Author: Jesus V, November 4, 2023.
Introduction
Corrosion is defined as the deterioration of a metal or alloy due to a chemical or electrochemical reaction with its environment. These materials are essential for the construction of infrastructures, platforms, tanks and pipes, among others, in the industry in general. In this article we will discuss corrosion in the Oil & gas industry.
It manifests itself when metals, subjected to specific environmental conditions, return to their original oxide state. This destructive process threatens the integrity of the structures, endangering safety and operability.
The oil and gas industry has a great impact on global energy production 1 , however, for its optimal functioning, corrosion must be managed and controlled , in order to avoid serious consequences, which we will learn about below.
The corrosive process
The corrosion process of a metal consists of the chemical or electrochemical interactions of the material with the environment 2 , specifically in contact with water and oxygen. Through these interactions, the surface of the active ingredient is gradually destroyed due to a reaction with substances in its external environment 3 .
In the case of electrochemical interaction, known as galvanic corrosion, two different metals must generate a potential difference in a conductive medium 4 , such as water. In this way, one becomes an anode and the other a cathode, and as a result, the former loses ions to maintain a balance of electrons, thus generating the corrosive phenomenon.
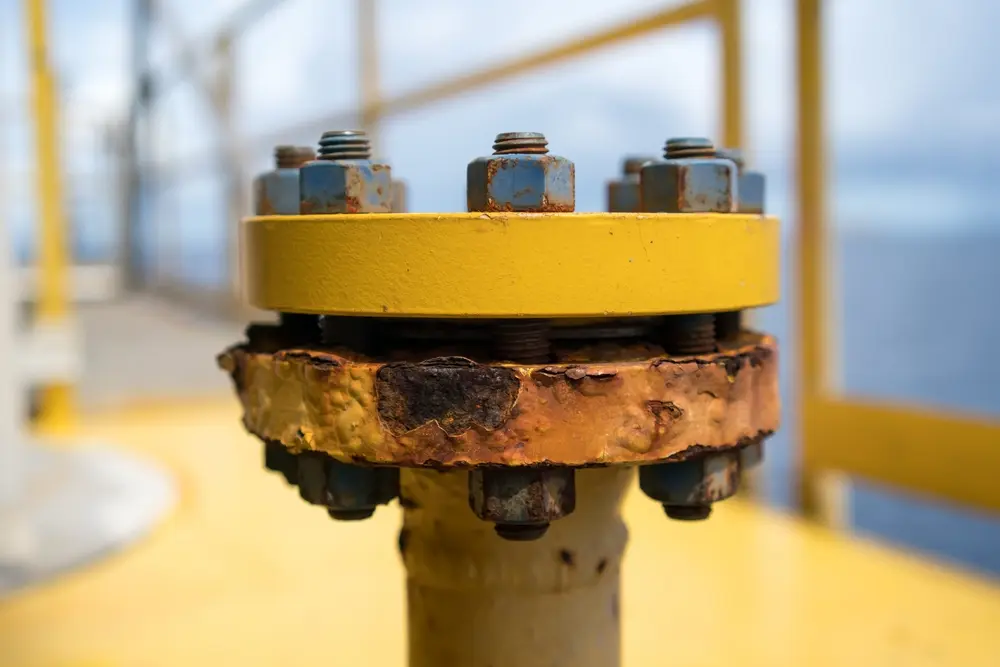
Due to the exposure of the oil and gas industry to the sea and its environment, corrosion is a natural reaction in this type of infrastructure (see figure 1). Therefore, it is common for companies that consider the maintenance of their facilities to be important to implement techniques such as the use of additives and coatings as a way to prevent and slow down the reaction.
Possible causes of corrosion
- Exposure to corrosive conditions: Conditions such as humidity and salinity are the most frequent in the generation of corrosion, however, there are additional agents such as gases, chemicals and other substances that can also accelerate this type of reaction in pipes and equipment.
- Lack of maintenance: Failure to have optimal maintenance focused on the detection and treatment of corrosion can lead to its formation and evolution.
- Lack or deterioration of coatings: Coatings serve as a way to protect the surface of structures from detonating agents. If it has a poor coating, or does not have one at all, the deterioration of the materials
- Isolation: When isolating equipment, it can be affected by a wide variety of external factors present in the environment where it is located. As a consequence, corrosion under insulation ( CUI ) can be generated, manifesting itself through a galvanic, acid or alkaline method, or else by chloride.
- Impurities in working fluids: In its natural state, the crude oil to be extracted has impurities in its composition. Some of these compounds are water, solid particles and sediments. Each of these presences in the fuel affect the pipes during transportation.
Consequences in the Oil & Gas Industry
- Leaks: Uncontrolled corrosion can expand through the pipes to generate leaks, as a consequence of the proportional wear. This effect can have serious consequences such as oil spills or gas leaks. Thus attacking the environment, and at the same time compromising the lives of the plant workers.
- Structural failures: The deterioration of infrastructure can trigger unfortunate events that threaten the integrity of those around them. Additionally, it could be the cause of interventions and sanctions due to the risks posed by the work environment.
- Production problems: The presence of high-grade corrosion in pipes, equipment and structures will require immediate changes to allow optimal work. With this, interruptions occur in the processes, causing periods of pause and decrease in production.
