Introduction
The joint use of conventional cathodic protection systems and Pulsed Current Cathodic Protection can increase the efficiency of the protection system of a buried pipeline when the conventional system alone does not guarantee adequate control. To ensure the safe transportation and storage of petroleum products through pipelines, it is essential to apply various corrosion control methods, including coatings, cathodic protection and corrosion monitoring.
Cathodic Protection (CP) has proven to be an efficient control method to mitigate corrosion, where the metallic structure to be protected acts as a cathode electrically connected to the anode, forming an electrochemical cell1. The current necessary for CP is obtained through a sacrificial anode or through an anodic reaction that occurs in an anode bed.
In the case of large structures exposed to a corrosive environment with a relatively high electrical resistance of the electrolyte, the potential gradient between the cathode and the sacrificial galvanic anodes is not sufficient. To supply enough current to protect the cathode, Impressed Current Cathodic Protection (ICCP) is used. This method employs a steady-state direct current source to provide the current required for CP.
However, Direct Current Cathodic Protection (DCCP), as a conventional technique, presents problems such as: high current and energy consumption, eddy current interference2 and cathodic disengagement. In this context, in seeking to resolve these difficulties, improvements are being developed in Cathodic Protection by Direct Current, through the use of pulsed current.
Pulsed Current Cathodic Protection (PCCP), according to studies carried out3, offers greater control in mitigating corrosion in buried lined pipes compared to the traditional direct current method, as long as the pulse current parameters are appropriately selected. . The purpose of this article is to address Pulsed Current Cathodic Protection (PCCP) as an innovative option for corrosion prevention.
Direct Current Cathodic Protection (DCPP)
Cathodic protection is a control method in the fight against corrosion, it is defined as the process of reducing the corrosion of a metal immersed or buried in an electrolyte. This method transforms the surface of the metal into a cathode, decreasing its electrical potential by making it more electronegative.
It is achieved by applying direct current or by connecting a sacrificial material, such as magnesium, aluminum or zinc, as can be seen in the following video courtesy of CorrConnect. Its application is common in buried or submerged iron and steel structures. Cathodic protection is essential to preserve the integrity of metal structures exposed to corrosive environments.
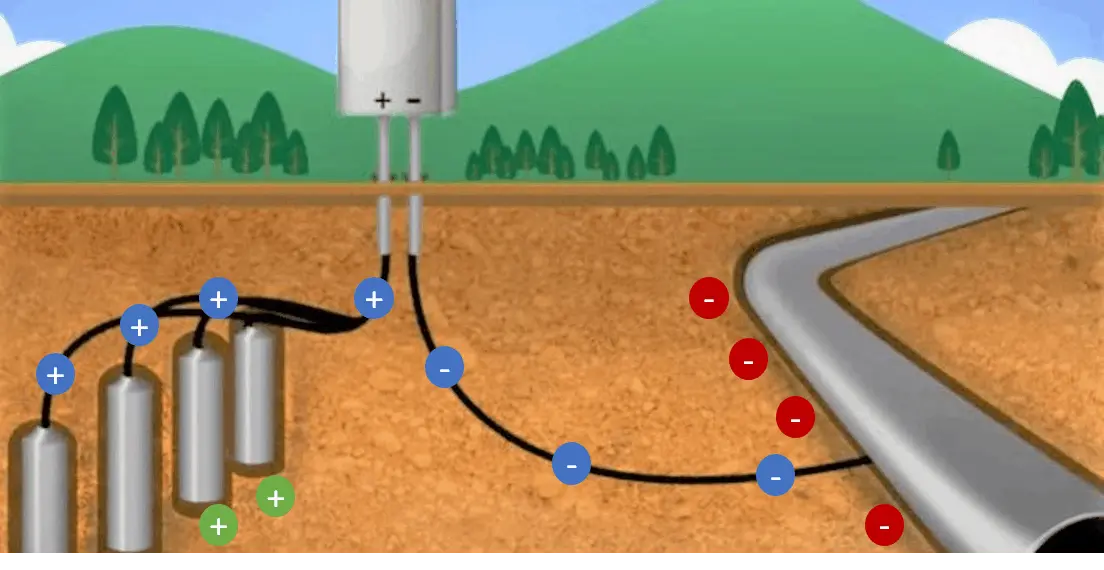
Cathodic Protection by Printed Current
External and internal factors in the effectiveness of Direct Current Cathodic Protection (DCPP)
The performance of a DCCP system, designed to mitigate corrosion in metallic structures, can be affected by a series of external and internal factors 4 . These elements, both environmental and those related to the design and operation of the system, play a fundamental role in the system’s ability to provide effective protection over time.
