Non-Destructive Testing has positioned itself as a powerful tool in the detection of failures in the different components of the various process units to avoid disasters in the energy industry.
Safety and operational reliability are of particular importance in the energy industry.
Industry interest in quality assurance and inspection has greatly influenced the understanding and development of test methods that benefit virtually all industries that depend on the manufacturing process.
The inspection through the use of END, represents a significant step in all phases of the production chain of goods and services: from manufacturing and construction (controlling raw materials), to the control of construction processes (construction inspections), as well as in operation and maintenance, being key to the reliability of the expected results and the capacity of the personnel who carry out these inspections.
It is for this reason that the people who apply these techniques must have a high degree of competence due to the importance of their function, and this competence is acquired through previous education, specific training in the different tests that are used, the experience that goes acquiring and good vision skills (visual acuity and color perception). This competition makes it possible to make the entire production process of goods and services more secure, reliable and profitable, maintaining the continuity of operations and avoiding the occurrence of failures, which can be catastrophic, especially when it comes to the energy industry.
NDT and how to avoid disasters in the energy industry
What are non-destructive tests?
Non-destructive tests are inspection methods that allow the detection and evaluation of defects in materials and structures, as well as knowing their properties without causing permanent damage. There are different types of END, such as ultrasound, radiography, visual inspection, magnetic particles, infrared thermography, and electromagnetic tests, among others.
These tests are used in the inspection of critical equipment and structures in the oil, gas, nuclear energy, and other areas related to the energy sector.
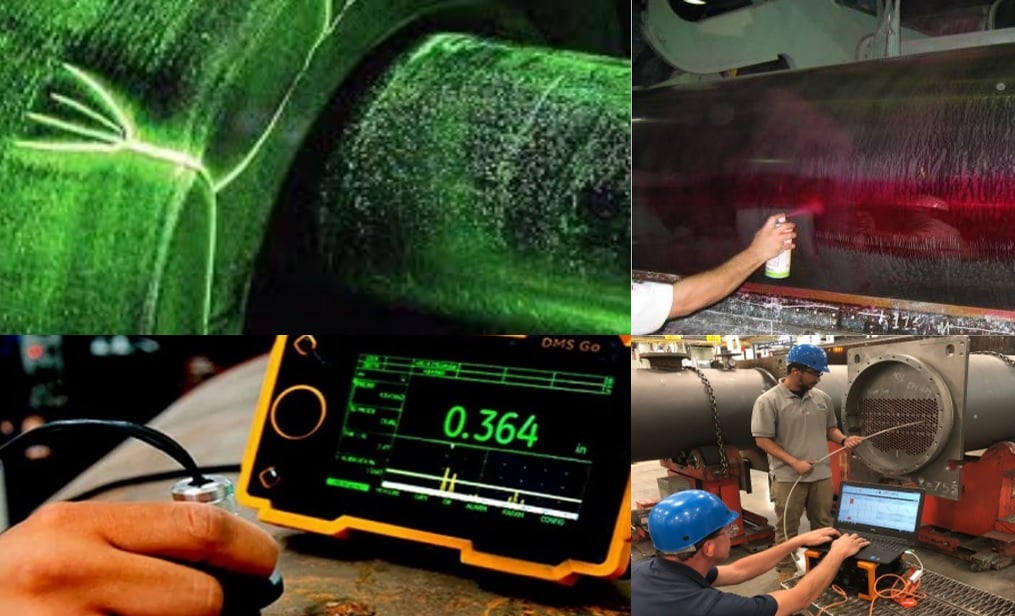
oil, gas, nuclear power industries and other areas related to the energy sector.
Causes of disasters in the energy industry
The energy industry is essential to the functioning of modern society, but it is also one of the most dangerous. Disasters such as explosions, oil spills, and nuclear power plant failures can have devastating consequences for human safety and the environment. Below are some of the main causes of disasters in the energy industry.
- Technical failures: Disasters can occur due to equipment or infrastructure failures. For example, an explosion at an oil refinery can be caused by a pipeline leak or a safety valve failure.
- Human errors: Workers in the energy industry can make mistakes that result in disasters. For example, a nuclear power plant operator can make a mistake in adjusting the reactor pressure, which can cause a core meltdown and a release of radiation.
- Extreme weather conditions: Storms, floods, earthquakes, and other natural events can affect energy infrastructure and cause disasters. For example, Hurricane Katrina caused severe damage to oil rigs in the Gulf of Mexico.
- Terrorism and sabotage: Acts of terrorism and sabotage can cause disasters in the energy industry. For example, an attack on a gas plant can cause an explosion and fire that endangers people’s lives and causes damage to infrastructure.
- Lack of regulation and supervision: The lack of measures and review in companies in the energy industry makes them operate in an unsafe manner, causing disasters such as the BP oil spill that occurred in the Gulf of Mexico in 2010.
Disasters in the energy industry can occur for a variety of reasons, including technical failures, human error, extreme weather conditions, terrorism and sabotage, and lack of regulation and supervision. It is essential that measures are taken to prevent these disasters and protect human safety and the environment, and in this regard, the use of END applied by qualified personnel is key to avoiding many of these causes.
