Introduction
Welding inspection is a fundamental process to assess the quality of a weld and to determine whether it meets specific standards and requirements by detecting susceptible defects in the welding process. The competence of the professional in charge is significant, requiring a thorough knowledge of welding procedures, testing experience and defect identification.
Welding is a complex process that requires very special attention and rigorous monitoring at all stages, from planning to quality control release. As safety and quality requirements increase, so do weld inspection methods and the training and preparation requirements of weld inspectors to ensure the integrity and durability of welds.
This includes assessing surface preparation, choice of material and correct welding processes, as well as verifying the appearance and mechanical properties of the completed weld. This article discusses advances in welding inspection techniques, best practices for their implementation and methods used to verify the quality of a weld.
What is welding inspection?
The inspection and quality control welding are the process of evaluating and ensuring that welded joints meet the required standards and technical specifications. It includes destructive and non-destructive methods to verify the integrity and quality of the weld, such as radiography, ultrasound, dye penetrant, tensile and impact testing, among others. These methods can detect inconsistent weld structures, cracks, porosity or inclusions, ensuring that the weld has the strength and durability necessary for its application and to prevent structural failure, ensure safety and comply with industry standards.
As a general rule, quality and specified standard requirements should not be sacrificed for the convenience of production.
Welding inspectors
Welding inspectors are qualified professionals responsible for ensuring that welds performed on various projects meet quality standards and are carried out according to specification and established procedures. The role of the welding inspector can cover all areas of a welding process, from pre-procedures, execution, checks, and post weld testing.
Areas of knowledge of welding inspectors
A welding inspector must keep up to date and master welding standards and codes, metallurgy, non-destructive inspection methods, interpretation of drawings and technical specifications, industrial safety and quality control welding to ensure the integrity and safety of welded structures. Therefore their technical training should cover the following area of knowledge:
- Types of joints and welding processes: Knowledge of the different types of joints such as overlap, butt, edge and corner joints, among others. As well as solid knowledge of welding processes such as gas metal arc welding (GMAW), gas tungsten arc with inert gas (GTAW), flux cored arc (FCAW) and submerged arc welding (SAW), among others.
- Standards and codes: Familiarity with international standards and codes governing welding and non-destructive testing, such as The American Society for Non-destructive Testing (ASNT), American Welding Society (AWS), the American Society of Mechanical Engineers (ASME), the International Organization for Standardization (ISO), and others.
- Materials and metallurgy: Knowledge of the various materials that make up a welded joint, such as steels, special alloys, non-ferrous metals and consumable electrodes. This knowledge includes understanding how the properties of these materials can influence both the welding process and the final result.
- Non-destructive testing (NDT): Competence in performing and interpreting NDT methodologies such as visual inspection, radiography, ultrasound, magnetic particle and liquid penetrant testing. Must also be knowledgeable in advanced NDT techniques and their application, such as acoustic emission, magnetic field leakage, eddy current and digital radiography, among others.
- Welding procedures: Understanding of welding procedures (WPS) and the ability to assess whether they are correctly followed during the process.
Certifications for welding inspectors
There are several certifications that a welding inspector can obtain to demonstrate their competence and knowledge in the field. Some of the most recognised certifications are:
- Welding inspector certification (CAWI, CWI, SCWI) from the American Welding Society (AWS): This is one of the most recognised certifications worldwide. The certifications awarded are: Certified Associate Welding Inspector (CAWI), Certified Welding Inspector (CWI), Senior Certified Welding Inspector (SCWI).
- CSWIP welding inspector from the welding institute (TWI): TWI is an internationally recognised UK organisation that certifies CSWIP 3.0 (Level 1): Visual Welding Inspector, CSWIP 3.1 (Level 2): Welding Inspector and CSWIP 3.2 (Level 3): Senior Welding Inspector.
- American Society for Nondestructive Testing (ASNT): ASNT certification is a credential provided by the American Society for Nondestructive Testing to NDT technicians. This certification verifies that a person is competent in non-destructive testing.
- Certification based on ISO 9712: NDT certifications covering the competence of inspectors in non-destructive testing.
Welding inspection methods
Tests and procedures for performing welding inspection are designed to provide a record of the welding variables used and the inspection results obtained during the procedure qualification test, and may also provide instructions for the welder to use in production to create acceptable welds. Welding inspection is important to ensure the safety and integrity of the welded structure.
Some of these methods are summarised below:
Visual inspection: Visual inspection is the most basic and common method of evaluating a weld. It consists of examining the weld with the naked eye or using tools such as magnifying glasses and special lights to detect surface defects such as cracks (figure 1), porosity, misalignment, spatter, lack of filler. Although simple, this technique is essential and should be carried out by trained and experienced personnel who can identify obvious problems before more advanced inspections are carried out.
