Table of Contents
- Introduction
- Fundamentals of cathodic protection in storage tanks
- Why is it necessary to design cathodic protection and coatings on storage tanks?
- What are Volatile Corrosion Inhibitors (VCI) and how do they work?
- Synergy between coatings, cathodic protection and vapor inhibitors
- Relevant case studies in the oil industry
- What are the main factors to consider when choosing between CP and VCI to protect a storage tank?
- Benefits of synergetic protection in storage tanks
- Conclusion
- References
Introduction
Corrosion in storage tanks represents a complex and costly problem in the oil, gas and chemical industry, particularly degradation in the bottom plates of storage tanks in direct contact with the ground. Traditional mitigation methods, such as coatings and cathodic protection (CP), have proven to be effective, but have limitations in certain environments. The incorporation of vapor corrosion inhibitors (VCI) emerges as a complementary solution that, when combined with CP, can provide a more robust, functionally integrated, robust defense against corrosive subway environments.
This type of corrosion in tanks represents one of the most aggressive and silent forms of damage, because it occurs in an area that is not very visible and difficult to access for frequent inspections; therefore, it can progress undetected for long periods of time, compromising the structural integrity of the tank and generating significant risks of leaks, environmental contamination, operational losses and catastrophic failures.
This article aims to analyze the technical and operational interaction between protective coatings, cathodic protection and vapor corrosion inhibitors (VCI) as part of an alternative solution to mitigate corrosion in the bottom plates of storage tanks. Mechanisms of action, application conditions and criteria for selecting and combining these technologies to optimize protection, increase asset reliability and reduce total life-cycle costs at critical facilities in the energy sector are discussed.
Fundamentals of cathodic protection in storage tanks
Cathodic protection is an electrochemical technique that reduces the potential of steel, forcing it to behave as a cathode. It can be implemented by means of sacrificial anodes, which oxidize instead of the base metal, or by impressed current, where an external source supplies the current intensity necessary to maintain the structure within the protection potential according to the criteria NACE Standards: Performance Criteria for Cathodic Protection Systems. In the case of tanks, this technology is widely used to protect bottom plates in contact with aggressive soils or impregnated sand platforms.
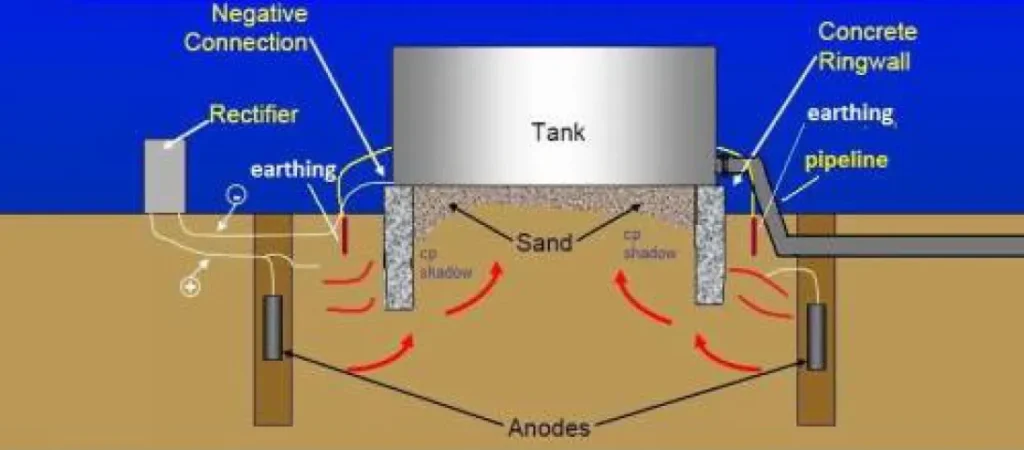
However, the presence of air spaces, dry areas or low electrical contact interfaces, such as in tanks on compacted sand, can reduce the efficiency of the CP system.
Why is it necessary to design cathodic protection and coatings on storage tanks?
The design of cathodic protection (CP) systems in storage tanks cannot be considered in isolation, but as part of a comprehensive corrosion mitigation strategy that includes the simultaneous use of coatings. This combination increases system efficiency, and significantly reduces long-term operating and maintenance costs.
