Author: Ph.D. Yolanda Reyes, July 13, 2022.
Introduction
Acoustic Emission (EA) is a Non-Destructive Testing Method (NDT), based on a physical phenomenon that takes place inside materials. Considering the physical phenomenon, the Acoustic Emission is defined as the spontaneous energy emitted by a material, in the form of transient elastic waves [1]. The application of stress, severe environmental conditions on a metallic material, can produce changes in its internal structure, such as: the growth of cracks, local plastic deformation, corrosion or phase changes that are normally accompanied by the emission of elastic waves. inside. These waves therefore contain valuable information about its internal behavior. Also, an EA test is useful for monitoring defect formation in a material by detecting and analyzing the acoustic emission waves generated.
This type of test differs from the rest of the NDT in two fundamental aspects: The first lies in the origin of the EA signal, since it is a passive method, it detects the energy that is released in the material itself, while the other methods require artificial input of energy for the detection of defects (for example: X-rays, gamma rays, ultrasound, thermal energy or microwaves). The second is that it reveals dynamic phenomena. This characteristic is especially relevant, since during the test only active phenomena are detected, such as the growth of cracks, and not geometric discontinuities as the rest of the NDT methods do.
The EA test is effective in detecting the behavior of fracture and fatigue in a variety of materials such as metals, advanced composite materials, plastics, concrete, wood, etc. In this sense, the test is useful to monitor the integrity of structures non-invasively, as well as for the characterization of materials subjected to deformation and/or fracture. Some applications in which the use of this test is common are the detection of faults and/or leaks in pressure vessels, piping systems, storage tanks, welding control, detection of corrosion processes, inspection of structures or machinery.
Through the EA test, it is possible to measure, only qualitatively, the amount of damage that occurs in a structure or component. In order to obtain quantitative results on the size, depth and acceptability of the damage it is necessary to combine this test with other methods. Another drawback is sensitivity to background noise, both mechanical and electrical, making it difficult to use in harsh service environments. To guarantee the success of the test, the discrimination and reduction of noise signals is crucial, considering noise as the signals generated by all the mechanisms that are irrelevant to the test that is being carried out.
Analysis of the results of the EA technique
Acoustic emission analysis is capable of revealing damage processes in materials throughout the loading history, it is obvious that the recording of damage processes from the microscopic to the macroscopic scale produces large data sets even for relatively short periods of time [ two]. The number of events can be several thousand during a test. The high number of acoustic emissions is a fact that must be taken into account during the analysis procedure, due to the often low signal-to-noise ratio of the signal, several additional data processing steps are needed before interpretable results are obtained.
Although its domain requires high-level training, and personnel with certain qualifications, the reliability of its results and the real-time data that it allows to record, makes it a high added value. In addition to this, the versatility it offers, such as the study of behavior under load of structures and civil works, as well as a wide variety of equipment and components from industries such as oil and aeronautics, increases its attractiveness in terms of services to be provided. .
It is necessary to be clear about a couple of basic principles regarding the performance of the EA, since its performance depends on them.
By its very nature, it differs from conventional volumetric Non-Destructive inspection methods in certain respects. The first aspect to consider is that an effect or discontinuity such as a crack must necessarily be propagating and releasing energy so that the sensors can capture this event and identify the area. A “static” crack that is not releasing energy, by not producing any emission, will not be detectable with this technique, therefore. Methods such as UT or RT detect these defects by communicating energy to the material, which interacts with it. In the case of AE, the energy comes from an applied load, in many cases typical of the work performed by the structure itself.
The second important aspect to consider is that this technique detects dynamic processes strongly linked to the mechanisms of deterioration of structural integrity in real time.
In Figure. 1, it can be seen how the array of sensors allows establishing the location of the sources of the events.
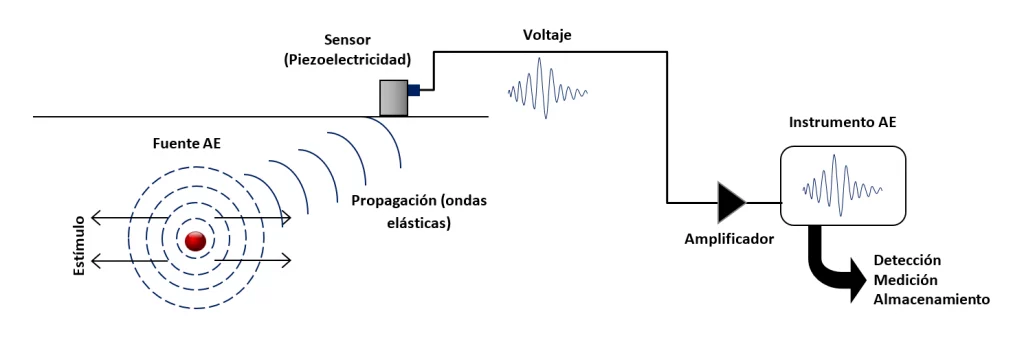
Why is acoustic emission testing important?
We must be aware that carrying out quality acoustic emission tests will help reduce costs in the future, since we will be able to reduce maintenance and repair costs. In addition, to help guarantee the safety of equipment and facilities, verifying their quality.
As an example we can cite the case of atmospheric storage tanks (AGST) in the oil production industry.
The test allows a ranking of the tanks belonging to a storage yard, based on the condition of integrity that they present during the test. It is especially suitable for verifying the integrity of floor sheets. If there are leaks or seepage through the floor, they will be detected immediately. The same happens with the existence of corrosive processes, since the by-products of the corrosion process generate events that are detected during monitoring.