Below are the key aspects that affect the effectiveness of cathodic protection:
- Eddy current and external factors: The presence of these currents generated by high voltage power lines in the vicinity of pipes can represent a problem for cathodic protection. These external currents can interfere with the flow of protective current, affecting the distribution and amount of current to the structure to be protected.
- Continuous current injection: Internally, continuous current injection into the cathode system can accelerate the hydrogen evolution process, which can lead to cathode detachment, structure delamination and overshielding; which can compromise the integrity of the system and its protection efficiency, especially in corrosive environments.
- DCCP Limitations and detached coatings: Research has revealed that DCCP may be insufficient to effectively control corrosion in situations where coating detachments occur 4 . This scenario highlights the importance of considering alternative solutions, such as the (PCCP).
- Design and Operation Considerations: Fundamental aspects of system design, such as proper material selection, anode arrangement, and precise current control, are important factors in optimizing the effectiveness of cathodic protection. Additionally, operating conditions, such as changes in soil resistivity, must be monitored and adjusted to maintain optimal performance.
Understanding and considering these external and internal factors is necessary to maintain the integrity of cathodic protection systems and ensure effective protection against corrosion, extending the useful life of structures.
Pulsed Current Cathodic Protection (PCCP)
Pulsed Current Cathodic Protection (PCCP) is presented as an alternative solution to the aforementioned problems referred to DCCP. Introduced by Heuze, initially to address corrosion of well casings, it is proposed as an effective procedure not only for well casings, but also for buried pipes, heat exchangers, among others4.
Pulsed Current Cathodic Protection Principle
This control method operates using the principle of CP pulse potentials to optimize current distribution in a pipeline, especially in the presence of coating defects. This principle is based on the strategic manipulation of polarization by concentration during the on and off times of the pulsed current.
Figure 1 schematically illustrates the current distribution in a pipeline with coating defects under the cathodic protection (CP) pulse potential during the on and off periods5. During ignition moments, it is observed that cations accumulate on the surface of the steel, generating a polarization of the electrolyte concentration.
In contrast, at off times, cations disperse from the surface, because CP is not active in that range. As a consequence, the surface undergoes a temporary depolarization, eliminating concentration polarization and allowing greater penetration of the CP current into the steel surface. These two phenomena resemble the charging and discharging of a capacitor during the CP on and off moments.
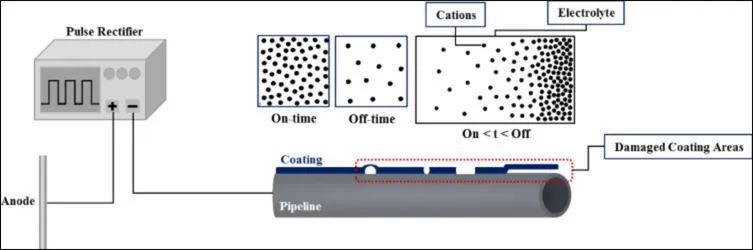
In general terms, this process achieves a decrease in polarization resistance and an increase in the penetration depth of the protection current. This result is explained by considering that the optimal distribution of CP potential is specifically achieved at designated levels of duty cycle and frequency.
Importantly, the coatings do not exhibit ideal behavior in electrolyte solutions due to defects and degradation. Therefore, the capacitive effect of the coating varies with time, which can affect the impedance of the system.
Furthermore, the impedance of the system is attributed to both the inductive effect of the pipe and the resistance of the electrolyte, where capacitive and inductive reactance are fundamental components of the system, contributing to the total impedance of the cell.
The relationship between capacitive and inductive reactance with frequency is inverse and direct, respectively. Consequently, adjusting the frequency and duty cycle optimally is closely linked to the main system components, environmental conditions and cathodic protection (CP) parameters 5 .
Benefits of Pulsed Current Cathodic Protection
Pulsed Current Cathodic Protection offers a number of benefits compared to conventional direct currents, especially in the preservation of lined buried pipelines. The application of electrical pulses of several hundred volts, with extremely short periods and frequencies of several thousand per second, stands out as a more effective and cost-effective alternative.
Key benefits include more uniform current distribution, improved shielding current depth, decreased eddy current interference, and reduced anode bed requirements.
This pulse control method not only optimizes the efficiency of cathodic protection, but is also proven effective, supported by sound operating principles, equivalent electrical circuits, and sound design considerations.
Key benefits include:
- Uniform Current Distribution: Pulsed current technology ensures more uniform current distribution along lined pipes in unprotected areas, optimizing overall process efficiency.
