Table of Contents
Carrying out pipeline inspections always allows professionals to observe and analyze the interior of the network. This process goes far beyond identifying and repairing faults. Likewise, the objective of a pipeline inspection is also to obtain certain data and information. In this way, it allows us to plan possible changes or repairs that may be necessary in the future. In other words, carrying out a pipe inspection in a company will help to keep them in good condition for longer.
Importance of Pipeline Inspections in the Oil and Gas Industry
In the light product terminal industry, pipelines are a fundamental part of the liquid and gas transportation process. Over the years, there have been a wide variety of accidents involving pipe failure at light product terminals.
Pipeline inspections are important because they ensure the safe operation of pipelines. Lack of proper inspections and maintenance can lead to pipeline failure, which can result in significant ecological damage, loss of life, and property damage. Periodic inspections, Non-Destructive Testing , corrosion prevention, repair and maintenance, and education and training are essential to ensure the safe operation of pipelines in light product terminals and prevent accidents.
In addition, the application of best practices in pipeline inspections ensures early detection of insipient defects and deterioration, which will allow immediate application of solutions and maintenance, avoiding possible failures and catastrophic damage.
Pipelines are a critical part of the oil and gas industry, used to transport crude oil, natural gas, and other petroleum products from one place to another. Pipelines are also used to ship refined petroleum products such as gasoline, diesel, and jet fuel from refineries to storage terminals and distribution centers.
Past Accidents
The oil and gas industry has experienced several pipeline accidents in the past, and these accidents have resulted in considerable environmental damage, loss of life, and extensive property damage.
One of the most destructive pipeline accidents in recent history occurred in 2010 when the Deepwater Horizon oil rig exploded in the Gulf of Mexico , resulting in the largest oil spill in United States history. The accident caused the loss of 11 workers and significant ecological damage.
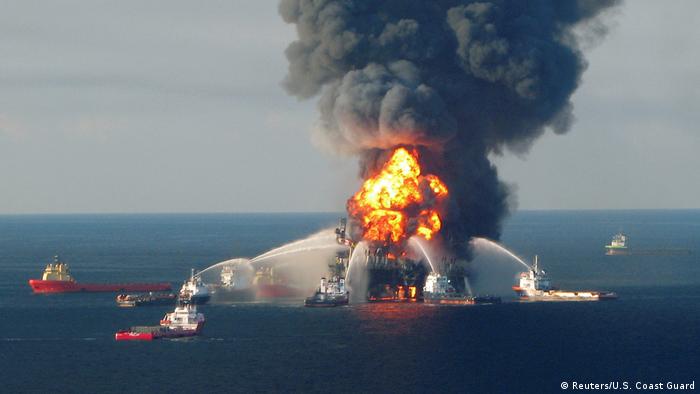
Another major such accident occurred in 2013 when a pipeline carrying crude oil from North Dakota to Illinois ruptured, spilling more than 20,000 barrels of oil into a nearby river. The ecological damage caused was considerable and residents near the disaster area had to be evacuated.
These accidents and others like them have highlighted the need for best pipeline inspection practices and the importance of regular maintenance and repair.
Best Practices for Light Product Terminal Piping Inspections.
Another important lesson that we can learn from past accidents is the importance of having a well-established risk management system. An effective risk management system can help identify and assess the risks associated with pipelines in light product terminals and take the necessary steps to mitigate those risks.
The safe operation of pipelines requires regular inspections and maintenance to ensure that pipelines are in good condition and free of defects that could lead to failure. The following are some of the best practices for light product terminal piping inspections:
scheduled inspections
Scheduled pipeline inspections are critical to the safe operation of pipelines . Inspections must be carried out at regular intervals to identify and detect any defects or early signs of wear or damage that could lead to failure. The frequency of inspections will depend on the time in service and condition of the pipeline, the type of product being transported, and the location of the pipeline.

Non destructive essays
Non-Destructive Testing (NDT) is an important part of pipeline inspections . These techniques, such as ultrasonic testing (UT), magnetic flux leakage (MFL), and pulsed eddy current (PEC), can be used to detect corrosion and other defects in pipelines without damaging the pipeline. These tests must be accompanied by visual inspections to ensure that defects and imperfections are detected.
Corrosion Prevention
Corrosion is the degradation of a metal or metal alloy due to the effect of oxidizing agents which makes it a serious problem in pipelines and can lead to failure if not addressed. Corrosion prevention measures such as cathodic protection, coatings, and inhibitors should be used to minimize this phenomenon. It is recommended conduct scheduled inspections to ensure that corrosion prevention measures are working properly.
Predictive Maintenance
Maintenance in all its stages must be systematized, since its good application, both predicative and corrective, in the case of repairs, are critical for the safe operation of the pipelines. Any defects or damage identified during inspections must be repaired immediately to prevent premature damage.
Training
The training and training of the personnel that carry out the inspections are essential for the safe handling of the lines of the terminals. Operators and inspectors must receive training on best practices for pipeline inspection and maintenance. They must also receive training on the dangers associated with pipelines and the importance of industrial safety.
The safe operation of pipelines is critical to the oil and gas industry, and any failure can cause significant ecological damage, regrettable loss of life, and property damage.
Planned inspections, non-destructive testing, corrosion prevention, maintenance, and training are essential for the best and safe performance of light product terminals . Lessons learned from past accidents have highlighted the need for best line and pipeline inspection practices and the importance of scheduled maintenance and repair.
Accident prevention is a priority for any industry. Accidents can cause significant injury, loss of life, and financial and reputational damage. One of the most effective ways to prevent accidents is through planned inspections of equipment and infrastructure.
However, traditional inspection methods can be time consuming and expensive, and may not always identify developing problems before they become critical. That’s where advanced technology like artificial intelligence and machine learning can really help.
Inspection planning may include the use of state-of-the-art technology to determine patterns and trends that could indicate a developing problem . Artificial intelligence and machine learning algorithms can analyze vast amounts of data from multiple sources, such as sensor readings, maintenance records, and historical data, to identify potential indications of failure signals before they become critical.
For example, suppose you are responsible for the maintenance of a large industrial plant. It could use artificial intelligence and machine learning algorithms to analyze data from various sensors throughout the plant, such as temperature, pressure, and vibration sensors. Algorithms can identify patterns and trends in data that could indicate a problem that is just beginning, such as a cavitating pump or a leaking valve.
Once a potential problem is detected, you can take proactive steps to address it before it becomes a critical problem. This could include scheduling maintenance on the affected equipment or taking it offline for repair.
By taking these measures proactively, you can reduce the risk of accidents and avoid costly downtime.
Artificial intelligence and machine learning algorithms can also help with predictive maintenance. By analyzing data from sensors and other sources, algorithms can predict when equipment is likely to fail and schedule maintenance accordingly.
In addition to preventing accidents, the use of advanced technology for inspection planning can also save time and costs . Traditional inspection methods often require manual data collection and analysis, which can be time consuming and expensive. By automating these processes with artificial intelligence and machine learning, inspection planning can be optimized and costs reduced.
Another important lesson that we can learn from past accidents is the importance of having a well-established risk management system. An effective risk management system can help identify and assess the risks associated with pipelines in light product terminals and take the necessary steps to mitigate those risks.