Storage tanks, especially those built on wet, saline or chemical-impregnated soils, are exposed to severe corrosive conditions. Bottom plates, in particular, are vulnerable to soil corrosion due to the accumulation of moisture, oxygen and other electrolytes that favor the formation of galvanic cells. In this context, cathodic protection acts as an active system by injecting current into the metal structure, shifting the metal potential to a safe zone where oxidation does not occur.
However, when the metal is fully exposed to the medium without any coating, the current density needed to achieve full protection is high, which demands a higher consumption of anodes (either sacrificial or impressed current) and an increase in energy requirements. This is where coatings play a crucial role. By reducing the exposed surface area of the metal to the electrolyte, coatings act as physical barriers that decrease the current demand of the PC system. As a result, anode life is extended, the need for corrective maintenance is reduced and the energy efficiency of the system is improved.
From a regulatory standpoint, standards such as NACE (now AMPP) and API explicitly recommend the combination of PC with coatings as best practice for tank bottom protection. This synergy ensures a more uniform distribution of the protection potential, minimizes the formation of shaded zones (areas without adequate protection) and facilitates monitoring by techniques such as potential mapping or the use of corrosion probes.
What are Volatile Corrosion Inhibitors (VCI) and how do they work?
These types of corrosion inhibitors are volatile compounds that sublimate and diffuse into confined spaces, forming a protective film on metal surfaces (Figure 3). This film interrupts the electrochemical reactions necessary for corrosion to progress, protecting both wet and dry areas, even where cathodic protection does not reach. Corrosion protection is obtained thanks to the adsorption action of the inhibitor on the metal surfaces, promoting hydrophobic interactions and ionic bonds that block corrosive processes.
They reach areas that are difficult to inspect and represent an ideal control method to complement CP systems with coatings in complex geometries or environments with low relative humidity.
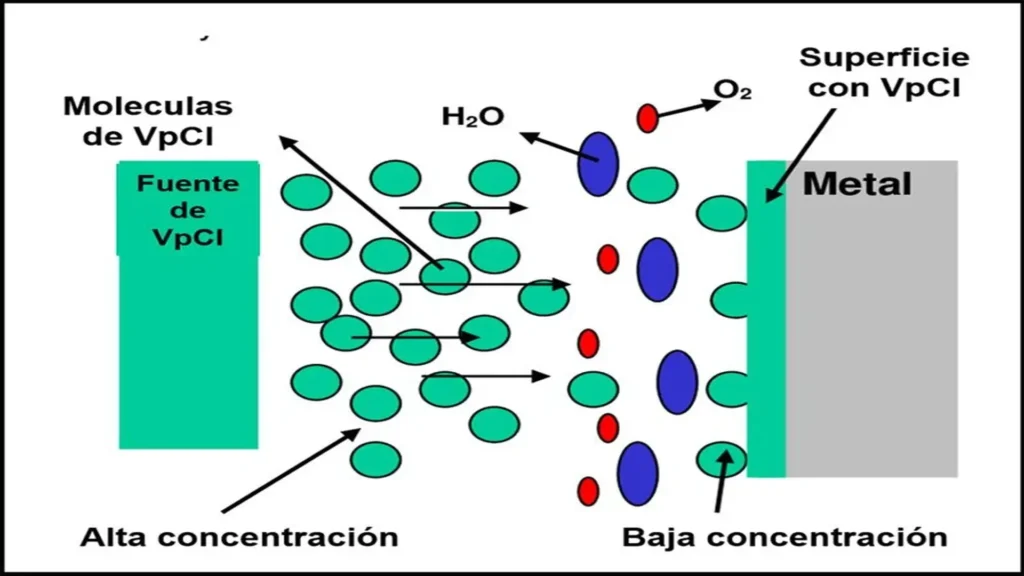
These function on the principle of Fick’s law of diffusion, which describes the movement of molecules from a zone of higher concentration to a zone of lower concentration until an equilibrium state is reached. Inhibitor molecules in the vapor phase volatilize or sublimate, increasing in concentration until the pressure within an enclosed space is equalized. If the equilibrium pressure decreases to a critical level, the inhibitor begins to activate until the inhibitor is completely consumed.
