the acidity of the carbonic acid generated during corrosion. Operators can also use alloys that are resistant to uniform and localized corrosion, in environments that are corrosive to carbon and low-alloy steels.
How can we control corrosion?
Corrosion is a major problem to be avoided in any structure made of metal. If we need to install some type of metal structure in the industry, it is important that we take into account the following factors [5,6].
- Use in the manufacture of metal structures high quality materials and high resistance to corrosion.
- Know the environmental conditions (humidity, temperature, etc.). Since not all metals, and even not all stainless steels, are equally resistant to corrosion in all conditions.
- Know the type of substances with which the structure can come into contact and use the most suitable material.
- There are treatments to prevent corrosion in metals. By applying a coating, direct contact of potentially corrosive substances or fluids with the metal is avoided. Apply non-metallic coating treatments (painting, oiling, enameling, ceramics, etc.); as well as metal coatings with various chemical procedures or the use of special alloys. Some treatments will be specific to certain industrial applications.
- Keep metal and stainless steel structures and surfaces clean. In order to prevent the treated metal or stainless steel from losing the passive surface layer. The loss of this layer can cause a corrosion reaction and deterioration of the structure.
- Inspect points where corrosion may appear and repair damage. Corrosion can start at some points for various reasons: permanent accumulation of dirt or corrosive substances; physical breakdown of the coating, environmental conditions, etc. Once the corrosion process has started, it can spread until it completely damages the metal structure. For this reason, adequate maintenance and repair of the affected areas is essential.
- Along with resistance to corrosion, the materials must also meet other specific requirements for each industrial or technological application (resistance, ductility, welding properties and finishes, etc.).
- The most important thing is to know and apply the most appropriate control method (corrosion inhibitors, cathodic protection, coatings, etc.), for each type of corrosion and to follow the rules of conservation of structures, which is essential to reduce damage. caused by corrosion and the safety and breakdown problems associated with this problem.
References
- G. Koch, M. Brongers, N. Thompson, Payer, and J. Payer, “Corrosion Costs and Preventive Strategies in the United States” PUBLICATION No. FHWA-RD-01-156.
- Popoola LT, Grema AS, Latinwo GK, Gutti B, and Balogun AS: “Corrosion Problems During Oil and Gas Production and Its Mitigation,” International Journal of Industrial Chemistry 4, no. 1 (2013). Chillingar et al.
- Heidersbach R: Metallurgy and Corrosion Control in Oil and Gas Production. Hoboken, NJ, USA: John Wiley & Sons, Inc., 2011.
- Revie RW and Uhlig HH(2008). Corrosion and Corrosion Control – An Introduction to Corrosion Science and Engineering. Wiley & Sons, Inc: USA. Schweitzer. PA (2010).
- Fundamentals of Corrosion – Mechanisms, Causes and Preventive Methods. Taylor & Francis Group, LLC: USA.