Table of Contents
- Fundamentals of CFRP ultrasonic testing
- Automated ultrasonic testing
- Robotization of composite material ultrasonic testing
- Adaptive segmentation: innovation in data interpretation
- Application in curved geometries
- Comparison with manual inspection
- Data automation: the next level in NDT
- Use cases and industrial implementation
- Practical considerations for implementation
- Future of CFRP inspection
- Conclusions
- References
Introduction
In the aerospace, automotive and energy industries, the use of composite materials has increased significantly due to their high strength-to-weight ratio. One of the most widely used composites is CFRP (Carbon Fiber Reinforced Polymer), or carbon fiber resin composite material. While this material offers notable structural advantages, it also presents significant challenges for Non-Destructive Inspection (NDT) due to its anisotropic microstructure, particularly with regard to the detection of internal defects such as delamination.
In this context, automated ultrasonic testing is considered as an efficient and accurate tool for the nondestructive evaluation of CFRP. With the advancement of industrial ultrasound and data automation, techniques such as adaptive segmentation, also called smart zoning, optimize defect detection by adapting the analysis parameters to the structural particularities of each component.
Fundamentals of CFRP ultrasonic testing
Ultrasonic testing can detect internal discontinuities in a material by propagating high-frequency acoustic waves. In CFRP, the ultrasonic waves interact with the anisotropic microstructure of the material, making the interpretation of the data more complex than in homogeneous materials such as metals.
The use of industrial ultrasound in CFRP mainly seeks to identify defects such as:
- Delaminations.
- Internal voids.
- Foreign inclusions.
- Separation between layers of material.
Traditionally, these tests were performed manually, but manual inspection is prone to human error, limits the repeatability of results and hinders traceability in high production processes. The following image (figure 1), shows typical defects in composite materials detected by ultrasound, (source: Evident).
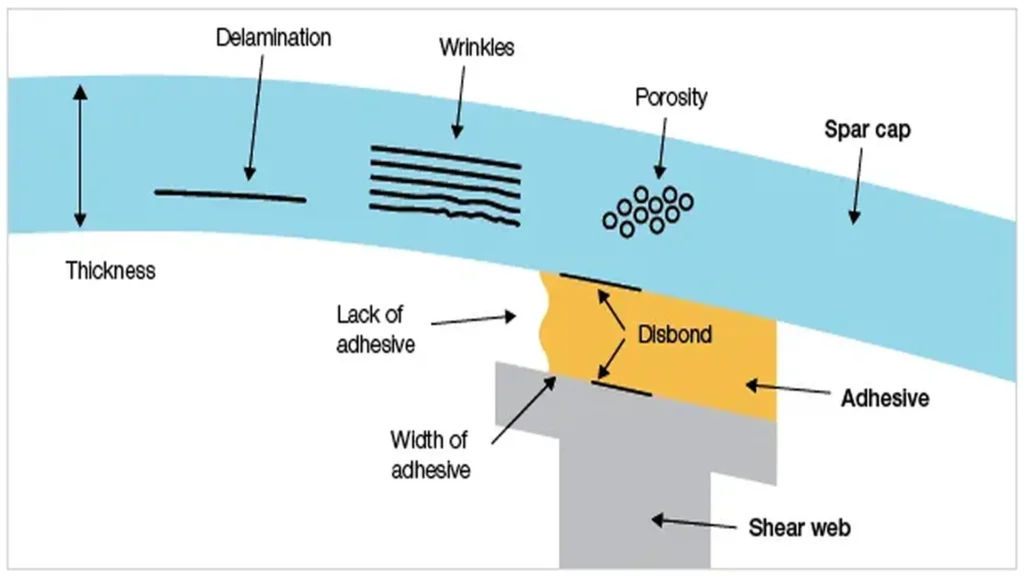
Automated ultrasonic testing
Consist in the use of robotic or motorized systems that allow precise, repeatable and fast inspections. These platforms can be integrated with high resolution data acquisition systems that favor data automation for subsequent analysis.
The main benefits of automated ultrasound include:
- Increased surface coverage in less time.
- Full data traceability.
- Reduced human error.
- Improved resolution of flaw detection in composite materials.
As automation technologies advance, the need arises to optimize not only the acquisition but also the interpretation of data. This is where adaptive segmentation comes into play.
Robotization of composite material ultrasonic testing
The implementation of robots in CFRP ultrasonic testing has significantly transformed the way this test is performed. Robotization allows inspections to be performed continuously, with controlled and precise movements on flat or complex surfaces, without the constant intervention of an operator.
Robots can be programmed to follow specific trajectories, maintain constant transducer pressure, and adapt the orientation of the inspection head according to component geometry. This is especially useful in:
- Large-scale aeronautical components.
- Automotive chassis with multiple curvatures.
- Composite structures with limited access.
In addition, robotization allows better integration with data acquisition and processing systems, contributing directly to process efficiency and quality of results. The figure 2, courtesy of WayGate Technologies, shows an automated robotic ultrasonic inspection solution for small to medium-sized composite parts.
