Table of Contents
- Introduction
- What are confined spaces?
- Types of confined spaces
- Associated risks in confined spaces
- Working in confined spaces: Challenges and safety measures
- Standards and regulations for confined spaces
- PPE for confined spaces: Selection and proper use
- Inspection and maintenance of confined spaces
- Conclusions
- References
Introduction
Confined spaces pose hidden threats across multiple industries due to the unique conditions that hinder access and ventilation. These areas, while essential for operations like maintenance and construction, present significant safety risks if not properly managed.
Ensuring confined space safety involves not only understanding inherent hazards but also identifying the types of confined spaces, using appropriate equipment, adhering to rigorous procedures, and complying with specific regulations designed to prevent accidents and protect lives. Among these measures, the use of suitable personal protective equipment (PPE) is indispensable for mitigating risks.
Throughout this article, the main challenges of working in confined spaces, applicable regulations, the importance of PPE, and inspection and preventive maintenance measures have been addressed. These aspects are essential to ensure a safe and efficient working environment.
What are confined spaces?
A confined space is defined as an enclosed or partially enclosed area not designed for continuous human occupancy but may require entry for specific tasks. Key characteristics include limited access points, restricted ventilation, and potential atmospheric or physical hazards.
The process of identifying and classifying confined spaces is essential to ensuring workplace safety. OSHA establishes a clear two-step approach for this evaluation: identifying all confined spaces and determining which ones require specific permits. This video, courtesy of OSHA Training Services, provides a detailed explanation of OSHA’s criteria for defining a confined space, offering practical examples to facilitate understanding and application in the workplace:
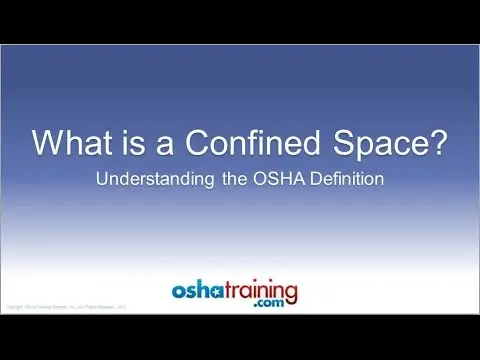
Identifying Confined spaces.
Common examples of such spaces include storage tanks, silos, sewers, tunnels, industrial reactors, and underground chambers. These examples illustrate how confined spaces are found in industries like petrochemicals, construction, mining, and agriculture.
It is crucial to distinguish between confined and restricted spaces. While both have limited access, the former implies additional hazards requiring specific control measures. For instance, a utility basement may be a restricted space, but if it poses risks such as toxic gases, it is classified as confined.
Understanding these spaces and their characteristics is the first step in implementing effective confined space safety strategies and preventing accidents.
Types of confined spaces
Confined spaces are classified based on the risks present:
- Atmospheric Risks
- Conditions such as oxygen deficiency, toxic gas accumulation (e.g., hydrogen sulfide), or the presence of flammable gases.
- Example: Tanks with chemical residues and minimal ventilation.
- Structural Risks
- Hazards like collapses, entrapments, or structural failures.
- Example: Construction tunnels with inadequate support systems.
- Fire or Explosion Risks
- Areas where flammable materials or explosive atmospheres can lead to severe accidents.
- Example: Spaces storing combustible liquids or fine powders such as flour or coal.
Each type of confined space requires specific evaluations to identify risks and plan safe interventions. Correctly identifying these risks minimizes accidents and enhances operational safety.
Associated risks in confined spaces
Confined spaces present various risks that must be carefully addressed:
- Atmospheric Risks
- Oxygen deficiency: Can cause asphyxiation within minutes.
- Toxic gases: Examples include carbon monoxide and hydrogen sulfide.
- Flammable gases: Risk of explosions when ignition sources are present.
- Mechanical Risks
- Entrapment: Moving machinery or components can trap workers.
- Impact from objects: Falling tools or materials in tight spaces.
- Falls: Complicated access points or slippery surfaces heighten the risk.
- Uncontrolled Energy
- Contact with energized electrical lines or improperly deactivated equipment.
- Psychological Risks
- Claustrophobia and stress from working in restricted environments.
- Mental fatigue, which can lead to human errors.
Mitigating these risks is essential to ensure safety and accident prevention. This requires rigorous procedures, proper equipment, and trained personnel. In this context, PPE, such as respirators and gas detectors, plays a crucial role in protecting workers’ lives.
Incident case: Confined space accident at a wastewater treatment plant
In July 2019, a tragic accident at a wastewater treatment plant in Ohio, USA, claimed the lives of two workers. The incident occurred when an employee entered a storage tank for maintenance without first assessing the confined space atmosphere. The tank contained hazardous levels of hydrogen sulfide (H₂S), a toxic and colorless gas that can cause unconsciousness and death within minutes.