- Equipment deterioration: Failure to control the corrosive effects on the equipment will end up causing it to not have the desired performance, causing its useful life to be shorter. Likewise, the solution to this problem includes monetary expenses and changes in logistics.
Economic impact
From an economic perspective, the corrosion phenomenon imposes a significant financial burden on the Oil & Gas industry. Direct costs are linked to the need to repair or replace corroded equipment, which can represent considerable investments in maintenance and the purchase of replacement components.
According to estimates by the National Corrosion Association (NACE), the global economic impact of corrosion is estimated at 2.5 trillion dollars, equivalent to 3.4% of the world’s Gross Domestic Product in 2013. To this must be added the unexpected stops of operations, derived from failures attributable to corrosive deterioration, which adds an additional burden in terms of loss of production.
Significant indirect costs must also be taken into account. For example, inadequate pipeline integrity management can result in leaks that threaten the environment, giving rise to potential legal implications. Likewise, plant interruptions or stoppages due to equipment malfunction can affect the supply chain, exerting negative impacts on the availability of energy resources and triggering variations in prices.
Study cases
Silver Eagle Refinery (2009)
At the beginning of 2009, the Silver Eagle refinery was reporting failures, even causing a fire as a result of the release of a large cloud of flammable vapor from a storage tank 5 . As a result, four workers were injured, but the incident did not escalate into a major event.
Its largest incident would come on November 4, when one of its pipes suffered a rupture , thus triggering an explosion that caused great damage to the closest communities.
According to metallurgical studies, the main reason for the collapse of the pipe was the corrosion present in it, which was caused by the lack of maintenance over the years. Fortunately, there were no casualties in this incident, however, the community of Wood Cross, Utah, was marked by imminent terror as a result of the explosion that occurred.
Co-operative Refineries Limited (2011)
The unfortunate incident that took place at the company’s facilities took place on October 6, 2011. One of the infrastructure pipes had damage due to corrosion 6 , and this was not previously detected, causing wear to evolve until it ruptured.
As a result, a large fire formed that was accompanied by an explosion, harming workers near the area. Although there were no losses, a total of 52 people were injured, and approximately 13 people needed immediate medical attention due to their injuries.
Among the main factors of the accident was the fact that they previously implemented changes in their refining process, generating an increase in the corrosion rate. This, added to inadequate control of infrastructure degradation, led to the catastrophic event in a matter of time.
Richmond Refinery (2012)
On August 6, 2012, some workers at the Chevron industrial plant located in Richmond detected a small leak coming from one of the pipes. Due to the concerns this generated, the work team decided to remove the insulation of the pipe to better appreciate the cause of the leak; however, this action resulted in the formation of a vapor cloud due to a rupture 7 .
The reason for this was that the pipe had a decrease in its thickness as a result of internal corrosion that had been developing for a long time. Despite the intervention of the fire department, the poor condition of the pipe in question allowed the steam leak to increase until it completely covered the area, making it difficult for the workers to withdraw.
In a matter of minutes, the hydrocarbons reacted and formed a fire that ended up engulfing the Chevron facility. No worker’s life was involved during the event, however, approximately 15,000 people went to nearby hospitals for symptoms and illnesses related to the incident.
Conclusion
Effective corrosion management is important to prevent these consequences and protect the integrity of infrastructure, the safety of people and the environment. Furthermore, the economic impact of corrosion at a global level is significant, due to direct and indirect costs that affect the Oil & Gas industry and the economy in general. Therefore, it is essential to implement corrosion prevention and control strategies to safeguard both the safety and economic viability of this important industry.
References
- Andrade, A. (2023, June 28). The economic impact of corrosion in Oil and Gas . Retrieved November 1, 2023, from https://vidyatec.com/blog/economic-impact-corrosion-oil-and-gas/
- Andrade, A. (2022, August 2). The Corrosive Process in the Oil and Gas Industry . Retrieved November 1, 2023, from https://vidyatec.com/blog/the-corrosive-process-within-oil-and-gas/
- Corrosionpedia. (2019). What Does Chemical Corrosion Mean? . Retrieved November 1, 2023, from https://www.corrosionpedia.com/definition/6394/chemical-corrosion
- Brondel, D., Edwards, R., Hayman, A., Hill, D., Mehta, S., Semerad, T. (1994). Corrosion in the Oil Industry. Retrieved November 1, 2023, from https://www.slb.com/-/media/files/oilfield-review/p04-18
- US Chemical Safety Board. (2014, April 10). CSB Releases Analysis Showing Cause of Rupture and Hydrogen Blast in 2009 Silver Eagle Refinery Accident in Woods Cross, Utah. Retrieved November 2, 2023, from https://inspectioneering.com/news/2014-04-10/3854/csb-releases-analysis-showing-
- CTVNews. (2015). Co-op fined $280K in 2011 Regina refinery explosion. Retrieved November 2, 2023, from https://regina.ctvnews.ca/co-op-fined-280k-in-2011-regina-refinery-explosion-1.2371679#:~:text=In %20October% 202011 %2C% 20a %20corroded,negligence% 20put %20workers% 20at%20risk .
- The Guardian. (2012). Chevron refinery fire probe hones in on corrosion of decades-old pipe. Retrieved November 2, 2023, from https://www.theguardian.com/business/2012/aug/11/chevron-refinery-fire-inspection-pipe