Table of Contents
- Hydrogen embrittlement (HE)
- Metal additive manufacturing and its potential in industry
- Hydrogen embrittlement of metals manufactured by AM
- Microstructure and embrittlement mechanisms
- Advances in resistance to embrittlement by AM
- Additive Manufacturing: The future of metallic materials resistant to hydrogen embrittlement
- Conclusions
- References
Hydrogen, as a central component in the transition to a sustainable economy, is widely used in industrial applications. However, its interaction with certain metallic materials can cause a phenomenon known as hydrogen embrittlement (HE). This is particularly affects metals used in hydrogen transport and storage, especially steels, and results in a loss of ductility and strength, compromising the structural integrity of the components.
In this context, additive manufacturing of metals emerges as a viable alternative for the manufacture of high-density metal components resistant to this corrosion phenomenon compared to those produced by traditional methods.
Additive manufacturing (AM), also known as 3D printing, has gained prominence for its ability to create complex metal structures with processes such as selective laser melting (SLM) and direct energy deposition (DED). However, metals produced by AM are also susceptible to hydrogen embrittlement, which creates additional challenges in their use in industrial applications. This article discusses the main challenges and advances offered by additive manufacturing to improve the HE resistance of metal components.
Hydrogen embrittlement (HE)
Hydrogen embrittlement is a well-documented problem affecting high-performance metallic materials such as steels, titanium alloys, and superalloys. This phenomenon is characterized by a reduction in structural properties, including tensile strength and fatigue resistance. These properties can result in unexpected structural failures that are difficult to avoid, due to the entry of hydrogen atoms into metals, especially in environments containing seawater, hydrogen gas, or moist air.
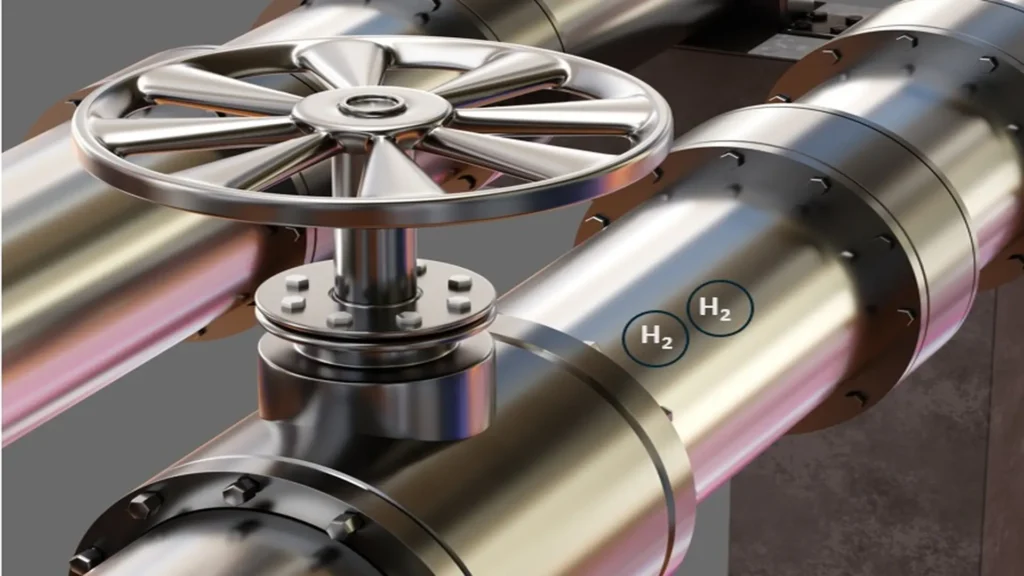
Despite extensive research1 for more than a century, hydrogen embrittlement remains a challenging problem for engineers and materials scientists. Selecting or developing materials suitable for hydrogen-related applications is critical, especially when it comes to additive manufacturing, where microstructures may differ from conventionally produced metals.
Metal additive manufacturing and its potential in industry
AM is an innovative manufacturing method that enables the creation of parts with high geometric complexity, from design to delivery of final products, reducing waste compared to traditional methods. The main AM processes include Powder Bed Fusion (PBF) and Direct Energy Deposition (DED). These methods are used in a variety of industries, including aerospace, automotive, medical, and energy, and have revolutionized the manufacture of high-density metal components such as steels, aluminum alloys, titanium, and nickel-based superalloys.
This process achieves the production of parts with a minimum amount of material, reducing machining steps and, therefore, production costs. Due to the purpose of using this manufacturing process in industry, these parts are likely to be subjected to aggressive conditions and environments.
However, the rapid solidification and intense thermal gradients inherent in AM processes result in microstructures that differ significantly from those of conventionally fabricated metals, which influences susceptibility to hydrogen embrittlement.
Hydrogen embrittlement of metals manufactured by AM
Hydrogen embrittlement in components produced by AM has received relatively little attention to date, although there have been recent studies suggesting that susceptibility to HE varies depending on the type of AM process and alloy used. For example, 304L stainless steel, fabricated by Direct Metal Deposition (DMT), demonstrated superior resistance to embrittlement compared to its counterpart produced by cold rolling. However, this resistance varied depending on the microstructure and environmental conditions.
This phenomenon is partly explained by the inherent microstructural differences in metals fabricated by AM. The microstructures of these materials are usually more heterogeneous and present a grain size and phase distribution that differs significantly from those obtained by traditional methods. These factors can influence the absorption and diffusion of hydrogen in metals, increasing or decreasing the susceptibility to HE.
Microstructure and embrittlement mechanisms
In additive manufacturing, powder bed fusion and direct energy deposition processes generate rapid cooling rates and directional solidification, resulting in microstructures with higher dislocation density, refined grain size, and possible unwanted inclusions. These microstructures can act as sites of hydrogen absorption and accumulation, accelerating the embrittlement process.
