Introduction
In an increasingly competitive business environment, companies are constantly looking for ways to optimize their processes to improve efficiency, reduce costs and maintain a high level of competitiveness. In this context, Lean Manufacturing has established itself as a fundamental methodology for achieving these objectives.
Lean is not just about reducing costs, but about creating more value with fewer resources. This approach, which originated in the automotive industry with the Toyota Production System (TPS), has evolved into a comprehensive philosophy that applies to companies in all sectors. Lean Manufacturing is a way of managing production processes with the objective of maximizing value and minimizing waste at every stage of the production chain.
But what are the key characteristics of Lean Manufacturing? While Lean has several facets, there are two key characteristics on which its long-term success is based: elimination of waste and continuous improvement. These two characteristics are fundamental for an organization to implement Lean effectively, optimizing resources, improving quality and reducing cycle times, with a corresponding increase in competitiveness.
What is Lean Manufacturing?
Lean Manufacturing is a production management philosophy that seeks to optimize processes by eliminating waste and maximizing the value delivered to the customer with the least amount of resources possible. Its origin is found in the Toyota Production System (TPS), but today, its applicability extends beyond manufacturing, encompassing various industrial and commercial sectors.
The purpose of Lean is to do more with less: to reduce costs, improve efficiency and increase quality, all while minimizing waste of time, materials and labor. Throughout its evolution, Lean has proven to be a powerful methodology that enables companies not only to remain competitive, but also to foster a culture of continuous improvement.
Lean Manufacturing fundamentals
Although Lean Manufacturing includes a variety of strategies, tools and techniques, they are all based on the following key principles:
- Customer value: Lean starts with a clear definition of what really matters to the customer. This principle focuses on identifying which aspects of a product or service add value to the end customer and which activities do not. This allows efforts to be focused on what really benefits the customer, eliminating all activities that do not add value (i.e., waste).
- Waste elimination: A central aspect is the elimination of waste. Waste (or “Muda” in Japanese) refers to any activity that consumes resources (such as time, money or energy) without adding value to the customer.
- Continuous flow: Establish a continuous workflow, eliminating interruptions and bottlenecks. This involves managing processes so that materials, information and people move smoothly, reducing waiting times and increasing efficiency.
- Just-in-time production (JIT): This principle involves producing and delivering products only when they are needed, in the right quantity and at the right time. Just-in-time production helps to reduce inventories and improve efficiency, ensuring that resources are used optimally, and unnecessary products are not accumulated.
- Continuous improvement (Kaizen): Continuous improvement, also known as Kaizen, is a fundamental principle of Lean. Kaizen emphasizes the need to make small but constant improvements in all aspects of the production process, involving all personnel in identifying problems and implementing solutions. Through this cycle of constant improvement, companies can adapt to market changes and overcome operational obstacles efficiently.
- Respect for people: Although this principle may not be as well known as the previous ones, it is significant in the Lean philosophy. Respect for people involves fostering an environment where the knowledge and skills of all employees are valued and leveraged. Rather than imposing solutions from above, Lean promotes the active participation of workers in decision-making and process design, which strengthens the culture of continuous improvement.
Why is Lean Manufacturing important?
Implementing Lean Manufacturing has multiple benefits for companies, including:
- Cost reduction: By eliminating waste and optimizing in processes, companies can reduce operating costs.
- Increased efficiency: By improving workflows and eliminating inefficiencies, Lean increases productivity.
- Quality improvement: Constant improvement in processes and reduction of defects leads to higher quality products.
- Customer satisfaction: By delivering quality products, on time and at a competitive cost, companies can improve customer satisfaction and loyalty.
- Increased responsiveness to change: Lean’s continuous improvement, agile operations and flexibility enable companies to adapt quickly to changes in demand or the marketplace.
The two key characteristics of Lean Manufacturing
Although Lean Manufacturing includes a variety of principles, approaches and tools, in this article we are going to focus on two essential characteristics that are fundamental to the success of Lean in any company:
- Waste elimination (Muda)
- Continuous improvement (Kaizen)
These two characteristics are the pillars of operational efficiency and competitiveness, and their effective implementation is what truly transforms a company into a lean organization. Throughout this article, we will explore how these characteristics are interrelated and how you can successfully implement them in your company.