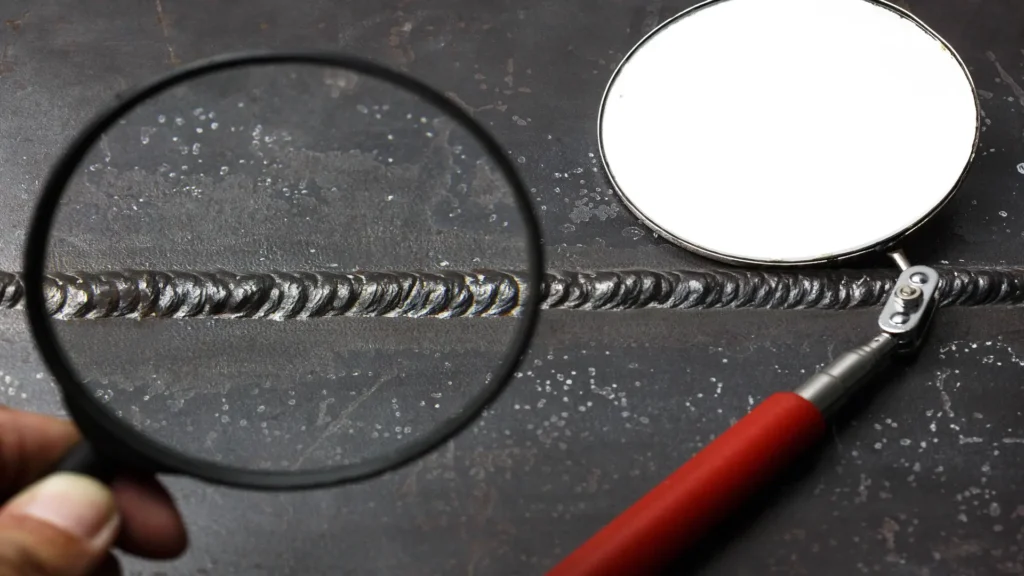
- Liquid penetrant inspection: This method is mainly used to detect surface defects in welds of non-porous materials. It consists of applying a liquid penetrant to the welded surface, followed by a remover and a developer that makes the surface discontinuities visible. It is an effective technique for detecting surface cracks and porosities that may not be visible to the naked eye.
- Magnetic particle inspection: Used for the inspection of ferromagnetic materials. A magnetic field is induced into the weld using a tool called a yoke and a magnetic particle powder is applied to the weld as shown in figure 2. Defects in the weld cause distortions in the magnetic field, attracting the particles and making the defects visible. This technique is effective in identifying surface and sub-surface cracks in welds.
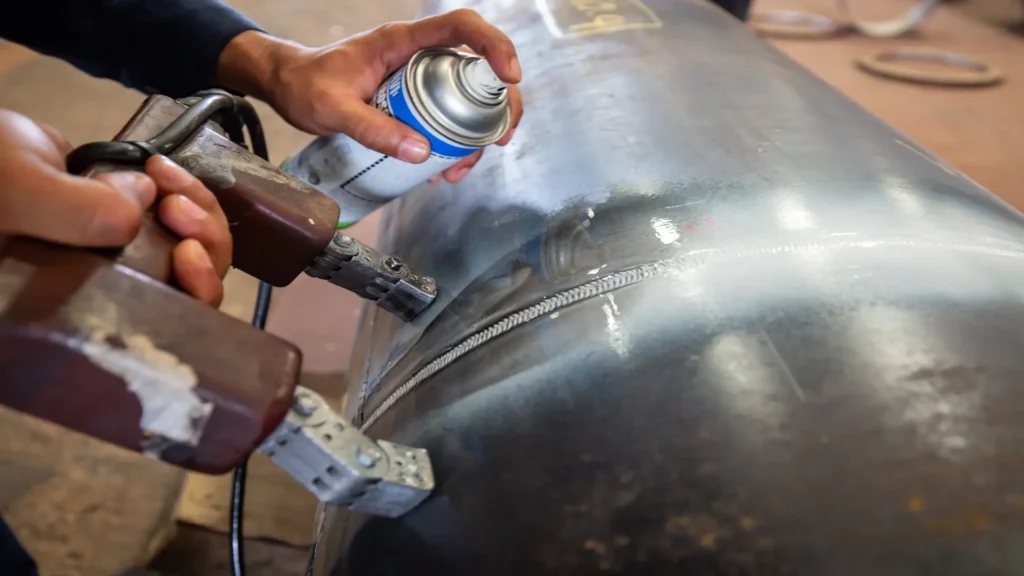
- Ultrasonic inspection (UT): An advanced methodology that uses high-frequency sound waves to detect internal defects in the weld. A transducer sends ultrasonic waves through the weld and detects the waves reflected from internal discontinuities. This method is very effective in detecting inclusions, lack of fusion, cracks, and other internal defects that are not visible with surface methods.
- Radiographic inspection: This methodology uses X-rays or gamma rays to examine the internal integrity of a weld. The radiographic images obtained show the internal density of the weld, as shown in figure 3, allowing the detection of defects such as porosities, inclusions, certain types of cracks, and lack of fusion, among other discontinuities. It is a costly and high-risk technique due to radioactive contamination, but extremely accurate and useful for welds. Inspectors working with this method use radiation detectors during their working day and have a very strict occupational health control.