Why is it necessary to integrate corrosion inhibitors in systems protected with cathodic protection and coatings?
Traditionally, the protection of these surfaces by the application of impressed current cathodic protection (CP) or sacrificial anodes is reinforced with protective coatings, which function adequately when soil and design conditions permit.
As the liquid level in the tank changes, the tank bottom undulates and loses contact with the ground. When this occurs, air pockets are created between the bottom of the tank and the soil beneath the tank. Moisture and chlorides in the air penetrate below the tank bottom through the spaces between the tank ring plates and the foundation (concrete ring) and accumulate in these pockets creating corrosion initiation sites.
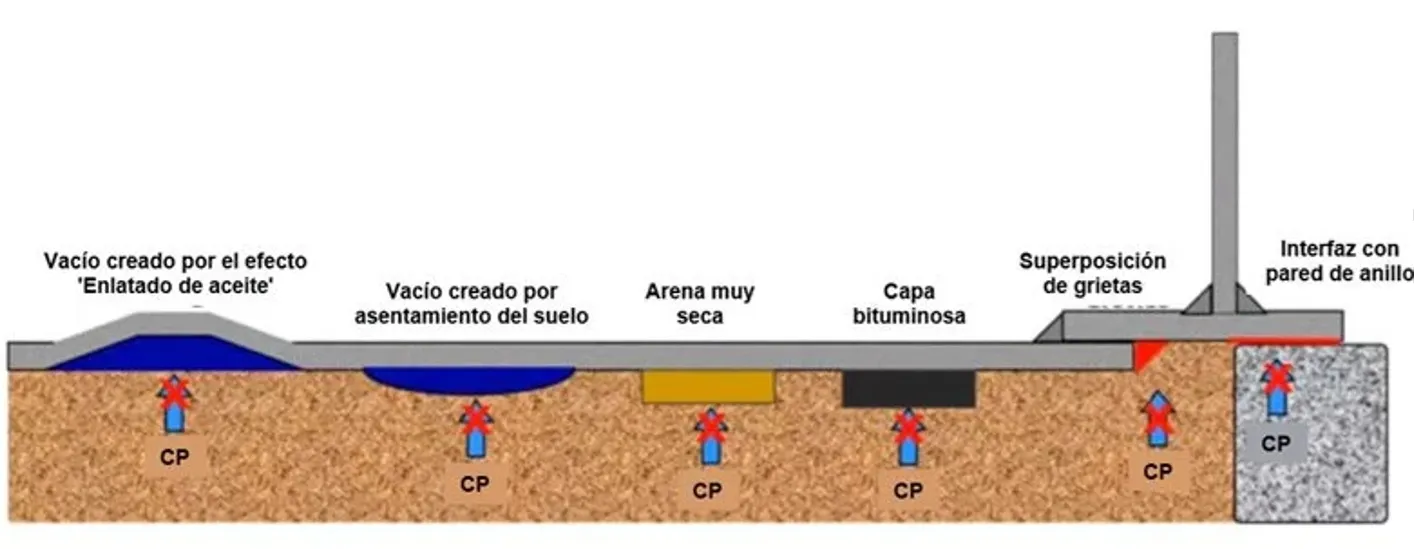
In this context, the incorporation of vapor-phase or volatile corrosion inhibitors (VCI) is presented as an innovative and complementary technical alternative. VCIs can diffuse into confined spaces, adsorb on exposed metal surfaces, and form a molecular barrier that interrupts electrochemical corrosion processes, even in conditions of low humidity or areas inaccessible to the electric field of the CP.
The synergy between VCI and cathodic protection has begun to emerge as a more robust and durable solution, especially in challenging environments such as those described in desert or coastal regions, where tank bottom corrosion can advance rapidly if not comprehensively controlled.
Synergy between coatings, cathodic protection and vapor inhibitors
The protection of storage tanks in the petroleum industry requires a multidisciplinary approach that integrates passive and active technologies. The combined use of protective coatings, cathodic protection (CP) and vapor corrosion inhibitors (VCI) represents an advanced strategy to mitigate corrosion mechanisms on bottom plates exposed to severe soil conditions.