- Greater depth of protection: The application of high-frequency electrical pulses allows achieving a greater depth of protection compared to conventional direct currents. This is essential to ensure corrosion control in specific environments.
- Reduced Eddy Current Interference: Pulsed technology minimizes eddy current interference, a common problem in environments where high voltage power lines surround structures. This reduction improves the precision and stability of the cathodic protection process.
- Reduced requirements for the anode bed: The protection efficiency is greatly improved, and the requirements for the anode bed are reduced compared to direct currents. This implies a more efficient and economical implementation of the technology.
- Validation in field environments: Experience in field cathodic protection registration supports the effectiveness of pulsed current.
- Operating principles and equivalent electrical circuits: They support the application of pulsed current, ensuring its coherence and effectiveness. Likewise, the equivalent electrical circuits provide a technical basis for its implementation.
- Design Considerations: They are supported by fundamentals, ensuring an effective and safe implementation of Pulsed Current Cathodic Protection.
In summary, pulsed current technology stands out for its significant benefits, effectively addressing the problems associated with corrosion in specific structures.
Research and current challenges in Cathodic Protection by Pulsed Current
Pulsed current cathodic protection (PCCP) emerges as an alternative solution in cathodic protection in the fight against corrosion, challenging the paradigms established by conventional techniques. Research in this field has gained momentum, seeking to unlock the secrets of this innovative technology and address its inherent challenges.
Recent research has provided information on the effectiveness of PCCP, relative to conventional direct currents. Strategically applied high-frequency electrical pulses offer more uniform current distribution and greater depth of protection. These advances promise to innovate the way to mitigate corrosion in buried structures5.
In the development of these studies the combined effects of the reduced amount of current required by PCCP compared to DCCP and on the significant reduction of current consumption. The relationship between frequency, duty cycle, and distance under peeling coatings has not yet been comprehensively addressed; However, PCCP electrical circuits have been examined from an electronic perspective, without proper consideration of frequency and duty cycle.
Although PCCP has promising benefits, it is not without challenges. Mitigating eddy current interference, optimizing the frequency-duty cycle ratio, and fully understanding long-term effects are critical issues that still require attention.
Eddy current interference: One of the most prominent challenges is eddy current interference, especially in complex industrial environments. Researchers are studying solutions that minimize this effect, allowing the PCCP to deploy its full potential without external disturbances.
Optimum frequency-duty cycle relationship: Determining the optimal relationship between pulse frequency and duty cycle is significant to maximize PCCP efficiency and find this perfect balance that guarantees effective protection without excessive energy consumption.
Long-term effects: Although initial results are promising, understanding the long-term effects of PCCP is critical. The research includes the analysis of protection durability, resistance to changing environmental factors and continuous evaluation of structural integrity.
Future perspectives
As researchers delve into these challenges, Pulsed Current Cathodic Protection is presented as an effective control method in the fight against corrosion. The path to widespread implementation involves overcoming challenges through collaboration between academia, industry and regulatory bodies.
Ultimately, current research in PCCP is not only focused on optimizing the technology, but ensuring its adoption is sustainable and effective in the long term. These discoveries and overcoming challenges promise a future where corrosion is mitigated, innovating traditional cathodic protection methods for greater control efficiency.
Conclusions
- Pulsed Current Cathodic Protection (PCCP) technology is presented as a promising and efficient alternative to combat corrosion in metallic structures. Its benefits, such as uniform current distribution and increased protection depth range, highlight its ability to overcome limitations associated with conventional cathodic protection methods.
- PCCP emerges as an innovative solution in corrosion mitigation, offering greater effectiveness compared to traditional methods. As research and development continues, successful implementation of PCCP may represent a significant advance in the preservation of metal structures exposed to corrosive environments.
References
- Shigeru. A et al. “Manual of electrochemistry”; ScienceDirect. 2007, Pages xix-xx
- Ormellese. Yes, Beretta. M, Brugnett. F, Brenna. TO; “Effects of non-stationary stray current on carbon steel buried pipelines under cathodic protection” Constr. Build. Mater., 281 (2021), Article 122645
- Heuze. B; A new cathodic protection technique based on matching the quantity of electricity to the potential in: Proceedings of the First International Conference on Metal Corrosion, London 2023, p. 394.
- Barnes.JR, Bein. R, Doniguian.TM; “Measurement of corrosion beneath an unbonded coating”; Corrosion, San Antonio 2020, pp., 25-30
- Afshari. M, et al. “Investigation on utilizing pulse CP in a city gas station: A comparison with conventional CP”; Journal of Pipeline Science and Engineering, June 2023, 100109.