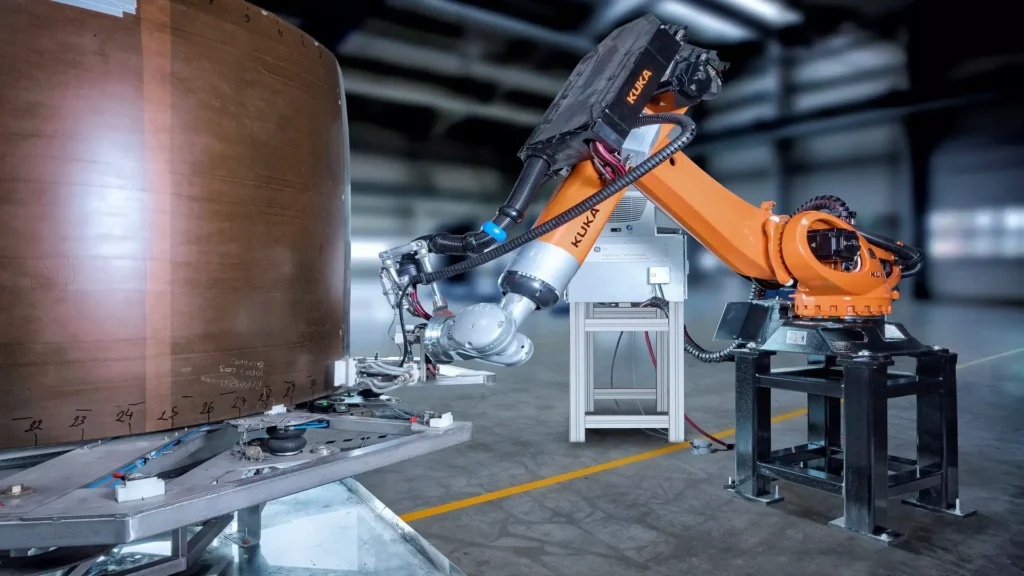
Adaptive segmentation: innovation in data interpretation
Adaptive segmentation, or smart zoning, is a processing technique that divides ultrasound images into regions or zones with similar acoustic characteristics. This allows for more accurate and localized detection of defects in complex CFRP structures.
As the microstructure can vary significantly within a single part, adaptive segmentation allows the inspection parameters to be tailored to the specific conditions of each zone, improving detection sensitivity. Adaptive segmentation algorithms can identify regions with different acoustic properties and apply specific detection thresholds, which is particularly useful for:Detection of shallow and deep delaminations.
- Identification of critical zones in complex geometries.
- Optimization of data automation for predictive analytics.
Application in curved geometries
One of the main concerns of NDT technicians is to verify the efficient application of this technology in non-planar geometries. The answer is yes. Adaptive segmentation can be adapted to curved surfaces using algorithms that incorporate 3D models of the component to be inspected. This is achieved through:
- Three-dimensional mapping of the component.
- Dynamic adjustment of ultrasound incidence angles.
- Adaptive curvature of transducers.
These characteristics allow adaptive segmentation to maintain its effectiveness even in curved components such as fuselages, tubes, turbine blades, among others.
Comparison with manual inspection
The implementation of automated ultrasonic testing with adaptive segmentation is not intended to completely replace manual inspection, but it does represent a significant improvement in terms of efficiency and accuracy.
Advantages over manual inspection:
- Increased repeatability and consistency.
- Reduced inspection time.
- Quantitative rather than qualitative analysis.
- Ability to store large volumes of data for traceability.
Limitations of manual inspection:
- Dependence on operator skill.
- Increased susceptibility to error.
- Difficulty inspecting complex geometries.
In this sense, it can be stated that adaptive segmentation and automated ultrasound complement and strengthen the work of inspectors, providing them with innovative tools for decision-making.
Data automation: the next level in NDT
It is a significant component in modern inspection systems. Through artificial intelligence-based analysis platforms, automated ultrasound data can be processed in real time, generating defect maps, failure frequency histograms and predictive models.
This is particularly important in predictive maintenance, where early detection of failures in CFRP components can prevent structural catastrophes. In addition, data automation systems enable:
- Reduce cognitive burden on the operator.
- Generate automatic and standardized reports.
- Integrate information with quality management systems.
Use cases and industrial implementation
Numerous industries have already begun implementing automated ultrasonic testing solutions with adaptive segmentation. Among the most prominent cases are:
- Inspection of CFRP aircraft parts.
- Quality control in wind blades production.
- Structural verification of sports car chassis.
In all these cases, the detection of defects in composite materials using this methodology has been shown to improve operational efficiency and reduce costs due to undetected failures.
Practical considerations for implementation
To successfully implement this type of system in an industrial environment, the following aspects must be considered:
- Proper selection of industrial ultrasound equipment that supports automation and real-time processing.
- Integration with robots or motorized scanners adapted to the shapes and dimensions of the component.
- Specialized training of personnel to interpret results and adjust system parameters.
- Periodic validation and calibration of adaptive segmentation algorithms.
Future of CFRP inspection
As composite materials become more common in critical applications, nondestructive inspection must evolve to offer more accurate, faster and automated solutions. The combination of automated ultrasound, adaptive segmentation and data automation is emerging as a very promising strategy.
In the future, the integration of intelligent sensors, machine learning and multivariate analysis is expected to provide real-time diagnostics with minimal human intervention.
Conclusions
Automated ultrasonic testing is a major breakthrough for CFRP inspection, enabling more effective detection of complex defects such as delamination or interlayer separation. Thanks to adaptive segmentation, it is now possible to tailor the inspection to the geometrical and structural particularities of each component, including curved geometries.
This methodology does not completely replace manual inspection, but complements it, improving the accuracy, speed and traceability of quality control processes. Data automation, in turn, allows closing the cycle through intelligent analysis that facilitates decision-making.
With these innovations, the industry is better equipped to ensure the structural integrity of critical carbon fiber and resin composite components, setting a new standard for defect detection in composite materials.
References
- Zhang, Y., Wang, X., & Li, J. (2024). Adaptive ultrasonic full-matrix imaging of internal defects in CFRP laminates. Composites Part B: Engineering, 260, 110123.
- AIMPLAS. (n.d.). Defectos en materiales compuestos: Detección y análisis con ultrasonidos. AIMPLAS Instituto Tecnológico del Plástico. Retrieved May 20, 2025, from https://www.aimplas.es/blog/defectos-en-materiales-compuestos-deteccion-y-analisis-con-ultrasonidos/