When the first worker failed to respond, a coworker entered the tank to attempt a rescue, also without using the necessary PPE or following established confined space protocols. Both workers succumbed to poisoning before emergency teams could intervene.
Lessons learned
- Risk Assessment: The tank was not monitored for toxic gases or sufficient oxygen levels, violating OSHA 1910.146 regulations.
- Use of PPE: Neither worker had portable gas detectors or appropriate respirators, critical elements of confined space PPE.
- Inadequate Training: Lack of proper training on confined space risks and rescue procedures contributed to the tragedy.
- Entry Protocols: No entry permits were issued, nor was external supervision in place to monitor the confined space conditions.
Corrective Measures: After the incident, the plant implemented a robust safety training program, acquired advanced gas monitoring equipment, and reinforced mandatory PPE policies. Periodic drills were also established to enhance emergency response capabilities.
Impact: This case underscores the importance of strict adherence to protocols and using proper equipment to prevent confined space accidents. It reinforces the call for companies to invest in safety and training to protect workers’ lives.
Working in confined spaces: Challenges and safety measures
Working in various types of confined spaces or enclosed areas presents multiple challenges for workers due to the nature of these environments. Limited space and mobility hinder movement and task execution, while restricted communication complicates team coordination and emergency responses. These factors increase the risk of accidents and exposure to hazardous conditions.
To ensure confined space safety, it is essential to implement fundamental procedures, such as entry permits and access control, and select appropriate PPE. Proper ventilation and constant atmospheric monitoring are key to preventing the accumulation of toxic or flammable gases and ensuring safe oxygen levels. Additionally, continuous supervision by trained personnel is indispensable to detect incidents and respond promptly.
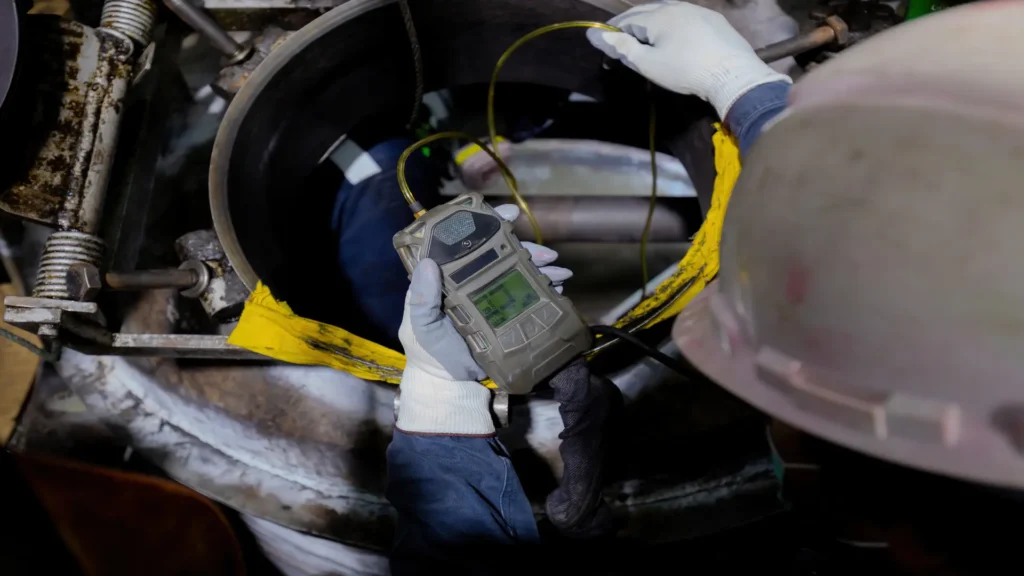
Technology also plays a crucial role in confined space safety for risk mitigation. Tools like portable gas detectors and remote monitoring systems enable real-time detection of hazardous conditions. Drones inspection and robots are gaining popularity as they can perform initial inspections without putting workers at risk.
Working in confined spaces requires a comprehensive safety approach combining technical, administrative, and technological measures to protect operators’ lives.
Standards and regulations for confined spaces
The Occupational Safety and Health Administration (OSHA) is an agency of the U.S. Department of Labor, established in 1970 under the Occupational Safety and Health Act. Its primary goal is to protect workers’ health and safety by reducing workplace hazards through the creation and enforcement of specific regulations. OSHA also provides training, education, and technical assistance to promote safe working environments.
Compliance with confined space standards is essential to reduce risks and ensure worker safety. OSHA 1910.146 establishes specific requirements for entering confined spaces in high-risk industries, while ISO 45001 provides a global framework for occupational health and safety management.
Key requirements include identifying confined space hazards, implementing safe entry procedures, and training involved personnel. In certain industries, such as oil and gas, advanced atmospheric monitoring and rescue systems are mandatory.
Continuous training is essential to ensure workers understand risks and know how to respond appropriately. An example of practical implementation is conducting periodic drills to test rescue procedures and assess the effectiveness of safety measures in a controlled environment.
