Corrosion control is a problem in industries, especially in sectors that depend on pipelines for the transport of fluids such as oil, gas and water, such as the petroleum, petrochemical and nuclear sectors. Internal corrosion of pipelines, if not properly controlled, can lead to catastrophic failures, environmental damage, loss of life and large financial losses.
Detecting and monitoring corrosion in pipelines is crucial to ensure the integrity and safety of infrastructures. Traditional inspection methods often face limitations, especially when dealing with small diameter pipes. However, technological advances, particularly in Phase Array Ultrasonic Testing (PAUT), have revolutionized the method of corrosion mapping, even in these challenging environments.
Importance of corrosion control in small diameter pipelines
Pipeline corrosion is a persistent problem facing the industry, and when it comes to small diameter pipelines, the challenges can be even greater because they are more prone to certain types of corrosion and can be difficult to monitor and maintain.
Corrosion in this type of pipeline can manifest itself in several ways, including uniform corrosion, pitting corrosion and erosion corrosion. These problems can be exacerbated by factors such as the composition of the transported fluid, environmental conditions and the presence of impurities in the system. In addition, lack of adequate access for inspection and maintenance can hinder early detection and treatment of corrosion.
To address these challenges, it is crucial to implement corrosion control management strategies. This includes the selection of corrosion-resistant materials, regular monitoring of pipeline condition through techniques such as visual inspection, non-destructive testing and on-line corrosion monitoring, and the implementation of preventive maintenance practices such as cleaning and surface coating.
What is the corrosion mapping technique with PAUT?
Ultrasonic ph ased array corrosion mapping is a non-destructive testing technique used to evaluate the extent and location of corrosion on metallic structures such as pipelines, vessels or other critical infrastructure. Phased array ultrasound testing (PAUT) uses multiple ultrasonic elements arranged in an array to generate and receive ultrasonic waves.
During the inspection process, the phase array probe moves over the surface of the material under test. When the waves encounter a change in material properties, such as corrosion or defects, they are reflected back to the probe.
This capability enables accurate imaging and mapping of internal structures for corrosion monitoring, including the presence and extent of corrosion, allowing inspectors to identify critical areas, assess corrosion damage and make informed decisions about maintenance and repair.
Corrosion control through PAUT in minor pipelines
In small diameter pipelines, conventional inspection techniques may have difficulties due to limited access and space constraints. However, PAUT offers a solution to provide high-resolution images of internal pipe surfaces even in confined spaces by using specialized scanners and probes. As well as advanced signal processing algorithms, through which effective corrosion control can be achieved by accurately detecting and quantifying deterioration in small diameter pipelines.
Currently and from a commercial point of view, the large companies that have been developing PAUT inspection technologies offer accessories and applications in their instruments for corrosion mapping in small diameter pipelines and from 1 inch in diameter. However, at the research level, recent studies have shown that corrosion mapping can be performed on even smaller diameters, so it is possible that in the near future the necessary tools for corrosion control in a lower diameter range will be available.