Driving efficiency through waste elimination (Muda)
Waste elimination, or Muda in Japanese, is one of the fundamental pillars of Lean Manufacturing. It refers to the identification and elimination of all activities that do not add value to the final product or service. The main idea of Lean is that each step in the production process must contribute to the creation of value for the customer. If a step does not, it is considered waste and should be eliminated or minimized.
What is waste?
Waste is any activity or resource used that does not directly contribute to the final value perceived by the customer. This can include material resources such as time, human effort, energy and space, among others. The basic principle of Lean is that all waste must be identified and eliminated, not only to improve efficiency, but also to improve quality, reduce costs and streamline processes.
7 types of waste in Lean Manufacturing
- Overproduction: Producing more than needed or before it is needed. Overproduction is one of the worst types of waste, as it not only consumes resources, but also generates unnecessary inventories and reduces the company’s flexibility.
- Waiting: The downtime of employees, equipment or materials while waiting for the next task or process. This may include waiting for materials to arrive, waiting for information, or waiting for equipment to become available.
- Unnecessary transportation: The unnecessary movement of products, materials or information from one location to another. This may include transporting parts from one area to another without adding value to the product.
- Overprocessing: Performing more work than necessary, such as adding features to the product that the customer does not require or performing additional steps that do not add value.
- Inventories: Inventories are necessary to maintain production, but having too much inventory creates several problems, such as unnecessary storage space, higher maintenance costs, and potential obsolescence.
- Unnecessary movements: Excessive or inefficient movements made by workers when performing their tasks. These can be physical movements, such as walking or adjusting tools, that do not add value to the work.
- Defects: The time and resources wasted in producing defective or error-prone products that must be corrected or discarded. Quality must be controlled at all stages of production to avoid these defects.
In this video, the 5 fundamental principles of lean manufacturing to optimize processes are presented. This guide provides a clear overview for those looking to improve their organizations. Courtesy of: TRADESAFE.
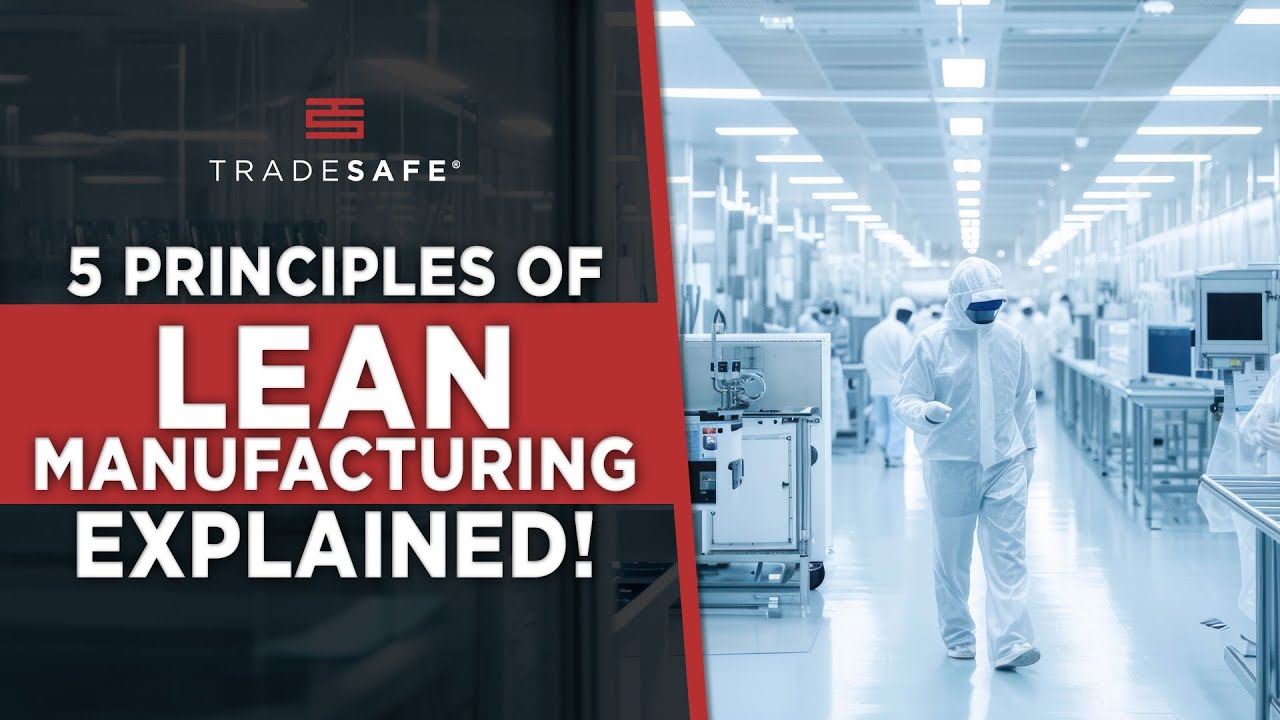
What is Lean Manufacturing? 5 principles explained!
