Table of Contents
- Understanding AE and ASTM E1211
- ASTM E1211: Standard practice for leak detection and localization
- Principles of leak detection using AE sensors
- Applications of ASTM E1211 in Leak Detection
- Benefits of using ASTM E1211 with AET sensors
- Challenges and Limitations
- Future perspectives and technological advances
- Conclusions
- References
Leak detection in various industrial and environmental settings is a critical task that ensures safety, efficiency, and sustainability. One of the sophisticated methodologies used for this purpose involves the use of acoustic emission (AE) sensors, a technology that has been standardized and enhanced through ASTM E1211.
This article delves into the importance of utilizing the ASTM E1211 standard for the application of the AE testing method and as a tool for monitoring, locating, and detecting leaks. It also addresses the fundamentals and principles, applications, benefits, challenges, and future prospects in the field of AE monitoring.
Understanding AE and ASTM E1211
Acoustic Emissions: An overview
Sound waves generated by the rapid release of energy from sources within a material or system.
These emissions occur when a material is stressed and releases energy in the form of sound waves, which can be indicative of various phenomena, including the formation or propagation of cracks, leaks, and other structural failures. The image below shows the principle of sound wave generation and leak detection using AE sensors1.
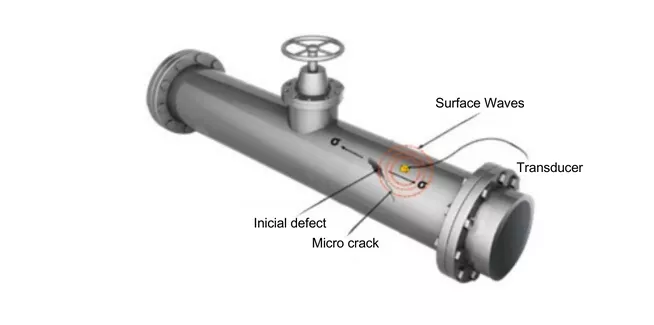
ASTM E1211: Standard practice for leak detection and localization
ASTM E1211 is a standard developed by ASTM International, specifically addressing the use of surface-mounted acoustic emission sensors technology for leak detection and localization1. It outlines methodologies, equipment specifications, calibration procedures, and data analysis techniques necessary for effective leak detection based on AE. The standard provides a comprehensive framework ensuring reliability, accuracy, and consistency in leak detection practices using AE sensors.
This standard describes a passive method for detecting and locating the steady-state source of gas and liquid escaping from a pressurized system. The method utilizes surface-mounted AE sensors or sensors connected to the system via acoustic waveguides and can be used for continuous in-service monitoring and hydraulic testing monitoring of pipeline systems and pressure vessels2.
Principles of leak detection using AE sensors
The fundamental principle behind AE-based leak detection relies on capturing and analyzing sound waves emitted from a leak site. When a fluid (gas or liquid) escapes under pressure through a leak, it generates acoustic emissions that propagate through the surrounding medium. Strategically placed AE sensors around the area of interest detect these emissions. The data collected by the sensors are then analyzed to determine the location and magnitude of the leak.
AE inspection and monitoring involve listening to sounds emitted by material deformation, structural movement, or external impact that are typically inaudible to humans. This can be achieved through highly sensitive passive listening means, capable of detecting subtle energy movements, thereby allowing early conclusions about the structural health of the infrastructure based on an analysis of the generated sound waves.
In leak detection applications, the noise produced by the fluid escaping through a small opening in a pipe or tank is the source of acoustic energy. The sound emitted during such events depends on the nature of the source and its magnitude. In the case of this buried pipeline, the interaction of the escaping fluid with the surrounding sandy soil produces localized impacts that mimic burst-type acoustic signals instead of a typical continuous leak signal3.
Equipment and Setup
According to ASTM E1211, AE equipment includes sensors, preamplifiers, data acquisition systems, and analysis software. The standard specifies the characteristics and calibration of these components to optimize sensitivity and precision. The setup involves placing AE sensors in positions that maximize coverage and the likelihood of detecting emissions from potential leak sites. The following figure shows a schematic of the main components of an AE system (1. Stimulus, 2. Growing Discontinuity (AE Source), 3. AE Waves, 4. Sensor, 5. Preamplifier, 6. AE Signal, 7. AE Equipment)4.
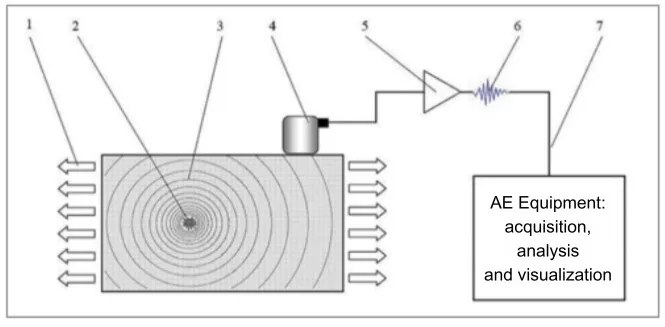
Data Analysis and Interpretation
Acoustic data captured by the sensors undergo signal processing to filter out noise and enhance the signals of interest. Techniques such as triangulation, time-of-flight analysis, and amplitude analysis are employed to pinpoint the location of the leak. The ASTM E1211 standard provides guidelines on interpreting these signals, taking into account the properties of the material or system being monitored and the environmental conditions.