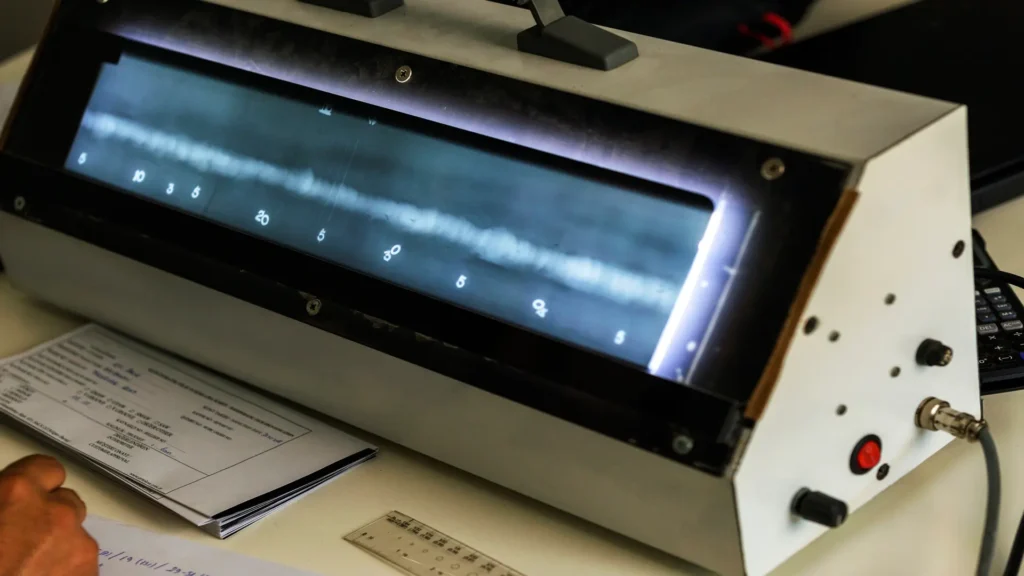
- Eddy Current Inspection: This method is based on the induction of electric currents in the weld by means of an induction coil. Variations in conductivity and magnetic permeability caused by defects alter these currents, which is detected by specialised equipment. Eddy current inspection is useful for detecting surface and sub-surface cracks in conductive materials.
Advanced weld inspection
Thermographic imaging techniques
Infrared thermography is an advanced technique that detects differences in the surface temperature of a weld. These differences can indicate the presence of internal defects or heat distribution problems during the welding process. It is a non-destructive technique that can be used to inspect large areas quickly and without the need for direct contact. Active thermography is applicable in outdoor environments for the detection, characterisation, and measurement of surface discontinuities by studying temperatures and cooling rates.
Computed tomography technique
This is an advanced technique that provides three-dimensional images of the weld. Using X-rays at different angles, CT allows a detailed visualisation of the internal structure of the weld. Although expensive, it is a highly accurate inspection technique in critical applications.
Acoustic emission inspection
This method detects acoustic waves emitted by defects in the weld when subjected to stress. Sensors placed on the surface of the weld pick up these emissions, which are analysed to identify and locate internal defects. Acoustic emission inspection is useful for monitoring structural integrity in real time during the operation of a structure. It requires complementary NDT techniques such as ultrasound to define the shape and depth of the discontinuity.
Best practices in weld inspection
- Personnel training: Personnel performing welding inspection must be properly trained and certified. Continuous training and updating of knowledge on new techniques and regulations are essential to maintain high quality standards.
- Planning and documentation: A detailed inspection plan should be developed before starting any welding project. This plan should include the inspection methods to be used, acceptance and rejection criteria, welding maps and an inspection schedule. Documentation of each stage of the inspection process is a very important factor in ensuring the traceability and quality of the project.
- Use of suitable equipment: Inspection equipment must be calibrated and certified, and must be suitable for each inspection process. Equipment should be calibrated regularly and maintained in good condition. In addition, the use of advanced technologies should be considered for projects requiring a high level of accuracy.
Defect analysis and correction
When defects are detected in a weld, their causes must be analysed and determined. This analysis may involve reviewing the welding process, the quality of the materials used and the environmental conditions. Once the cause has been identified, corrective measures should be implemented to prevent recurrence of the defects and included in the lessons learned in the final report.
Post-process inspection and maintenance
Inspection should not end at the completion of the initial weld. Post-process inspections are necessary for monitoring welds subjected to certain service conditions, such as those exposed to hydrogen attack at high temperatures. Inspection methods for these cases will be determined by the corrosion mechanisms and service conditions.
Conclusions
Advances in welding inspection techniques have led to significant improvements in weld quality and safety. From traditional methods such as visual inspection to advanced techniques such as computed tomography, the variety of tools available offers multiple ways to ensure weld integrity. The implementation of best practices in inspection and quality control, training of personnel, use of appropriate equipment and compliance with regulations is critical to achieving optimum results.
Advanced weld inspection and continuous quality verification are necessary to ensure that welds meet the highest standards of safety and performance. With constant attention to innovation and continuous improvement, the welding industry can continue to move towards a safer and more efficient future.
References
Own source