Impact of waste disposal
Eliminating waste improves efficiency, reduces operating costs, improves quality and speeds up delivery times, resulting in greater customer satisfaction and increased competitiveness in the marketplace. By reducing the time it takes to produce a product or provide a service, companies can respond more quickly to market demands, improve their flexibility and be more adaptable.
Eliminating waste also contributes to the creation of a healthier and more efficient work environment, where employees can perform their tasks without the interruptions and obstacles that often arise from operational inefficiency.
How to implement waste elimination in an organization
- Value stream mapping: Use tools such as value stream mapping to identify all stages of the process and visualize where waste occurs.
- Set clear objectives: Set specific goals for waste reduction in key areas and measure progress with performance indicators.
- Continuous training: Train all personnel in Lean principles and encourage proactive identification of waste in their work areas.
- Lean tools: Implement tools such as 5S (order and cleanliness), Kanban (visual inventory management) and Kaizen (continuous improvement) to support waste elimination.
Continuous improvement (Kaizen), a key feature for competitiveness
The concept of continuous improvement, known as Kaizen in Japanese, is one of the most powerful and essential features of Lean Manufacturing. It refers to the practice of making constant small improvements in all aspects of a process, whether in production, management or services. The key to Kaizen is that these improvements need not be large or revolutionary, but are based on a gradual and sustainable approach that generates significant results over time.
What is Kaizen?
Kaizen comes from the Japanese words “Kai” (change) and ‘Zen’ (good), which together mean “change for the better” or “continuous improvement”. It is a work philosophy that seeks constant improvement at all levels of the organization, involving all employees in the process. Kaizen is not limited to a single area of the company, but must be applied transversally, touching all processes, from the production line to top management.
Unlike approaches that seek rapid and drastic changes, Kaizen emphasizes constant evolution. Improvements are small but cumulative, and each action taken focuses on optimizing processes and increasing efficiency.
The continuous improvement cycle: PHVA
A central tool of Kaizen is the PHVA (Plan, Do, Check, Act) cycle, an iterative process that allows improvements to be constant and sustainable:
- Planning: Identify the problem or area for improvement, set clear objectives and design a strategy to implement them.
- Do: Implement solutions in a controlled manner, often in a test environment or with a small group before scaling up.
- Verify: Measure the results of the actions taken, compare them with the objectives and analyze the data to verify if the improvement has been achieved.
- Act: If the results are positive, make permanent changes; if not, adjust and retest. This cycle is repeated continuously.
This cycle allows organizations to adapt quickly and make adjustments as needed, ensuring that processes are always evolving towards greater efficiency.
Impact of Continuous Improvement in Lean Manufacturing
The continuous improvement approach in Lean Manufacturing has a significant impact on several aspects of a company’s operation:
- Defect reduction: Through constant improvement, process failures are identified and corrected before they become defects, which improves product quality and reduces the need for rework.
- Increased efficiency: Kaizen helps identify areas where processes can be faster and less costly, resulting in higher productivity.
- Better employee participation: By involving all employees in the improvement process, a more collaborative work environment is fostered, with each team member contributing ideas and solutions.