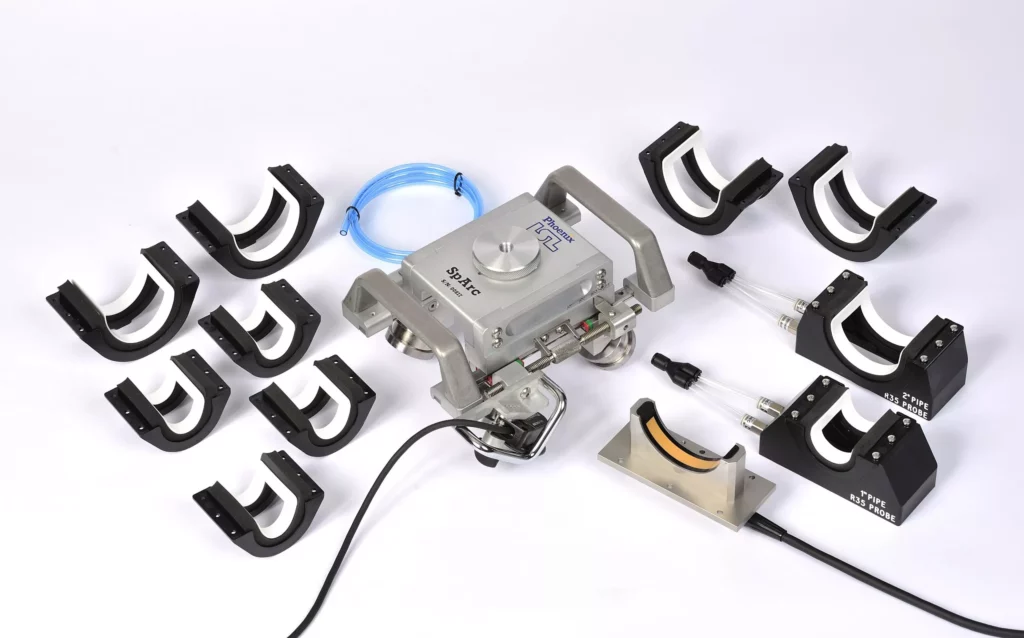
Benefits of PAUT for corrosion control of small diameter pipelines
- Accuracy: Provides highly detailed images of corrosion patterns, enabling accurate measurement and characterization of defects.
- Efficiency: Offers faster inspection times compared to traditional methods, reducing downtime and operating costs.
- Versatility: It adapts to various pipe materials and geometries, making it suitable for a wide range of applications.
- Safety: It is a non-destructive testing method, minimizing the risk of damage to the pipe during the inspection.
Below is a video about the new NAVIC scanner, an automated modular solution for corrosion mapping and weld scanning. Courtesy of: JIREH Industry.
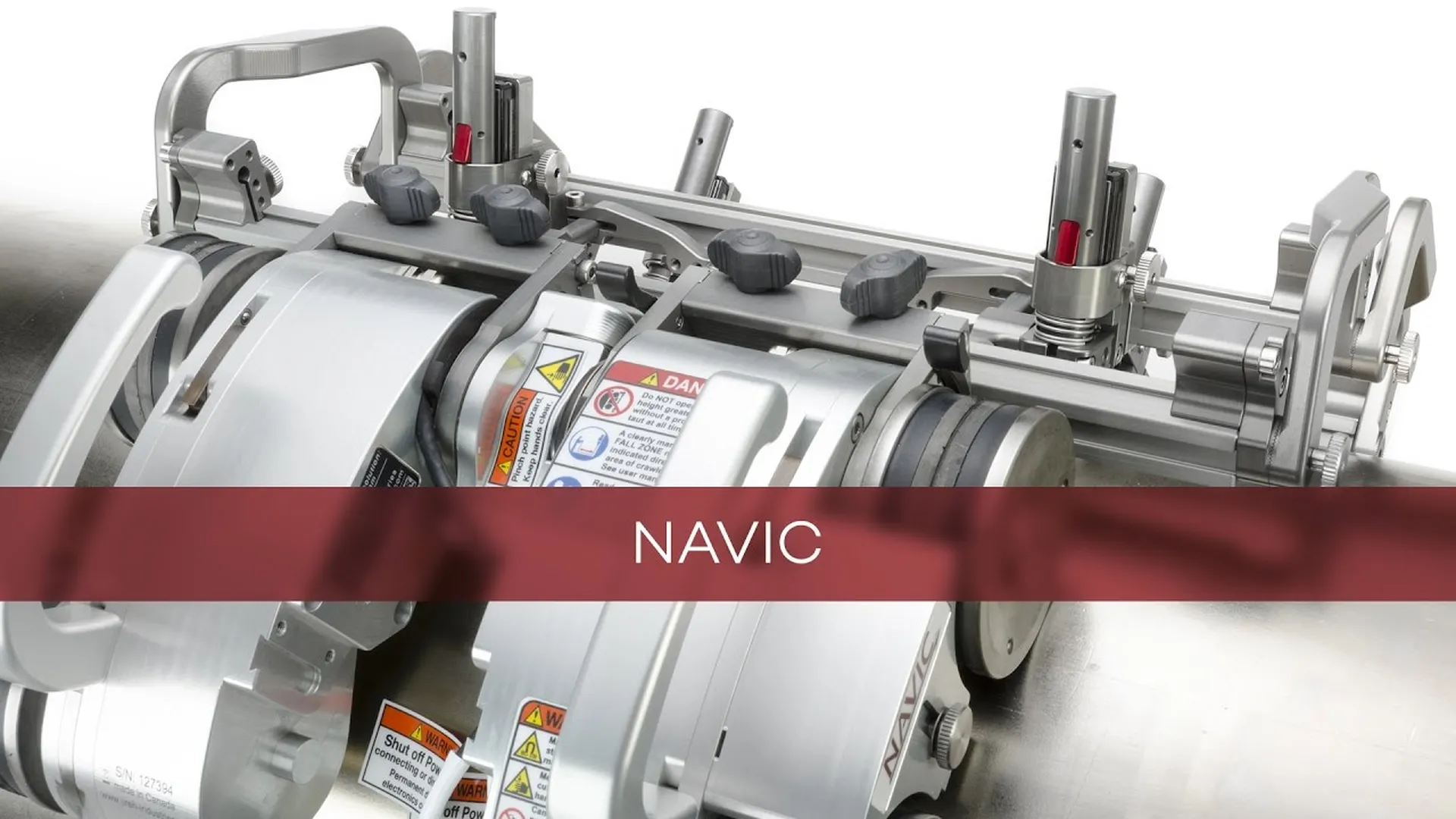
Escáner NAVIC para inspección de soldadura y mapeos de corrosión en tuberías. (Fuente: JIREH)
Conclusion
Phase Array Ultrasonic Testing represents a novel technique for corrosion mapping in small diameter pipelines, offering accuracy, efficiency and versatility for corrosion control. With technological advances and ongoing research, PAUT continues to evolve and provide industries with the means to safeguard their infrastructure and ensure operational integrity. As the demand for reliable inspection methods increases, PAUT is poised to play a pivotal role in addressing the challenges of corrosion detection in small diameter pipelines.