These by-products have a physically much more brittle structure than steel and the detachment of this residue under load is what produces these events Figure 2. The advantages of the technique are enormous, from the operational point of view, since it avoids having to take the tank out of service to proceed with the inspection of the floor. Monitoring is carried out by means of EA and the conditions are established according to the evaluation of the results obtained.
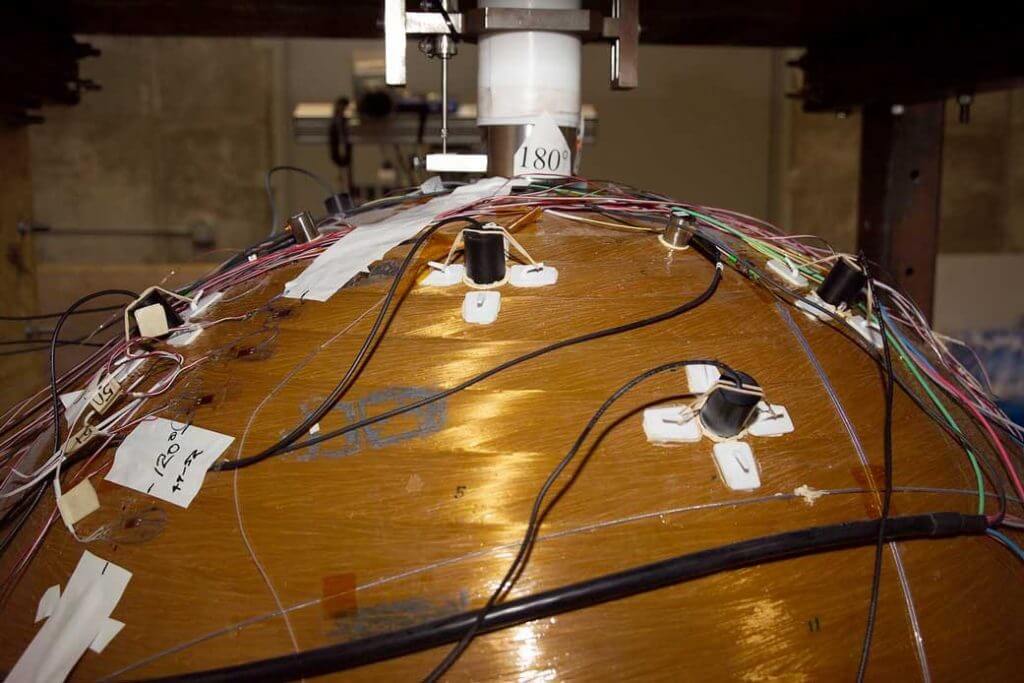
Acoustic Emission Scope
One of the most impressive features of the Acoustic Emission is the wide dynamic range of the observed signals. Signals from a few tenths of micro-Volts induced by micro-deformation processes, to signals of several Volts generated by fracture processes, can be detected. This feature allows the development of a wide variety of applications.
In the laboratory, the Acoustic Emission method is a tool used to study deformation and fracture processes. In the industrial sector it is used for the inspection of pressure vessels, storage tanks, aircraft and space vehicles, power plant utilities, bridges, railway tanks and hoisting cranes. Acoustic emission is typically used for the detection of cracks, corrosion, weld defects, and material embrittlement.
Some of the most widespread applications of this NDT method are summarized below:
- Testing and characterization of various materials: metals, advanced composite materials, plastics, wood, concrete, biological material, etc.
- Chemical and oil industry: integrity tests on pressure vessels, tests on storage tanks, cryogenic tanks, reuse time tests on thermal reactors, towers, columns and piping systems, tests on the bottom of tanks, detection of corrosion in real time, testing of FRP tanks, inspection of the pipe network, detection of leaks in valves and buried pipes, detection of sand in offshore pipes and monitoring of offshore platforms
- Diagnosis of power plants
- Aviation and aerospace industry: aircraft testing, aircraft aging testing, component fatigue testing, underwing corrosion detection, on-site inspection of landing gear parts, helicopter blade testing, crack detection in the fuselage, etc.
- Metallurgical industry: tool wear and breakage detection, detection of contact between parts, quality control of metalworking processes, collision detection and prevention in manufacturing processes.
- Civil engineering: inspection of the structure of concrete buildings, tests on bridges and tunnels, continuous monitoring of damage or propagation of cracks, tests on cranes, etc.
- Applications in transport: detection and location of faults in trailers, rail cars and tank trucks, detection of cracks in railway materials and structures, integrity tests of bridges and tunnels, control of the condition of bearings and bearings of trucks and trains, detection of cracks in the wheels and axles of trains, etc.
- Other applications: welding control, geological and seismological applications, supervision of motor conditions, on-line process control of rotating machines, etc.
Conclusion
This method is very effective when used to detect fatigue and fracture behavior in metals, advanced composites, plastics, fiberglass, ceramics, concrete, and wood. With the right equipment and trained personnel, faults on the micro-metric scale can be detected. Its numerous advantages and applications have made EA a well-established and reliable NDT method for damage assessment and failure prevention in a material. This method can help avoid costs associated with repairs to damaged structures if a defect is not detected.
About the Author
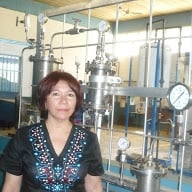
Ph.D, in Electrochemistry and Corrosion, with more than 30 years of experience and a wide and versatile knowledge in Corrosion Sciences and Chemical Technology at the Academic and Industrial level. Advisor of plans for maintenance programs in the industry in oil companies, in charge of chemical and mechanical cleaning services for equipment such as: boilers, tanks, heat exchangers, among others. Read more