- Adaptability: Continuous improvement allows companies to adapt quickly to changes in the market, technology or customer requirements, giving them a competitive advantage.
How to implement continuous improvement in your organization
Implementing Kaizen requires a continuous commitment to improvement and a structured approach. Here are some key steps to put continuous improvement into practice:
- Foster a Kaizen culture: All levels of the organization must be committed to continuous improvement. From top management to rank-and-file employees, everyone must be an active part of the process.
- Ongoing training: Staff should be regularly trained in Kaizen methodologies and how to identify areas for improvement within their roles and tasks.
- Involve all employees: Kaizen is only successful when all employees are committed to improvement. Involving every team member in identifying problems and solutions ensures that improvements are practical and effective.
- Set clear goals: Improvement objectives should be specific, measurable and achievable. Setting clear goals for each improvement cycle will help maintain focus and ensure that efforts are effective.
- Measure progress: Tracking results is crucial to assess whether improvements have been successful. Use key performance indicators (KPIs) to monitor progress and ensure that objectives are being met.
- Repeat the cycle: Continuous improvement is a never-ending process. After each cycle, it is important to evaluate the results and continue to look for new areas of improvement.
How to implement Lean Manufacturing successfully
Implementing Lean Manufacturing is not an overnight task. It is a structured and gradual process that requires commitment, planning and active participation from all levels of the organization. Here are the key phases to successfully implement Lean Manufacturing:
Top management commitment: Implementing Lean Manufacturing starts with absolute commitment from top management. Leaders must be the first to drive the change to a lean culture and support the transformation at the organizational level.
Actions:
- Vision and strategy: Top management must clearly communicate the vision of lean and how it fits within the company’s strategic objectives.
- Allocation of resources: Adequate staff, time and resources must be allocated for Lean to be implemented effectively.
- Commitment to continuous improvement: It is critical that leaders commit to practicing the principles of continuous improvement (kaizen) and lead by example, actively engaging in improvement projects.
Initial assessment and diagnosis: Before starting with the implementation of Lean, it is necessary to perform a detailed diagnosis of the current processes. This step consists of evaluating the current state of the company’s operations to identify areas for improvement.
Actions:
- Value Stream Mapping: This tool allows visualizing the flow of materials and information in the production process, identifying areas where waste is generated.
- Waste identification: Using the 7 Mudas (overproduction, waiting, transportation, overprocessing, inventories, unnecessary movements and defects), all processes are analyzed to identify which activities do not add value.
- Key indicators analysis: Current KPIs, such as cycle time, defect rate, costs and productivity, should be reviewed to have a clear reference on how to improve.
Staff training and coaching: For Lean to be successful, it is essential that all employees are trained and aligned with the Lean philosophy. This includes not only production personnel, but also supervisors and managers.
Actions:
- Lean tools training: Train personnel in specific Lean tools, such as 5S, Kanban, Just-in-Time (JIT) and Kaizen.
- Problem-solving training: Employees should be trained in problem-solving techniques, such as root cause analysis and use of the PDCA cycle.
- Encourage active participation: Ensure that employees understand how they can identify waste and propose improvements in their work areas.
Progressive implementation and pilot projects: Instead of implementing Lean throughout the company immediately, it is advisable to start with pilot projects in specific areas. This allows adjustments to be made before a full-scale implementation.
Actions:
- Select pilot areas: Choose areas or processes where quick and tangible results can be obtained with Lean implementation, such as a production line or a logistics department.
- Implement specific improvements: In the pilot areas, apply tools such as Kanban to manage inventories, 5S to improve order and cleanliness, and JIT to reduce lead times.
- Measure results: Evaluate the results of the pilot through KPIs, such as cycle times, waste reduction and quality improvement. Use these results to make adjustments before expanding Lean to other areas.
Measuring results and adjustments: Lean implementation is a continuous process. It is critical to measure results regularly to ensure that initiatives are achieving the desired objectives. Adjustments should be made according to the results obtained.
Actions:
- Establish KPIs: Define key performance indicators (KPIs) related to waste elimination and continuous improvement. Examples of KPIs include cycle times, defect rate, inventory level and operating costs.