The HE behavior of metal alloys produced by AM is affected by factors such as process type, heat treatment conditions, and alloy type. The susceptibility to HE in stainless steels, titanium alloys, and nickel-based superalloys is especially critical due to their use in highly demanding applications such as aerospace and medical.
Advances in resistance to embrittlement by AM
There are several strategies to improve HE resistance in AM metals, such as tuning manufacturing process parameters, optimizing heat treatments, post-processing, and incorporating simulation and computational modeling. These approaches allow predicting how fabrication parameters affect the microstructure and hence the resistance to hydrogen embrittlement.
Current research is focused on developing hydrogen-resistant alloys and adjusting AM processing conditions to control hydrogen absorption into metal components. In addition, advanced modeling and simulation provide insight into the underlying physical mechanisms and optimize the design of parts manufactured using AM.
In this context, research is currently being carried out to evaluate the corrosion behaviour of metals manufactured by (AM). A recent study examined the effect of low hydrogen content on hydrogen-assisted cracking (HAC) in 17-4 martensitic stainless steel (SS)2 , produced by AM. Electron microscopy results (figure 2) show that conventional (CM) specimens exhibit more severe cracking than those produced by AM, indicating a higher resistance to HAC in the AM specimens.
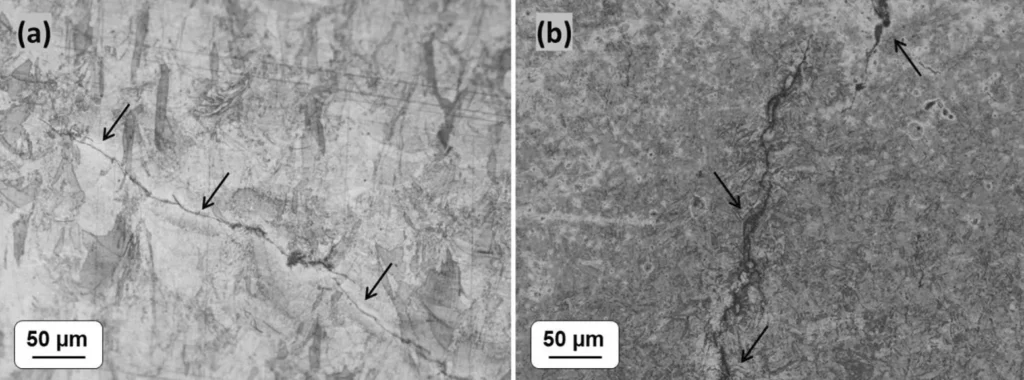
This phenomenon is attributed to a higher initial amount of retained austenite and the absence of brittle nitride phases. The ductile austenite phase can clog the crack tip and act as an effective hydrogen trap due to its higher solubility for hydrogen. In addition, the presence of austenite in the matrix reduces the dislocation density and internal stresses, thus improving the strength of the material against HAC.
Another study was carried out to compare the resistance to HE in 316 L stainless steel manufactured by additive manufacturing (AM) and conventional manufacturing (CM). The results obtained showed that the 316L stainless steel sample fabricated by AM in the hot isostatic pressed (HIP) condition demonstrated better resistance to HE compared to the conventionally fabricated (CM) material, especially at -50°C3.
Both investigations highlight the potential of AM to improve the resistance of metallic materials to hydrogen embrittlement. In particular, stainless steel processed by advanced techniques such as hot isostatic pressing (HIP) showed superior ductility compared to conventionally fabricated material, even under low temperature conditions and in the presence of hydrogen. The results obtained from different research in this area underline how microstructural control achieved by AM allows the development of stronger materials adapted for applications in critical environments, marking a significant advance in materials engineering.
Additive Manufacturing: The future of metallic materials resistant to hydrogen embrittlement
Additive manufacturing is changing the metallic structure of metallic materials, especially in the control of hydrogen embrittlement, a phenomenon that compromises the integrity and durability of metals in critical applications. This process allows the creation of metal structures with complex geometries and optimised microstructures, facilitating the design of materials that are less susceptible to embrittlement.
Through additive manufacturing, it is possible to adjust process parameters such as cooling rate, grain distribution and material porosity, which are key factors in resistance to hydrogen embrittlement. In addition, additive techniques offer the ability to integrate composition gradients and specific metal phases to reduce areas vulnerable to hydrogen embrittlement.
AM is also opening up new opportunities in the development of advanced alloys and specific coatings that mitigate the effects of hydrogen. These advances are driving the creation of metal parts with extended service life and improved safety in sectors such as oil, gas, energy and aerospace, where the control of HE is critical to prevent catastrophic failures.
Conclusions
Additive manufacturing offers significant opportunities for the creation of complex, customised components, but hydrogen embrittlement poses considerable challenges in its application in hydrogen-abundant environments. Understanding and controlling the microstructure of metals fabricated by AM is critical to minimising susceptibility.
As AM technology continues to advance, the development of more hydrogen-resistant alloys and optimisation of manufacturing parameters will play an important role in improving the reliability of metal components in industrial applications.
References
- Eugene BroermanIII,Peter Renzi; “Hydrogen Embrittlement”; From: Journal of Natural Gas Science and Engineering, 2022.
- Guy Ben-Hamu, Polina Metalnikov, Dan Eliezer; “The effect of low hydrogen content on hydrogen embrittlement of additively manufactured 17–4 stainless steel”; Progress in Additive Manufacturing (2024) 9:1319–1330.
- G. Álvarez, Z. Harris, K. Wada; “Hydrogen embrittlement susceptibility of additively manufactured 316L stainless steel: influence of post-processing, printing direction, temperature and pre-straining”; physics.chem, 14 Nov 2023.