Introduction
A compressor is a device capable of increasing the pressure of a compressible fluid while reducing its volume. They are important components in the petroleum industry, playing a key role in the production, processing and transportation of natural gas through a variety of equipment, including pipelines, valves, separators and filters, by providing the necessary pressure and flow. Driving efficiency and profitability throughout the hydrocarbon supply chain.
In this article, we will address the importance of compressors in the oil industry, discuss the design and selection of this crucial equipment, and offer ideas for optimizing their performance and contributing to the success of oil production.
Importance of compressors in the oil industry
Compressors play many important roles in the oil industry. First, they are used to increase fluid pressure in oil wells, which facilitates the extraction and transport of crude oil from underground to the surface. In addition, compressors are indispensable in natural gas processing, where they are responsible for compressing the gas for transport over long distances through pipelines. Also, in refineries, compressors are essential for the compression of process gases and the generation of energy needed for production operations.
Similarly, compressors can be used to improve efficiency and recovery in natural gas production in oil fields. This is achieved by injecting compressed gas into wells to stimulate hydrocarbon flow and pressure, which contributes to more effective and convenient extraction of natural resources.
Criteria for compressor selection and design
The design and selection of compressors in the oil industry are critical processes that require careful consideration of several factors. First, it is critical to evaluate the specific operating conditions of each application, including gas flow rate, required discharge pressure, gas composition and ambient conditions. From this information, different types of compressors can be selected, such as centrifugal, positive displacement or axial compressors, each with their own advantages and limitations.
Compressors must be designed to withstand the extreme conditions and variable loads encountered in the oil industry. This includes consideration of corrosion resistance, compatibility with aggressive fluids present in oil and gas, and the ability to operate reliably in harsh environments such as extreme temperatures or high vibration levels. In addition, compressor design must be optimized to ensure energy efficiency and minimize operating costs over the life of the compressor.
Design evaluation and selection begins with a review of the different machinery configurations available to address a wide variety of potential applications.
It is essential to establish clear descriptions of the components and subcomponents that make up a typical centrifugal compressor before addressing these configurations. Some common terms within the industry need precise definitions to maintain consistency in the analysis.
While it is impossible to address all available configurations, the goal is to provide a detailed description along with supporting information on the most commonly used designs. Figure 1 shows an image of a four-stage axial compressor1.

As new applications emerge and designs evolve, it is important for users and buyers to evaluate and understand the advantages and disadvantages of each specific configuration.
Compressors in hydrogen production
Currently, most compressors used for hydrogen gas compression are positive displacement compressors, such as reciprocating or reciprocating compressors. These use a controlled piston to compress the hydrogen, thus reducing its volume and increasing its pressure, and are ideal for applications that demand a high compression ratio.
On the other hand, centrifugal compressors are also used in hydrogen compression, especially in pipeline transport applications. Due to the low molecular weight of hydrogen, centrifugal compressors need to operate at higher peak speeds than in the case of compressors used for natural gases. However, their efficiency and moderate compression ratio make them a favorable choice for these applications, a representative image of this type of compressor can be seen in Figure 2.
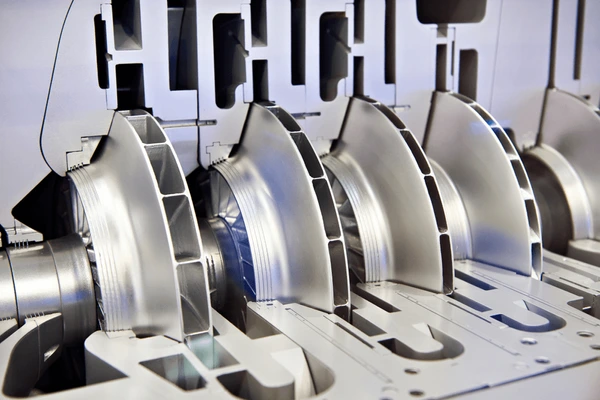
Compressors in energy sustainability
Compressors play a key role in CCUS (Carbon Capture, Utilization and Storage) projects by compressing carbon dioxide (CO₂) for subsequent transport and storage.
This compression is necessary to capture carbon emissions from the most difficult to reduce industries and move them to suitable storage sites. Current compression technology has been developed to handle CO₂, taking into account its highly corrosive properties.
CCUS systems and processes vary depending on the size of the plant and the specific application. Generally, a storage pressure of at least 1600 psia is required, while current pipeline specifications can reach 2215 psia. To minimize variable operating and maintenance costs in CCUS systems, it is crucial to integrate efficient and reliable compression technologies into the capture process.
Compressors are vital elements in the decarbonization of the oil and gas sector for many reasons:
- Carbon capture and storage (CCS) technology: Designed to pressurize and transport CO₂ generated by industrial processes, including those in the oil and gas sector.
- Natural gas processing: In natural gas processing facilities, compressors are indispensable for compressing the raw gas coming from wells, facilitating its transport through pipelines to treatment plants where impurities such as CO₂ and H2S. This helps reduce emissions by efficiently purifying the gas.
- Hydrogen production: Compressors are significant in the production of hydrogen through processes such as steam methane reforming and electrolysis. In these processes, they are used to pressurize hydrogen gas for purification and storage, thus contributing to obtaining a clean and renewable energy source.
Conclusion
Compressors are necessary devices in oil production because they provide the power needed to drive operations throughout the hydrocarbon supply chain. Their proper design and selection are critical to ensure optimum performance and reliable operation in demanding environments. By continuing to explore the latest innovations and trends in the industry, we can drive the development and efficiency of compressors, thus contributing to the continued success of the oil industry worldwide.
References
- Vorreiter Arne, Fische S, Saathoff H, Radespiel R; “Numerical investigations of the circulation efficiency in a compressor”; Journal of Turbomachinery, 134 (2), March 2012.