- Monitor progress: Conduct periodic assessments to measure the impact of Lean on processes and correct areas of opportunity.
- Adjust and optimize: Based on the data collected, make adjustments to Lean processes, extend improvements to other areas and continue to work on waste reduction.
Foster Lean culture: The true transformation to Lean Manufacturing only occurs when Lean becomes part of the organizational culture. This means that everyone in the organization must be committed to continuous improvement and elimination of waste.
Key actions:
- Involve all levels: Lean should not only be the responsibility of management or the production department. All employees must be committed to Lean principles.
- Recognize achievements: Recognize and reward employees who actively contribute to continuous improvement and waste elimination.
- Maintain continuous improvement: Ensure that Lean is not a short-term initiative, but a work philosophy that lasts over time.
Below is a table illustrating some points that relate the phases of Lean Manufacturing implementation to the two fundamental characteristics studied in this article.
Key characteristics of Lean Manufacturing
Implementation phase | Waste disposal (Muda) | Continuous improvement (Kaizen) |
---|---|---|
1. Top management commitment | Define key areas for waste reduction and set clear goals for waste elimination. | Promote an organizational culture based on Kaizen, where all levels of the company are committed to constant improvement. |
2.Initial evaluation and diagnosis | Perform value stream mapping to identify the types of waste in the processes. | Apply Kaizen to detect opportunities for continuous improvement in current processes. |
3. Staff training and coaching | Training in the identification and elimination of waste in day-to-day operations, using tools such as 5S and Kanban. | To teach the PACV cycle and the Kaizen philosophy to implement small constant improvements in the processes. |
4. Progressive implementation and pilot projects | Implement improvements in pilot areas focused on eliminating waste (e.g., reducing lead times and overproduction). | Implement the Kaizen cycle in pilot projects, where small improvements are made constantly to optimize the process. |
5. Performance Measurement and Adjustments | Measure waste reduction, such as reduction of defects and cycle times. | Measure the results of the implemented continuous improvements and make adjustments using the PDCA cycle. |
6. Promoting Lean culture | Promote the active participation of all employees to identify and eliminate waste at the individual and group level. | Reinforce the practice of Kaizen as part of the company’s DNA, ensuring that continuous improvement is a daily commitment of all employees. |
Conclusions
Lean Manufacturing is a methodology to improve operational efficiency and reduce costs in companies, focusing on the elimination of waste and continuous improvement, so that organizations can optimize processes, improve quality and maximize the value delivered to the customer. The elimination of waste, such as overproduction, waits and defects, is fundamental to eliminate inefficiencies and reduce operating costs. Implementing tools such as value stream mapping helps to identify and eliminate these wastes at all stages of production.
On the other hand, continuous improvement fosters a culture of constant innovation through the PHVA cycle, which allows for small, continuous and measurable improvements over time, contributing to the sustainable success of the organization. This philosophy must be adopted by all levels of the company, from top management to operational staff, to generate a significant impact on competitiveness and productivity in the long term.
Implementing Lean successfully requires a gradual approach, starting with a clear diagnosis, staff training and pilot projects. It is a process that involves both waste reduction and continuous improvement, two characteristics that must work together to achieve efficient and sustainable results. By adopting these practices, companies reduce costs and establish a culture of operational excellence that fosters growth and constant innovation.
References
- Womack, J. P., & Jones, D. T. (2008). Lean thinking: Banish waste and create wealth in your corporation. Free Press.
- Liker, J. K. (2014). The Toyota way: 14 management principles from the world’s greatest manufacturer. McGraw-Hill.
- Ohno, T. (2008). Toyota production system: Beyond large-scale production. Productivity Press.
- Rother, M., & Shook, J. (2021). Learning to see: Value stream mapping to add value and eliminate muda. Lean Enterprise Institute.
- Imai, M. (1986). Kaizen: The key to Japan’s competitive success. McGraw-Hill.
- Liker, J. K., & Meier, D. (2016). The Toyota way to continuous improvement: Linking strategy and operational excellence to achieve superior performance. McGraw-Hil