Meeting confined space standards not only protects employees but also ensures legal compliance, minimizing potential penalties and improving operational productivity.
PPE for confined spaces: Selection and proper use
Personal Protective Equipment (PPE) for confined spaces is a critical element for safeguarding workers’ safety. Basic items include respirators to protect against contaminated atmospheres, portable gas detectors for monitoring environmental conditions, and harnesses with lifelines to prevent falls. Other important equipment includes safety helmets and durable gloves designed for specific conditions.
Proper PPE selection should be based on an environmental assessment, considering factors such as the presence of toxic gases, fall risks, or extreme confinement. Additionally, compliance with applicable regulations, such as OSHA 1910.146, which specifies minimum requirements for equipment used in these tasks, is crucial.
Maintaining and storing PPE for confined spaces is equally important. Respirators must be cleaned regularly, and gas detectors calibrated periodically to ensure functionality. Harnesses and lifelines should also be inspected before each use to detect potential damage.
Selecting and correctly using PPE for confined spaces is a fundamental measure to ensure safety and efficiency in these high-risk activities.
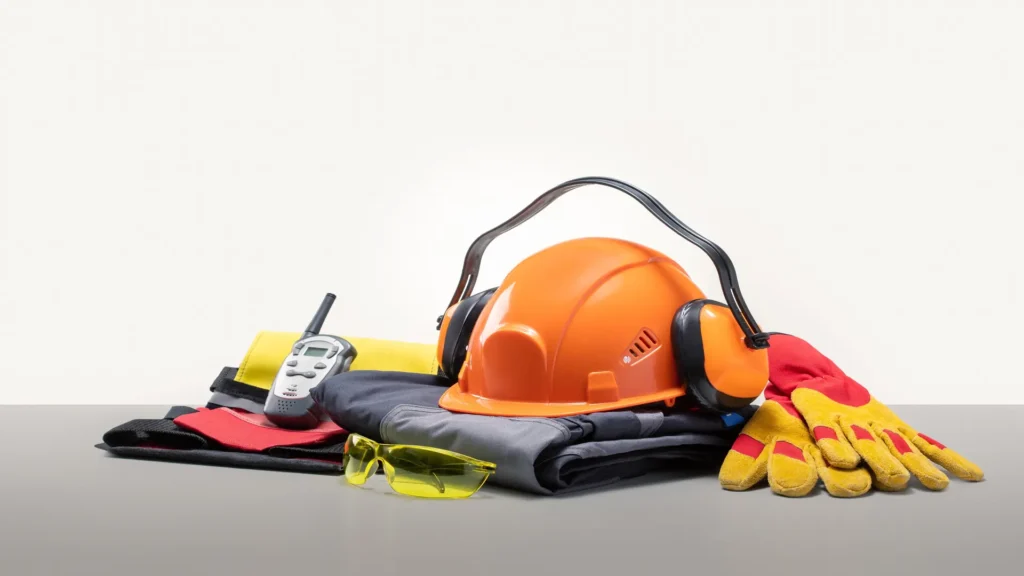
Inspection and maintenance of confined spaces
The inspection and maintenance of confined spaces are essential to ensure safety and prevent accidents. Periodic inspection and maintenance help identify risks such as dangerous gas accumulation, deteriorated structures, or equipment failures, mitigating potential incidents before they occur.
Common methods of atmospheric monitoring include portable gas detectors, which measure oxygen levels and detect toxic or flammable gases in real time. These devices are complemented by visual analysis and detailed inspection and maintenance of physical conditions, such as structural integrity, lighting, and accessibility.
Preventive inspection and maintenance play a fundamental role in confined space safety. This includes regularly checking and calibrating monitoring equipment, conducting detailed inspections of structures for corrosion or wear, and ensuring the proper functioning of ventilation and rescue systems. Routine inspection and maintenance not only address existing hazards but also improve the longevity of confined space infrastructure and equipment.
Implementing a robust inspection and maintenance program reduces the risks associated with confined spaces, protects workers’ lives, and ensures operational continuity across industries. Organizations that prioritize inspection and maintenance as a proactive strategy can effectively minimize safety risks while maintaining productivity.
Conclusions
Companies must adopt best safety practices, continuously train their personnel, and update procedures in line with current regulations. Investing in technology, such as advanced gas detectors or drones for remote inspection and thickness measurement, can significantly mitigate risks.
Looking to the future, technological innovations and advances in materials promise new solutions to improve safety in these environments. With proper implementation of these measures, it is possible to transform enclosed areas into safer environments for workers, reducing accidents and improving productivity.
Confined space safety is a fundamental pillar to protect lives and ensure operational continuity. Complying with specific regulations minimizes risks, and fosters a culture of prevention in organizations. By integrating safe practices, appropriate equipment and constant training, it is possible to significantly reduce incidents, strengthening the well-being of workers and the success of industrial operations.
Professionals and organizations, stay informed and committed to continuous learning to keep moving forward.
References
Own source