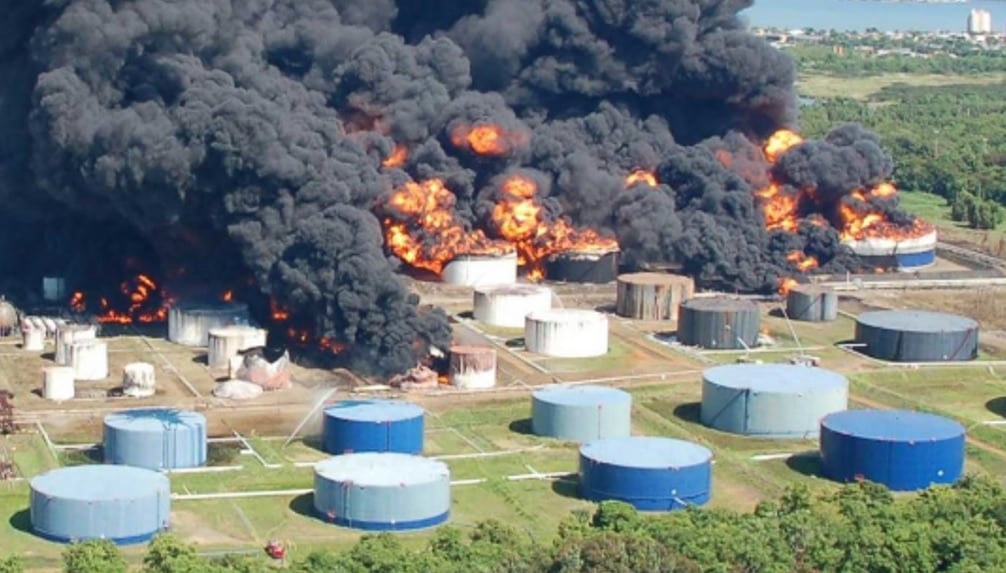
Importance of NDT training
The energy industry encompasses all those industrial sectors related to the production and sale of energy. Among which stand out: The fossil fuel industries (oil, gas and coal), the nuclear energy industries, the renewable energy industry, among others.
In reference to the oil and gas industry, and due to the raw material (hydrocarbons) that they process and the products that they generate, there is a high risk of occurrence of unwanted events that can be catastrophic.
Industrial disasters have been in this sector and for various reasons, such as ignorance and poor maintenance of piping systems, tanks, pressure vessels, among other components, constituting one of the latent risks to the health and safety of the population. In general, company personnel and the environment.
Safety regulations and standards are important for organizations seeking to guarantee, through processes, the safety, excellence and profitability of materials. This same criterion applies to other energy sectors, such as nuclear energy, due to the radioactive materials used as fuel and the waste they generate.
END training is necessary to ensure that technicians are trained to perform assays safely and effectively, providing reliable results. The training includes theoretical and practical knowledge, as well as the use of instruments with updated technology for the evaluation of the various components of the sector, and knowledge of safety requirements and quality protocols. NDT-trained technicians can identify the different types of defects in materials and structures, allowing preventive measures to be taken to avoid catastrophic failures with the aforementioned consequences.
Benefits of NDT training
END training allows inspectors to identify defects in materials and structures, preventing the occurrence of catastrophic failures and ensuring safety in the workplace. This reduces maintenance costs by allowing early detection of problems and making repairs before defects become major problems.
The application of the tests in the quality assurance phase of the raw material (tubes, plates, accessories, among others) is required for the subsequent manufacture of the different components of the different process units of the energy industry (pressure vessels, tanks, exchangers, among others).
It allows the early detection of defects and with it the delivery of materials that do not meet the required quality, representing significant savings in the construction of the different components of the energy sector by avoiding rework and with it the extra consumption of time, manual labor work and energy.
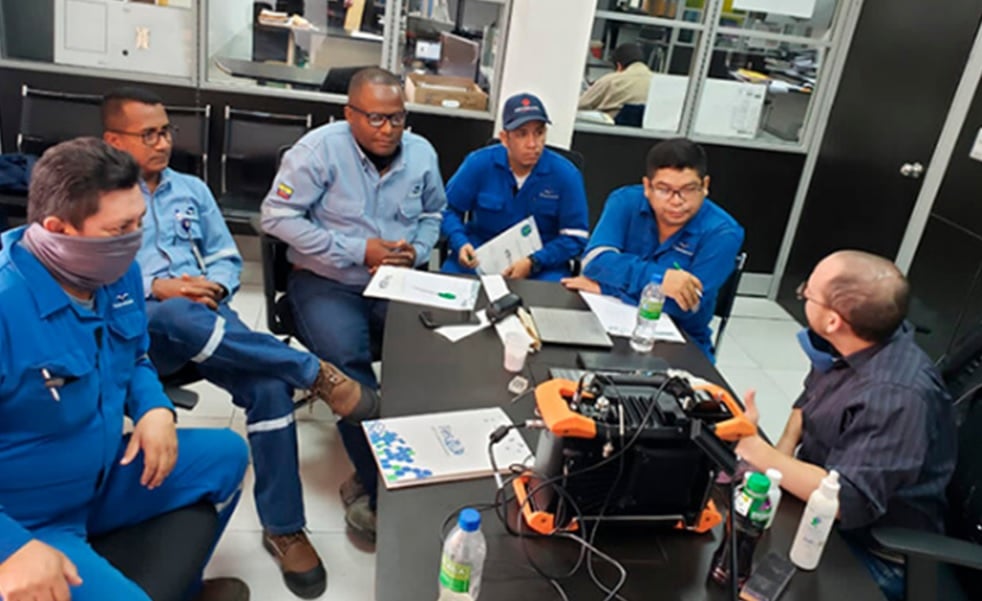
Conclusion
END training is essential for risk management in the energy industry, by applying these tests on time, defects in materials and structures can be detected, which can prevent disastrous failures and guarantee safety in the workplace. Therefore, technicians must be adequately trained in END to certify a safe, effective inspection and the delivery of reliable results of critical equipment and structures in the sector.