Applications of ASTM E1211 in Leak Detection
ASTM E1211 has broad applications in various industries, including oil and gas, chemical processing, power generation, and water management. In the oil and gas sector, it is used for pipeline monitoring, tank inspections, and offshore platform safety. In chemical processing plants, AE sensors monitor storage tanks and process lines to detect leaks that could lead to hazardous spills.
Power generation facilities employ AE monitoring to ensure the integrity of boilers and steam lines, while water management systems use it to detect leaks in underground pipes.
The method employs surface-mounted acoustic emission sensors or sensors connected to the system via acoustic waveguides and can be used for continuous in-service monitoring and hydraulic pressure testing of pipe systems, pressure vessels, tanks, among others. High sensitivities can be achieved, although the values attainable depend on sensor spacing, background noise level, system pressure, and the type of leak3.
The following video demonstrates an application of AE in steam boiler monitoring.

Application of AE in steam boiler monitoring. (Source: Mistras).
Benefits of using ASTM E1211 with AET sensors
The use of ASTM E1211 in conjunction with AE sensors offers several advantages:
- Early detection: AE monitoring can detect leaks in their early stages, long before they become visible or cause significant damage.
- Non-invasive: The technology is non-invasive, so it does not necessarily require taking the component being examined out of operation.
- Comprehensive coverage: AE sensors can monitor large areas and complex geometries, providing comprehensive coverage.
- Cost-effectiveness: Early detection and prevention of operational disruptions lead to significant cost savings
Challenges and Limitations
Despite its advantages, AE-based leak detection faces challenges:
- Ambient Noise: Background noise can interfere with the detection of acoustic emissions, requiring sophisticated filtering techniques.
- Sensor Sensitivity: The effectiveness of AE sensors depends on their sensitivity and the complexity of the monitoring environment.
- Data Complexity: Analyzing the vast amounts of data generated by AE sensors is challenging, requiring advanced algorithms and expertise.
Future perspectives and technological advances
The future of leak detection and localization using ASTM E1211 and AE sensors is promising, with ongoing research and development focused on improving sensitivity, reducing noise interference, and enhancing data analysis algorithms. Innovations in sensor technology, such as the development of more sensitive and selective sensors, are expected to enhance the accuracy and reliability of leak detection.
Furthermore, the integration of machine learning and artificial intelligence into data analysis can significantly improve the ability to interpret complex AE, making leak detection more efficient and effective. Machine learning is applied to strengthen the method of distinguishing non-leak-associated data from leak-associated data for precise leak detection and location.
Conclusions
ASTM E1211, when combined with acoustic emission sensors, offers a powerful tool for leak detection and localization across a wide range of industries. This technology facilitates early detection, minimizes operational disruptions, and ensures safety and environmental protection. Despite facing challenges related to ambient noise and data complexity, ongoing advancements in sensor technology and data analysis promise to overcome these obstacles, further solidifying the role of ASTM E1211 in the future of leak detection.
As industries continue to prioritize safety and efficiency, the adoption and refinement of AE-based leak detection methods will drive innovations such as the adoption of artificial intelligence and machine learning to enhance the capacity and reliability of this critical technology.
References
- ANTONIO ZAVARCE. Fundamentals and applications of Acoustic Emission (AE); Accessed on April 1, 2024; https://inspenet.com/articulo/fundamentos-aplicaciones-emision-acustica-ea/
- ASTM. ASTM E1211/E1211M-17: Standard Practice for Leak Detection and Location Using Surface-Mounted AE Sensors; Accessed on April 1, 2024. AMERICAN SOCIETY FOR TESTING AND MATERIALS.
- THOMAS M. JULIANO, JAY N. MEEGODA, AND DANIEL J. WATTS. AE Leak Detection on a Metal Pipeline Buried in Sandy Soil; Accessed on April 2, 2024. https://www.researchgate.net/publication/273745882_Acoustic_Emission_Leak_Detection_on_a_Metal_Pipeline_Buried_in_Sandy_Soil
- EVA MARTÍNEZ, ANTONIO GALLEGO. Technical report “Acoustic emission as an NDT method: definition, advantages, and limitations”; Accessed on April 1, 2024. https://idie.ugr.es/wp-content/uploads/2020/12/2013_AEND_Martinez.pdf
- HAYDEN GEMEINHARDT, JYOTSNA SHARMA, Machine-Learning-Assisted Leak Detection Using Distributed Temperature and Acoustic Sensors; Accessed on April 3, 2024; https://www.researchgate.net/publication/376215436_Machine_Learning-Assisted_Leak_Detection_using_Distributed_Temperature_and_Acoustic_Sensors.