The coatings act as a first barrier that reduces the contact of the metal substrate with the corrosive medium, thus reducing the current demand of the cathodic protection. This synergy reduces both anode consumption and energy costs, optimizing the system from an economic and operational point of view. However, coatings are not infallible. A crack, however small, can allow moisture to enter and activate a localized corrosion cell.
This is where cathodic protection, either by impressed current or sacrificial anodes, complements the system, polarizing the metal and suppressing anodic reactions. However, its efficiency may be limited in soils with low conductivity, areas with air accumulation or inhomogeneous layers such as impregnated sand.
In such cases, vapor corrosion inhibitors (VCIs) offer an additional solution. As volatile compounds, VCIs migrate to inaccessible areas of the system-such as the voids between the floor and tank bottom plates-where they adsorb onto the metal surface, forming a protective molecular layer. This effect is especially useful in non-wetted spaces where conventional CP loses effectiveness.
The combination of these three technologies generates comprehensive protection, capable of adapting to active, passive and hard-to-reach areas. This strategy improves system performance, minimizes unplanned interventions and extends the life of strategic assets such as crude oil tanks.
Relevant case studies in the oil industry
Case 1: Tank farm in the Arabian Peninsula (Middle East)
In a crude oil tank farm built on an impregnated sand platform, severe corrosion rates were recorded on the bottom plates, despite having impressed current cathodic protection. The presence of air voids reduced the conductivity of the media, affecting the effectiveness of the CP.
During a scheduled shutdown, VCI was applied by injection into the space between the soil and the plates, and a monitoring system with ER probes was installed. The results during the first year showed a significant drop in the corrosion rate, validating the effectiveness of the synergy between coating + CP + VCI.
Case 2: Storage tanks in the Gulf of Mexico
In tanks exposed to saline soils, a combined system of epoxy coatings plus magnesium sacrificial anodes, supplemented with VCI in the form of solid capsules installed in the sand bed, was used. This approach was particularly successful in areas where the CP did not achieve sufficient polarization. The projected service life of the tank bottom was extended by more than 15 years, with significant savings in corrective maintenance.
Case 3: Facilities in South America (coastal refinery)
In a context of highly corrosive clay soils, the choice was made to integrate rich zinc paints, a dual cathodic protection system (impressed current and hybrid anodes) and the implementation of encapsulated powder VCI during the filling of the tank base. Subsequent evaluation revealed a controlled corrosion rate (<1 mpy) even in air-soil interface zones, considered high risk.Key factors in choosing between CP and VCI
What are the main factors to consider when choosing between CP and VCI to protect a storage tank?
When selecting a corrosion protection strategy, consideration should be given to:
- Humidity and conductivity of the medium: CP requires a conductive electrolyte; VCIs are effective even in dry environments.
- Accessibility of the area to be protected: VCIs are ideal for areas inaccessible by coating or electric field.
- Expected lifetime: CP provides continuous long-term protection; VCIs require periodic recharging.
- Installation and maintenance costs: CP may involve a higher initial investment; VCIs allow for simpler implementation during maintenance shutdowns.
- Soil conditions or base platform: Dry, loose or low conductivity soils may limit the effectiveness of CP.
A hybrid strategy allows to capitalize on the best of both systems.
Benefits of synergetic protection in storage tanks
The interaction between protective coatings, cathodic protection and corrosion inhibitors generates a comprehensive approach that:
- Significantly reduces the rate of bottom plate thickness loss.
- Minimizes repair, replacement and operational downtime costs.
- Improves structural safety and reduces the risk of leaks.
- Increases the service life of critical assets in aggressive environments.
Conclusion
Corrosion in storage tanks represents a tangible threat to the global energy industry. The joint implementation of VCI and cathodic protection systems has demonstrated superior effectiveness against adverse conditions where traditional methods fail. This integrated strategy, reinforced with monitoring technologies such as ER probes, not only protects assets, but also optimizes resources, preserves the environment and ensures operational continuity. On the road to smarter integrity management, the synergy between CP and VCI makes a key technical and economic difference.
References
- https://www.revistaimg.com/una-mirada-a-la-problematica-que-afecta-a-los-tanques-de-almacenamiento-sobre-el-suelo/