References
- NEIL PEARSON. The Efficiency of Phased Array UT for Corrosion Mapping; Accessed February 29, 2024. https://blog.eddyfi.com/en/the-efficiency-of-phased-array-ut-for-corrosion-mapping?_gl=1*1jyppdy*_up*MQ..*_ga*MTM4NjAxMjA4MC4xNzA1MzMzMzcx*_ga_Q4YHE7GCQH*MTcwOTU2MjY1Ni4yNS4wLjE3MDk1NjI2NTYuNjAuMC4w&gclid=EAIaIQobChMIlr2dn-jahAMV_KRaBR1J0gHhEAAYAiAAEgLaYPD_BwE
- CARLOS TRIVENO. The latest about an effective corrosion mapping with Phased Array UT; Accessed March 01, 2024. https://www.linkedin.com/pulse/effective-corrosion-mapping-pa-ut-carlos-a-trive%C3%B1o/
- EVIDENT. Corrosion Mapping on Carbon Steel Using the RollerFORM Scanner; Accessed March 11, 2024. https://www.olympus-ims.com/en/corrosion-mapping-on-carbon-steel-using-the-rollerform-scanner/
- FLORIN TURCU, TIMON JEDAMSKI, AND DR. DIRK TREPPMANN. In-service Corrosion Mapping-Challenges for the Chemical Industry; Accessed March 4, 2024. https://www.ndt.net/article/ecndt2018/papers/ecndt-0075-2018.pdf
- Phoenix ISL. Corrosion Mapping/ C-Scan Inspection; Accessed February 22, 2024. https://www.phoenixisl.com/industries-we-serve/corrosion-mapping-c-scan-inspect