Author Ing. Edward Madriz, 23 November 2021.
Summary
Storage tanks play a very important role in the oil, gas and petrochemical industries, since the products of industrial processes are stored in them; and feed streams to processing plants. However, due to the little maintenance that is carried out on them; It is of great importance to innovate and improve the equipment that is commonly used to carry out inspections on these assets, in order to provide a guarantee in each evaluation applied; either on floors, walls or ceilings. In this context, it is important to look for technological alternatives, through the use of techniques and test methods that allow the useful life of these assets to be extended, to maintain their tightness and thus prevent them from collapsing.
Introduction
In this article, we will focus on the evaluation of floors or bottoms of storage tanks, where different inspection techniques are usually used depending on whether the container is open (for the entry of evaluating personnel) or is operational (with fluid handling). , inspections may be carried out; either, through the combination of conventional Non Destructive Tests (NDT) or currently developed such as: Penetrating Liquids (PT), Magnetic Particles (MT), Visual Inspection (VT), Radiographic Examinations (RT), Phased Array (PAUT) with corrosion probes to accurately measure thickness losses, the Magnetic Flux Loss (MFL) technique; which are techniques applied when the evaluating inspector manages to enter the interior of a tank. Otherwise, when the container is kept in the operating process (with fluid inside), the techniques of Acoustic Emissions (AT), Induced Currents (ET), Short-Range Guided Waves (SRUT) are used for the most critical area of the tank bottom.
Magnetic Flux Leakage (MFL)
At present, high-tech software and equipment have been developed and improved for an optimal diagnosis of mechanical integrity focused on the MFL Magnetic Flux Loss technique, (New generation of tank floor inspection, see Figure 1), where the competition lies in offering a high quality in the resolution of the image obtained, with a power distribution that allows the evaluation of the floor when the sheets are thicker than the usual ones (3/8”) with high sensitivity, among others qualities that make the design of each manufacturer look like the equipment that is required.
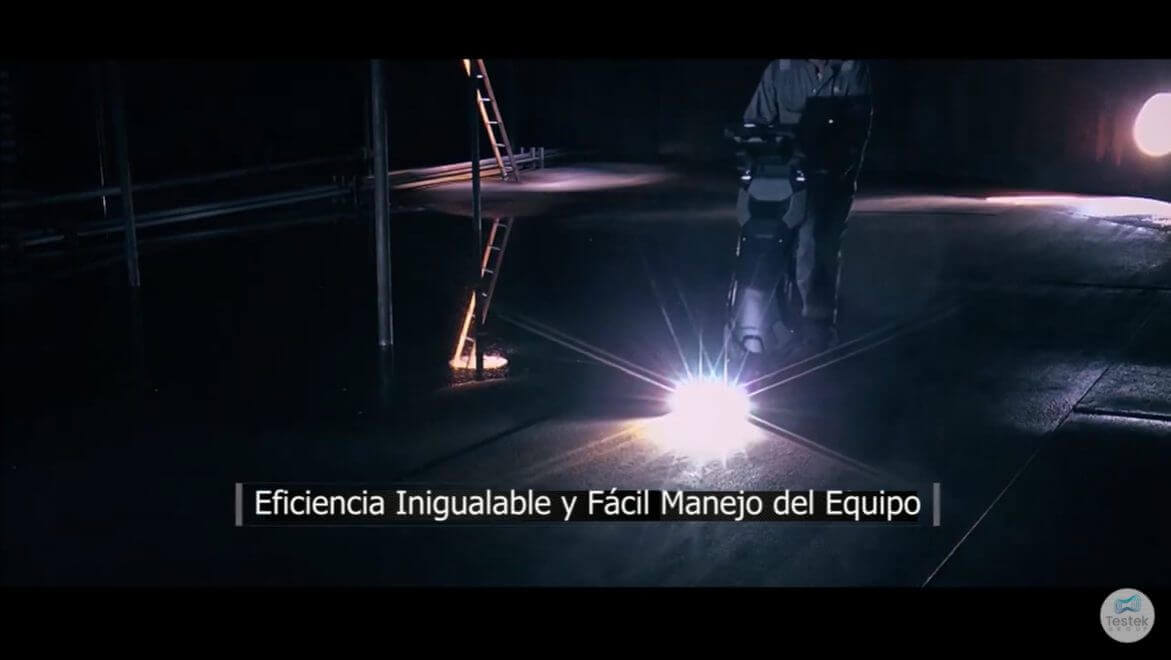
Figure 1. MFL equipment for evaluation of tank floors (Floormap X Eddyfi, video courtesy Grupo Testek). [one]
These kits represent a new way of inspecting storage tank floors. Algorithms developed to filter out flow leakage distortion provide the operator and customer with greater insight into visual data displays. Data samples are stored on each track run and can be correlated with subsequent inspections for predictive analysis of increased corrosion. They consist of a Magnetic Flux Leakage (MFL) storage tank floor plate scanner; which introduces a new dynamic in the inspection of the tank floor and has a high resolution scanning system and offers an incomparable level of inspection.
These systems are easy to use and very practical, folding to a locked transport position, with the operation of a single lever. With its small physical size and lower weight, handling and setup requires little effort.
Guided Waves
Guided waves is a non-intrusive non-destructive testing technique, therefore the examination can be performed with the tank in service. This type of test is carried out from the outside of the tank covering a certain distance (short range) towards the center of the tank. They are generally used in tanks to check the condition of the annular plate of the bottoms of carbon steel storage tanks.
Among the equipment with more technological advances is the ISONIC 3510 Figures 2,3; which was designed and built with the aim of improving fault detection, productivity and reducing the cost of inspection. In addition to recording indications found and being exhaustive in the inspection reports created automatically. Among its benefits is the evaluation in 5 inspection modalities: PAUT, TOFD, CHIME, SRUT GW, conventional UT and a combination of them, excellent ultrasonic performance, consists of an intelligent platform based on applications for performing regular ultrasonic tests and advanced [2]
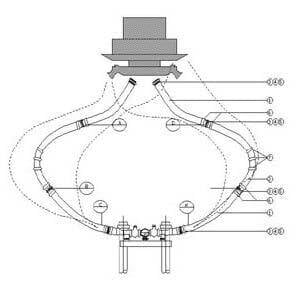
Acoustic Emission (EA)
It is a non-destructive testing and inspection technique that allows locating, evaluating active defects, leaks in pressure equipment and analyzing the condition of storage tanks. This technique is characterized by the creation and propagation of transient elastic waves, which result from internal local displacements of a material (cracks, inclusions, corrosion, leaks, among others) and are captured through low-frequency high-frequency piezoelectric sensors. sensitivity that allow locating (in the form of triangulation) these emitted sources.
The company Physical Acoustics South America (PASA)[3], developed TankPAC™; which is a test method that uses the Acoustic Emission technique to determine the condition of integrity of the bottom of the tanks. The technique consists of capturing, by means of transducers, signals originating from the corrosion process that occurred in the internal or external part of the bottom of the tank, thus evaluating the integrity and eventual circumstance of a corrosion process.
References
1. https://youtu.be/Nj8dFEDVKEw. 2. ISONIC 3510 ( https://www.youtube.com/watch?v=orUlXBVs3HE ). 3. http://www.pasa.com.br/espanhol/tanques_tankpac.asp]. |
About the Author
ing Edward Madriz. Equipment Inspector. 8 years of experience in the area of inspection in the Oil and Gas industry.
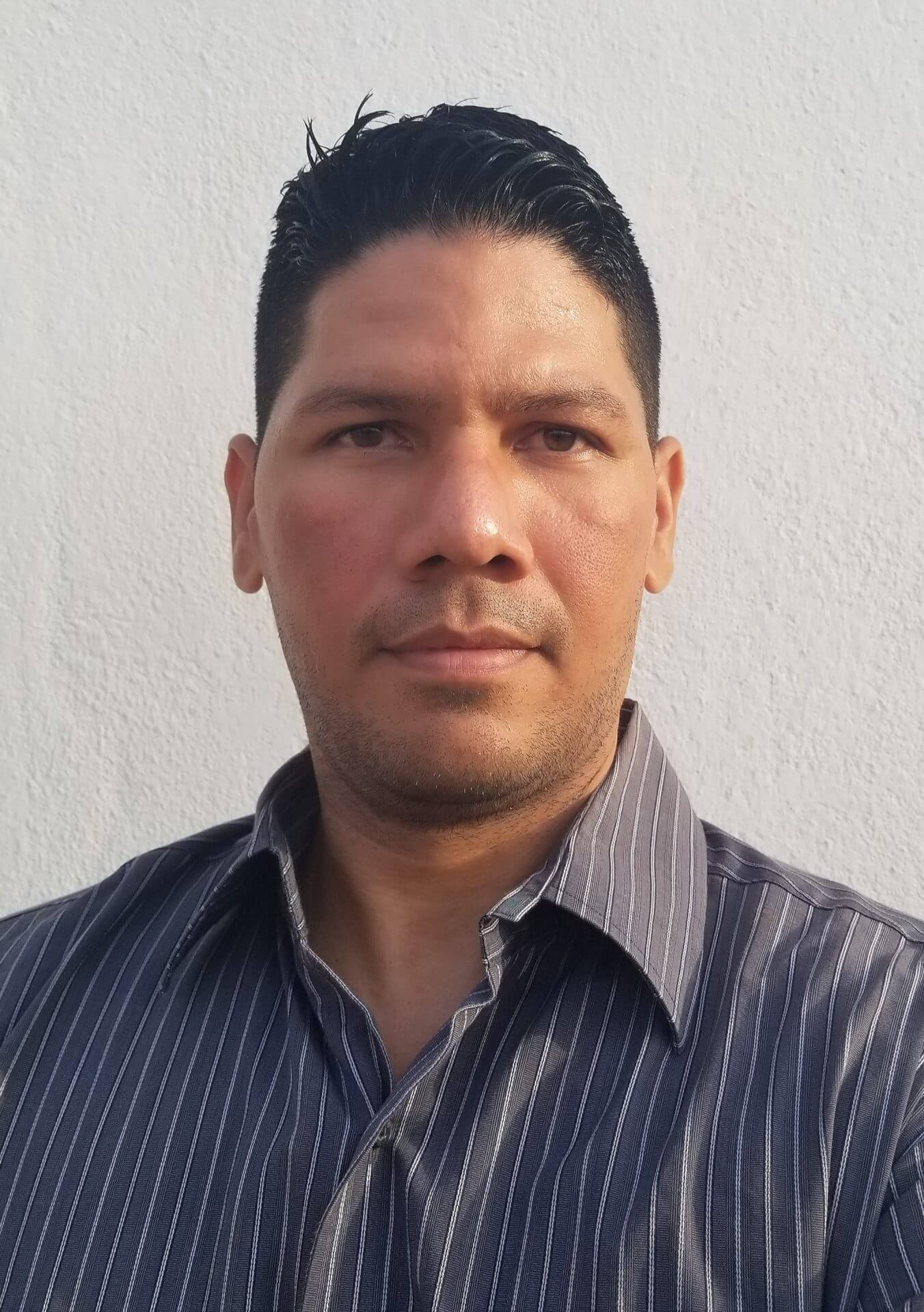